1 Introduction
The reduction of aromatic ring is a useful and important technique for obtaining a variety of cyclohexane derivatives. Because of the stabilization of the aromatic ring by resonance hybridization, aromatic hydrocarbons are seldom hydrogenated at room temperature over base metals and palladium catalysts [1]. However, at elevated temperatures and pressures, most aromatic hydrocarbons are hydrogenated without difficulty over nickel and cobalt catalysts [2–4]. Over ruthenium and particularly, over rhodium and platinum, benzene and its derivatives are hydrogenated at considerable rates, even at room temperature [5–7]. Previously reported methods for developing cyclohexane rings from arenes are classified into two types of reactions:
- • one is the reduction with greater than stoichiometric amounts of reducing agents, such as LiAlH4, borane derivatives [8–11], or dissolving metals (Birch reduction) [12,13]. These reagents are moisture-sensitive and the reaction should be conducted under anhydrous, strongly reducing and basic conditions. These reaction conditions cannot be tolerated by some co-existing functional groups, such as esters and ketones. Moreover, large amounts of metal waste are produced from the reducing agents in these reactions;
- • another one is hydrogenation with a transition metal catalyst, which is a simple, convenient and sustainable method [14,15]. Although some homogeneous catalysts promote arene hydrogenation efficiently [16,17], the presence of residual metal in the products makes the industrial application of this method difficult. On the other hand, the hydrogenation of arenes through the use of heterogeneous metals (Ni, Rh, Ru, Pt and Pd) [15] has some advantages, such as easy handling, lesser metal contamination in the products and reusability, which would make it suitable for industrial production.
Catalytic hydrogenation of organic compounds with catalysts and hydrogen gas is one of the most useful methods in the field of organic synthesis [18–20]. It was reported by Tashiro's group that aromatic compounds were reduced to the corresponding cyclohexane products in high yields, by using Raney Ni–Al [21]. Recently, Maegawa et al. reported the convenient reduction of aromatic compounds by a hydrogenation procedure based on the use of heterogeneous platinum group catalysts. Rh/C is the most effective catalyst for the hydrogenation of the aromatic ring, which can be conducted in iPrOH under neutral conditions and at ordinary to medium H2 pressures (< 10 atm) [22]. They also reported the solvent-free and solid-phase hydrogenation of various reducible functionalities, which was effectively catalyzed by heterogeneous palladium on carbon (Pd/C) [23]. Palladium catalysts embedded on molecular sieves (MS3A and MS5A) were also developed for chemoselective hydrogenation [24].
Wang et al. developed polymeric mesoporous carbon graphitic nitrides (mpg-C3N4) and ordered mesoporous graphitic carbon nitrides (ompg-C3N4), which were used to prepare palladium catalysts (Pd@C3N4). These catalysts demonstrated excellent activity and selectivity for hydrogenation of quinoline to 1,2,3,4-tetrahydroquinoline under mild temperatures (30–50 °C) and H2 pressure (1 bar) [25]. A green approach was reported about the hydrogenation of bisphenol A (BPA) utilizing a special Ru catalyst in water medium [26]. Utilization of water as a chemical reagent is an essential aspect of green chemistry [27]. Water has many advantages as a solvent for organic reactions from the aspects of cost, safety, operation simplicity, and environmental concerns as compared to the use of an organic solvent [28–30].
In the above-mentioned literature, different aspects of aromatic ring reduction were discussed. In present study, we investigated the reduction of aromatic compounds using Al powder with Pd/C, Rh/C, Pt/C and Ru/C in water under atmospheric pressure at lower temperature. Biphenyl, fluorene, and 9,10-dihydroanthracene were selected because they were employed as model compounds in pioneering works [21,22,31]. To the best of our knowledge, there is no literature referring to any partial and complete aromatic ring reduction technique utilizing Al powder with these catalysts at lower temperature in water. In this article, we developed new method for partial and complete aromatic ring reduction using Al powder with commercially available Pd/C and Pt/C, respectively.
