1 Introduction
Biodiesel is defined as the mono alkyl esters of fatty acids without aromatics; its low SOx content has revealed its promise as an alternative fuel for diesel engines [1,2], and now it has been used as blended with diesel. Conventionally, biodiesel is produced by transesterification of glycerol triglyceride with short-chain alcohols, such as methanol and ethanol, in the presence of inorganic homogeneous base catalysts, which results in many problems, such as the recovery of the catalysts and the treatment of wastes [3,4]. Transesterification using heterogeneous catalysts has been established to simplify the process of catalyst separation from liquid products and eliminate large consumption of water [5,6]. However, a by-product, crude glycerol, produced in the conventional transesterification process in excessive amounts, is an oversupplied chemical, as biodiesel production has kept growing in recent years. The current utilization of glycerol is not efficient enough to support its predicted increase. Therefore, it becomes imperative to find new convenient uses for glycerol and more perspectives for increasing the economy of biodiesel production [7]. With this purpose, alternative strategies to transform glycerol into high-value glycerol derivatives are under investigation, and some new technologies for the use of glycerol have been developed, such as glycerol hydrochlorination and dehydration of glycerol to acrolein [8].
Recently, great interest has risen to promote the economic feasibility of the use of glycerol in biodiesel production by using DMC, an eco-friendly and chemical reactive reagent, as an acyl acceptor for transesterification to produce biodiesel and glycerol carbonate (GC) simultaneously [9,10]. By this new transesterification process, glycerol carbonate with higher commercial value, instead of glycerol, is obtained as a by-product. Fabbri et al. prepared biodiesel and GC simultaneously from transesterification between soybean oil and DMC by utilizing NaOH as a catalyst [11]. In this work, a high soybean oil conversion rate, 99%, was obtained at 90 °C after 6 h, but it suffers from tedious separation and purification procedures. Consequently, Saka and Tan conducted a non-catalytic DMC process to produce biodiesel and GC by using supercritical DMC technology under critical reaction conditions [12,13]. The transesterification rate between oil and DMC is accelerated dramatically and it is easy to get a high yield of FAME over 97% in less than 30 min [14]. However, its large-scale application is limited, due to the high temperature and pressure needed, since 350 °C and 17.8 MPa are required. Furthermore, in this procedure, the yield of FAME goes on decreasing with the reaction time due to its poor thermal stability under high temperatures and pressures. In recent years, biocatalytic production of biodiesel in mild reaction conditions has attracted much attention to overcome the problems encountered with the chemical method. Min and Lee employed lipase to perform biodiesel biosynthesis and GC from corn oil and DMC [15]. Although a high yield of biodiesel, nearly 94%, is attained, and although good stability of lipase with over 80% yield of FAME after seven recycling operations is observed, large dosage of enzymes (75–100 g/l) and long reaction times (24–48 h) limit its wide application [16,17].
Typical transesterification for biodiesel production from oil and methanol is catalyzed by basic catalysts, and solid bases such as CaO and CaO-supported catalysts have been used to avoid the problem caused by catalyst separation [18,19]. Among all kinds of solid bases, CaO has exhibited excellent catalytic performance with yields of over 92% of FAME after 4–6 h at 65 °C, which contributed to its strong basicity and low cost [20,21].
In this paper, in order to develop a new efficient process for biodiesel production without any issue concerning the crude glycerol by-product under mild reaction conditions, a new coupling transesterification process was designed and applied to prepare biodiesel and GC. The effects of individual reaction parameters and their interactions with the yield of FAME have also been screened to obtain the optimum reaction conditions. Some of the major biodiesel properties were measured according to the European standard EN 14214 at last.
2 Method
2.1 Materials
Rapeseed oil was purchased from a coal market (Xi’an, China). Before the reaction, the oil was treated by sodium hydroxide and bentonite; after that, the acid content lowers to less than 1 mg KOH/g and the water concentration is below 1 mg/g. Analytical-reagent-grade dimethyl carbonate, methanol, and CaO were purchased from Sinopharm Chemical Regents Co., Ltd. (Beijing, China), and used without further purification.
2.2 Catalytic testing
For transesterification, a given amount of commercial CaO catalysts was added into the mixture of methanol, rapeseed oil and dimethyl carbonate in a three-necked round-bottomed flask equipped with a reflux condenser and a thermometer. The mixture was heated at a certain temperature under stirring and samples were taken out from the reaction mixture every 1 h. Then, the catalyst was separated by centrifugation and the excess methanol was distilled off under vacuum.
