1 Introduction
Porous materials have experienced a great development in various fields of application [1]. Among these porous materials, the M41S family, which was discovered at the beginning of the 1990s by researchers from Mobil and which is composed of three materials (MCM-41, MCM-48 and MCM-501) [2,3]. This class of material has a uniform pore size distribution in the mesoporous range, which is tunable between 2 nm and 10 nm, a high specific surface area of up to 1500 m2/g, and a high porosity (< 1 cm3/g). These proprieties lead the M41S family and especially MCM-41 which is the best studied member to be used in catalyst [4] and for adsorption purposes [5]. Several studies proposed to convert the coal fly ash by hydrothermal activation methods into zeolites using alkaline solutions (mainly NaOH and KOH solutions), which is analogous to the formation of natural zeolites from volcanic deposits [6]. Most of the zeolites synthesized by this conversion process contain a non-converted part of fly ash and not all aluminum silicate phases were converted [7]. For the first time, an alkaline fusion process was introduced to synthesize conventional zeolites similar to chabazite or mordenite [8]. This method improved the conversion rate of aluminum silicate phases and resulted in very interesting types of zeolites. MCM-41 and SBA-15 (Santa Barbara amorphous – 15) with a specific surface area of 842 m2/g and 483 m2/g, respectively, were obtained from coal fly ash using the fusion method [9]. Kang et al. [10] reported the synthesis of Al-MCM-41 by using water glass (or silicate sodium) as a Si source and metakaolin as the only Al source. Recently, Adjdir et al. [11] and Ali-dahmane et al. [12] reported the synthesis of Al-MCM-41 by using Volclay® and Algerian bentonite, respectively, as sources of both aluminum and silica. They adopted the alkaline fusion and water treatment of fused clay (resulting from 1:4, fusion mass:H2O; weight ratio) to synthesize an Al-MCM-41 nanomaterial. In this contribution, the weight ratio of fusion mass:H2O was increased to 1:8, to synthesize a highly structurally ordered MCM-41 under the same reaction conditions. In addition, glass tubes instead of autoclaves have been utilized to increase the rate of reaction by reducing the volume and increasing the saturated pressure compared to the situation in an autoclave. The original materials employed and the entire design of this MCM-41 production process is cheaper and hence more cost effective than the previously known practices.
2 Experimental
2.1 Starting materials
The Volclay used in this study is comprised mainly of smectite (dioctahedral) and was obtained from Südchemie AG, Germany (Table 1) [13].
Mineral phase content of Volclay (wt%).
Phases | Sample Volclay (wt%) |
Smectite (Na-rich di) | 60.0 ± 4.2 |
Smectite (Ca-rich di) | 19.8 ± 3.6 |
Muscovite/illite | 2.8 ± 0.9 |
Quartz | 4.4 ± 0.5 |
K-feldspars (orthoclase) | 4.0 ± 0.9 |
Plagioclase (albite) | 4.1 ± 0.8 |
Calcite | 1.3 ± 0.4 |
Gypsum | 3.6 ± 0.6 |
Its chemical composition is given in Table 2.
Elemental weight compositions of Volclay (%).
Wt% | SiO2 | Al2O3 | Fe2O3 | TiO2 | CaO | MgO | Na2O | K2O | MnO | P2O5 | LOI |
Volclay | 56.50 | 18.56 | 3.56 | 0.15 | 1.14 | 2.26 | 1.88 | 0.52 | 0.01 | 0.04 | 15.4 |
The other reactants employed in this study were cetyltrimethylammonium bromide (C19H42NBr; CTAB, Aldrich; 99%) as the surfactant, ammonium hydroxide, 25% (NH3, 99.99%, Aldrich), and acetic acid min. 99.8% (Aldrich).
