1 Définitions
Les trois termes, fer, fonte, acier, d’utilisation très ancienne n’ont reçu une définition scientifique qu’à la fin du XIXe siècle. Ils désignent des alliages ferreux présentant des teneurs en carbone différentes : le fer doux contient moins de 0,02 % de carbone, l’acier comprend entre 0,02 et 2 % de carbone et la fonte en comporte plus de 2 %. La teneur en carbone modifie les caractéristiques d’usage du produit.
Dans sa définition moderne la cémentation consiste en un enrichissement en carbone de la surface d’une pièce en acier doux (C < 0,25 %) par maintien à température élevée dans un milieu susceptible de céder du carbone à l’acier. Pendant ce maintien en température, le carbone pénètre vers l’intérieur de la pièce par diffusion. La cémentation est toujours suivie d’un traitement de trempe qui permet d’obtenir le durcissement de la couche enrichie en carbone.
Le mot cémentation provient du fait que, (historiquement), la carburation de l’acier était obtenue en chauffant le métal au milieu d’une poudre nommée cément (de l’anglais cement).
La trempe est un traitement thermique qui consiste à refroidir brusquement une masse métallique portée à haute température.
2 Grandes lignes de l’histoire de la sidérurgie [1]
La première industrie du fer apparaît dans le sud du Caucase, vers 1700 avant J.C. chez les Hittites et les Chalybes. Le minerai de fer se présentait sous forme de petites roches à fleur de sol. Les hittites faisaient chauffer un mélange de minerai et de charbon de bois dans un simple trou. Ils obtenaient une masse pâteuse qui était battue afin de la débarrasser de ses impuretés et de ses scories avant d’être forgée. Tout en gagnant l’Europe, au cours du millénaire suivant, l’outil de production du fer se perfectionne et évolue vers le « bas foyer », sorte de four semi enterré dans lequel on entasse des couches de minerai de fer et de charbon de bois. L’air envoyé par un soufflet manuel active la combustion. La température est portée à 1100° à 1200° et on obtient ainsi par réduction une masse pâteuse de fer de quelques kilos appelée loupe. À la suite d’améliorations successives, les bas foyers s’agrandissent et se perfectionnent. Leur cuve s’élève au-dessus du sol.
Au Moyen âge la combustion est activée par des soufflets mus par l’énergie hydraulique qui actionne aussi les martinets qui servent à battre les loupes de fer. La production augmente mais reste modeste par cette méthode dite « directe ».
Au début du XIVe siècle la hauteur des fourneaux a augmenté et les conditions de soufflage se sont perfectionnées. Ainsi, la température de la combustion dans les parties basses du fourneau s’est élevée suffisamment pour que le fer puisse absorber des quantités croissantes de carbone. Le fer carburé fondant à une température plus basse que le fer pur, on obtient pour la première fois un métal liquide : la fonte. Dure et cassante, la fonte solide ne peut être ni soudée ni forgée comme le fer, mais on peut la couler dans des moules. En la débarrassant de son carbone par affinage (on faisait fondre des lingots de fonte dans des foyers de forge sous un vif courant d’air) on peut obtenir du fer, pur ou irrégulièrement et faiblement carburé. Dans certaines régions, du fait de minerais privilégiés ou d’un bon tour de main l’affinage produisait de l’acier qualifié de « naturel ».
Intérêt de cette double opération dite « méthode indirecte » : au lieu de quelques kilos quotidiens de métal pâteux obtenus par la méthode directe, le fourneau devenu « haut-fourneau » permet de produire plusieurs tonnes de fonte par mois. L’industrie sidérurgique prend ainsi un nouveau départ. On publie les premiers ouvrages consacrés au travail du fer au XVIe siècle. (De la Pirotechnia, V. Biringuccio, 1540 ; De Re Metallica, G. Agricola, 1556) (Fig. 1).

Martelage et trempe des barres d’acier.
G. Agricola, De Re Metallica (1556), traduction française de A. France-Lanord, G. Klopp éd. 1987, p. 346.
Le travail du métal n’est plus un travail artisanal, mais s’oriente vers une production de masse. Le fer produit par affinage va vers les laminoirs, les tréfileries, les fenderies qui permettent de le convertir en une foule d’objets usuels.
On distinguait l’acier naturel du fer de diverses manières : couleur, dureté par rapport à des roches, grain, cassure, flexibilité et surtout capacité à devenir extrêmement dur par refroidissement rapide à l’eau (trempe).
On connaissait une autre technique de production de l’acier, la cémentation. Le procédé certainement très ancien est décrit minutieusement dans les deux ouvrages de Biringuccio et d’Agricola. Il consiste à réchauffer des blocs de fer doux dans la fonte en fusion. Au XVIe siècle se développent des procédés de cémentation basés sur l’emploi de poudres carburantes constituées de charbon mélangé à des substances organiques, utilisés sur des objets en fer terminés dans le but d’obtenir une zone superficielle en acier capable de durcir par trempe (cémentation superficielle). C’est seulement au XVIIe siècle que la fabrication de l’acier cémenté (appelé acier artificiel) se développe quand on commence à utiliser la cémentation pour la transformation en acier de masses de fer destinées à être ultérieurement travaillées.
Au XVIIIe siècle, l’histoire du fer est intimement liée à celle de la révolution industrielle anglaise. La disparition progressive de leurs forêts conduit les anglais à remplacer le charbon de bois par la houille (Darby 1709, première coulée de fonte au coke). Le machinisme qui se développe (machine à vapeur de Watt 1770) permet d’extraire les quantités de houille nécessaires. C’est aussi un anglais Cort qui met au point (1784) le procédé de puddlage (fours à réverbère dans lesquels la fonte liquide est brassée et convertie en fer avec un rendement amélioré par rapport à l’affinage traditionnel).
C’est encore un anglais, Huntsman, qui en 1745 obtient de petites quantités d’acier fondu au creuset à partir d’acier cémenté.
