1 Introduction
The spray-deposition of polyelectrolyte multilayers [1–11] has recently been gaining interest as an alternative to the well established assembly of such films by “dipping” (see for example : [8,12–21]).
In our earlier article [2] we have pointed out that one of the most interesting aspects of spray-deposition lies in the fact that spray-assembly can enormously accelerate the deposition time. Today we have cases in which the multilayer assembly of certain materials can be accelerated by a factor of up to 500. However, in the same article we have also pointed out that layer-by-layer assembled films prepared by “dipping” or by “spraying” may show considerable differences with respect to their properties. Most importantly it was noted that films with the same number of layers prepared from the same solutions by “dipping” or “spraying” differ in thickness, for films composed of the sodium salt of poly(styrene sulfonate) (PSS) and poly(allyl amine hydrochloride) (PAH) we noticed that spray-assembled films only had a thickness of about 70–75% of that observed for classic deposition by “dipping”. Investigations by atomic force microscopy (AFM) revealed that both kinds of films also differ with respect to surface roughness. These structural differences, whose origin is far from being understood, demanded to investigate if spray deposited films also possess a stratified structure that was observed earlier by us by neutron reflectometry [22] for the case of multilayer films assembled by dipping. These first experiments also led to a structural model of polyelectrolyte multilayer films, that explained that a stratified albeit “fuzzy” structure is consistent with the often observed charge stoichiometry between polyanions and polycations [14]. Subsequent investigations of polyelectrolyte multilayers by neutron reflectometry revealed many more structural details of such films, including for example water or ion content [23–40].
Here we report on the first semi-quantitative analysis of neutron reflectometry experiments which we carried out on polyelectrolyted multilayers composed of PSS and PAH that were spray assembled in various superlattice architectures by selective positioning of perdeuterated layers of PSS in selected layers. We have used classic algorithms for establishing the main parameters for a structural model as described for example by Parratt [41] or Russell [42]. Our data sets were analyzed using the Motofit software package [43] which uses the Abeles matrix formalism [44]. More specifically, we have used a classic box model in which each layer i (slab) is characterised by three variables: a scattering length density (SLDi), a thickness (Di) and a surface roughness (σi). Since we investigate superlattice structures with a complex layer sequence, we had to devise a strategy to minimize the number of parameters for any manual or numerical curve fitting in order to arrive at a small number of physically meaningful structural data.
The chemical structures of the polymers are depicted in Scheme 1.
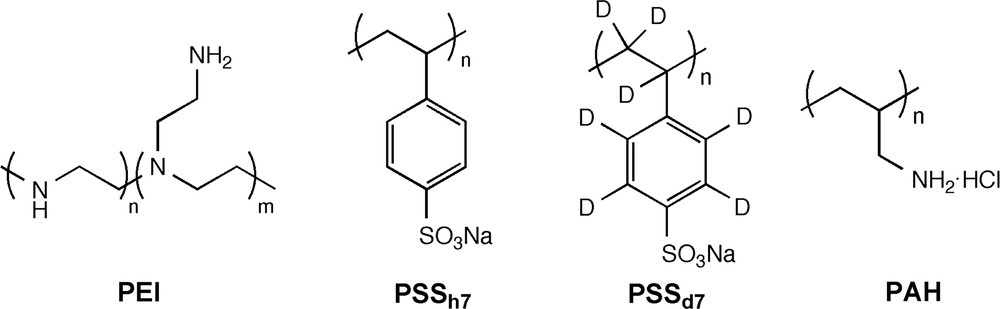
Chemical structures of the polymers used for film fabrication.
2 Materials and methods
2.1 Polyelectrolyte solutions
Poly(sodium 4-styrenesulfonate) (PSSh7, , Lot PI06005MU), poly(allylamine hydrochloride) (PAH, , Lot 05212MO-083) and branched poly(ethyleneimine) (PEI, , Lot 09620EA-193) were purchased from Aldrich (Lyon, France). Deuterated poly(sodium 4-styrenesulfonate) (PSSd7, , Lot pssd8181105na) was purchased from Polymer Standards Service GmbH (Mainz, Germany).
All solutions were prepared using ultrapure water (Milli-Q system, Millipore) with a resistivity of at least 18.2 MΩ cm.