2 Experimental
2.1 Materials and apparatus
All melting points are uncorrected. 1H NMR spectra were recorded at 300 MHz on a Nippon Denshi JEOL FT-300 NMR spectrometer in CDCl3 with Me4Si as an internal reference. IR spectra were measured as KBr pellets on a Nippon Denshi JIR-AQ2OM spectrometer. Mass spectra were obtained on a Shimadzu GC–MS-QP5050A Ultrahigh Performance Mass Spectrometer AOC-20I, 100 V using a direct-inlet system. GLC analyses were performed with a Shimadzu gas chromatographer GC-2010.
2.2 General procedure for the reduction of aromatic compounds
To the mixture of substrate (20 mg, 0.13 mmol) (Wako), Al powder (500 wt%) (53–150 μm, 99.5%) (Wako) and Pt/C, Pd/C, Ru/C and Rh/C (20 mg) (4.5 mol% metal) was added water (0.5 mL) (Wako distilled water). After heating at 60–80 °C for 12–24 h, the mixture was cooled to room temperature. The solution was diluted with 1 mL of water and then stirred overnight at room temperature in a sealed tube. After 24 h, the solution was extracted with diethyl ether (2 mL × 3) following the reported procedures [32]. The organic layer was combined, dried with MgSO4, filtered through a cotton layer and concentrated in vacuum to give the corresponding hydrogenated product. The yields were determined by GLC analysis by using the standard compound (1,2,3,4-tetrahydronaphthalene) and the products were identified by GC–MS.
3 Results and discussion
In our present research work, we tried to reduce biphenyl without using any alkaline solution, isopropyl alcohol or any extra hydrogen pressure at lower temperature. To acquire the optimized reaction conditions (i.e. catalysts, reaction time and temperature), hydrogenation of biphenyl was carried out using Al powder at 60 °C for 12 h in water in the sealed tube; hydrogenation was not initiated. Prolonging the reaction time (24 h) and increasing the reaction temperature at 120 °C (12 h) afforded the same results. Hydrogenation proceeded in the presence of a co-catalyst (Pd/C, Rh/C, Pt/C or Ru/C); and the results are shown in Table 1 (Scheme 1).
Reduction of biphenyl (1a) by using Al powder in H2O in the presence of a co-catalysta,b.
Entry | Co-catalyst | Temp (oC) | Yield [%]d | ||
2a | 3a | Recovery 1a | |||
1 | None | 60 | 0 | 0 | 100 |
2 | Pt/C | 60 | 10 | 84 | 6 |
3 | Pt/C | 80 | 0 | 100 | 0 |
4 | Pd/C | 60 | 54 | 0 | 46 |
5 | Pd/C | 80 | 59 | 22 | 19 |
6 | Ru/C | 80 | 35 | 39 | 26 |
7 | Rh/C | 80 | 60 | 11 | 29 |
8c | Pd/C | 60 | 91 | 5 | 4 |
9c | Rh/C | 60 | 7 | 90 | 3 |
a Substrate: 20 mg (0.13 mmol), co-catalyst: 4.5 mol% (metal), Al powder: 100 mg (500 wt%), H2O: 0.5 mL.
b Conditions: time, 12 h.
c Conditions: time: 24 h.
d The yields were determined by GLC.

Reduction of biphenyl (1a) by using Al powder in H2O in the presence of a co-catalyst.
The benzene rings of biphenyl were reduced to afford a mixture of cyclohexylbenzene (2a) and cyclohexylcyclohexane (3a) in 10 and 84% yield, respectively, along with the recovery of biphenyl (1a) in 6% yield at 60 °C using Pt/C. Consequently, we have succeeded in reducing both benzene rings of biphenyl (1a) to obtain cyclohexylcyclohexane (3a) in quantitative yield by increasing the reaction temperature to 80 °C (Table 1; entry 3). When Pd/C and Rh/C were used as co-catalysts under the same reaction conditions, the partial reduction of biphenyl (1a) afforded cyclohexylbenzene in 54–60% yield (2a) along with the recovery of the starting compound (1a) (Table 1; entries 4,5,7). In the case of Ru/C, only 35% of the compound 2a was observed under the used reaction conditions. Thus, it could be noted that the Pt/C catalyst has a higher activity than Pd/C, Ru/C, and Rh/C (Table 1; entries 5–7).
