1 Introduction
H2 production from the dry reforming of methane can contribute to the use of H2 as an alternative fuel, removing the difficulty of storage and distribution [1–3]. Hydrogen can be used in the chemical industry and as a fuel for fuel cells. Methane and carbon dioxide are harmful molecules and contribute to the greenhouse effect; consequently CO2 reforming or dry reforming of methane may have an important environmental implication. In the last few years, the reaction between CO2 and CH4 which produces H2 and CO attracted many researchers [3–5]. The gas produced with a determined H2/CO ratio, is more suitable for Fischer–Tropsch synthesis to liquid hydrocarbons and oxygenated derivatives. Thus, the Dry Methane Reforming is described by the following reaction:
(1) |
This reaction is endothermic and should be carried out at high temperature (∼800 °C). The conventional catalysts in dry methane reforming are based on Ni, Co or a noble metal (Pt, Ru, …) [3]. One of the main problems for the preparation of effective reforming catalysts is the deactivation due to coke formation. In the presence of noble metals and an adequate support, coke formation can be attenuated [6]. Dispersing the active metal on a high surface area support material and the use of promoters then improve catalyst stability and activity.
In this paper alumina and ceria are chosen as supports. Alumina has high surface area and is thermally stable [7]. Cerium oxide or ceria is an important material for a variety of catalytic reactions because of the physico-chemical properties and O2 mobility [8]. Recently, successful studies on ceria for the “dry methane reforming” reactions have been performed [8,9] due to its ability to reduce carbon formation. The main objective of the present work is to study the influence of ceria addition on alumina on the activity of ruthenium-based catalysts (5 wt%).
2 Experimental
2.1 Preparation of catalysts
Al2O3 was prepared by a sol–gel method [10] according to the following procedure: 50 mL of aluminum sec-butoxide was dissolved in 100 mL of 2-butanol and then 50 mL of 1,3-butanediol was added. 35 mL deionized water was added drop by drop under mild stirring. The precursor solution was vigorously stirred at 85 °C for 1 h. After that the resulting gel was dried at 100 °C for 24 h, and finally alumina was obtained after calcination at 600 °C for 4 h.
CeO2 was prepared by precipitation of cerium(III) nitrate hexahydrated solution Ce(NO3)·6H2O in an alkali solution of NaOH [11]. The solid was filtered, washed, dried at 100 °C and then calcined at 600 °C for 4 h.
Different CeO2/Al2O3 oxides were synthesized by impregnation of cerium(III) nitrate hexahydrated with calcined alumina as synthesized above. Then the sample was dried at 100 °C and calcined at 600 °C for 4 h. Cerium containing solids were denoted 1Ce10Al, 3Ce10Al, 5Ce10Al, where the number before chemical symbol represents the atomic content in the solid.
The ruthenium-based catalysts were prepared by impregnating 5 wt% of Ru on the support material with the aqueous solution of precursor (Ru(NO)(NO3)3). The solids obtained were then dried at 100 °C for 20 h, and calcined in air at 600 °C for 4 h.
The ruthenium-based catalysts were denoted Ru/CeO2, Ru/Al2O3 and Ru/nCe10Al (n = 1,3,5).
2.2 Catalytic reaction
The catalysts (100 mg) were tested under atmospheric pressure in a fixed-bed quartz reactor after a pretreatment under Ar flow at 400 °C. The reactor was fed with CH4:CO2:Ar (5:5:90) for a total flow rate of 100 mL min−1. The reaction products were analyzed with a Varian chromatograph equipped with a CTRI column and a TCD detector. Dry reforming of methane was performed with temperatures ranging from 400 to 800 °C.
2.3 Characterization of catalysts
Brunauer–Emmett–Teller (BET) surface area of catalysts was measured by using the adsorption of liquid nitrogen at −196 °C by Qsurf analyzer, after a treatment at 120 °C for 30 min.
XRD analysis was performed on a BRUKER Advance D8 powder X-ray diffractometer using Cu Kα radiation (l = 0.15406 nm). Diffraction patterns were recorded over a 2θ range of 20–80° and using a step size of 0.02 and a step time of 10 s.