Polyelectrolyte solutions were always freshly prepared by direct dissolution of the respective adequate amounts to yield solutions with final concentrations of PEI of 1 mg/mL, PSSh7 and PSSd7 of 0.6 mg/mL and PAH of 0.27 mg/mL. Each polyelectrolyte, except PEI, was dissolved in Milli-Q water containing 0.5 M sodium chloride (NaCl, Reagent Plus, ≥99.5%, Batch#: 096K0076 was purchased from Sigma). PEI itself was dissolved in pure Milli-Q water. All final polyelectrolyte concentrations correspond to about 3 × 10−3 monomol/L in which monomol corresponds to moles of the respective monomer repeat unit. Here, we have ignored the molecular weight difference between PSSh7 and PSSd7.
2.2 Film substrate
Silicon wafers with an orientation (100) and a thickness of 0.5 mm were purchased from Wafernet Inc. (San Jose, USA) They were then cut to a size of about 45 mm × 20 mm for polyelectrolyte film deposition.
Before the film deposition, all silicon wafers were cleaned by immersing firstly in a mixed solution of methanol and hydrochloric acid (1:1, v/v) for 30 min and then stored in a concentrated sulfuric acid solution for at least an overnight. All wafers were extensively rinsed in Milli-Q water after cleaning and used within a few hours for the deposition of multilayer films.
2.3 Ellipsometry
Measurement of the film thickness was carried out with a Multiskop instrument (Optrel GbR, Kleinmachnow, Germany) operating at a laser wavelength of 632.8 nm and a constant angle of 70°. For each substrate studied, several points were measured to obtain the average value for the film thickness.
2.4 Film buildup
All polyelectrolyte multilayer films were assembled after the deposition of a PEI precursor layer. The cleaned Si-wafers were dipped into a PEI solution for 5 min, rinsed in Milli-Q water and dried under a nitrogen flux prior to deposition by spraying or dipping.
The spray-deposition was carried out by using manual spray cans as described before [2]. Different spray cans were used for the PSSh7, PSSd7, PAH and the rinsing solution (a 0.5 M aqueous solution of NaCl), respectively. The spray conditions were as follows: polymer solution spraying time t1 = 5 s, contact time t2 = 15 s, rinsing time t3 = 5 s, waiting time t4 = 15 s. The deposition time for a single layer pair corresponds accordingly to (t1 + t2 + t3 + t4) × 2 = 80 s.
The film deposition by dipping was carried out by immersing the substrate for 20 min in the polyelectrolyte solution followed by three rinsing steps of 100 s, 100 s, and 120 s.
2.5 Neutron reflectivity measurements
Specular neutron reflectivity experiments were carried out on the time-of-flight reflectometer EROS (LLB, CEA Saclay, Gif-sur-Yvette, France) [45]. The data were collected at a fixed angle of 0.93° with a neutron white beam covering wavelengths from 2.5 Å to 25 Å with a δλ/λ of 0.025. We used collimation slits of 2 mm and 1 mm, which leads to a δθ of 0.004° (δθ/θ ∼ 0.045). The final accessible Q-range was 0.008–0.081 Å−1. A standard treatment of raw data was applied to obtain reflectivity curves in absolute scale.
3 Results and discussion
In a first series, we fabricated the following six film architectures for characterisation by neutron reflectometry. Fig. 1 represents the general film architecture of all samples as summarized in detail in Table 1.
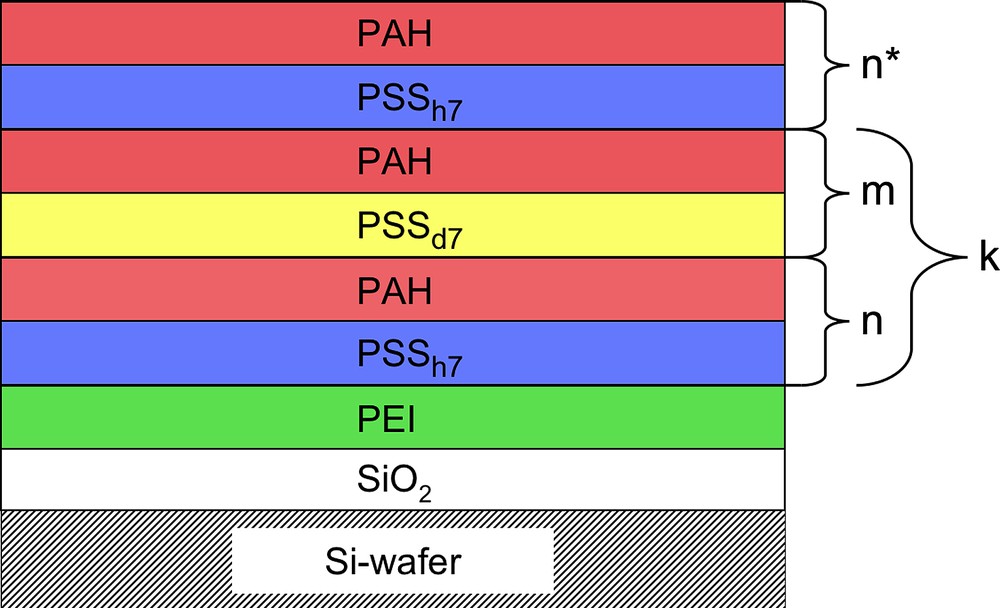
Graphic representation of the layer architecture of the different multilayer samples.