For obtaining partial reduction of biphenyl using Pd/C and Rh/C, the reaction time was increased to 24 h. In the case of Pd/C, cyclohexylbenzene (2a) was obtained in 91% yield at 60 °C, while Rh/C afforded cyclohexylcyclohexane (3a) in quantitative yield under the same reaction conditions (Table 1, entries 8, 9). For the different catalytic activities of Pd/C and Rh/C, they showed different selectivities to reduce the benzene ring of biphenyl (1a).
We investigated the reduction kinetics using Al powder with the co-catalyst Pt/C, as it is the most powerful co-catalyst; the results are summarized in Table 2. We observed that the yield of the desired compound 3a was increasing with time. On the other hand, the maximum yield for 2a was found at 6 h (34%); after that, 2a was gradually converted to 3a with time, and quantitative yield was observed at 12 h.
Reduction of biphenyl (1a) by using Al powder in the presence of Pt/Ca,b.
Entry | Time (h) | Yield [%]c | ||
2a | 3a | Recovery 1a | ||
1 | 2 | 5 | 0 | 95 |
2 | 4 | 12 | 1 | 87 |
3 | 6 | 34 | 14 | 52 |
4 | 8 | 23 | 53 | 24 |
5 | 10 | 15 | 79 | 6 |
6 | 12 | 0 | 100 | 0 |
7 | 14 | 0 | 100 | 0 |
a Substrate: 20 mg (0.13 mmol), co-catalyst: 4.5 mol% (metal), Al powder: 100 mg (500 wt%), H2O: 0.5 mL.
b Condition: temperature: 80 °C.
c The yields were determined by GLC.
We also investigated the hydrogenation of diphenylmethane (1b) with Al powder in the presence of noble metal catalysts in water in the sealed tube under the same reaction conditions as those used in the case of biphenyl (1a). Both benzene rings of diphenylmethane (1b) were reduced with Al powder in the presence of Pt/C to afford bicyclohexylmethane (3b) in 88% yield along with the recovery of 7% of diphenylmethane (1b). Unfortunately, lower partial reduction products (2b) were observed when using Pd/C (28%), Ru/C (25%) and Rh/C (41%) as co-catalysts. This suggests that the lack of extended conjugation of diphenylmethane is responsible for the lower partial reduction (Scheme 2).
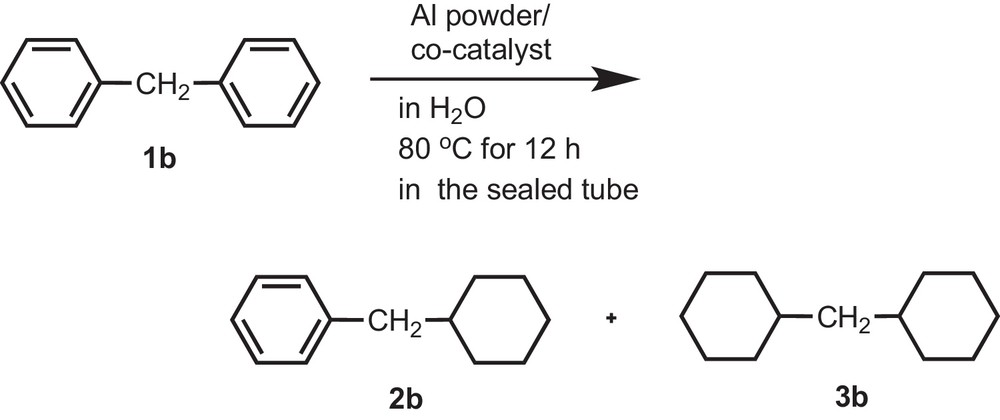
Reduction of diphenylmethane (1b) by using Al powder in H2O in the presence of a co-catalyst.
In the presently developed method, we have succeeded to reduce the benzene rings of biphenyl and diphenylmethane for the first time by using noble metal catalysts and Al powder in water under mild reaction conditions without using any organic solvent at lower temperature under atmospheric pressure. Maegawa et al. also reported the reduction of diphenylmethane and other aromatic compounds by using Rh/C (10 wt%) catalyst under high hydrogen pressure in isopropylalcohol as an organic solvent [22].