The amount of deposited coke on the catalysts was determined by Thermogravimetric and Differential Thermal Analyzes (TGA/DTA), NETZSCH STA 409 model. The samples were heated from room temperature up to 1000 °C (5 °C min−1) under air flow of 75 mL min−1.
The temperature programmed reduction experiments were carried out in an Altamira AMI-200 apparatus. The TPR profiles were obtained by passing a 5% H2/Ar flow (30 mL min−1) through 20 mg of samples heated at 5 °C min−1 from ambient temperature to 900 °C. The hydrogen concentration in the effluent was continuously monitored by a thermoconductivity detector (TCD).
3 Results and discussion
The BET surfaces of the calcined catalysts are shown in Table 1. The surface area decreases in the order of Ru/Al2O3 > Ru/1Ce10Al > Ru/3Ce10Al > Ru/5Ce10Al > Ru/CeO2. This diminution is explained by partial blocked pores of the alumina by ceria deposited on the surface.
Specific areas of catalysts before and after catalytic test and amount of coke by the weight loss.
Catalysts | SBET before test (m2 g−1) | SBET after test (m2 g−1) | Weight loss after test (%) |
Ru/Al2O3 | 326 | 282 | 0 |
Ru/1Ce10Al | 279 | 267 | 1.3 |
Ru/3Ce10Al | 146 | 139 | 1.1 |
Ru/5Ce10Al | 121 | 110 | 0 |
Ru/CeO2 | 125 | 28 | 1.4 |
Fig. 1a and b shows the CH4 and CO2 conversions at different temperatures for Ru/Al2O3, Ru/CeO2, Ru/1Ce10Al, Ru/3Ce10Al and Ru/5Ce10Al. CO2 conversion is always higher than that of CH4 for the whole range of temperature. In fact, both CO and H2 are produced by the reaction (1), but parts of hydrogen react with CO2 and CO and H2O are produced (Reverse water–gas shift reaction (2)).
(2) |
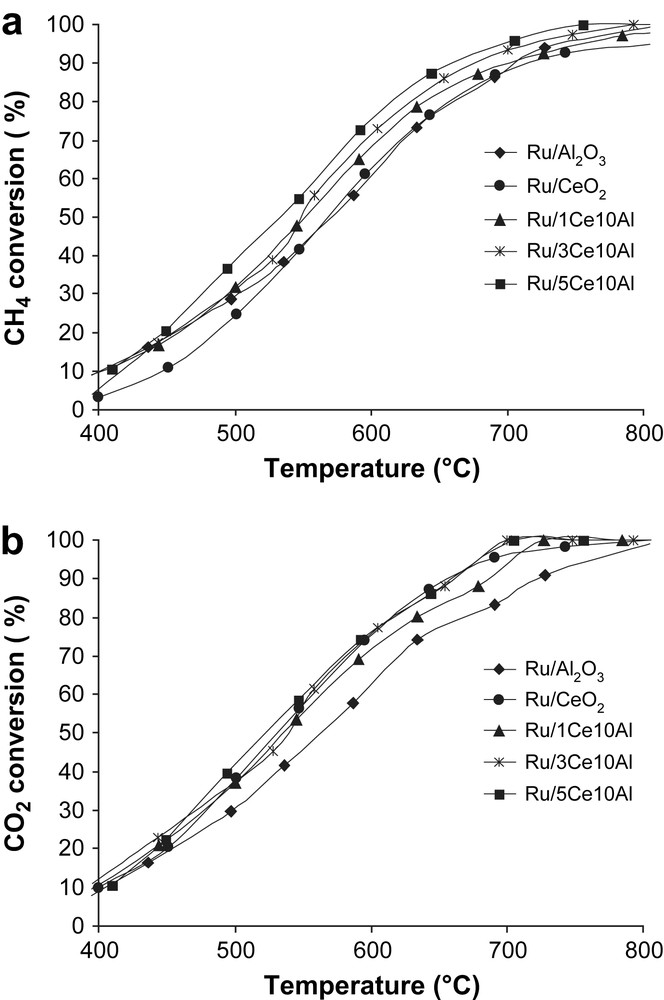
Methane (Fig. 1a) and CO2 (Fig. 1b) conversions (%) during dry reforming of methane vs reaction temperature (°C). Catalyst: 100 mg; CH4/CO2/Ar (5:5:90): 100 mL min−1.