2.3 Product analysis and fuel properties of biodiesel
The FAME yield was defined as the ratio of the weight of FAME determined by GC (HP-6890) to the weight of fatty acid methyl esters that the oil used in the reaction, assuming that only traces of esters were transferred to the polar phase and that the extraction of methanol and glycerin only takes place. The products were analyzed by GC equipped with an HP-5 capillary column using an inner standard method. The nitrogen was used as a carrier gas at a flow rate of 20 mL/min. The oven temperature was kept at 280 °C in isothermal conditions [18–20]. The relative density of FAME at 15 °C was determined using an Anton Paar density meter (DMA 4500 M). The cloud, pour points and flash point were determined using the ASTM standard test methods.
3 Results and discussion
3.1 Design of bitransesterification for no-glycerol biodiesel production
As suggested by Fabbri et al. [11], the transmethylation reaction of vegetable oil and DMC under mild reaction conditions (90 °C, 5 h, 5% catalyst) only effectively proceeds over the base catalyst, while the heterogeneous catalysts tested in their study (hydrotalcite, titanosilicate, and zeolite) provided less than 5% conversion of triglyceride under the same conditions. Similarly, in our research, 65 °C, normal pressure and 15% CaO catalyst, the transesterification between vegetable oil and DMC has hardly any possibility to take place. But a comparable FAME yield of 84.5% was obtained when CaO was replaced with KOH. However, the separation of biodiesel is very complex due to the serious saponification caused by KOH. In contrast, the clear phase surface between CaO and the product is in favor of a consequent separation process.
The transesterification of vegetable oil and methanol is well known to be proceeded rapidly over a solid base, such as CaO, to produce FAME and glycerol under mild reaction conditions [22–24]. Additionally, previous reports have revealed that CaO also exhibits good catalytic performance in the transesterification of DMC and glycerol, showing a yield of over 97% of glycerol carbonate after 1 h under refluxing at normal pressure [25]. Therefore, a new method for producing no-glycerol biodiesel under mild reaction conditions can be designed by integrating the two transesterifications above, successively using a tri-component (methanol, oil and DMC) as reactants over CaO. The new reaction was named “coupling transesterifications”.
Based on the easy formation of methoxide over the CaO surface when mixing methanol with CaO as suggested by Liu et al. [26], the reaction mechanism of the coupling transesterifications could be proposed as follows. In the first step, the methoxide attracts the carbonyl group of rapeseed oil to form FAME along with a by-product, glycerol, as suggested in Fig. 1. In the second step, the O2−of CaO can also extract an H+ from the hydroxyl group of glycerol, and then it attracts the carbonyl group of DMC to form GC and methanol. The overall reaction can be expressed by Eqs. (1) and (2). As a result, the conversion of rapeseed oil is enhanced by activating and converting glycerol to GC, which shifts the transesterification of methanol and rapeseed oil (Eq. (1)) favorably to give high FAME yields. On the other hand, methanol is regenerated from the subsequent reaction between glycerol and DMC. Then, high consumption of methanol to ensure high conversion of rapeseed oil can be reduced in this new method consequently.