After that, we performed the partial reduction of various types of aromatic compounds with the Pd/C catalyst under the same reaction conditions (Table 3). It is noteworthy that biphenyl (1a) possesses a flexible skeleton, but the partial reduction proceeds in a high yield. In this case, benzene rings are not in the same plane. We observed that diphenylmethane converted to lower amounts of cyclohexylphenylmethane (2b) along with large amount of recovery. Diphenylmethane slightly comes up to Pd/C metal surface because the rapid rotation of two phenyl groups centers methylene group. To ensure this, we further examined diphenylethane (1c) under the same reaction conditions. The similar result was also obtained for one benzene ring reduction (2c, 45%) with recovery (55%) of the starting compound. In addition, fluorene (1d) and 9,10-dihydroanthracene (1e) afforded high yields of partial reduction of one benzene ring owing to their rigid structure. Sajiki et al. developed special Pd catalysts and these catalysts achieved unique chemoselective hydrogenations of alkyne, alkene and azide functionalities of benzene derivatives under hydrogen atmosphere at room temperature [24]. In our case, commercially available Pd/C with Al powder give the partial reduction of aromatic compounds where water is the proton source. Recently, Wang et al. developed new catalysts using Pd and observed selectivity in the hydrogenation of quinoline to 1,2,3,4-tetrahydroquinoline at mild temperatures (30–50 °C) and under H2 pressure (1 bar) [25]. But in our case, we did not apply extra hydrogen pressure to reduce the benzene ring.
Reduction of aromatic compounds (1) by using Al powder in the presence of Pd/Ca,b.
Entry | Substrate (1) | Product (2) | Yield [%]c,d | Recovery (1) |
1 | 91 [70] | 4 | ||
2 | 35 [25] | 65 | ||
3 | 45 [30] | 55 | ||
4 | 77 [52] | 16 | ||
5 | 90 [70] | 6 |
a Substrate: 20 mg, co-catalyst: 4.5 mol% (metal), Al powder: 100 mg (500 wt%), H2O: 0.5 mL.
b Conditions: temperature: 60 °C, time: 24 h.
c The yields were determined by GLC.
d Isolated yields are shown in square brackets.
We further investigated fused aromatic compounds, such as fluorene 1d, 9,10-dihydroanthracene 1e, anthracene as well as diphenylether 1f and diphenylamine 1g. The results are compiled in Table 4.
Reduction of aromatic compounds (1) by using Al powder in the presence of Pt/Ca,b.
Entry | Substrate | Product yield [%]c,d | Recovery (1a) | |
1 | 1a | 2a (0) | 3a (100) [90] | 0 |
2 | 7 | |||
3 | 11 | |||
4 | 0 | |||
5 | 13 | |||
6 | 4 (17) | 6 |
a Substrate: 20 mg, co-catalyst: 4.5 mol% (metal), Al powder: 100 mg (500 wt%), H2O: 0.5 mL.
b Conditions: temperature: 80 °C, time: 12 h.
c The yields were determined by GLC.
d Isolated yields are shown in square brackets.
Fluorene (1d) was treated under similar reaction conditions. From the figure (Supplementary data, ESI, Fig. S31), we found that the Ru/C catalyst is the most inactive for the hydrogenation of the benzene ring. Compared to biphenyl, both Rh/C and Pd/C are effective catalysts for fluorene reduction. The Pt/C catalyst has almost the same reactivity as that of the biphenyl (1a). It is also reported that fluorene (1d) is converted principally into hexahydrofluorene (3d) over Pd–Al2O3 (71% yield) and into perhydrofluorene over Rh–Al2O3 (72% yield) in decalin at 200 °C and 7 MPa H2 [33]. Pt–Al2O3 showed a much lower activity under the same conditions. Treatment of fluorene (1d) with Raney Ni under refluxing toluene in the presence of triethylamine leads to the exclusive formation of cis-hexahydrofluorene [34]. After that, 9,10-dihydroanthracene and anthracene were treated with the metal catalysts under the same conditions as those described above. In the case of 9,10-dihydroanthracene, we obtained 97% yield of the reduction product (3e) of both benzene rings. Unfortunately, lower yields were obtained from anthracene in these conditions. The yields of tetradecahydroanthracene (3e), octahydroanthracene (2e), and 9,10-dihydroanthracene (1e) were 43.4%, 49.4%, and 1.2%, respectively, with 6% recovery of anthracene. When the reaction time was increased to 24 h at 80 °C, tetradecahydroanthracene (3e) in 97% yield and octahydroanthracene (2e) in 3% yield were obtained. It is also reported that anthracene is hydrogenated over copper–chromium in ethanol at 100 °C or in decalin at 150 °C applying extra hydrogen pressure through the formation of 9,10-dihydroanthracene [35,36].