Dès le début du XVIIIe siècle des savants s’intéressent au fer sous ses différents aspects. En 1722, de Réaumur cherche les liens entre les trois métaux fer, acier, fonte. Il est le premier à remettre en cause l’opinion d’Aristote suivant laquelle l’acier est une forme plus pure de fer. Il comprend que c’est le fer la forme la plus pure et que c’est la présence en quantités variables de ce qu’il nomme les « sels et de soufres » qui caractérise la fonte et l’acier.
Il faut attendre les travaux de Lavoisier, les analyses de Bergman et Scheele, pour que, en 1786, le véritable rôle du carbone dans la trilogie fer-acier-fonte soit exprimé par Vandermonde, Berthollet et Monge dans un mémoire célèbre publié à l’Académie Royale des Sciences.
Connaissant la composition et les avantages de l’acier, il ne restait plus qu’à le produire en grandes quantités. Il faudra plus de 50 ans pour y parvenir, pendant lesquels le haut-fourneau se perfectionne et s’agrandit, la qualité de la fonte s’améliore. Ce sont les progrès réalisés dans la maîtrise des hautes températures, le perfectionnement des fours et des réfractaires qui permirent de résoudre le problème. En 1856, Bessemer produit de l’acier liquide par décarburation de la fonte liquide dans un convertisseur dans lequel on soufflait de l’air. Le procédé est ensuite adapté en 1877 à l’affinage de la fonte phosphoreuse par Thomas et Gilchrist. De son côté, Martin en aménageant le four à récupération inventé par les frères Siemens, réussit à obtenir en 1864 de l’acier liquide par co-fusion d’un mélange de ferrailles et de fonte (Fig. 2).
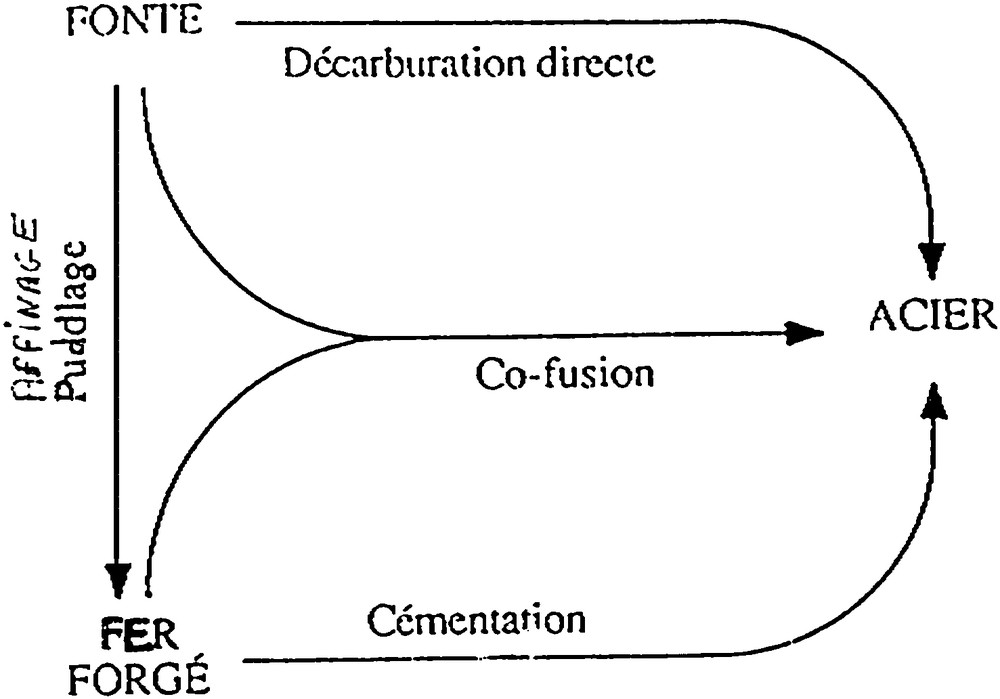
Diagramme de la co-fusion.
B. Jacomy, Une histoire des techniques, Points Seuil, 1990, p. 98.
Grâce à ces nouveaux procédés industriels de fabrication, l’acier devient un produit d’usage courant qui va bientôt supplanter le fer. En 1890 la production d’acier égale celle du fer, en 1910 on ne produit plus que de l’acier.
Après 1880 on améliore et diversifie les propriétés de l’acier en incorporant des éléments d’alliages tels que nickel, chrome, tungstène, etc. C’est le début des « aciers alliés ». D’abord élaborés empiriquement, pour répondre aux besoins militaires, ils connaîtront un essor prodigieux après 1910 lorsque les connaissances scientifiques permettront de contrôler leurs propriétés.
3 René Antoine Ferchault de Réaumur (1683–1757) entrevoit les principes de la sidérurgie moderne
On peut affirmer que ce sont les spéculations mécanistes des philosophes du XVIIe siècle qui ont inspiré l’ouvrage de Réaumur publié en 1722, « L’art de convertir le fer forgé en acier et l’art d’adoucir le fer fondu » (Fig. 3).

René de Réaumur (1683–1757).
Réaumur reprend les hypothèses des physiciens mécanistes qui l’ont précédé puis, combinant les représentations corpusculaires de l’univers cartésien avec ses observations remarquablement soigneuses et précises de la structure du métal révélée par la cassure, il élabore une explication du mécanisme de durcissement de l’acier mettant en jeu des transformations moléculaires produites par la chaleur, qui servira de guide à toutes les expériences ultérieures et qui ne sera guère améliorée jusqu’à la fin du XIXe siècle. Seul, à cette époque, Réaumur utilise des essais mécaniques dans un esprit scientifique d’étude du métal. Il indique « les manières de connaître les défauts et les bonnes qualités de l’acier et plusieurs vues pour parvenir à comparer les aciers de différents degrés de perfection ». Il étudie le grain sur des cassures d’éprouvettes entaillées et trempées d’un seul côté, il recherche la dureté en essayant de rayer le métal par des corps constituant une échelle : verre, cristal de roche, silex, agate, etc. ; il crée l’essai de pliage et même l’essai de traction sur fil pour comparer, notamment un fil trempé au fil initial. Sa théorie sur la trempe lui permet d’expliquer aussi de façon très cohérente le phénomène de cémentation.