For this reason, the CO production is higher than H2 production [12]. The H2/CO ratio for all catalysts is close to 3/4 (Fig. 2). The conversion decreases in order of Ru/5Ce10Al > Ru/3Ce10Al > Ru/1Ce10Al > Ru/CeO2 > Ru/Al2O3. The increase of ceria's quantity on Al2O3 leads to higher conversions of CH4 and CO2.
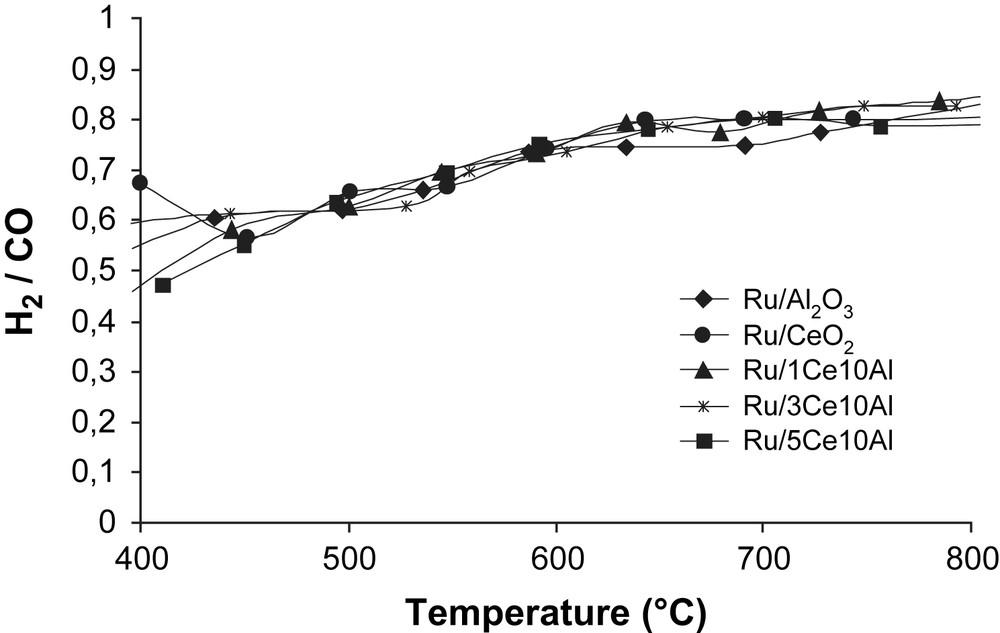
H2/CO ratio during dry reforming of methane vs reaction temperature (°C). Catalyst: 100 mg; CH4/CO2/Ar (5:5:90): 100 mL min−1.
As the specific areas of solids are determined, the activities per mol m−2 s−1 can be calculated for each temperature as following:
The activities of Ru-based catalysts are presented as a function of temperature in Fig. 3. The performance of the catalysts is better illustrated by activities than conversions, although the catalytic orders for the both Figs. 1a and 3 are practically identical. However, the Ru/CeO2 sample which presents a low specific area exhibits a better catalytic performance in Fig. 3. The promoting effect of ceria appears clearly and the activity decreases in order of Ru/5Ce10Al > Ru/CeO2 > Ru/3Ce10Al > Ru/1Ce10Al > Ru/Al2O3.