Multilayer architecture and preparation conditions of the 6 samples investigated by neutron reflectometry.
sample | layer sequence | n = n∗ | m | k | total number of layer pairs | ellipsometric film thickness/Å | deposition by | |
total | per layer pair | |||||||
A | Si/SiO2/PEI/(PSSh7/PAH)10 | 0 | 10 | 0 | 10 | 247.5 ± 0.7 | 24.8 | spraying |
B | Si/SiO2/PEI/(PSSd7/PAH)10 | 0 | 10 | 0 | 10 | 254.8 ± 3.0 | 25.5 | spraying |
C | Si/SiO2/PEI/[(PSSh7/PAH)3/(PSSd7/PAH)1]6/(PSSh7/PAH)3 | 3 | 1 | 6 | 27 | 639.1 ± 1.9 | 23.7 | spraying |
D | Si/SiO2/PEI/[(PSSh7/PAH)5/(PSSd7/PAH)1]6/(PSSh7/PAH)5 | 5 | 1 | 6 | 41 | 988.1 ± 12.3 | 24.1 | spraying |
E | Si/SiO2/PEI/[(PSSh7/PAH)4/(PSSd7/PAH)1]8/(PSSh7/PAH)4 | 4 | 1 | 8 | 44 | 1050.9 ± 2.6 | 23.9 | spraying |
F | Si/SiO2/PEI/[(PSSh7/PAH)4/(PSSd7/PAH)1]8/(PSSh7/PAH)4 | 4 | 1 | 8 | 44 | 1388.6 ± 7.6 | 31.6 | dipping |
All multilayer films were deposited on Si-wafers with a size of 45 mm × 20 mm × 0.5 mm, for technical reasons the dimensions of the multilayer films were 40 mm × 20 mm. The wafers were cleaned as previously reported and then immediately coated with a single layer of non-deuterated poly(ethyleneimine) (PEI).
For obtaining the base parameters for all samples we need to identify the thickness, the roughness and the SLDs for a single layer pair (PSS/PAH) either deuterated or non-deuterated. One of the problems of doing so arises from the fact that we require a layer of PEI on top of the SiO2 surface, the direct adsorption of PAH on SiO2 leads only to a very thin layer of PAH. For the preparation conditions used in the work presented here we have an ellipsometrically determined average thickness of this PEI layer of 11.5 Å which we feed directly into the model for calculating reflectivities. Another problem arises from the experimental scatter of data from different samples, which basically requires us to fit many data sets in parallel refining certain parameters by using data from several different data sets at the same time. While global fitting is one of the advantages of the MotoFit package, we wanted to avoid using an automated global fitting procedure for the first test experiments. We have therefore approached a true global fitting by manually adjusting parameters by small fractions and then applying the model to different data sets until we got good agreement of a single model with as many data sets as possible. This is the reason why we prefer to report below the values e.g. for thicknesses with a precision of 0.1 Å, while the resolution of the EROS beamline is only on the Å scale. We feel that this is justified since those values represent a “manual global average” over several data sets. A “manual” approach is only reasonable for a few data sets, in the future we are planning to extend our work by automatically fitting a large number of different data sets in parallel. In the discussion below we avoid going into the details of the “manual fitting”, we prefer to elaborate how well a simple “manual approach” already works.
3.1 Sample A
A film composed of 10 layer pairs (or 20 layers) of PSSh7 and PAH (film architecture Si/SiO2/PEI/(PSSh7/PAH)10). This is the reference film for all non-deuterated slabs in all film architectures.