2.2 Synthesis of Al-MCM-41
To extract the Si and Al needed to synthesize Al-MCM-41 from Volclay, a fusion process at 550 °C during 1 h was adopted; it consisted of a treatment of sodium hydroxide with Volclay. Two kinds of sodium hydroxide, powder and pastilles, which exhibit a marked difference in their prices (powder is expensive than pastilles), were used. Sample A was a 1:1.2 mixture of Volclay:NaOH pellets and the second sample B was a 1:1.2 Volclay:NaOH powder mixture. In addition, an appropriate concentrated sodium hydroxide solution was mixed with 1 g of Volclay and stirred for several hours at room temperature (sample C). The Al-MCM-41 was synthesized by using a supernatant derived from sample A. The supernatant was obtained by the fusion process at 550 °C for 1 h. Volclay was treated with sodium hydroxide (pellet) in a ratio of 1:1.2, Volclay:NaOH and heated at 550 °C to obtain a fusion mass that was cooled at room temperature overnight. The powder fusion samples were mixed with water (1:8, fusion mass:H2O weight ratio) and stirred for 1 day at room temperature. After centrifugation of the mixture for 10 min, a liquid solution obtained from the water treatment was analyzed; its elemental composition is given in Table 3.
Elemental compositions of supernatant 1 (sup-1) and supernatant (sup-2) determined by ICP–OES.
Elements | Sup-1a (mg/L)* | Sup-2b (mg/L)* | Yield (%) |
Si | 881.90 | 1060.40 | 20.24 |
Al | 64.60 | 65.30 | 1.08 |
Na | 4758.11 | 6622.42 | 39.18 |
a Supernatant 1 with weight ratio (1:4, fusion mass:H2O) [11].
b Supernatant 2 with weight ratio (1:8, fusion mass:H2O).
According to the ICP–OES data of the supernatant with weight ratio 1:8, the synthesis procedure of Al-MCM-41 was as follows. 0.867 g of cyltrimethylammonium bromide (C16TMABr), 15 mL water and 0.75 g NH4OH were combined with 40 mL of the supernatant and stirred at room temperature during 1 h at pH 9.5, while acid acetic was added. The hydrogel was treated at 100 °C in a glass tube instead of an autoclave for 48 h. The material obtained was calcined at 550 °C (heating rate of 2 K/min) for up to 6 h under N2 gas to remove the surfactant (C19H42N+) from the pores of Al-MCM-41.
3 Characterization
An inductively coupled plasma optical emission spectrometer (ICP–OES) was used to determine the elemental composition of both supernatant solutions. The formation and the structure of Al-MCM-41 was checked by XRD. Diffraction patterns were recorded in the 2θ range from 1 to 70° with a step of 0.02° 2θ and a step time of 5 s on a Bruker D5000 diffractometer with Cu Kα radiation (λ = 1.5406 Å, 40 kV, 40 mA). A talc/vermiculite mixture was added as an internal standard. For the peak positions, the ICCD files 083-1768 for talc, 076-0847 for vermiculite, 04-010-1394 for Na2SiO3 () and 04-002-8210 NaAlO2 (*) were applied. N2 gas sorption measurements were performed at 77 K with a Quantachrome Autosorb1 MP. The samples were degassed at 383 K in vacuum for 24 h before measurements. Specific surface areas were calculated by using the BET isotherm [14]. The pore size distribution curves were calculated using the NLDFT equilibrium model with a cylindrical pore shape based on the DFT/Monte-Carlo method. Pore volumes were obtained from the amount of N2 adsorbed at p/po = 0.7, corresponding to a pore width of 7.1 nm in order to exclude interparticle pores formed by the powder particles. Possible differences in particle morphology and of the grain-size distribution stemming from the different production processes was carried out by environmental scanning electron microscopy (ESEM) using a Philips ESEM XL 30 FEG. This kind of SEM uses a chamber atmosphere of 1–3 Torr water vapour instead of high vacuum.
4 Results and discussion
4.1 Inductively coupled plasma optical emission spectrometer (ICP–OES)
The results of the ICP–OES analysis of both supernatants are shown in Table 3. Differences were found between supernatants resulting from weight ratio of fusion mass:H2O from 1:4 to 1:8. While the weight ratio of fusion mass:H2O of 1:8 gave significant proportions of its different constituents (Si = 1060.40 mg/L and Al = 65.30 mg/L), reduced amounts of the same elements are found with weight ratio 1:4 (Si = 881.90 mg/L and Al = 64.60 mg/L). The increase in the weight ratio of fusion mass:H2O increases silica and aluminum extraction. A significant increase is found with weight ratio 1:8, which reached 20.24% for silica and 1.08% for aluminum. This result is in agreement with the XRD pattern in Fig. 1 where the peaks that characterize sodium silicon oxide are found lower than those that characterize the sodium aluminum oxide. This result clarifies the huge amount of silicon extracted by the alkaline fusion process compared to the amount of aluminum extracted by the same process.