En France, au début du XVIIIe siècle on ne fabriquait pas d’acier cémenté. Cet acier était commercialisé sous le nom « d’acier artificiel » par divers pays d’Europe dont les fabricants tenaient les procédés jalousement secrets. C’est pour remédier à cette lacune que Réaumur effectue une étude systématique des procédés de cémentation superficielle alors connus en France dans l’espoir de maîtriser la fabrication de l’acier artificiel. Il étudie surtout l’influence des céments alors constitués de mélanges de substances organiques tels que les ongles, le cuir, la fiente et l’urine de certains animaux. Grâce à de nombreuses expériences, il établit que le meilleur cément est une poudre formée d’une partie de charbon de bois, deux parties de noir de fumée, une partie de cendres et trois-quart de partie de sel marin. Il indique comment les résultats de l’opération peuvent être classés par le grain de la cassure et que la transformation du fer en acier va de la surface vers l’intérieur. Il insiste sur l’importance du chauffage et donne des dessins détaillés des fours qu’il utilise. Il constate que dans l’opération, le métal augmente de poids, ce que tout naturellement il attribue à l’absorption du « soufre et des sels » volatils [2].
4 De Réaumur à 1914
4.1 Les études sur la cémentation
Les recherches de Réaumur donnèrent une forte impulsion à l’industrie de l’acier cémenté mais, contrairement à l’espérance de leur auteur, elles profitèrent surtout à d’autres nations que la France qui ne produisait pas, alors, de fer de la qualité voulue pour fournir un bon acier par cémentation. En Suède, en Allemagne et surtout en Angleterre cette industrie devint florissante. On préparait des barres que l’on forgeait en paquets : c’était l’acier poule (blister steel) nom dû aux petites soufflures qui caractérisaient la surface des barres d’acier cémenté. En 1745 l’horloger anglais Hunstman élabore le procédé de fusion de l’acier au creuset. À dater des dernières années du XVIIIe siècle, le fer suédois, cémenté en Angleterre constitue la matière première du meilleur acier anglais au creuset.
Les conclusions théoriques de Réaumur, concernant la nature de la trempe et de la cémentation contenaient à côté d’une certaine part de vérité, de graves erreurs, inévitables conséquences des théories chimiques acceptées au début du XVIIIe siècle.
Bientôt, dans la seconde moitié du XVIIIe ces théories évoluèrent. Les travaux de Bergman (qui affirme que fer, acier, fonte ne sont que du fer pur contenant une proportion variable de graphite, considéré, alors, comme un composé à base de phlogistique), ceux de Scheele (il établit que le graphite contenu dans la fonte n’est qu’une espèce de charbon minéral formé d’air fixe (anhydride carbonique) et de phlogistique et surtout ceux de Vandermonde, Berthollet et Monge (1786 Mémoire sur le fer considéré dans ses différents états métalliques) [3] qui, suite aux travaux de Lavoisier sur la combustion, démontrant la fausseté de la théorie du phlogistique, reprennent les travaux de Réaumur, Bergman et Scheele et démontrent que la matière étrangère qui, unie au fer pur dans une proportion variable, produit l’acier et la fonte n’est autre que le carbone. Leur démonstration s’appuie sur le phénomène déjà observé par Réaumur, de l’augmentation de poids éprouvée par le fer pendant sa transformation en acier grâce à une cémentation exécutée en présence de charbon de bois seul en dehors du contact de l’air et de l’humidité. Ils prouvent que cette transformation ne peut être due qu’à l’« absorption » graduelle du carbone par le fer.
Ainsi, dès les dernières années du XVIIIe siècle on a une perception relativement exacte du phénomène de cémentation. Notons cependant que le mot diffusion n’est pas utilisé dans les textes de l’époque et que l’on n’a aucune idée précise sur le mécanisme du phénomène. Voici par exemple la manière dont s’exprimait Monge dans L’art de fabriquer les canons, « Pendant la cémentation, le charbon s’introduit dans le fer et y pénètre peu à peu, à peu près comme l’eau s’introduit dans l’intérieur des bois secs ; il lui faut un certain temps pour pénétrer à une certaine profondeur, de manière que si on arrête l’opération avant qu’elle soit complète et si, après l’avoir laissé refroidir, on casse une des barres, il est facile de reconnaître à l’aspect grenu de la cassure, la partie du métal dans laquelle le charbon s’est introduit » [4]. Bien que ces textes fondateurs insistent sur le rôle du charbon seul, l’opinion subsista que l’addition de substances convenables autres que le charbon de bois ou l’emploi de matières carburantes plus complexes devait permettre d’abréger beaucoup le temps nécessaire pour une cémentation donnée. Cette opinion fut la cause d’un très grand nombre de tentatives tout au long du XIXe siècle destinées à perfectionner les procédés de cémentation connus, tentatives conduites dans un esprit exclusivement empirique.
La fabrication de l’acier cémenté se développa rapidement dans toute l’Europe et en Amérique durant la première moitié du XIXe siècle. Après 1860 cependant, l’introduction de nouvelles méthodes de fabrication de l’acier (Bessemer, Thomas, Siemens-Martin) beaucoup moins coûteuses limita l’application de ce procédé à la production des aciers les plus fins fondus au creuset.
Par ailleurs, l’industrie mécanique prenait un grand développement et réclamait de plus en plus de pièces possédant une âme non fragile et une très grande dureté superficielle ; la cémentation des objets en acier doux, déjà finis, répondait à ces besoins.