This sample was used to verify that the scattering length density of the silicon wafer (SLD-Si) could be set to its regular value of 2.07 × 10−6 Å−2, which was kept constant for all samples. The SLD of the surface layer of oxide (SLD-SiO2) was set to 3.15 × 10−6 Å−2, the surface roughness of the Si/SiO2 and SiO2/air interfaces (σ-Si/SiO2) and (σ-SiO2/air) was set to their common value of 4 Å and the thickness of the oxide layer (D-SiO2) was determined to be 12.5 Å, all of these values were then kept constant for all further samples. Using these values as basic parameters, the scattering length density (SLD-nd) of the non-deuterated polymer film was determined to be 1.11 × 10−6 Å−2. As total thickness (D-nd) for the polyelectrolyte film we obtained 265.7 Å, 11.5 Å of which we attributed to the PEI layer leaving 254.2 Å for the (PSSh7/PAH)10 part of the film. Finally the surface roughness (σ-nd) of a polyelectrolyte film containing no deuterated material was set to 13 Å. A free fit of this parameter typically resulted in slightly higher values, but a slight overestimation of roughness values is common when using numerical fitting routines. The roughness of the PEI layer was set to a value of 9 Å because it is in direct contact with the inorganic surface and typically slightly thinner than the subsequent polyelectrolyte layers. The SLD for the PEI layer was assumed to be identical to the average density of sample A (1.11 × 10−6 Å−2), all these values were then kept constant for all samples, the sole exception is discussed below.
3.2 Sample B
A film composed of 10 layer pairs of PSSd7 and PAH (film architecture Si/SiO2/PEI/(PSSd7/PAH)10). This is the reference film for all deuterated slabs in all film architectures.
This film was used only for the determination of the scattering length density (SLD-d), the thickness (D-d) and the roughness (σ-d) of a polyelectrolyte film with a maximum of deuteration. The parameters (SLD-Si), (SLD-SiO2), (D-SiO2), (σ-Si/SiO2) and (σ-SiO2/film), were kept identical to the values in sample A. The total thickness of the deuterated film was determined to be 264.6 Å, leaving 253.1 Å for the (PSSd7/PAH)10 part of the film by considering a thickness of the PEI layer of 11.5 Å as in sample A. The roughness of the PEI layer and the roughness of the film/air interface were set to 9 Å and 13 Å respectively, the same values as in sample A.
Since the thicknesses of the deuterated and non-deuterated films cannot be distinguished within the experimental error we can now define the average thickness value for a (PSS/PAH)1 layer pair to be 25.4 Å which is the average of D-d and D-nd divided by 10. This value is the base value for all model calculations when we compute the thickness of a deuterated (PSSd7/PAH)m slab or a non-deuterated (PSSh7/PAH)n slab in any film architecture.
Please note that we have to use different SLD values for the PEI layers in samples A and B. When trying to introduce a layer of PEI as in all other samples (D-PEI = 11.5 Å, SLD-PEI = 1.11 × 10−6 Å−2 and σ-PEI = 9 Å), a fit of SLD-PEI always approached the same value as the density of the deuterated film (SLD-d), which was determined to be 2.75 × 10−6 Å−2. If the SLD of PEI was kept at 1.11 × 10−6 Å−2 and the thickness of the PEI layer was numerically fitted, it always approached 0 Å. In fact, this should have been expected since adjacent polyelectrolyte layers strongly overlap [14], a detail which also shows up in the interfacial roughnesses of deuterated and non-deuterated layers of 13 Å. In sample B it is therefore impossible to use an independent PEI slab with a SLD of 1.11 × 10−6 Å−2 as in all other films, since in sample B the density of the PEI layer cannot be distinguished from the density of the rest of the deuterated film (SLD = 2.75 × 10−6 Å−2).
Fig. 2 depicts on the left the experimental reflectivity data with the corresponding error bars and the calculated reflectivities (R) for the reference samples A and B using the model parameters as described above and summarized in Table 2. The SLD-profiles corresponding to the calculated reflectivities are shown on the right.
