1 Introduction
Ascanio Sobrero discovered nitroglycerine in 1847. In 1879, William Murrell proposed to use it for the treatment of angina pectoris, due to the dilator properties of the chemical [1]. Until the beginning of the 20th century, nitroglycerine was the most used explosive in the world.
(3-Nitrooxy-2,2-bis(nitrooxymethyl)propyl) nitrate, also known as Pentaerythritol tetranitrate (PETN), a nitrate ester, is used for diagnosis and treatment for heart diseases [2,3]. It is still used worldwide in many detonators and/or priming systems. These two examples show the duality, which exists for some small organic molecules, which were used or known as medicaments, before being used as explosives. These nitroaromatics, nitramines, and nitrate esters are used in the defense area as well as in the medicament field. Furthermore, to show dual use applications of the process engineering research originally concentrated on the production of energetic nanomaterials, the work will also give the example of some purely small model medicament molecules, for example caffeine. Caffeine is well known as a stimulant of the nervous system and a muscle relaxant. Often, to enhance its bioavailability and to reduce sensitivity to humidity, caffeine is cocrystallized with oxalic acid, which is much more stable to humidity than the cocrystal caffeine/glutaric acid [4,5].
After seeing dual applications of some organic molecules in the explosive and medicament fields, one has to recognize that these molecules are always small organic molecules, with elements having low atomic numbers (H, C, O, and N). In the case of such substances, there is also a dual or shared need to produce them in the form of small particles and even in the form of nanoparticles. The smaller the particle size, the higher the bioavailability in the case of medicaments, and the higher the effectivity in the case of explosives. Another important need in the use of nanoparticles is the possibility to engineer nanoparticles in the form of nanococrystals to enhance further and precisely their performances. The specific properties can be tuned due to the cocrystal nature, by combining in a certain way the individual properties of each pristine molecule, which is part of the cocrystal. Within the medicament field, cocrystals introduce the precise or tuned Active Principle Ingredient (API) liberation through cocrystallization of an API with an adapted coformer [6]. In the energetic field, cocrystals offer the possibility to tune or to adjust the reactivity and sensitivity of an explosive formulation at the same time [7].
After advancing the high potential of these organic particles that are explosives and medicaments in the form of pure submicron- or nano-sized particles, in the pure or in the cocrystal state, one has to recognize the current poorness of the existing production technologies to face the challenge of producing these particles in high amounts – compatible with industrial needs. Therefore, present work will show the production of high amounts and the use of the presented technique for reactive synthesis: the production of nanodiamond particles with ultimate small sizes (<5 nm) and the need to characterize the organic materials as their size is regularly decreased in the last few years.
2 Continuous nanocrystallization: principle and production of model medicaments and energetic materials
Without having the objective to give an exhaustive review on available techniques and processes to nanocrystallize organic materials such as medicaments and explosives, one can cite among the ten most known techniques four main approaches that are conducted in the pharmaceutical and energetic fields. First one is the sol-gel approach. There are no intrinsic precursors, nor for medicaments nor for explosives, which are for example available in the case of the synthesis of nano-oxides, such as for example alkoxides. Nanoexplosives were elaborated, during the sol-gel synthesis of SiO2 for instance [8,9]. This technique has in fact two drawbacks:
- - First, it is hardly possible to recover the explosive within its original particle size and in its pure form after synthesis.
- - Second, as the technique is discontinuous, it is also difficult to obtain high industrial amounts, with constant quality in terms of particle size distribution and morphology.
The second technique, which should be mentioned, is the so-called antisolvent technique. Using this process, medicaments and/or explosives are obtained in small particle sizes, by dissolving the compounds inside an organic solvent, and then, by rapidly mixing the solution into an anti-solvent, subsequently inducing a fast crystallization of the organic material [10,11]. Here again, despite that in this case it is possible to produce pure particles, it is also difficult to master a reproducible, narrow particle size distribution. Again – and even more important for energetic materials – batch techniques are very difficult to be up-scaled for industrial purposes, as the risk is clearly enhanced by the amount of energetic materials. The latter is due to safety reasons. This trend will be more and more present in the future, with continuous severity increasing of the security rules.