La production de l’acier cémenté proprement dit allait donc en diminuant à la fin du XIXe siècle tandis que se développait de jour en jour l’industrie de la cémentation superficielle des pièces mécaniques finies. La complexité des problèmes techniques à résoudre explique l’ardeur des recherches et le nombre de tentatives faites dans la seconde moitié du XIXe siècle pour perfectionner les procédés. Leur application s’étendit rapidement à de nombreuses branches de l’industrie telles que la fabrication des outils destinés au travail du bois et des métaux, la fabrication des organes de machines, la fabrication des cuirasses des navires, etc.
À côté des innovations techniques, on cherchait aussi à expliquer le phénomène ce qui donnait lieu à d’interminables discussions qui prouvent l’importance prise par l’opération et combien le milieu scientifique s’y intéressait. Mais ce milieu scientifique était surtout constitué de chimistes et les chimistes de l’époque raisonnaient essentiellement en termes de réactions chimiques, ce qui n’est pas une bonne approche du phénomène de diffusion. Il serait fastidieux de revenir sur toutes ces discussions. Citons seulement quelques uns des chimistes qui ont participé à ce vaste débat dont les points de controverse principaux étaient le rôle des gaz dans le mécanisme et le rôle des produits autres que le charbon de bois ajoutés dans les céments. [5].
Le Play (1841) considère la cémentation comme une opération « inexpliquée et mystérieuse » et il attribue l’introduction du carbone au cœur des barres de fer à la seule action de l’oxyde de carbone gazeux ; Laurent admet qu’il se forme des vapeurs de carbone que le métal absorbe ; Gay-Lussac combat les opinions de Le Play et de Laurent et déclare que la cémentation doit avoir lieu par absorption directe du carbone par le fer (1846). Il avouait que l’étude de ce procédé avait ébranlé sa foi dans l’axiome des vieux chimistes Corpora non agunt nisi soluta (les corps n’agissent pas sinon en solution), car il est certain dit-il « que tous les corps solides, liquides, ou aériformes, agissent les uns sur les autres, mais que des trois états des corps, l’état solide est le moins favorable à l’exercice de l’affinité » ; survient ensuite la fameuse et interminable (1860–1865) discussion de Caron, Fremy et Margueritte qui n’apporte finalement aucune certitude ; Boussingault (1875) attribue au carbone l’action principale des céments. En 1879 Mannesmann publie un très important mémoire qui relate des séries d’essais d’ordre industriel. À la suite de ses expériences il affirme que : dans la pratique de la cémentation, une grande part doit revenir à l’action carburante du charbon à l’état solide, par simple « contact » et, par suite, à la diffusion du carbone par « migration moléculaire » dans la masse de l’acier solide.
De nombreuses opinions (appuyées sur des expériences plus ou moins probantes) continuent à être émise sur le processus de cémentation : Marsden (1881) pense que le carbone diffuse sous forme de poudre impalpable ; Hempbel (1885) croit que le diamant cémente à une température beaucoup plus basse que le carbone sous ses autres formes, etc.
Les doutes qui pouvaient subsister sur la possibilité de cémenter le fer en l’absence de tout intermédiaire gazeux sont levés par une expérience faite par Roberts Austen en 1889 qui carbure du fer pur dans le vide par le diamant à une température très inférieure au point de fusion (rouge vif) du fer et dans des conditions qui excluaient complètement la présence de gaz occlus.
Osmond obtient des résultats très précis (1891). Il opère avec des diamants et du fer électrolytique dans un courant d’hydrogène pur et constate que, entre 1035 et 1065 °C, la cémentation ne se produit que là où il y a contact ; entre 1085 °C et 1125 °C les diamants disparaissent ; il y a formation de fonte blanche.
D’un point de vue industriel l’opération de cémentation avait alors une grande importance, ce qui explique un regain de travaux scientifiques pour en comprendre les mécanismes. Citons l’utilisation du procédé Harvey (brevet de 1891) pour la cémentation des plaques de blindages.
La cémentation s’effectue dans un four couvert par une voûte mobile que l’on enlève pour mettre la plaque à traiter, amenée par des rails qui disparaissent dans la couche de sable inférieure. La plaque est recouverte de charbon de cémentation. Le four est amené à une température de chauffage correspondant à peu près à celle de la fusion de la fonte, cette température est maintenue jusqu’à ce qu’on ait obtenu une carburation suffisante (l’opération s’avère très longue, 120 heures pour une plaque de 0,265 m d’épaisseur et 48 heures d’échauffement du four). Puis, on laisse tomber le feu, la voûte est enlevée, la plaque est progressivement dégagée pour refroidir à l’air. Elle est ensuite réchauffée une première fois pour faire disparaître les déformations subies pendant la cémentation, refroidie puis réchauffée pour être enfin soumise à une trempe par aspersion d’eau froide sur la face carburée (pendant quatre heures).
À partir de 1893, le gouvernement américain adopte pour le blindage de sa flotte, exclusivement, le métal cémenté par le procédé Harvey. En Europe les usines Vickers d’Angleterre acquièrent le procédé Harvey, puis en 1895 l’usine Krupp en Allemagne et l’usine du Creusot en France le modifient : la cémentation au charbon solide est remplacée par une cémentation aux gaz carburés. Cette cémentation gazeuse est plus rapide. L’exposition universelle de 1900 à Paris confirme que le métal cémenté est devenu d’usage général. Les usines françaises vont ensuite apprendre à combiner le procédé Harvey à l’emploi des aciers spéciaux.
C’est dans cette dernière décennie, qui voit une intense activité de recherche sur les alliages et en particulier sur le diagramme fer-carbone, que sont effectués des travaux faisant le lien entre le procédé industriel de la cémentation et le phénomène plus général de diffusion dans les solides.
En 1896, Roberts Austen publie ce qui semble être la première courbe représentant la variation de concentration du carbone dans la couche carburée obtenue en soumettant un acier pour rail à 0,26 % de carbone, à la cémentation par le procédé Harvey (Fig. 4).