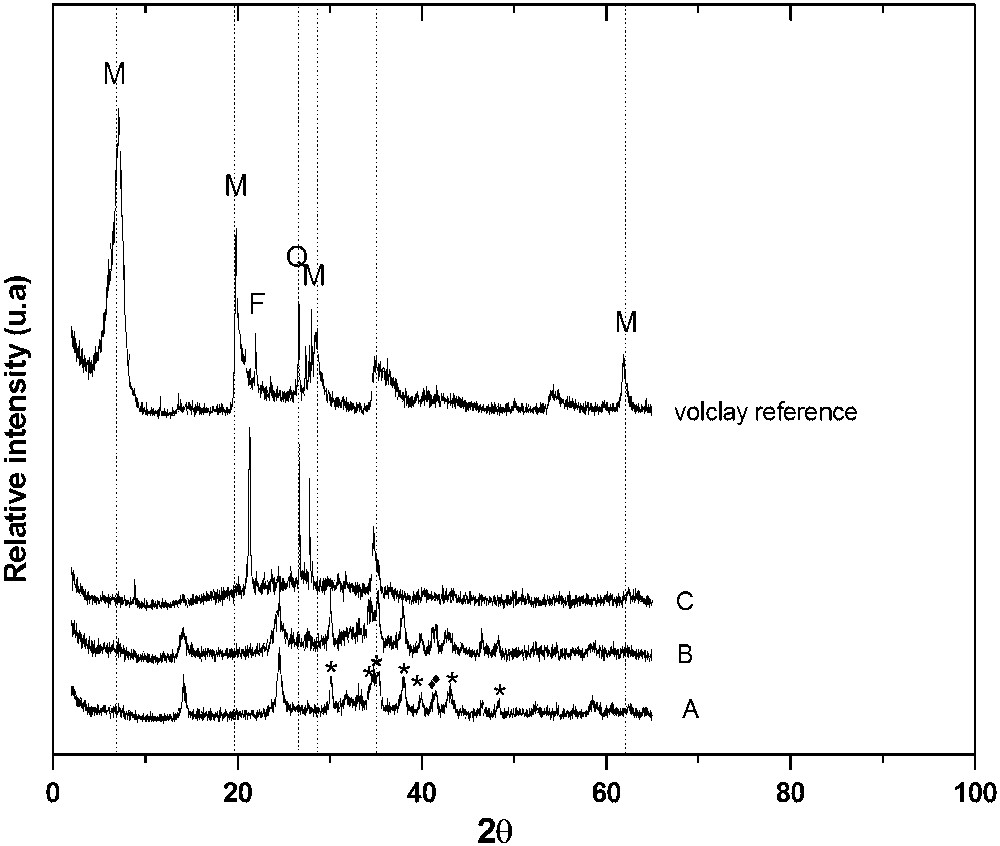
XRD patterns of volclay as reference, A 1:1.2 volclay:NaOH pellets, B 1:1.2 volclay:NaOH powder and C Volclay:NaOH 2 M; (M) montmorillonite, (F) feldspars, (Q) quartz and (Mus) muscovite, () 04-010-1394 for Na2SiO3 and (*) 04-002-8210 NaAlO2.
4.2 X-ray diffraction
Fig. 1 revealed that the major mineralogical compositions that exist in Volclay are montmorillonite, quartz and muscovite-illite (Table 2). The silica (SiO2) content in Volclay is predominant, and is about 56.50%, followed by that of alumina (Al2O3), which is 18.56%. Hematite (Fe2O3) was found to be the third in terms of abundance, with an average of 3.56%. The two clay minerals muscovite-illite and K-feldspars were dominant, and non-clay minerals, referred to as “impurities”, were found, including quartz (Fig. 1). The disappearance of the peaks that characterize montmorillonite, muscovite-illite and quartz confirms that the alkaline fusion of Volclay dissolved all of these species and give rise to the precipitation of sodium silicate (Fig. 1A and B), except for sample C (Volclay + NaOH 2 M) (Fig. 1C). This incomplete dissolution of quartz and montmorillonite was also described by Morino et al. [7]. The low-temperature alkaline fusion process using sodium hydroxide generates new phases called sodium silicate [Na2SiO3, Eq. (1)] and sodium aluminate [NaAlO2, Eq. (2)].