Furthermore, we tried to reduce heteroatom-containing aromatic compounds diphenylether and diphenylamine using Al powder with Pt/C. In our conditions, diphenylether gave a small amount of benzene ring reduction, but it produced cyclohexanol in higher yield. Interestingly, in the case of diphenylamine, we achieved a higher yield of dicyclohexylamine along with cyclohexylamine and cychohexanol under mild reaction conditions, as previously reported [37].
Finally, we examined the substituent effect of biphenyl to obtain the complete reduction product by using Al powder with Pt/C under the same reaction conditions. We obtained high yields (83%) of the reduction product of the benzene ring with cis and trans products for 4-methylbiphenyl. In the case of 4-methoxy- and 4-tert-butylbiphenyl, the yield of 3 decreased to 20 and 45% yield. In fact, for 4-methoxybiphenyl, we have also observed the formation of compounds 1a, 2a and 3a under the conditions used. These results strongly suggest that the presently developed reducing agent not only reduces the benzene ring, but also cleaves the polar C–O bond. In the case of 4-tert-butylbiphenyl comparatively higher yields (48%) of 4-tert-butylcyclohexylbenzene were obtained. Because of the steric effect of the tert-butyl group, the benzene ring directly attached to it cannot be easily reduced on the catalyst's surface. We also observed only one compound, which is 4-tert-butylcyclohexylbenzene, by spectroscopic analysis. We can assume that another benzene ring, which bears no tert-butyl group, can be easily reduced; chemoselectivity was observed. Moreover, as tert-butyl group is a bulky group, the tert-butyl substituent cannot approach parallel to the metal surface to give high yields of the reduction product of both benzene rings. From these results, we can conclude that the approach of the substituted biphenyl towards the highly porous surface of the Pt metal catalyst depends on the substituent (Scheme 3 and Table 5).

Reduction of substituted biphenyls (1a) and (1h–1j) by using Al powder in the presence of Pt/C.
Reduction of substituted biphenyls (1a) and (1h–1j) by using Al powder in the presence of Pt/Ca,b.
Entry | Substrate (1) | Yield [%]c | ||
2 | 3 | Recovery 1 | ||
1 | H | – | 100 | – |
2 | CH3 | 11 | 83d | 6 |
3 | OCH3 | 30 | 23d | 8 |
4 | C(CH3)3 | 48 | 45d | 7 |
a Substrate: 20 mg (0.13 mmol), co-catalyst: 4.5 mol% (metal), Al powder: 100 mg (500 wt%), H2O: 0.5 mL.
b Conditions: temperature: 80 °C, time: 12 h.
c The yields were determined by GLC.
d cis- and trans-isomers were obtained.
4 Conclusion
In conclusion, we have developed an efficient and practical method of hydrogenation of aromatic compounds using Al powder with a noble metal catalyst in water under mild reaction conditions. Without using any organic solvent, Al powder with Pd/C is effective for the selective hydrogenation of one benzene ring and Al powder with Pt/C gives the complete hydrogenation of aromatic compounds. The hydrogenation product yields strongly depended upon the temperature, volume of water and amount of the metal catalysts used. Our hydrogenation process is operationally simple and no harsh reaction conditions (i.e. elevated temperatures, high pressures, a hydrogen atmosphere, an inert gas atmosphere or special apparatus) are required.
Acknowledgement
This work was performed under the Cooperative Research Program of the “Network Joint Research Centre for Materials and Devices (Institute for Materials Chemistry and Engineering, Kyushu University)”.