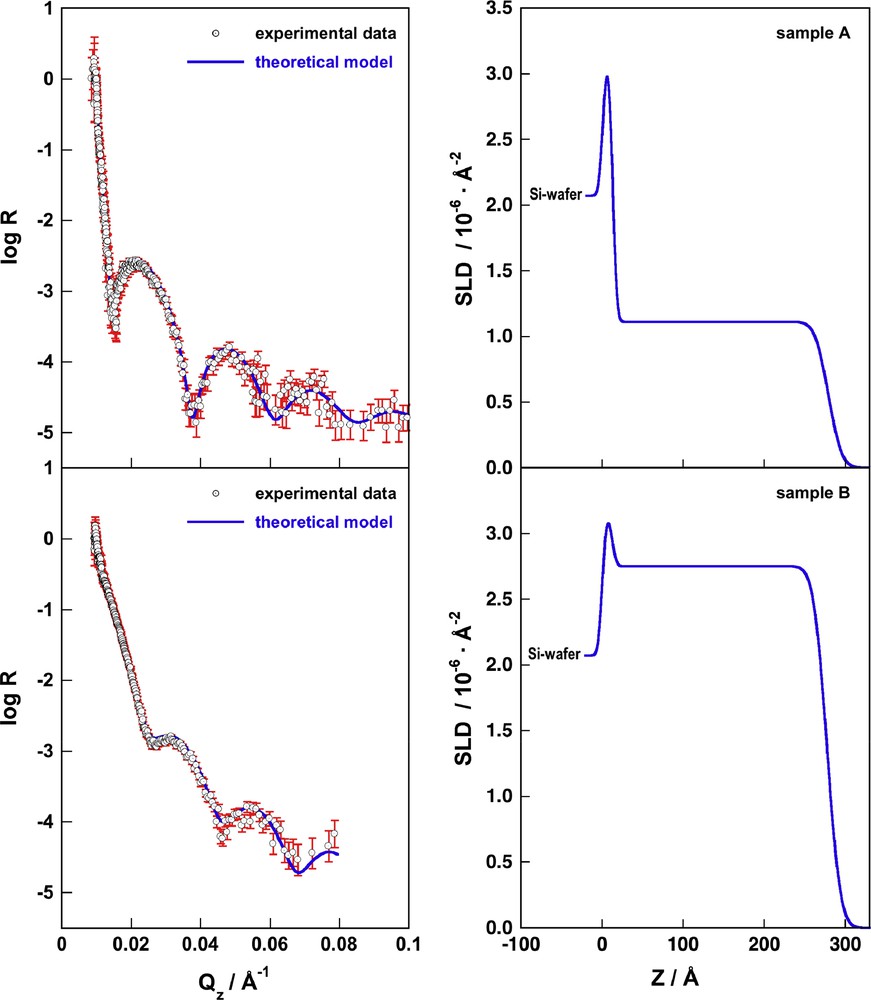
On the left we depict the experimental reflectivity data of samples A (top) and B (bottom), the error bars for each data point are shown in red. The blue lines represent the calculated reflectivities of the box model as discussed in the text and summarized in Table 2. On the right we show the scattering length density profiles corresponding to the calculated reflectivities on the left (For interpretation of the references to colour in this figure legend, the reader is referred to the web version of this article).
Model parameters used for calculating the theoretical reflectivities of samples A–F.
A. Parameters kept constant in all samples | |||||||||
layer/slab | D/Å | SLD/10−6 Å−2 | σ/Å | ||||||
Si | ∞ | 2.07 | 4.0 | ||||||
SiO2 | 12.5 | 3.15 | 4.0 | ||||||
PEI | 11.5 | 1.11/2.75a | 9.0 | ||||||
B. Adjusted or variable parameters in all samples | |||||||||
sample | number of multilayer repeat units | non-deuterated slabs | deuterated slabs | ||||||
SLD [10−6 Å−2] | number of layer pairs | thickness [Å] | roughness [Å] | SLD [10−6 Å−2] | number of layer pairs | thickness [Å] | roughness [Å] | ||
A | – | 1.11 | 10 | 254.2 | 13.0 | – | – | – | – |
B | – | – | – | – | – | 2.75 | 10 | 253.1 | 13.0 |
C | 6 | 1.11 | 3 | 76.1 | 13.0 | 2.75 | 1 | 25.4 | 13.0 |
D | 6 | 1.11 | 5 | 126.8 | 13.0 | 2.75 | 1 | 25.4 | 13.0 |
E | 8 | 1.11 | 4 | 104.8 | 13.0 | 2.75 | 1 | 26.2 | 13.0 |
F | 8 | 1.11 | 4 | 138.5 | 18.0 | 2.75 | 1 | 34.6 | 18.0 |
a See text for details.
3.3 Samples C and D
Samples C and D are superlattice films containing deuterated and non-deuterated slabs with the following general architecture .