Courbe représentant la variation de la concentration en carbone dans la couche carburée obtenue par cémentation d’un acier pour rail (0,26 % C) par le procédé Harvey.
Journal of Iron and Steel Institute, 1896, vol. I, p.139–42.
Après 1900, malgré la connaissance du diagramme fer-carbone, en l’absence d’une véritable théorie du phénomène, les recherches, qui portent toujours sur les mêmes sujets : influence de la température, influence des céments utilisés, influence de la durée de l’opération, et influence de la composition initiale de l’acier à cémenter, ne fournissent qu’un vaste catalogue de résultats expérimentaux, difficiles à relier et à généraliser. Au début du XXe siècle, les fours et les céments ont finalement peu changé depuis l’époque de Réaumur.
Ces difficultés viennent du fait que toutes les opérations industrielles qui dépendent à la fois de la température et du temps sont contrôlées par les lois de la diffusion. Or, celles-ci ne seront vraiment comprises, pour ce qui concerne la diffusion dans les solides, qu’à la fin des années 1940.
4.2 Les recherches sur la trempe
Pendant toute la première moitié du XIXe siècle la définition du mot acier est basée sur la teneur en carbone donnée par l’analyse et sur les qualités mécaniques liées à cette teneur (dont la plus caractéristique est la dureté obtenue par le procédé de trempe). Malheureusement on ignore tout des causes du durcissement de l’acier. Diverses théories sont élaborées pendant cette période mais dans un traité de métallurgie publié en 1865, Percy professeur de métallurgie à l’École des Mines à Londres reconnaît son ignorance. « Pourquoi la présence de carbone transforme-t-elle le fer en acier ? C’est un mystère. Pourquoi le carbone ainsi introduit permet-il au fer de rester magnétique ? C’est un mystère. Pourquoi l’acier peut-il être revenu ? C’est un mystère. Cependant, les distinctions entre fer et acier sont bien connues » [6]. Un grand pas vers une bonne compréhension du phénomène va être fait par Tchernoff, métallurgiste russe, ingénieur aux aciéries Oboukoff. Dans son premier article en 1868, il étudie la taille des grains observés visuellement sur les cassures, en relation avec le traitement thermique et la teneur en carbone et découvre l’existence de températures critiques correspondant à des transformations de l’acier à l’état solide [7]. Il n’y aura pas d’autres études originales sur la trempe jusqu’en 1885 date du premier mémoire de Osmond, ingénieur aux usines du Creusot, qui marque le début effectif de l’utilisation de la métallographie microscopique dans la recherche sur les aciers (Fig. 5).
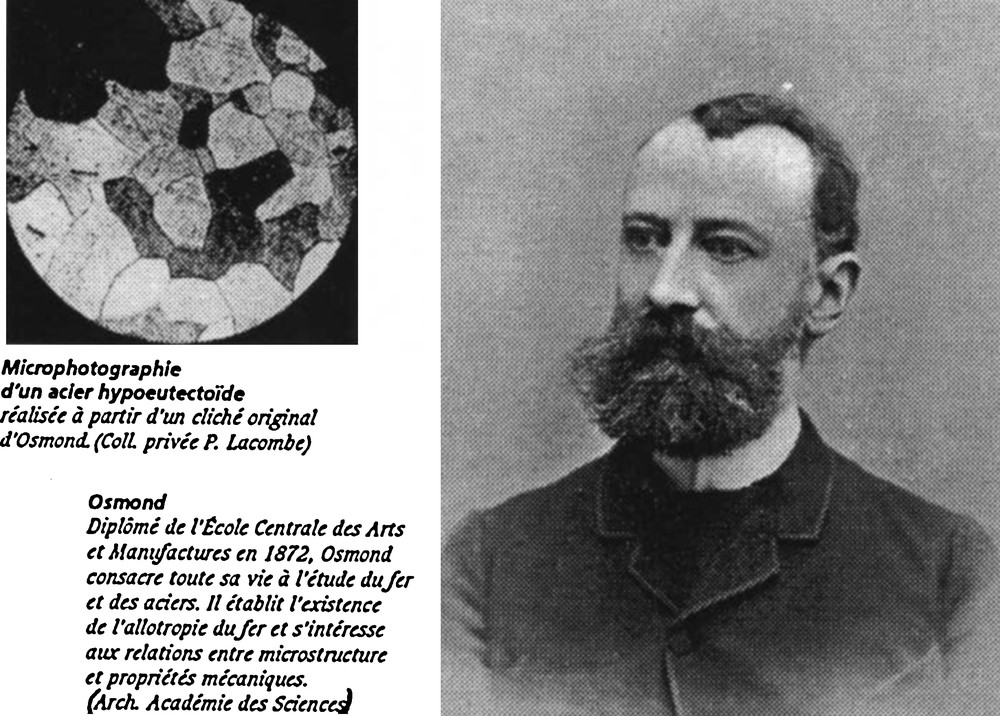
Floris Osmond (1849–1912).
Osmond examine au microscope les cassures polies et attaquées d’aciers, avant et après trempe, puis utilise en 1887 le thermocouple de Le Chatelier pour mesurer l’évolution de la température en fonction du temps, du fer et de l’acier, au chauffage et au refroidissement. Il utilise ainsi pour la première fois la technique dite d’ « analyse thermique » qui va s’avérer l’outil privilégié de la recherche sur les alliages. Avec Osmond on entre dans la phase scientifique moderne de l’étude des métaux ferreux.