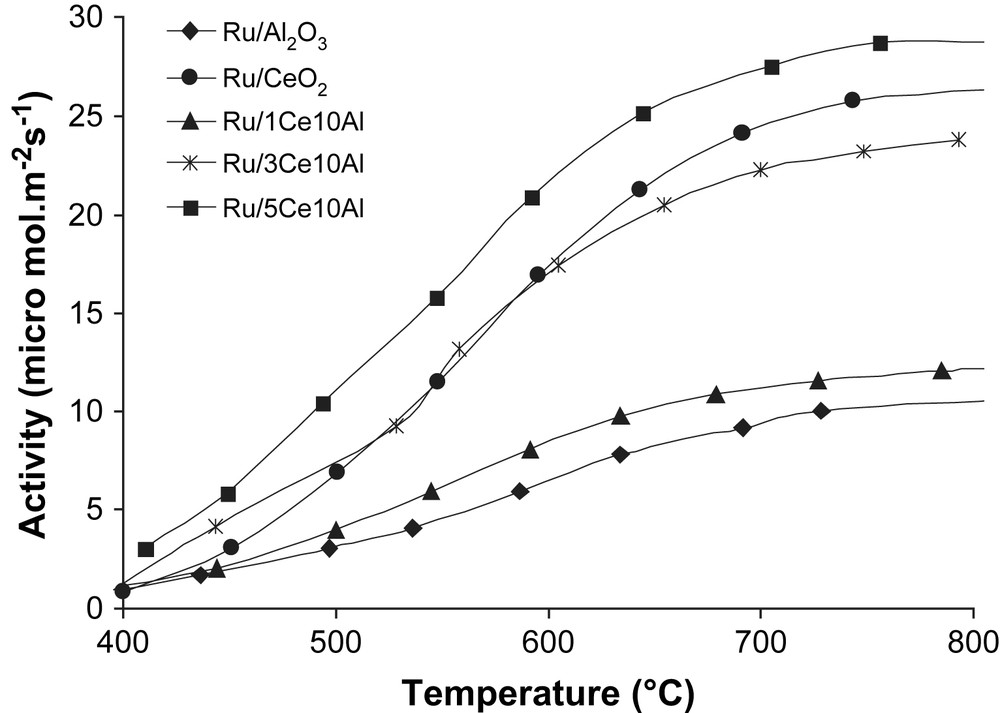
Activity per mol m−2 s−1 during dry reforming of methane vs reaction temperature (°C). Catalyst: 100 mg; CH4/CO2/Ar (5:5:90): 100 mL min−1.
Fig. 4 shows the X-ray powder diffraction patterns of calcined samples. Alumina is amorphous, thus peaks observed are only attributed to RuO2 species (index-pattern 40-1290 data base JCPDS-ICDD) in the pattern of Ru/Al2O3. Diffraction peak intensity of the RuO2 phase decreases with increasing ceria content. This indicates that Ru particles are probably well dispersed on catalysts containing much more ceria. For samples containing cerium, diffraction peaks corresponding to the cerianite phase (CeO2) are observed.
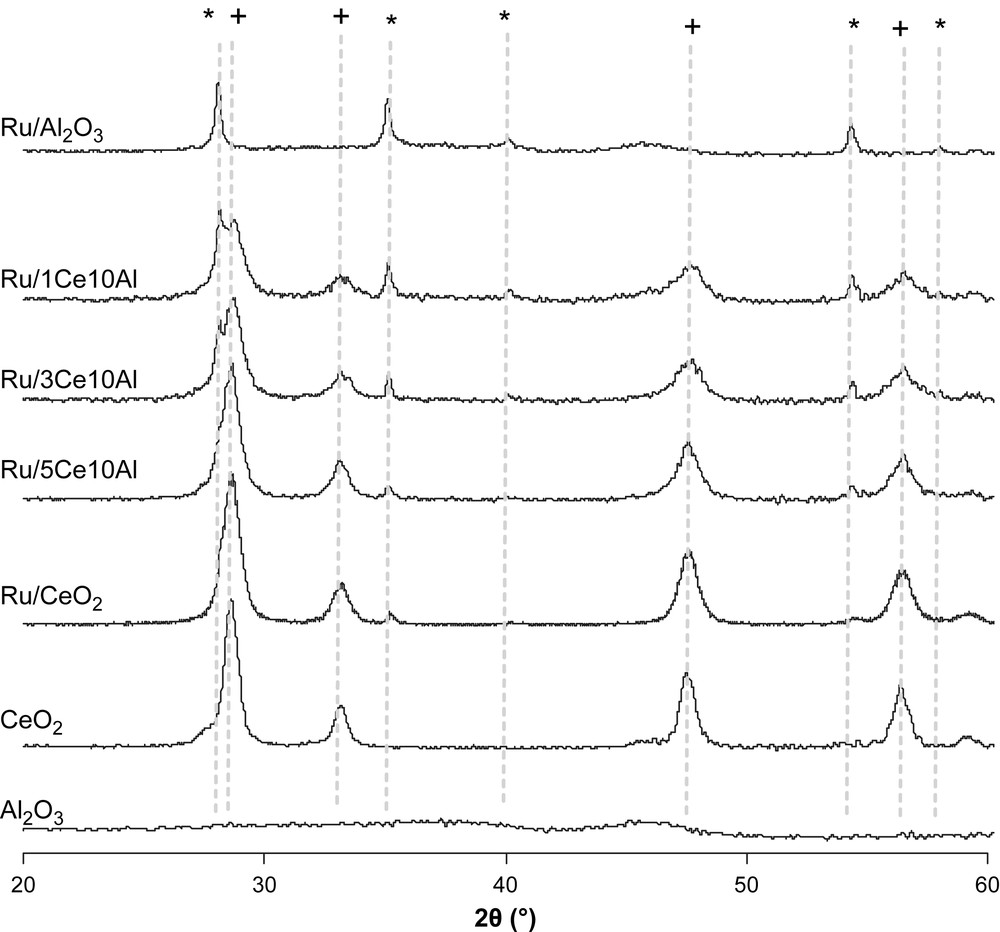
X-ray diffraction patterns of calcined samples. (∗) RuO2; (+) CeO2.