In recent years, two more different techniques appeared: the Rapid Expansion in Supercritical Solutions (RESS) and the Spray Flash Evaporation (SFE), the latter being conceived and developed in our NS3E laboratory. Concerning RESS, the process is able to produce nano-organic materials such as explosives or nanomedicaments by crystallizing them in a supercritical solvent such as CO2 under high pressure and high temperature. This is achieved in a continuous manner [12,13]. Although the technique is able to produce continuously well dried products, due to very low solubility of the materials in CO2, the production capacity is still very low, hardly reaching production capacities more than 1 gram/hour. To reduce and avoid all these drawbacks of different techniques, the Spray Flash Evaporation (SFE) process was developed and is described in detail in the following section.
2.1 Spray Flash Evaporation: principle and versatility
Historically, the Spray Flash Evaporation (SFE) technique was inspired by the ultra sound spray pyrolysis technique [14,15]. Even if this technique was integrating a concept of continuous production, the objective to produce high amounts with a constant quality was not possible due to the low spraying rate and the short lifetime of the transducers in organic solvents. An additional drawback that was limiting the potential of this technique was its difficulty to avoid the evaporation of pure solvents, thus leading to a progressive supersaturation of the pristine explosive inside the solvent or more generally, of the organic compounds to be crystallized.
Until now, different set-ups were conceived and designed, all of them containing the same principle (Fig. 1). The compound that is foreseen to be nanocrystallized, a pure one or a mixture of compounds, is dissolved in a low boiling organic solvent. In the majority of cases, acetone or ethanol was used, and in some rather rare cases solvent mixtures were taken. In these solvents, the solubility of each compound is generally comprised between 1 and 10 wt % at room temperature. Then the solution is pressurized to ∼40 bar, by compressed nitrogen gas, preventing any evaporation of the solvent and storing energy in the system by this way. After that, the solution is expanded through a heated hollow cone nozzle into a primary vacuum chamber. The nozzle is heated at temperatures between 130 and 160 °C, while the evaporation chamber is set under vacuum at 5–20 mbar. The extreme pressure drop from the high pressure zone to the low pressure zone and the subsequent temperature drop induce instantaneously evaporation and subsequent crystallization of the compound that was dissolved in the pristine solution. After its crystallization, the product can be trapped in a cyclone, in a filter, or in an electrical precipitator. Different set-ups were built until now, and the latest system successfully up-scaled to reach a production capacity of 100 grams per hour.

Top: photograph of a horizontal SFE nanocrystallizer. Bottom: scheme of the SFE process with its high-pressure zone on the left (solvent/solution/suspension tanks) and low-pressure zone on the right (atomization chamber and axial cyclones).
The SFE process distinguishes itself by its very high versatility in a positive way from other mentioned techniques. Depending on pure precursors or mixtures, and, in the latter case, depending on the intermolecular interactions between different molecules (e.g., hydrogen bonds, π–π stacking or van der Waals bonds) diverse hierarchical structured products can be formed. These structures go from pure nano- or submicron-sized particles to crystalline nanocomposites, with dissociated or core-shell particles. They can also be semi-amorphous or totally amorphous. In the case of intense intermolecular bonds, nano- or submicron-sized cocrystals are available (Fig. 2).
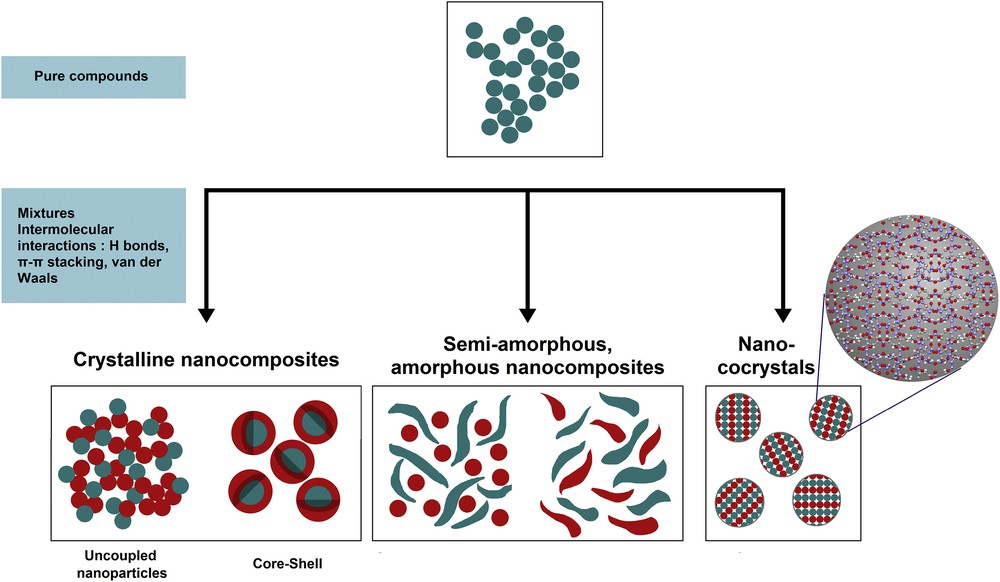
Versatility of the SFE process showing different accessible hierarchical and nanostructured materials.