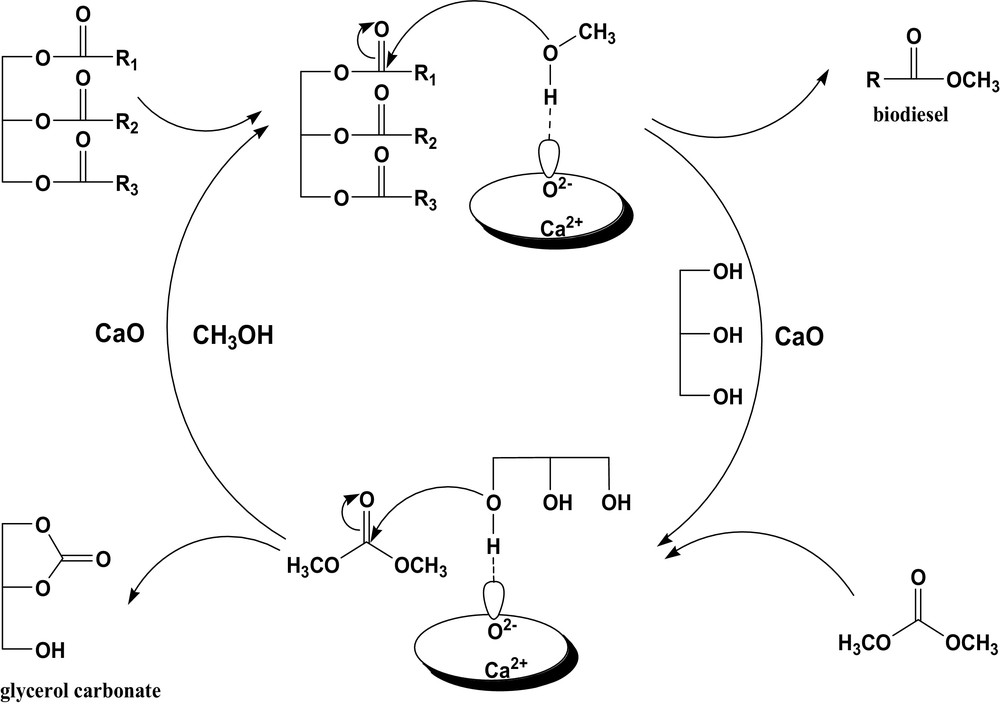
New processes for no-glycerol biodiesel production catalyzed by CaO.
3.2 Optimization of reaction parameters
In the proposed process, methanol can be regenerated over CaO; so it is confirmed that the amount of methanol plays an important role in the yield of FAME. Fig. 2 shows the effect of the methanol amount on the FAME yield at a DMC/rapeseed oil ratio of 1:1 with various molar ratios of rapeseed oil/DMC/methanol from 1:1:1 to 1:1:12. It can be found that the yield of FAME increases proportionately with the amount of methanol, which is similar to the trend in traditional biodiesel preparation methods and, therefore, a high mole ratio of methanol to rapeseed oil could be necessary to shift the transesterification between rapeseed oil and methanol equilibrium towards FAME formation. However, it should be noted here that the methanol-to-oil ratio providing the highest yield of FAME, 92.6%, is 8:1, which is much lower than that in traditional transesterification processes catalyzed by CaO, where an excess amount of methanol, much higher than 15:1, is needed to drive the reaction in favor of a higher yield of FAME [22]. It should be attributed to the integration of two transesterifications, methanol and rapeseed oil, glycerol and DMC, together, which results in promoting the transesterification between rapeseed oil and methanol towards the desired direction, as suggested in Fig. 1.
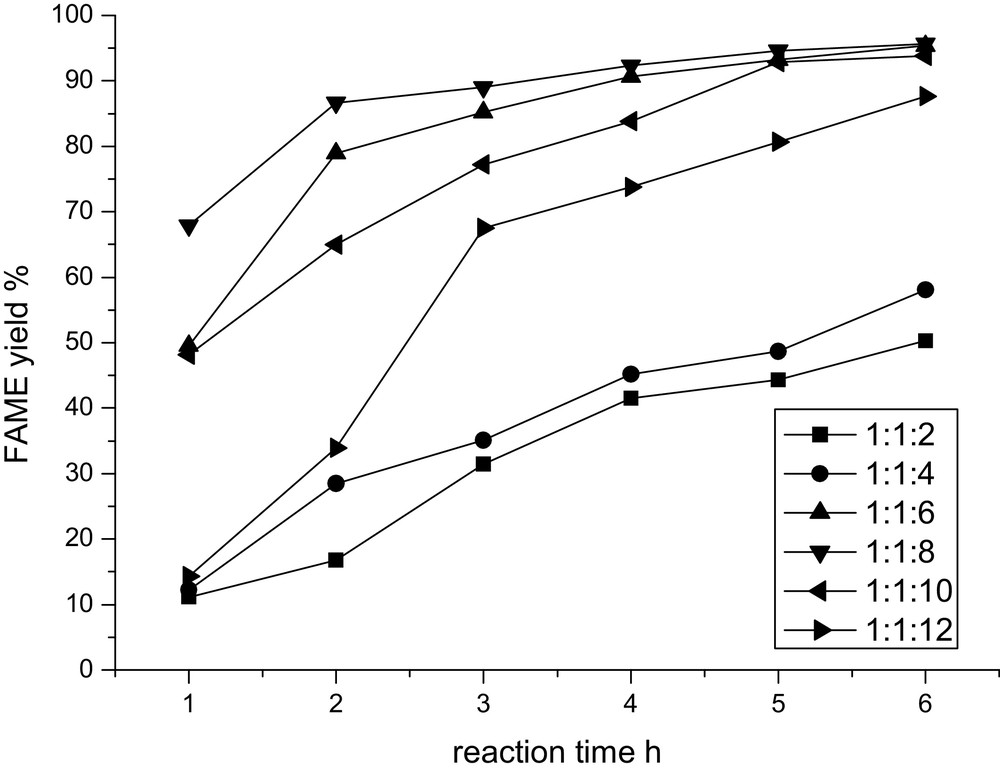
Effect of methanol concentration on the FAME yield.