The chemical equation describing this process is:
2NaOH + SiO2 → Na2SiO3 + H2O | (1) |
2NaOH + Al2O3 → 2NaAlO2 + H2O | (2) |
Based on a previous work, Adjdir et al. [11], referring to EDAX data expressed in percentages, concluded that there was a wide variation in the chemical constituents of fused Volclay, in which silicon is much higher than aluminum. This result indicates that large amounts of silicon and aluminum remain in the fused Volclay (they are not extracted from it). Based on this result, the weight ratio between fused mass and water is increased from 1:4 to 1:8. Referring to ICP–OES analysis (Table 3), this increase in water leads to an increase in the silicon and aluminum amounts extracted from the fused Volclay. The major amounts of silicon and aluminum extracted from the fused Volclay were consumed to produce Al-MCM-41 and result in higher amounts of aluminosilicate nanomaterials, which reach 9.3 g of Al-MCM-41 obtained from a weight ratio of fusion mass:H2O of 1:8, and 5 g of Al-MCM-41 obtained with weight ratio 1:4 (Table 4).
Structural properties of the samples.
Sample | a0 (nm) | FWHM (°) | Si/Al | SBET (m2/g) | Vmeso (cm3/g) | DDFT (nm) | Dp (nm) | bp (N2) (nm) | bp (XRD) (nm) | Weighta (g) |
Al-MCM-41 1:4 | 4.53 | 0.295 | 15 | 1060 | 0.72 | 3.78 | 3.85 | 0.72 | 0.65 | 05 |
Al-MCM-41 1:8 | 4.41 | 0.128 | 162 | 1044 | 0.70 | 4.25 | 3.67 | 0.16 | 0.74 | 9.3 |
a The weight was calculated referring to the same mass weight of volclay/NaOH for both nanomaterials.
The characteristic reflection (100) was observed in the low-angle X-ray patterns, which is characteristic of a hexagonal pore structure typical of Al-MCM-41 [15]. Moreover, appreciable characteristic reflections (110), (200) and (210) were observed, which show a better structuring of the hexagonal channels of Al-MCM-41 [3]. A high Na+ ion concentration in the initial solution is known to promote the formation of zeolites and hinder the formation of MCM-41 phases [16]. Under strong alkaline conditions, the silicon precursor was highly negatively charged, the electrostatic interaction between positive template and negative charged silicon species was too strong to form a stable mesoporous silica material structure. The adjustment of the pH has a direct impact on formation of a well-ordered material. Adjdir et al. [11] found that an adjustment of the solution pH by an acid is very important for the effective formation of uniform mesopores; however, the acid should be added into the mixture solution after the addition of a surfactant; otherwise, the formation of an ordered mesoporous structure would be affected. The explanation is that when an acid is added to a mixture without surfactant, the pH of the system will be reduced and will influence the interaction between anionic and cationic surfactant species in the silicate and aluminate mixture, leading to a poor polymerization of inorganic silicate and aluminate species. The powder XRD patterns of the Al-MCM-41 calcined samples resulting from weight ratios 1:8 and 1:4 weight ratios are depicted in Fig. 2. The XRD pattern exhibits the same peaks and consists of one very strong peak and three weak peaks corresponding to (100), (110), (200), and (210) reflections at 2θ values ranging from 2° to 6°. Referring to the XRD of both samples, it is deduced that the sample synthesized from weight ratio 1:8 presents a better ordered structure compared to the one resulting from weight ratio 1:4. This can be attributed to the higher aluminum content in the sample with weight ratio 1:4 (Si/Al 13.64) compared to that with weight ratio 1:8 (Si/Al 16.23). Adjdir et al. [17] found that when the aluminum content in the silicate framework increases, the crystallinity of this sample decreases. This approach is confirmed by the FWHM (full width and half maximum) of both samples; in the case of MCM-41 from the sample with weight ratio 1:4, the FWHM has a value of 0.295; however, the FWHM of MCM-41 resulting from weight ratio 1:8 is 0.128°.