2.2 Particles produced by SFE for dual use
Different examples of compounds can be given in the field of explosives as well as for medicaments. In this manner, for pure or fine-coated explosives, energetic materials like 1,3,5-trinitroperhydro-1,3,5-triazine (RDX) and octahydro-1,3,5,7-tetranitro-1,3,5,7-tetrazocine (HMX) were crystallized [16,17]. In this case, the addition of polyvinylpyrrolidone (PVP) and polyethylene glycol (PEG) could tune or adjust the mean particle size from 50 nm to 5 μm (Fig. 3(a)) [18]. For pharmaceutical issues, pure excipients were also nanocrystallized.
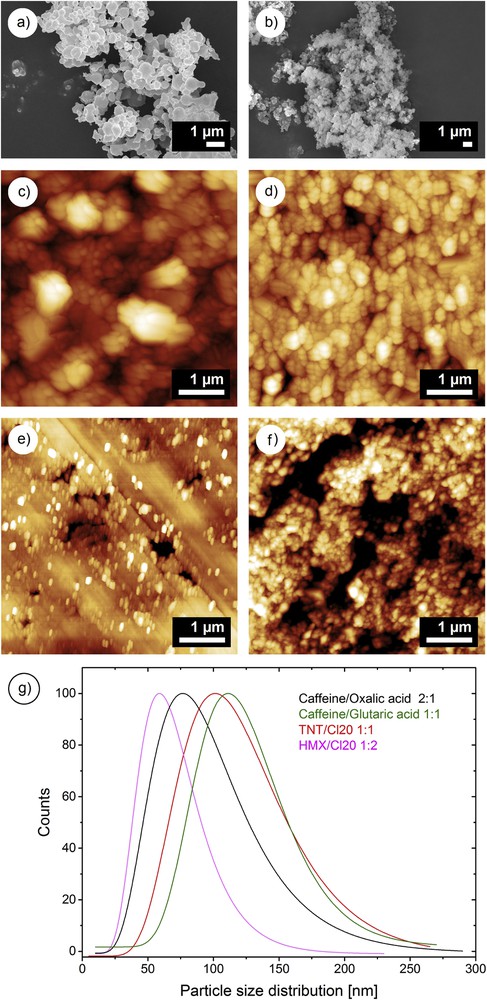
SEM images of crystalline RDX/1% PVP (a) and semi-crystalline energetic nanocomposite (b). AFM images of medicament nanococrystals (caffeine/glutaric acid 1:1 (c)); caffeine/oxalic acid 2:1 (d) and energetic nanococrystals (HMX/CL-20 1:2 (e)); TNT/CL-20 1:1 (f). Particle size distributions of the explosives and model medicament nanococrystals (g).
