1 Introduction
Knowledge of the physical properties and chemical behavior of materials at the pressure and temperature conditions of planetary interiors is required to model processes in the deep inaccessible interior of planetary bodies. Understanding the properties in high-pressure/high-temperature conditions is also of importance in materials science research as well as for exploring fundamental physics. The combination of the laser-heating technique with diamond-anvil cells (DAC) allows one to generate extreme pressure and temperature conditions and has been extensively used in conjunction with both laboratory measurements and synchrotron-based methods to make in-situ measurements of physical properties of materials (e.g., Boehler, 2000; Ming and Bassett, 1974)
Only a few years ago, high-pressure groups around the world developed compact “portable” laser heating systems (Boehler, 2009; Dubrovinsky et al., 2009; Shen et al., 2010) that drastically simplified the application of laser heating to DACs and opened the perspective for new type of experiments, including single-crystal XRD in the laser-heated DAC (Dubrovinsky et al., 2010). These developments were triggered by the increasing availability of compact high-power fiber lasers emitting radiation with a wavelength of approximately 1 μm. Fiber lasers are convenient to handle and are a prerequisite to develop “portable” laser heating systems, where the focusing optics that need to be close to the DAC are connected to the laser only by a thin optical fiber that can be several meters in length. However, despite the convenience in handling fiber lasers, heating with a 1-μm laser has several potential disadvantages as compared to heating with 10-μm-wavelength radiation delivered by a CO2 laser. Most importantly, a wide range of materials cannot be heated using 1-μm laser radiation because of low laser energy absorption. In these cases, a laser-absorber has to be added that can potentially react with the sample material and lead to inhomogeneous temperature distributions. CO2-laser radiation, in contrast, is sufficiently absorbed by most materials (e.g., Kimura et al., 2014). Further possible disadvantages of laser heating with 1-μm laser radiation as compared to 10 μm radiation, include (1) the possibility of localized heating due to an inhomogeneous distribution of the absorber (e.g., iron in most Earth relevant samples), (2) strong axial T-gradients as a result of limited penetration depths, (3) possible Soret diffusion of iron (Sinmyo and Hirose, 2010), and (4) the high laser input power needed for many samples that only weakly absorb the 1-μm laser radiation.
Heating with a CO2 laser that emits laser radiation with a wavelength of 10 μm overcomes most of these problems. However, CO2 lasers have been more complicated to handle and therefore their application to high-pressure diamond-anvil cell research has been restricted to few stationary heating setups (e.g., Petitgirard et al., 2014; Yagi and Susaki, 1992; Zhang et al., 2015). The increasing availability of 10-μm-wavelength transmitting waveguides opens the possibility to design flexible CO2-laser heating systems that can be conveniently used in combination with a variety of experimental probes. In principle, two different types of fibers have been designed that are capable of transmitting light of 10-μm wavelength. The first category consists of a solid polycrystalline core (such as AgBr) to guide the laser. The advantage of this type of fiber is its large acceptance angle that should allow simple coupling of laser light into the fiber. The disadvantage is the significant power loss throughout the fiber and its limited laser power stability. The second category that has been recently developed are Hollow Silica Waveguides (HSW) that transmit CO2 laser radiation through internal reflections. HSW show low power losses during wave transmission, but are characterized by very small acceptance angles (about 1°), complicating laser light launching. However, their low power loss, combined with a high power damage threshold, good mechanical stability, and unique optical properties (Kriesel et al., 2011) make them very promising as laser guides for a flexible laser heating system. Here we report results of test experiments, where a CO2 laser was coupled with a commercially available Hollow Silica Core Waveguide in order to design a flexible waveguide-based CO2-laser heating system for high-pressure/high-temperature research.
2 Materials and methods
Our prototype laser heating system is based on a 100-W Synrad Firestar CO2 laser, either fan- or water-cooled. The fan-cooled laser offers higher flexibility at the cost of reduced power output stability. A commercially available coupling module was mounted to the front of the laser (LaserComponents “FiberKey P”) (Fig. 1). The HSW-coupler allows the simultaneous coupling of a green guide laser that is inserted from the side in the coupling unit and is then transferred to the cladding of the CO2 waveguide. The CO2 waveguide is mounted to the coupling module using a standard SMA-connector. In our tests, we used a HSW with a core diameter of 1000 μm from LaserComponents, see also Kriesel et al. (2011). The end of the HSW is mounted to a “cage” system using the SMA connection. Different combinations of 1-inch-diameter ZnSe lenses have been used to collimate and focus the laser beam on the sample. Most of the here-reported experiments have been conducted with a combination of two ZnSe, where f = 20 cm for laser beam collimation and f = 5 cm for focusing on the sample. A focusing spot of about 150–250 μm is achieved with the chosen set of lenses. The green laser beam that is transmitted through the same waveguide can be used for first rough alignment of the laser beam. We also used the green laser for initial focusing by first focusing the green laser and then applying a calibrated correction to account for the difference in focal distance between visible light and the 10-μm CO2 radiation. The sample is monitored using an objective combined with a CCD camera. Temperature measurements have been performed by spectroradiometry employing either a separate lens system or using the Brillouin collecting optics. The signal was analyzed using a Princeton Instruments “Acton” Spectrometer with a PIXIS camera. The software “T-Rax” (by C. Prescher) was employed to derive the temperature from one side of the sample. The calibration of the temperature measurement was performed using a calibrated tungsten vacuum lamp.