In sample C n and n∗ have a value of 3 and in sample D n and n∗ have a value of 5. Sample C corresponds therefore to a film composed of a total of 27 layer pairs of PSS and PAH in which 6 deuterated layers of PSSd7 are distributed with an equidistant spacing within the whole film (film architecture Si/SiO2/PEI/[(PSSh7/PAH)3/(PSSd7/PAH)1]6/(PSSh7/PAH)3). Using the base value for a single layer pair of 25.4 Å yields thickness values for the (PSSh7/PAH)3 slabs of 76.1 Å while the (PSSd7/PAH)1 slabs have a thickness of 25.4 Å. Sample D (n = n∗ = 5) then corresponds to a film composed of a total of 41 layer pairs of PSS and PAH, again with 6 deuterated layers of PSSd7 distributed with an equidistant spacing throughout the whole film (film architecture Si/SiO2/PEI/[(PSSh7/PAH)5/(PSSd7/PAH)1]6/(PSSh7/PAH)5). Using the base value for a single layer pair of 25.4 Å yields thickness values for the (PSSh7/PAH)5 slabs of 126.8 Å while the (PSSd7/PAH)1 slabs possess the same thickness as in sample C (25.4 Å).
Samples C and D can be regarded as control specimen for testing the quality of the parameters determined from samples A and B. Please note that we do not have any free parameters for calculating the model reflectivities because the thicknesses of the deuterated and non-deuterated slabs are simply calculated from the corresponding number of base repeat units (PSS/PAH)1 with a thickness of 25.4 Å. We used a multilayer model with 6 identical repeat units to simulate the experimental data, that is to say that all deuterated slabs in samples C and D were set to a SLD-d of 2.75 × 10−6 Å−2 and all non-deuterated slabs were set to a SLD-nd of 1.11 × 10−6 Å−2.
Fig. 3 depicts on the left the experimental reflectivity data with the corresponding error bars and the calculated reflectivities (R) for the reference samples C and D using the model parameters as described above and summarized in Table 2. The SLD-profiles corresponding to the calculated reflectivities are shown on the right.
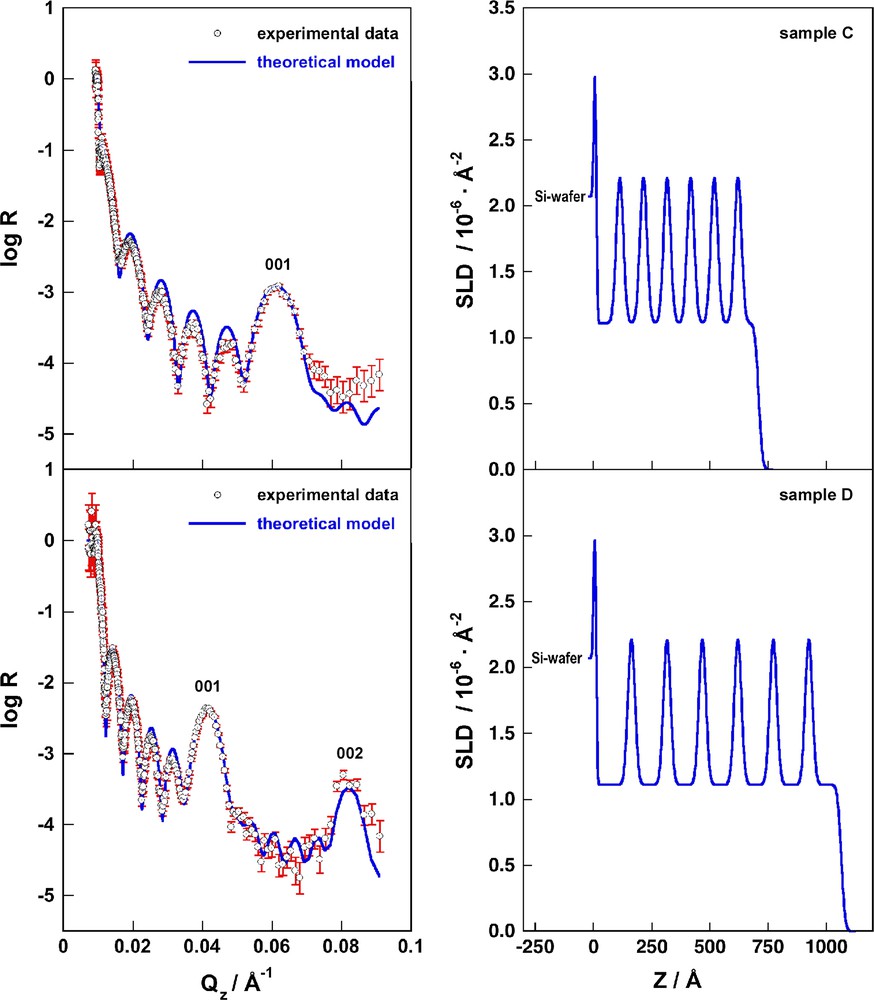
On the left we depict the experimental reflectivity data of samples C (top) and D (bottom), the error bars for each data point are shown in red. The blue lines represent the calculated reflectivities of the box model as discussed in the text and summarized in Table 2. On the right we show the scattering length density profiles corresponding to the calculated reflectivities on the left (For interpretation of the references to colour in this figure legend, the reader is referred to the web version of this article).