Son premier article de 1885, « Théorie cellulaire de l’acier » [8] établit clairement l’importance des différents états du carbone et l’existence de deux variétés allotropiques du fer, α et β. Le second article de 1887 [9] décrit un travail effectué dans le laboratoire de Le Chatelier à l’École des Mines. Il déduit de ses mesures d’analyse thermique une théorie de la trempe. Il affirme que l’acier trempé est un acier ou le fer et le carbone ont conservé plus ou moins complètement à froid l’état qu’ils possédaient aux températures élevées et que c’est essentiellement la persistance du fer β qui donne à l’acier ses caractéristiques, l’influence du carbone étant indirecte. Cette théorie allait à l’encontre des idées de l’époque et s’attira des attaques immédiates de métallurgistes renommés. L’américain Howe engage alors une controverse qui va susciter des antagonismes aussi bien scientifiques que personnels entre « allotropistes » et « carbonistes ». Les allotropistes soutenaient (avec raison) qu’il y avait une transformation dans le fer pur à la température du rouge brillant, et (à tort) que la forme haute température pouvait être préservée à l’ambiante par la trempe et qu’elle était très dure. Les carbonistes soutenaient que la dureté de l’acier dépend directement de la teneur en carbone et de l’état chimique sous lequel il existe, état variant avec la température. Cette querelle soutenue de part et d’autre par des scientifiques de valeur, induisit dans la décennie suivante une grande quantité de travaux expérimentaux qui, finalement menèrent à la vision moderne du phénomène.
Durant cette période les laboratoires deviennent les centres du progrès. Le microscope en est d’abord le principal outil, mais autour de lui vont se grouper toutes les techniques de mesures physiques (dilatomérie, mesures de résistivité, magnétisme, conduction thermique, etc.) dont l’ensemble forme les outils de la métallographie. L’étude de l’acier, avant et après trempe, permet de faire la jonction entre propriétés mécaniques et structure, ce qui se traduit dans la pratique par la liaison entre laboratoires de recherche et industrie. Cette liaison est concrétisée par la création en Angleterre, en 1890 et en France en 1895 de groupes de recherche pluridisciplinaires, le Alloys Research Comittee et la Commission des alliages. Une décennie de recherches expérimentales intensives, menées par une vingtaine de chercheurs de toutes nationalités, permet l’élaboration des premiers diagrammes d’équilibre d’alliages métalliques d’utilisation courante. Toutes les méthodes concourent à l’élaboration de ces diagrammes dont l’utilité industrielle devient vite incontestable. La micrographie qui autorise l’étude de la microstructure constitue alors l’outil central de ces recherches et permet d’aborder l’étude des systèmes hors d’équilibre. Dans les années 1887 à 1900 toutes les méthodes expérimentales d’investigation des diagrammes sont perfectionnées et exploitées, passant du prototype de laboratoire à des instruments d’utilisation industrielle.
La nature et le nombre des phases sont déterminés grâce aux études sur la fusibilité des alliages et sur leur conductivité électrique. Les températures critiques correspondant à des transformations à l’état solide sont étudiées quant à elles, par analyse thermique, micrographie, dilatométrie et détermination des propriétés magnétiques.
En 1895 Osmond publie son troisième article, « Méthodes générales pour l’analyse micrographique des aciers au carbone » [10] où il définit et décrit les différents constituants de l’acier grâce à de nombreuses micrographies. Il introduit dans cet article pour la première fois le fer γ. En 1897 Le Chatelier fait paraître une mise au point sur « L’état actuel des théories sur la trempe » [11] exposant la théorie élaborée en commun avec Osmond que l’on peut résumer ainsi : aux températures élevées, au-dessus de 900 °C, l’acier est constitué par une solution solide homogène, amagnétique de carbone dans le fer γ (plus tard nommé austénite par Osmond). Au refroidissement lent cette solution se comporte comme une solution aqueuse comportant un eutectique à 0,8 % C, la perlite, constituée de ferrite et cémentite. La particularité des aciers est que l’on peut éviter, par un refroidissement rapide le dédoublement et la cristallisation séparée de ces deux constituants : c’est la trempe, qui donne une solution solide instable magnétique, la martensite.
Pendant ce temps, le professeur Roberts Austen publie en 1896 un premier diagramme fer-carbone expérimental.
Ce premier diagramme, amélioré en 1899, est repris par Roozeboom qui lui applique la règle des phases récemment explicitée par J.W. Gibbs et fournit en 1900 un diagramme presque correct où il ne manque que les petits domaines d’existence du fer α (autour de 700°) et du fer δ (près de la fusion) aux très faibles teneurs en carbone [12] (Fig. 6). Osmond utilise alors ce diagramme pour expliquer les changements successifs de structure qu’il avait déjà rencontrés. Il nomme pour la première fois l’austénite (solution solide de carbone dans le fer γ). Il observe que la martensite représente une transformation de l’austénite au refroidissement et que cette transformation peut être supprimée par l’adjonction d’éléments d’alliages.
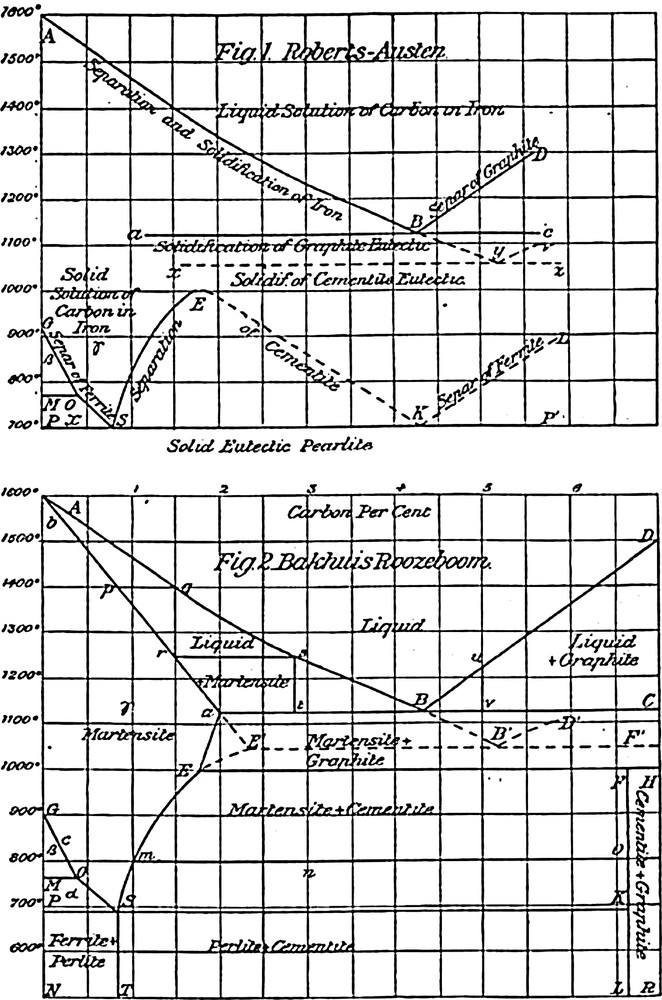
Comparaison du diagramme fer-carbone expérimental établi par W. C. Roberts Austen en 1899 avec le diagramme proposé par Roozeboom en 1900 pour tenir compte de la règle des phases.