Theoretically, equal mole ratios are required for the transesterification of DMC and glycerol at least, so the effect of the amount of DMC on the FAME yield was screened with DMC-to-rapeseed-oil molar ratios ranging from 1:1 to 4:1, with a constant methanol-to-rapeseed-oil molar ratio of 8:1. As shown in Fig. 3, increasing the amount of DMC, FAME yield follows a decreasing trend, obviously. This result is in opposition with the results obtained with the supercritical DMC method, in which high molar ratios of DMC to oil help to obtain high yields of FAME [12–14].
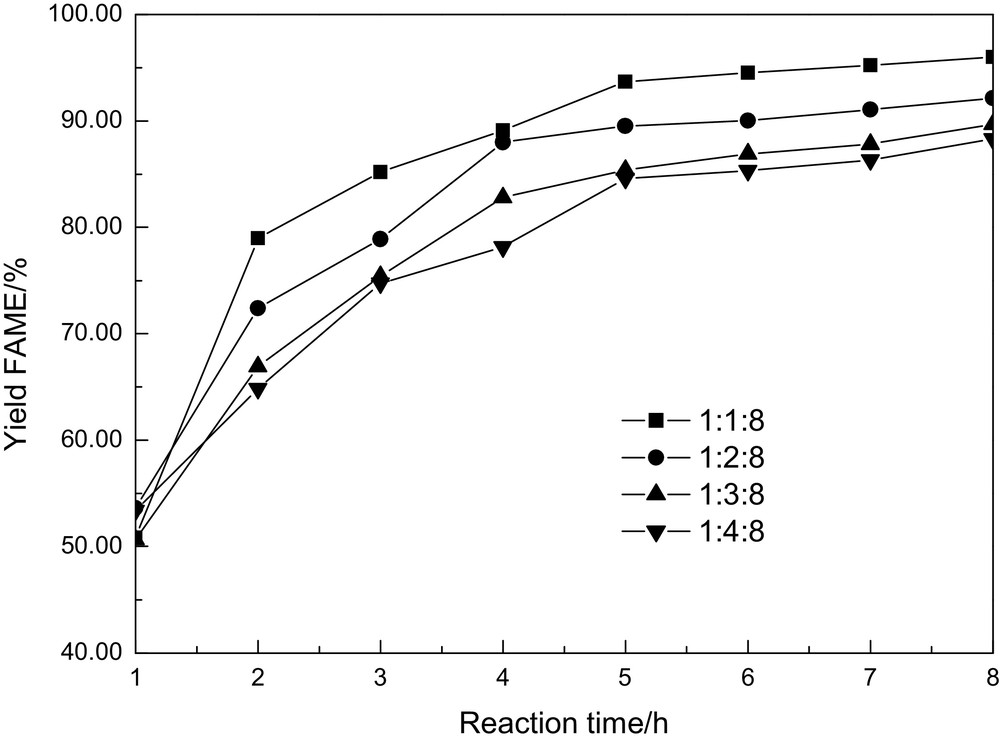
Effect of dimethyl carbonate concentration on the FAME yield.
The influence of CaO concentration on the FAME yield has also been investigated with CaO concentrations varying from 1 wt% to 25 wt% (weight to oil) at 65°C with an oil/DMC/methanol molar ratio of 1:1:8. From the obtained results (Fig. 4), it can be found that this reaction cannot process sufficiently at low concentration of catalyst, and increasing initially the amount of catalyst results in great enhancement of the FAME yield. However, the decrease in the FAME yield is found as the catalyst concentration is above 15 wt%. The reason for this decrease trend may be due to the saponification in the presence of high amounts of base, which increases the viscosity of the reactants and lowers the yield of FAME, as suggested by Yang [26]. Therefore, 15 wt% CaO is the optimal catalyst concentration in this reaction.