This excellent agreement between experimental data and a theoretical model without free parameters shows that the model is generally valid for spray-assembled polyelectrolyte multilayers of PSS and PAH in different superlattice architectures if prepared at identical conditions.
3.4 Samples E and F
Samples E and F are superlattice films containing deuterated and non-deuterated slabs with the same general architecture Si/SiO2/PEI/[(PSSh7/PAH)4/(PSSd7/PAH)1]8/(PSSh7/PAH)4. However, the samples were prepared by different deposition methods, sample E was fabricated by spraying and sample F was constructed by dipping. An important difference in comparison with samples A–D is that samples E and F were prepared from different solutions and about 6 months earlier than samples A–D.
Due to the fact that sample E was prepared at slightly different conditions than samples A–D, it was necessary to re-fit the thickness of the base repeat unit (PSS/PAH)1 for sample E. It turns out that the thickness of the base repeat unit of sample E is 26.2 Å, which is 0.85 Å or 3.3% thicker than the thickness of the base repeat unit of samples A–D (25.4 Å). All other parameters of the multilayer model were kept identical to the values used for samples C and D. Fig. 4 shows that the experimental data and the calculated reflectivities are in excellent agreement after fitting only a single parameter (the thickness of the base repeat unit).
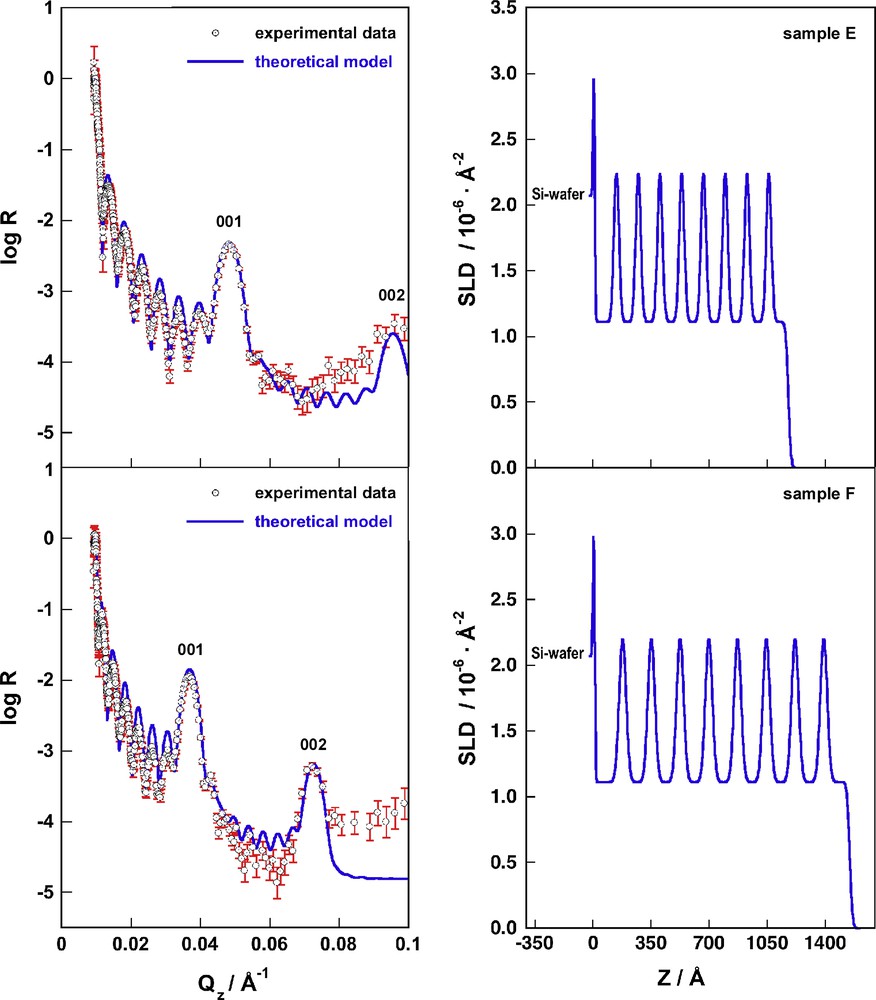
On the left we depict the experimental reflectivity data of samples E (top) and F (bottom), the error bars for each data point are shown in red. The blue lines represent the calculated reflectivities of the box model as discussed in the text and summarized in Table 2. On the right we show the scattering length density profiles corresponding to the calculated reflectivities on the left (For interpretation of the references to colour in this figure legend, the reader is referred to the web version of this article).
