1 Introduction
The present technology of solidification of actinides as constituents of high-level wastes by vitrification does not ensure a full immobilization of radionuclides because of low hydrothermal stability of glasses: the leaching rate of constituents of glasses rises by 1–3 order (s) of magnitude with increasing temperature from the ambient one up to 90 °С [1,2]. As an alternative, isomorphous incorporation of the actinides into crystalline phases being analogue of natural minerals and having high radiation and chemical stability (e.g., titanates with pyrochlore structure) is studied rather intensively [3]. For preparation of the mineral-like matrices, various methods were previously proposed, among which cold pressing and sintering [4], hot pressing [5] or induction melting in cold crucible [6] should be noted.
Self-propagating high-temperature synthesis (SHS) [7,8] is a new original method for immobilization of long-lived actinides in these matrices. SHS is based on locally induced strong exothermal chemical reaction between a metal and an oxidizer being in a charge consisting of a mixture of powders of chemical elements and mineral additions. The heat released as a result of this reaction induces exothermal reaction in adjoining layers of the mixture, resulting in a rapid self-propagating process. In such a process the chemical reaction proceeds in a narrow zone moving spontaneously with a linear speed of 0.1–15 cm/s at 1700–3000 °C.
2 Experimental
Composition of batch mixture used for performing SHS process, % wt.: Y2O3 – 43.4, Ti – 17.7, TiO2 – 4.6, MoO3 – 34.3. The formation of yttrium titanate occurred according to the following oxidation–reduction reaction, where Ti is the reducing agent and MoO3 is the oxidizing agent:
Preliminary experiments had shown the possibility of preparation of solid-state matrices which had a density of 3.5–4.2 g/cm3 (the density of the natural mineral is 5.1 g/cm3) and a compressive strength over 50 MPa. The mixing of the oxides of actinides 237Np, 237Pu, 241Am, and 238U (powders with the pore sizes of about 100 mesh, obtained as a result of calcination of hydroxides or oxalates of actinides at 800 °С under reducing conditions) with the batch mixture has been carried out in alcohol solution in a glove box, followed by filtration of the suspension. After filtration the press mold was dried for 5 h at 90 °C in a drying box and pressed. The obtained tablet was placed on a layer of incendiary mixture situated on a support of fire brick and covered with a safety quartz beaker. SHS was initiated by applying an electrical firing supplied from below, and the tablet was burned out. Contents of the actinide oxides in the prepared matrices are presented in Table 1.
The actinide-containing matrices prepared by SHS
Matrix | Content of actinides oxides (% wt.)/Specific activity of the matrices (Bq/g) | Weight (g) | Density (g/cm3) | |||
238UO2 | 237NpO2 | 239PuO2 | 241Am2O3 | |||
1 | – | – | 10/2.0 × 108 | 0.2/2.3 × 108 | 3.2 | 3.0 |
2 | – | 10/2.3 × 106 | – | – | 1.9 | 3.7 |
3 | 7/770 | – | 3/6.1 × 107 | – | 1.8 | 3.5 |
4 | 9.7/1.1 × 103 | – | – | 0.3/3.5 × 108 | 1.8 | 4.1 |
X-ray and SEM/EDS analyses were used for the structure examinations of the matrices prepared by SHS. X-ray lines characteristic of the compound with a pyrochlore structure proved to be identical to those of standard Y2Ti2O7 phase (Fig. 1). No proper phase of actinide oxides is revealed. It is seen from SEM-photomicrographs (Fig. 2) that the dominating phase of the matrices is pyrochlore, the lighter phase is molybdenum and, possibly, molybdenum dioxide and rutile.

X-ray diffraction patterns of the matrix 1 (Py – pyrochlore, Mo – molybdenum).
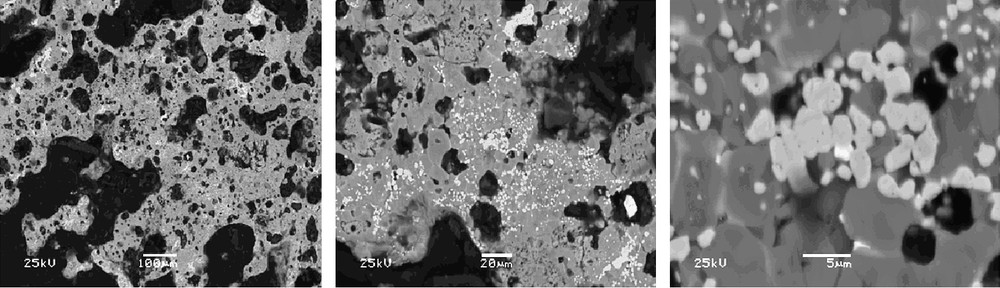
SEM-photomicrograph of the matrix 3 (gray – pyrochlore, light – molybdenum, black – pores).
The study on chemical stability of the matrices was carried out according to the MCC-1 [9]. The samples under study were placed into PTFE containers. Twice-distilled water (pH = 5.80) was used as leaching agent. The containers with the suspensions were placed into a drying box at a temperature of 90 °С for the necessary time, and cooled to ambient temperature. Radionuclide concentrations were determined in the leaching solutions. The leaching rate of actinide i is given by: Ri = mi/(fiStn) [g/(cm2 day)], where mi is the mass of actinide i in the solution, fi is the mass composition of actinide i in the initial sample, S is the open “geometric” surface of the sample, and tn is the leaching duration. The data obtained in leaching tests are presented in Table 2.
The leaching rates of the actinides contained in matrices produced by SHS (dates for Synroc and glass are presented for comparison)
Actinide | Test (conditions) | Leaching rate (g/(cm2 day)) | |||||
Matrix number | Synroc [10] | Glass (PNL76–68) [11] | |||||
1 | 2 | 3 | 4 | ||||
Np | MCC-1 (90 °C, 28 days) | – | 1.1 × 10−7 | – | – | 10−8–10−9 | 10−4–10−5 |
Pu | 7.0 × 10−8 | – | 4.1 × 10−7 | – | |||
Am | 1.5 × 10−8 | – | – | 7.0 × 10−8 | |||
U | – | – | 5.4 × 10−7 | 8.1 × 10−7 |
3 Conclusion
SHS-produced solid final products analogous to the natural pyrochlore, containing up to 10% wt. of actinide oxides incorporated, from the initial mixtures of reagents, mineral additions and constituents of HLW. Densities of the prepared matrices are equal to up to 80% of the density of the natural mineral. On producing matrices by the SHS material balance regarding actinides remains. The produced matrices had a high chemical stability: leaching rates of the actinides lie within the limits of 10−7–10−8 g/(cm2 day).