Roozeboom, « Le fer et l’acier au point de vue de la doctrine des phases », BSEIN, 5, 1900, p. 613.
Lorsqu’en 1902 commence l’étude systématique des aciers spéciaux les résultats sont d’abord difficiles à interpréter, mais progressivement ils vont permettre de voir plus clair dans le phénomène complexe de la trempe.
5 Les aciers spéciaux, tremplin de la métallurgie scientifique [13]
Rappelons que tout le champ des travaux métallographiques sur l’acier a convergé vers la mise au point du diagramme fer-carbone, point de départ d’un travail systématique sur les diagrammes d’équilibre d’alliages métalliques binaires. Cependant, l’étude des alliages binaires est insuffisante pour l’industrie qui utilise souvent des composés beaucoup plus complexes comme les aciers alliés (ou spéciaux, terme plus souvent utilisé après 1890) qui sont des alliages de fer et de carbone dans lesquels on incorpore volontairement un ou plusieurs éléments supplémentaires. Ces aciers alliés étaient connus avant les années 1880, en ce sens que les métallurgistes avaient souvent pu constater que l’incorporation de certains éléments dans les aciers leur conférait des propriétés particulières intéressantes. Mais jusque-là il s’agissait, soit d’étude de laboratoire sans conséquences commerciales, soit de l’obtention d’aciers à outils élaborés au creuset, donc commercialisés en petite quantités. Ce n’est que dans les années 1880 que sont réunies les conditions d’un véritable démarrage des aciers alliés industriels. Il fallait disposer en grandes quantités d’un échantillonnage complet d’aciers au carbone de qualité constante, il fallait aussi disposer d’éléments d’alliage (chrome, nickel, tungstène, etc.) produits industriellement et enfin qu’il y ait une demande pour des alliages ayant des performances particulières.
Le début des années 1880 correspond à la création et la mise en train des aciéries à grande production qui traitent la fonte phosphoreuse grâce au procédé Bessemer–Thomas (1878) ou Siemens–Martin à sole basique (1879), ce qui remplit la première condition soulignée : la quantité. La fabrication industrielle des métaux d’alliage potentiels est déjà ancienne pour certains : le vanadium depuis 1850, le chrome et l’aluminium depuis 1854, le tungstène depuis 1858. Le nickel est devenu abordable depuis 1877 grâce au minerai de la Nouvelle Calédonie. Quant à la demande, elle vient essentiellement dans les années 1880 à 1900 des besoins militaires : canons, obus, blindages pour lesquels il faut des matériaux toujours plus résistants et doués des qualités particulières de dureté ou de malléabilité les mieux appropriées aux applications voulues. C’est dans le cadre de cette intense activité de recherche sur les aciers au carbone et alliés destinés à l’armement que sont développés les premiers aciers spéciaux industriels élaborés empiriquement par le procédé Martin basique. Leurs propriétés mécaniques parfois étonnantes incitent alors ingénieurs et scientifiques à chercher de nouveaux moyens de caractérisation. À mesure que ces moyens se développent (micrographie, étude des propriétés physico-chimiques, nouveaux essais mécaniques) ils conduisent à une appréciation du rôle de la structure et des traitements thermiques comme facteurs déterminants des propriétés de l’acier.
La recherche sur les aciers spéciaux à usage militaires eut lieu en France dans les aciéries du Centre qui travaillaient déjà en 1880 pour les ministères de la Marine et la Guerre, fournissant des projectiles en fonte dure ou en acier, des blindages en fer et des canons en acier (Fig. 7).
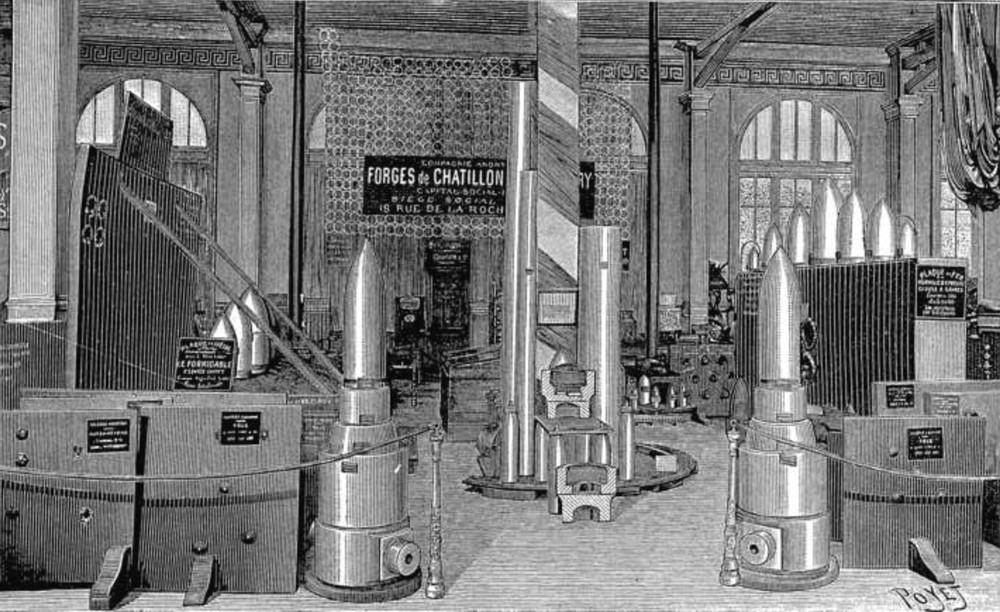
Vue générale de l’exposition de la Compagnie des Forges de Chatillon-Commentry, au pavillon du Ministère de la Guerre de l’exposition universelle de 1889.