Sample F was prepared by dipping and we already know from previous experiments [2] that films prepared by dipping and by spraying differ considerably in thickness. The ellipsometrically determined thicknesses of samples E and F were 1050.9 ± 2.6 Å and 1388.5 ± 7.6 Å, thus the dipped sample is 1.321 times thicker than the sample prepared by spraying from the same solutions. This value is in perfect agreement with the previously reported differences between spraying and dipping. The value for the base repeat unit of sample E was therefore multiplied by 1.321 to yield the value of the base repeat unit of sample F of 34.6 Å. However, there was still a large discrepancy between the experimental data and the calculated reflectivities at this stage of structural refinement. Of course, it is always possible to give up a strict model and to fit additional parameters in order to obtain a better agreement with the data. However, the only physical parameter for which we can justify a change is the roughness of the interface between the deuterated and non-deuterated slabs and the roughness of the film air interface. All these values were set to 18 Å, a value that yielded the best match for the intensities of the 001 and 002 peaks for the superlattice repeat unit. A slightly increased roughness for dipped films with respect to sprayed films was already observed before [2] and is also reflected in the standard deviations of the ellipsometrically determined thicknesses of samples E and F. The experimental data and the calculated reflectivities at this stage of structural refinement are presented in Fig. 4. The agreement between model and data is already quite good, however, the quality of the fit for sample F as expressed by the value of χ2 = 30.4 is not as good as the quality of the fit for sample E with a value of χ2 = 14.5. This indicates that there are even more subtle structural differences between polyelectrolyte multilayers that are assembled by spraying or by dipping. However, our current set of data does not allow us to refine further differences in a reasonable way. We are currently planning to investigate such structural details in the near future.
4 Summary and conclusions
Our first neutron reflectometry measurements on spray-assembled superlattice LbL-film architectures of deuterated and non-deuterated PSS and PAH clearly proof that such films are stratified. Depending on the distance between the deuterated layers, we observe one or two peaks (001 and 002) for the superlattice of the deuterated layers within our samples in the Q-range accessible with the EROS beamline at the Laboratoire Léon Brillouin. It is also very clear that spray-assembled films are about 30% thinner than films prepared by dipping. At the present state of structural refinement, we also have an indication for an increased surface roughness and increased interfacial roughnesses between deuterated and non-deuterated slabs in films prepared by dipping. However, our present set of data from samples prepared by dipping does not yet allow an exact determination of the SLD values for deuterated and non-deuterated slabs within films prepared by dipping.
The reflectivity data presented here and their structural refinement clearly show that subtle details in the architecture of polyelectrolyte multilayer films can be analyzed by neutron reflectometry. While the calculated reflectivities we present here do certainly not perfectly match the experimental data, they are in excellent agreement considering that these calculated reflectivities were obtained without any free parameter for samples C and D, and with only one free parameter for samples E and F. All results of the neutron reflectometry measurements are summarized in Table 2.
It will be very interesting to see in the future if even more subtle structural details can be picked up. At present, the spray-deposition of LbL-films is performed manually by using very simple pulverization cans which do not permit sufficient control over the spray process, especially with respect to pressure and delivered liquid volumes. A more precise control of the spray parameters is expected for future measurements with automated spray-deposition equipment with high quality nozzles.
However, the fact that spray-deposition does lead to stratified films and that such films are at least as smooth as films assembled by dipping – while the deposition times for spraying are reduced by at least a factor of 100 in comparison with dipping – makes spray-assembly an extremely attractive method for the fabrication of soft-matter thin films and devices. Spray-deposition allows for a more rapid deposition of multilayer films and apparently to a better control of the roughness, at least for the case of films composed of poly(styrene sulfonate) and poly(allylamine hydrochloride).
Acknowledgements
We acknowledge financial support from the Institut Universitaire de France (G. Decher), the Laboratoire Léon Brillouin, the Université Louis Pasteur, the C.N.R.S. and the French Ministère de l'Enseignement supérieur et de la Recherche (Z. Zheng). We appreciate the help of Dr. Andrew Nelson of ANSTO Australia in getting us started with his MotoFit package.