In the case of mixtures of pristine products, crystalline nanostructured binary mixtures of trinitrotoluene (TNT) and RDX were crystallized. These mixtures will be described in more detail within the part, which is dealing with reactive synthesis, and show rather smaller particle sizes, probably due to a certain mutual crystallization perturbation. Other mixtures of compounds were crystallized together. These resulting nanocomposites were rather semi-crystalline or totally amorphous. The latter was confirmed by XRD analysis (the pattern completely lacks in reflections). To finish this description and to insist again on the versatility of SFE, the technique could also be used for the nanococrystallization of medicaments as well as of explosives [19]. Fig. 3(c) and (d) show some examples including model medicaments (the nanococrystal caffeine/glutaric acid 1:1; caffeine/oxalic acid 2:1), as well as explosives (nanococrystal HMX/hexanitrohexaazaisowurtzitane (CL-20) 1:2 and TNT/CL-20 1:1) (Fig. 3(e) and (f)). The mean particle sizes of these compounds are between 60 nm for the nanococrystal HMX/CL-20 1:2 and 110 nm for the TNT/CL-20 cocrystal. For the model nanococrystalized medicaments, the mean particle size is between 80 nm for the caffeine/oxalic 2:1 nanococrystal and 120 nm for the caffeine/glutaric acid 1:1 cocrystal (Fig. 3(g)).
3 Reactive nanocrystallization: the ultimate sized nanodiamond synthesis
As previously mentioned, SFE process was used to nanocrystallize explosive mixtures such as RDX/TNT mixtures, named “HEXOLITE” (“HEXO” for “HEXOgen (trivial name for RDX)” or “RDX”; and “LITE” for “toLITE” or “TNT”), or even HMX/TNT mixtures, named “OCTOLITE” (“OCTO” for “OCTOgen” or “HMX”; and “LITE” for “toLITE”, or “TNT”). The synthesis of nanodiamonds by the detonation of hexolite or octolite mixtures is known since 1963. Pioneered by several Russian laboratories [20–22], the NS3E laboratory at ISL has been working on this synthesis for about 20 years. Important breakthroughs were recently made by the use of nanostructured explosive hexolite or octolite mixtures, which were detonated by the NS3E laboratory [23,24]. The size measurement of the resulting nanodiamond particles showed that the detonation of nanostructured explosive mixtures permits us to obtain smaller nanodiamonds than the detonation of the corresponding micronsized charges (Fig. 4).

Detonation synthesis principle and set-up (a), the AFM image of the nanostructured crystalline hexolite RDX/TNT 60/40 wt % mixture (b). TEM images of nanodiamonds obtained by the detonation of nanostructured (c) and microstructured (d) explosive hexolite charges. Nanostructured hexolite charge (e) and nanodiamond particle size distributions (f) obtained with nanostructured and with microstructured explosive charges.
These results show that the detonation of nanostructured charges permits the synthesis of smaller nanodiamonds than micronstructured charges. They suggest, by the same way, the conclusion that the detonation mechanisms of these two types of charges (μm vs nm) are different. The investigation of the nanodiamond particle size as a function of the explosive precursor is an alternative to other metrology methods, such as for example synchrotron X-ray real time studies. These techniques are undertaken under detonation and are therefore difficult to perform due to very short time scales of the detonation phenomenon itself [25–27]. The material method is also a real alternative to other theoretical simulation studies [28].
4 Perspectives, challenges of SFE and conclusions
In this communication, it is shown that the continuous nanocrystallization by the Spray Flash Evaporation (SFE) process is a very versatile and useful method to produce nanostructured materials with a very large structural and even hierarchical spectrum. Different examples were given from single pure nanocrystals to binary nanococrystals. Furthermore, nanocrystalline and amorphous nanocomposites, depending essentially on the type of intermolecular interactions between the different molecule types, were presented. Major challenges are currently under investigation, such as on-line studies of crystallization mechanisms by different on-line techniques such as Phase Doppler Analysis or also by on-line synchrotron X-ray diffraction. Another challenge concerns the product characterization by coupling Atomic Force Microscopy (AFM) with additional spectroscopy techniques to discriminate and to allow chemical mapping of nanostructured mixtures on the nanoscale. Some investigations are currently being done and should be published in the near future. The on-line and post-production characterizations will be fundamental for the further deep understanding of the SFE mechanism (which, in fact, depends also on the individual material system). These investigations are essential to be able to tune the hierarchical structure on demand. This in turn will permit us to further control the precise synthesis of nanodiamonds or to conceive precise nanomedicaments to treat specifically a disease such as cancer by the precise nanococrystallization of API/coformer or API/API (also called drug/drug) nanomedicaments [29]. To conclude, there are great challenges behind the comprehension of the presented breakthrough-technology of SFE and the subsequent precise tuning of structural and hierarchical nanocomposites.