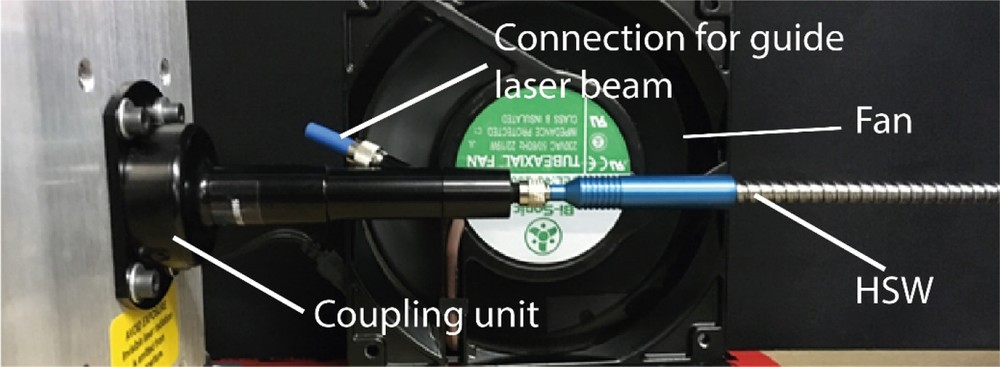
HSW-coupling unit mounted to a fan-cooled CO2 laser. The fan is used to cool the coupling unit during high-power operations.
3 Results and discussion
3.1 Performance of the HSW
To evaluate the capabilities of the HSW for laser-heating applications and the power losses within the HSW and the coupling unit, we monitored the loss of power as a function of the laser output power (Fig. 2a). We performed two test series, where (1) the HSW was installed straight and in line with the laser and (2) where the HSW was set up with a 90° curvature (r = 30 cm). After careful alignment of the coupling unit, we generally find power losses on the order of 20–30% (Fig. 2b). These losses are caused by energy dissipation during waveguide launch and during transmission. The increase of power loss caused by the introduction of a single curvature into the HSW is comparably small (Fig. 2b), see also Kriesel et al. (2011). We also tested power stability with time for two test setups where (1) a single-bend 90-cm-long HSW was used and (2) a double-bend 300-cm-long HSW was tested. The laser was operated at a fixed output power and the power variations at the exit of the HSWs were measured for approximately 20 min using a power meter. In both setups, power variations with time were on the order of 1–2% after laser stabilization, which leads to power variations in the first few minutes of laser operation (Fig. 3).
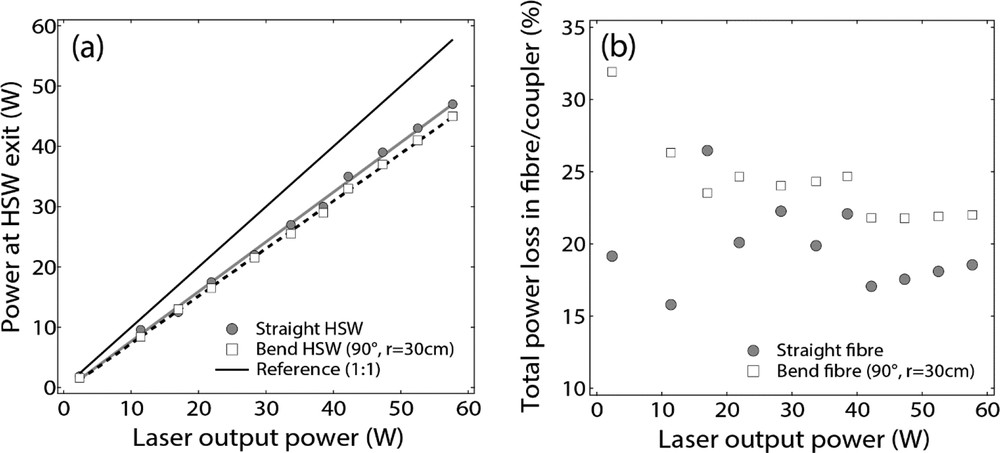
Power output at HSW-exit as a function of the laser output power for two different test setups (a). Combined power loss during laser coupling and transmission through the HSW for both our test arrangements (b).