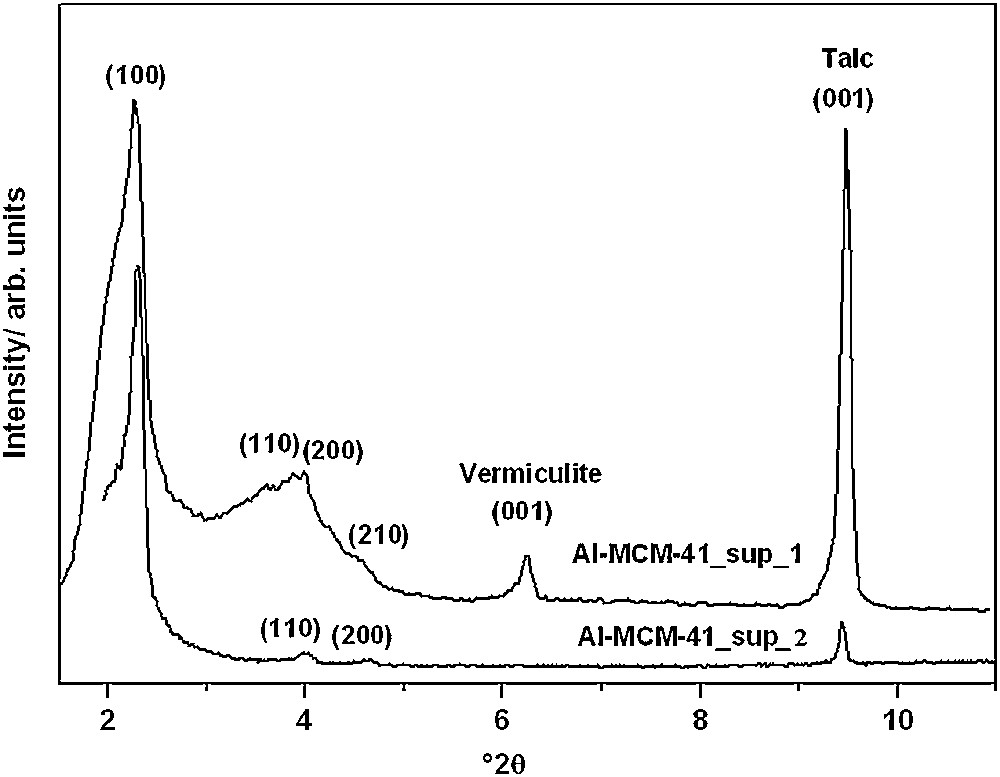
XRD pattern of Al-MCM-41 synthesized from supernatants 1 and 2; a talc/vermiculite mixture was applied as an internal standard for peak position correction.
4.3 N2-sorption
Fig. 3 shows the N2-sorption isotherm of Al-MCM-41 resulting from weight ratios 1:4 and 1:8. Table 4 summarizes the textural properties of both samples. The obtained isotherms are typical of the Al-MCM-41 phase. The corresponding isotherm is of type IV, characteristic of the mesoporous solids according to the IUPAC nomenclature [18]. The type-IV isotherm is defined by three stages: at low relative pressures, a slow increase in nitrogen corresponding to a monolayer–multilayer adsorption on the pore walls. At intermediate relative pressures, a sharp step is indicative of capillary condensation within mesopores. In the last stage, at high relative pressures, a final plate with a slight inclination associated with multilayer adsorption on the external surface of the particles. The isotherm presents a sharp capillary condensation step at p/po 0.3, typical of a uniform mesoporous material with pore sizes of around 3.85 nm and 3.67 nm (Fig. 4), which correspond to Al-MCM-41 resulting from weight ratios 1:4 and 1:8, respectively. The specific surface area of Al-MCM-41obtained from weight ratios 1:4 and 1:8 were 1060 m2/g and 1044 m2/g, with a pore volume of 0.72 cm3/g and 0.70 cm3/g, respectively, calculated at 0.42 p/p0. This p/p0 value was chosen to eliminate the adsorbate volume that can occur between the platy particles.

N2 adsorption–desorption isotherm of MCM_sup_1 () and MCM_sup_2 (). Full symbols, adsorption; open symbols, desorption.