The reducibility of the catalysts after their calcination at 600 °C was characterized by H2-TPR. Fig. 5 shows the TPR profiles of Ru/Al2O3, Ru/CeO2 and Ru/nCe10Al (n = 1,3,5). The TPR peaks are attributed to RuO2 and CeO2 reduction, while alumina is not reducible. Peaks observed at low temperature (T < 270 °C) for each catalyst correspond to the reduction of ruthenium oxide [13]. Ruthenium in RuO2 is reduced directly from Ru4+ to Ru0 without forming intermediate valence states such as Ru3+ or Ru2+. The reduction of ceria takes place mainly in two ranges of temperature. The first range is 300–600 °C and the second range is between 700 and 900 °C. These two ranges of reduction are the characteristics of ceria and they are assigned respectively to the reduction of surface and bulk ceria into Ce2O3 [14,15].
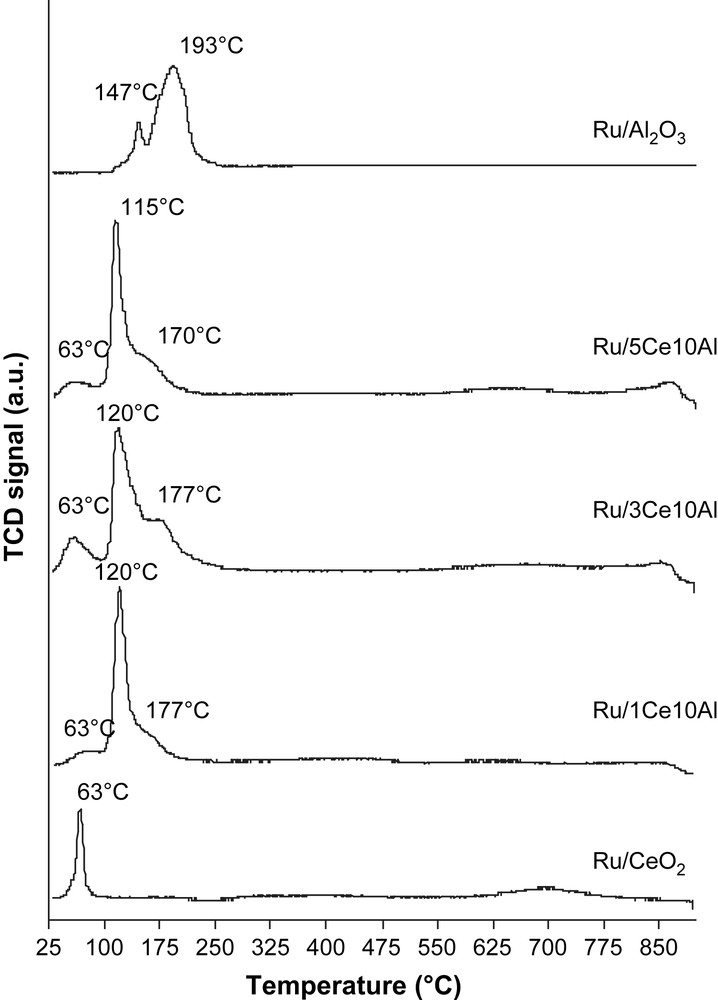
H2-TPR profiles of calcined catalysts.