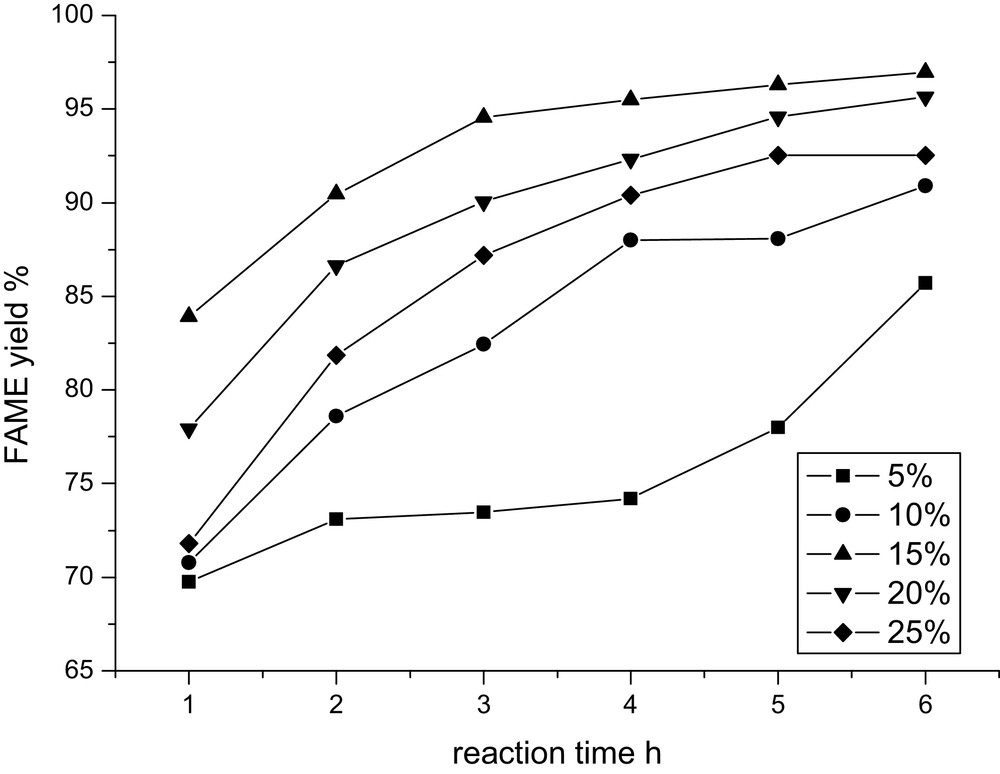
Effect of CaO concentration on the FAME yield.
The effect of the reaction time on the FAME yield can be evidenced from the result shown in Figs. 2–4. A longer reaction time should be adopted to achieve a higher FAME yield, while it should be noted that the FAME yield increases slightly, even when prolonging the reaction time from 5 h to 8 h. Considering the efficiency, the ideal reaction time is set at 5 h in the following research. It should be noted that the phenomenon of biodiesel decomposition with the reaction time under high pressures and reaction temperatures in the supercritical DMC method is avoided in this new no-glycerol biodiesel preparation method.
Encouragingly, a high FAME yield of 92.6% under 65 °C and normal pressure (with ultra-traces of glycerol) was obtained using CaO as a heterogeneous catalyst in the proposed coupling transesterification method. For comparison, the performance of traditional transesterification between methanol and rapeseed oil over CaO has also been tested and listed in Table 1. From the results, it can be seen that a half amount of methanol in the new process is enough to get the highest FAME yield. Furthermore, the reaction time for the highest FAME yield was shortened from 8 h in the traditional method to 5 h in the proposed method indicating the high reacting efficiency in the new process. What should be emphasized is that the amount of free glycerol in biodiesel obtained from the coupling transesterifications regarding the original value without any pretreatment is comparable to the value of the traditional transesterification method after a separation process. This is very important to simplify the biodiesel production process, and it can realize the economic feasibility and application of biodiesel in an industrial context.
Reaction parameters for obtaining the highest FAME yield in the traditional method compared to those with the new method.