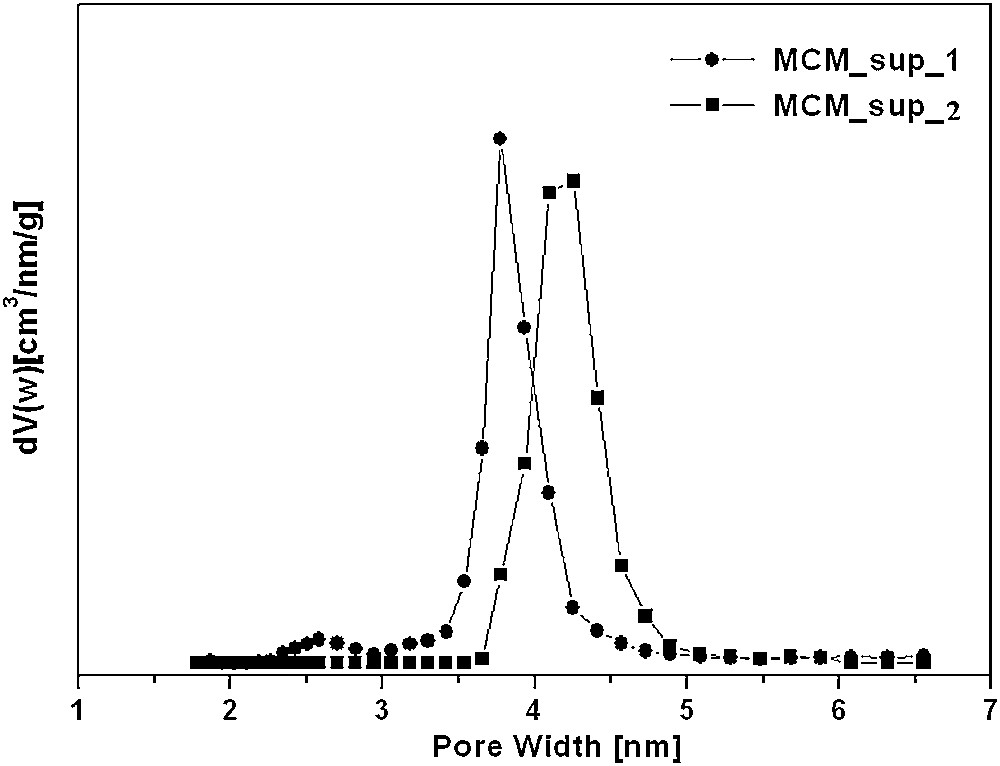
Pore size distributions of MCM_sup_1 and MCM_sup_2 derived from N2 adsorption isotherms calculated by the Monte-Carlo method.
4.4 Environmental scanning electron microscopy
The SEM images of the particle morphologies of the Al-MCM-41 samples synthesized from the laboratory reagents Ludox as silicon sources and sodium aluminate as aluminum sources (a, b), resulting from weight ratios 1:8 (c, d) and 1:4 (e, f), are shown in Fig. 5. It was found that the Al-MCM-41 worm-like particles obtained from laboratory-grade reagents are present in the morphology of Al-MCM-41 resulting from weight ratio 1:8; the acid treatment favors the formation of covalent Si–O–Si bonds within and between the silica walls of the mesostructure during the synthesis. This strengthening of the silica walls leads to the observed improvement in the long-range ordering and hydrothermal stability [19]. In contrast, no worm-like particles are found in the sample derived from weight ratio 1:4. The major difference between these three samples is their Si/Al ratio. The first two samples show a high ratio of around 50 for the laboratory-grade reagents (a, b) [17] and 162 for weight ratio 1:8 (c, d) processed samples, whereas samples synthesized using weight ratio 1:4 exhibit a Si/Al ratio of 15 (e, f) [11]. This indicates a strong influence of the aluminum content on morphology. Aluminum seems to block the Si polymerization sites, thus leading to a reduced growth in all dimensions. This finding is supported by the low values of the line width of the (100) peak around 0.128 compared to that of the sample resulting from weight ratio 1:4 around 0.295°, favoring a worm-like particle arrangement of the mesoporous channels for samples with a low Al content, as those present in the supernatant. Nevertheless, the co-existence of some aggregations of spherical particles is shown in all samples.