Ru/CeO2 presents just one reduction peak of the noble metal oxide at 63 °C. RuO2 reduction for Ru/Al2O3 and Ru/nCe10Al catalysts occurs at higher temperatures than those corresponding to Ru/CeO2 with several reduction peaks. The latter can be related to the presence of different type of ruthenium species on support surface.
After calcination of cerium containing catalysts, Ru–Ce–O bond can be created. This interaction between Ru and Ce can conduct then to well dispersed Ru species as shown by XRD patterns of solids. In addition, it has been demonstrated that Ru–Ce–O bond are fragile, afterward Ru is easily reducible [16]. On the basis of these results, peaks at 63 °C for Ru/CeO2, Ru/5Ce10Al, Ru/3Ce10Al and Ru/1Ce10Al are attributed to ruthenium species easily reducible presenting an interaction with ceria.
For the Ru/Al2O3 the first peak at 147 °C can be related to the reduction of ruthenium oxide well dispersed on alumina surface and the second big one at 193 °C to RuO2 agglomerated on the surface which is more difficult to reduce. And for Ru/5Ce10Al, Ru/3Ce10Al and Ru/1Ce10Al the second sharp peaks at 115 °C and 120 °C are attributed to the presence of ruthenium particles well dispersed on the surface and the third one observed at higher temperature (at around 170 °C) can be assigned to the reduction of bulk RuO2.
It seems that ceria addition on alumina has an influence on RuO2 reduction. The peak attributed to well disperse ruthenium particles (second peak) for Ru/nCe10Al is shifted at lower temperature and their intensity is higher than that of Ru/Al2O3. It is known that a higher dispersion of oxides not interacting with the support leads to a shift in the reduction peak [17,18]. These results are in agreement with XRD patterns of solids.
H2 consumption corresponding to ruthenium oxide reduction is at around 600 μmol H2 g−1 for all catalysts except for Ru/CeO2 (187 μmol H2 g−1). The smaller amount of H2 consumption may indicate that the reduced state of Ru is formed even during calcinations at 600 °C [14].
From the analysis of the thermo programmed reduction, catalytic behaviour of ruthenium catalyst can be related to the reducibility of the ruthenium oxide. Thus, the addition of ceria to alumina can enhance the activity of ruthenium-based catalyst for dry reforming of methane. The presence of well dispersed and easily reducible ruthenium species can be responsible for the higher activity of Ru/nCe10Al and Ru/CeO2.
After reaction, catalysts are characterized; BET surfaces and coke formation observed by TGA/DTA are summarized in Table 1. After test, the surface area of catalysts decreased. This result can be correlated to the sintering of particles or/and a formation of carbonaceous deposits. The amount of deposited carbon was evaluated by TGA/DTA, the weight loss is related to the removal of oxidizable carbonaceous compounds (coke). All catalysts exhibit coke deposition except Ru/5Ce10Al and Ru/Al2O3 samples. This result can be related to the redox properties of supports [6].
This work confirms the strong influence of the support in the activity of Ru-based catalysts. The best result is obtained with Ru/5Ce10Al, where cerium promotes a beneficial effect on the dispersion of ruthenium particles and its reducibility and consequently on its catalytic behaviour and the use of alumina leads to a catalyst resistant to coke deposition.
4 Conclusion
CO2 reforming of methane is studied with ruthenium-based catalyst (5 wt%). Ru/Al2O3 is a stable catalyst presenting no coke deposition after test, but its performance is lower than that of the other catalysts. The addition of ceria on alumina can enhance the activity of ruthenium-based catalyst by the presence of Ru–Ce interaction and well dispersed ruthenium species easily reducible. Thus Ru/5Ce10Al shows the highest activity and an absence of coke deposition after reaction.