Reaction parameters | Proposed method | Traditional method |
Reaction temperature (°C) | 65 | 65 |
Reaction time (h) | 6 | 8 |
Molar ratio of methanol to oil | 8:1 | 15:1 |
Catalyst concentration (wt%) | 15 | 15 |
FAME yield (%) | 92.6 | 90.1 |
3.3 Water resistant ability of the novel method
As we now know, water has a serious effect on the alkaline-catalyzed transesterification, causing soap formation, so the water content in the resource should be controlled within a very low level, which makes wide-range biodiesel production difficult due to the greed effort needed for removing water traces in industrial-grade methanol. In this proposed method, the water resistance ability was investigated under the following conditions: 15% CaO, 1:1:8 molar ratios of oil/DMC/methanol, 65 °C and 5 h of reaction time by adding various amounts of water in methanol. For comparison, the water resistance of the traditional method with commercial CaO was also investigated using optimal reaction conditions. Table 2 shows the effect of the water content in methanol on the FAME yield. From this result, it can be found that little water can decrease the FAME yield in any case, while the yield of FAME in the new biodiesel production method still remains at 82.6%, even if it contains 0.2% of water. In contrast, the FAME yield decreases from 90.6% to 61.4% in the traditional biodiesel production method. It is obvious that the water resistance of the new method is greatly improved.
The water resistance of CaO.
Water content (wt%) | FAME yield (%) | |
Proposed method | Traditional method | |
0.0 | 92.6 | 90.1 |
0.2 | 82.6 | 61.4 |
0.5 | 72.9 | 49.6 |
1.0 | 66.5 | 37.8 |
2.0 | 64.2 | 23.6 |
5.0 | 44.9 | 19.9 |
10.0 | 28.9 | 13.7 |
3.4 Properties of biodiesel
For commercial application, the produced biodiesel must be characterized using specified analytical methods to ensure that it meets international standards [27]. Therefore, some properties, including the viscosity, the density, the flash point and the free glycerol value of the biodiesel produced by traditional methods and the new one described above are listed in Table 3. The parameters of both biodiesels are similar according to European standard EN 14214 [28] and literature data [29]. It is a very important requirement for biodiesel production to avoid the risk of plugging fuel filters by reducing glycerol in it. It should be noted that the free glycerol in biodiesel obtained from the new method is comparable to that obtained using the traditional method after separation treatment, which indicates that coupling transesterifications eliminate glycerol efficiently, as we had suggested before. The viscosity of the obtained biodiesel is lower than the limit of EN 14214 due to the presence of glycerol derivatives [30], and this property may improve the spray injection behavior of the fuel [31].
Fuel properties of biodiesel prepared by the new method compared to traditional method.
Fuel property | Unit | Model biodiesel | EU (EN 14214) | |
Proposed method | Traditional method | |||
Density (15°C) | g/ml | 0.88 | 0.89 | 0.86–0.90 |
Kinematic viscosity (40 °C) | mm2/s | 3.18 | 3.87 | 3.5–5.0 |
Pour point | °C | –9.4 | –8.0 | – |
Cold-filter plugging point | °C | –10.0 | –9.2 | – |
Flash point | °C | 144.0 | 138.0 | ≥ 101 |
Free glycerol | % (m/m) | 0.018 | 0.019 | < 0.02 |
4 Conclusion
In this research, a method was proposed for producing FAME from rapeseed oil with the aim of solving the problem of glycerol, obtained as a by-product in conventional processes. High yields of FAME with ultra-low glycerol content under mild reaction conditions, 65 °C, normal pressure, 5 h, are obtained by integrating the transesterification of methanol and rapeseed oil within the reaction of DMC and glycerol. It was found that the transesterification reaction of rapeseed oil and methanol is enhanced by the subsequent reaction of glycerol with DMC. As a result, the methanol amount obviously decreases. Moreover, the high water tolerance of this new method presents a great potential for wide industrial application using industrial methanol as a resource. The lower cold-filter plugging point and the lower flash point of the biodiesel generated by the new method indicate that this new method for producing no-glycerol biodiesel is of great potential for being applied effectively.
Acknowledgements
This work was financially supported by grants from National Natural Science Foundation of China (21306149), Shaanxi Provincial Education Department (2013JK0646) and Excellent Master Degree Thesis Project of Xi’an Shiyou University in 2014 (2014yp130713).