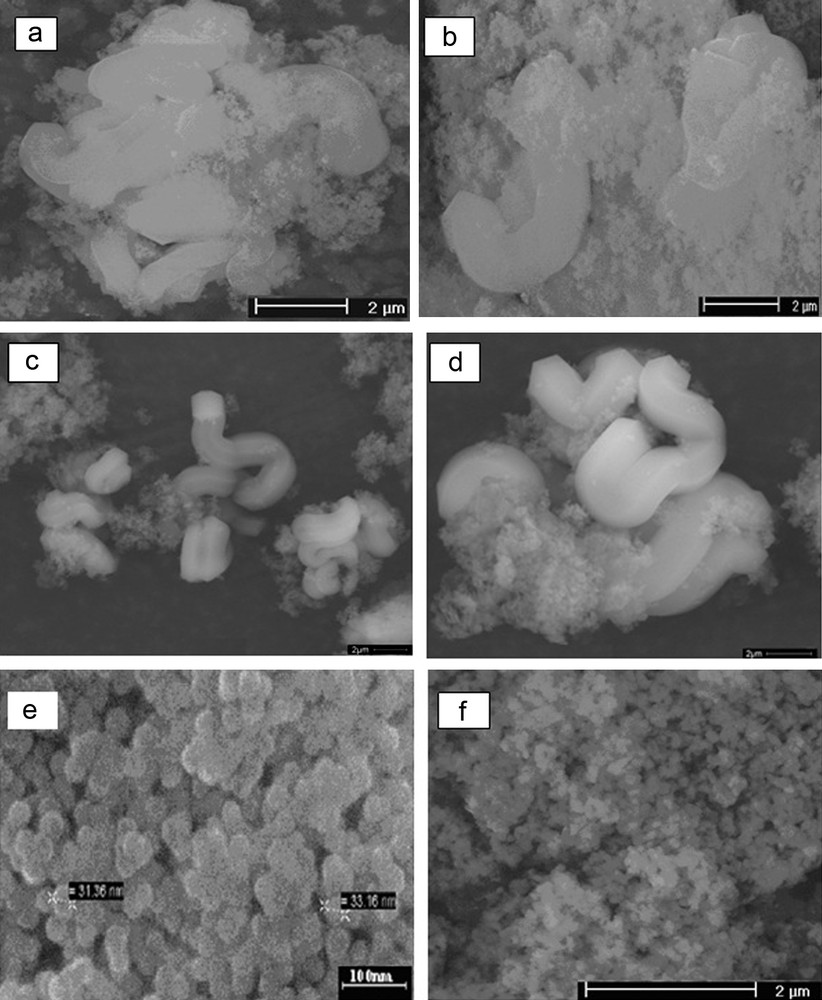
SEM of Al-MCM-41 (a, b) samples synthesized by the standard method, (c, d) and (e, f) for samples synthesized with weight ratios 1:8 and 1:4, respectively.
5 Conclusion
The form and the quality of sodium hydroxide do not play any role in alkaline fusion. The increase in the water treatment ratio is adequate to extract more silica and aluminum from fused Volclay. The physical properties of Al-MCM-41 resulting from weight ratio 1: 8, such as pore diameter (around 3.67 nm), pore volume (around 0.70 cm3/g), and SBET (around 1044 m2/g) are similar to those of the Al-MCM-41 resulting from weight ratio laboratory-grade reagents. No impurities from clay are observed in the final Al-MCM-41 nanomaterials. The amount of Al-MCM-41 resulting from 1:8 weight ratio is much higher than that from the sample with weight ratio 1:4 (around 9.3 g and 5 g, respectively). As a conclusion, the alkaline fusion and appropriate water treatment of clay is key to replacing laboratory-grade reagents in the synthesis of most nanomaterials, not only MCM-41, and therefore, their production cost can be strongly reduced.
Acknowledgments
The author (M.A) gratefully acknowledges the financial support of the German Academic Exchange Service (DAAD). The author (M. K) thanks Fundação para a Ciência e a Tecnologia (FCT) for Grant N°. SFRH/BPD/74477/2010. Special thanks are addressed to Heinle Marita for ICP–OES analysis.
1 Mobil Composition of Matter.