Génie Civil, 16, 1889–90.
Il serait intéressant mais un peu trop long dans le cadre de cet article de raconter en détail tous les épisodes de la lutte sans fin entre l’obus et le blindage. Toutes les aciéries concernées s’attachent à l’obtention d’aciers spéciaux appropriés pour les obus dont elles s’efforcent d’augmenter la résistance et la ténacité à mesure que la dureté et la résistance des plaques de blindage augmentent. Elles emploient à cet effet des compositions nouvelles d’acier : obus en acier au chrome (1882), blindage en acier au nickel (1888), puis au chrome-nickel (1891), etc. sur lesquelles de nombreux essais sont effectués (Fig. 8).

Essais comparatifs des plaques de blindages à Annapolis (États-Unis).
Génie Civil, 18,1891, p. 293–301, planche XVIII.
Les premières recherches scientifiques relatives à l’influence d’un tiers élément sur les alliages fer-carbone débutent en 1892 par un travail sur les aciers au chrome dû à Hadfield, industriel de Sheffield et Osmond. C’est encore Osmond qui énonce les principes fondamentaux qui gouvernent l’action d’un tiers élément dans trois notes relatives aux aciers au nickel publiées dans les Comptes rendus de l’Académie des sciences de 1893 à 1899 [14]. L. Guillet, suivant les traces d’Osmond, montre en 1903, comment on peut classer les aciers au nickel suivant leur structure. Puis de 1903 à 1907, il étudie systématiquement les effets d’autres éléments d’alliage tels que : silicium, manganèse, chrome, tungstène, molybdène, titane, vanadium,… sur la structure et les propriétés des aciers ce qui le conduit à de remarquables analogies entre les divers aciers pour un même type de structure. Il éclaircit également l’action des traitements thermiques. Il se tourne ensuite vers les aciers quaternaires, nickel-chrome, chrome-tungstène, etc.
L’action des traitements thermiques est progressivement mieux comprise. En 1902 Charpy et Grenet déterminent par dilatométrie les températures critiques des aciers. Grenet publie en 1911 un article « Trempe, Revenu, Cémentation » qui contient des courbes très générales dans lesquelles on peut reconnaître les actuelles courbes TTT (Température-Temps-Transformations) avec un système d’axes différent. De 1904 à 1916, Le Chatelier publie une série d’études sur la trempe des aciers à outils, aciers rapides, aciers spéciaux. En 1917 Portevin publie plusieurs mémoires importants sur le mécanisme de durcissement par trempe et sur l’existence d’une vitesse critique de trempe. L’emploi des rayons X après 1912 permet de connaître les modes de cristallisation des produits métallurgiques et de voir les variations de structure apportées par la trempe. On aboutit vers 1920 à une théorie de la trempe comme conséquence de la mise en solution, à température élevée, des carbures complexes dans les aciers spéciaux. [15].
On est alors entré dans l’ère de la métallurgie scientifique dont le rôle sera de concevoir et produire le matériau adapté à une utilisation particulière. La première moitié du XXe siècle voit le développement d’une large gamme d’alliages (aciers inoxydables [chrome, nickel]), aciers pour machines à outils à coupe rapide, (tungstène, chrome, vanadium), acier résistant à l’usure (manganèse), aciers résistants aux hautes températures (nickel), sur une base qui, bien qu’encore largement empirique, est reliée à la détermination simultanée des diagrammes binaires ou ternaires.
Le nouveau procédé d’élaboration de l’acier au four électrique (brevet de Heroult 1900 Fig. 9) est particulièrement adapté aux exigences d’élaboration des aciers spéciaux : précision de la composition, haute température atteinte dans le bain qui permet de dissoudre les éléments les moins fusibles et offre donc la possibilité d’élaborer des aciers à forte teneur en métaux réfractaires. Le procédé devient opérationnel au cours de la première décennie du XXe siècle, juste au moment où l’industrie électrique et l’industrie automobile naissantes deviennent des débouchés importants pour l’industrie des aciers spéciaux qui prend de l’ampleur à partie de 1910.

Four oscillant électrique, système Héroult avec tuyères, brevet du 1er février 1901, complément du premier brevet pris pour un four à deux électrodes verticales sur bain de scorie et métal le 27 mars 1900.
Note sur l’état actuel de la question des fours électriques, AFB01G0685, « Fonds Académie François Bourdon ».
6 Conclusion
La mutation de la filière sidérurgique vers le tout acier après 1880 est à l’origine de la naissance de la science du métal (appelée métallographie autour de 1900, puis métallurgie physique, après 1914 [16]). L’utilisation massive de ce matériau aux possibilités prometteuses, mais encore souvent imprévisibles, incite alors les producteurs et les utilisateurs d’acier à se lancer dans des recherches visant à relier les propriétés mécaniques du matériau à ses caractéristiques physiques et chimiques. Une collaboration internationale active s’établit entre ingénieurs et savants autour d’un objectif commun : construire un corpus scientifique susceptible d’expliquer les comportements encore mystérieux du matériau acier. L’étude des aciers alliés, d’abord élaborés empiriquement pour répondre aux besoins militaires, puis produits industriellement, mais dont les propriétés étaient encore mal comprises vers 1900 a largement contribué au développement de la métallurgie physique. Ces aciers spéciaux connaîtront un essor prodigieux après 1910 lorsque les acquis scientifiques permettront de contrôler leurs propriétés.