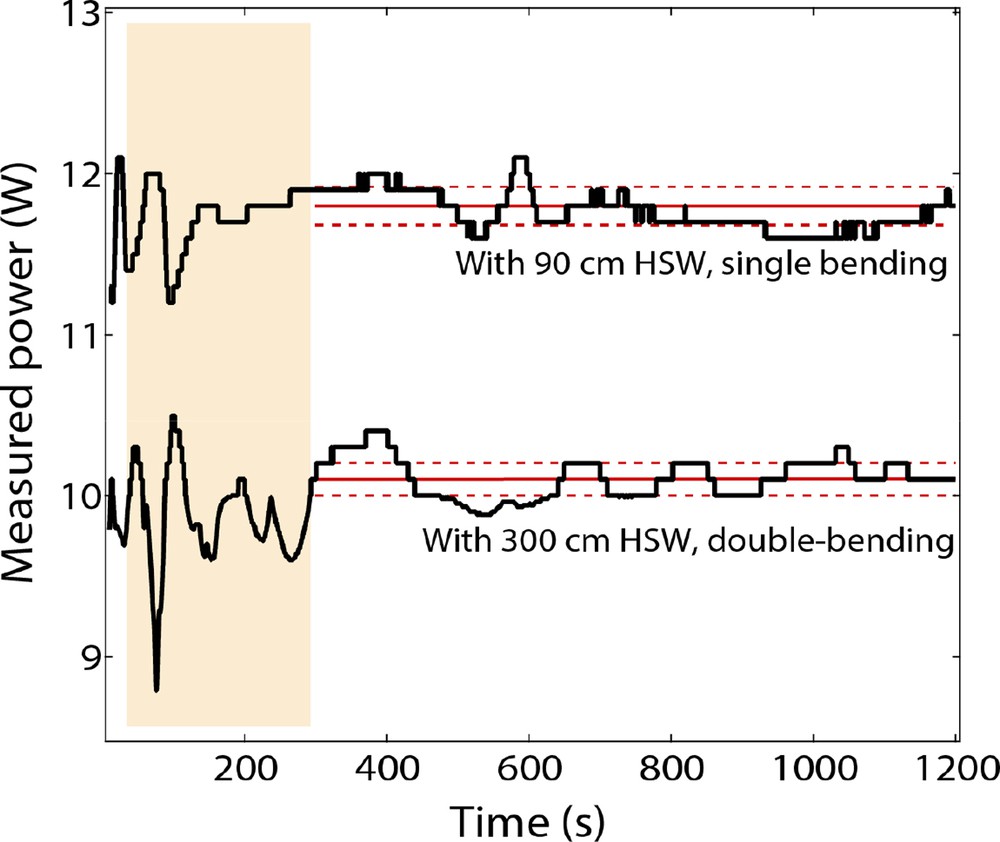
Variations of laser power measured at the HSW exit with time for two different test setups. Variations of power in the first ∼300 s are related to the initial stabilization of the laser itself (shaded region). The red line represents the average power calculated after > 300 s, the dashed lines are calculated as average value ±1%. After laser stabilization, the power measured at the HSW exit is mostly stable within 1–2%.
3.2 First applications using the HSW-based CO2-laser heating system
3.2.1 Heating in air and in the diamond-anvil cell
In the first test experiments, we employed the waveguide-based system to heat a thin foil of platinum as well as a single crystal of MgO. The melting of platinum at 2041 K was used to verify the temperature calibration. Fig. 4a shows a temperature/power curve measured for single-crystal MgO as an example. We also used the waveguide-based CO2-laser heating system to heat a single crystal of MgO inside a diamond-anvil cell. A photograph of the heated sample in the DAC is given as an inset in Fig. 4b, a measured temperature curve is shown in Fig. 4b. In the DAC run, diamonds with culet sizes of 250 μm were used. Neon gas was loaded to protect the sample and serve as a thermal insulator. The MgO sample was tilted inside the pressure chamber to avoid contact with the diamonds. Rhenium was used as gasket material and did not visibly heat. The measurement was performed at low pressure (< 1 GPa). The tests generally showed that the waveguide works reliably and can be applied to heating in air and in the diamond-anvil cell.

Heating tests using the HSW. Measured temperature-power curve for single-crystal MgO (a). Typical temperature curve measured from the heated MgO single crystal inside the diamond-anvil cell. Inset: heated MgO sample inside a diamond-anvil cell (b).
3.2.2 High-temperature Brillouin spectroscopy
We demonstrate the capabilities of the prototype laser heating system by successfully measuring the velocities of acoustic waves in single-crystal MgO up to a temperature of 2500 K. For this application, our proto-type flexible CO2-laser heating system was connected to a fan-cooled Synrad Firestar laser with a 300-cm-long HSW. The setup was attached to the Brillouin scattering system at BGI Bayreuth, Germany (Fig. 5). A single crystal of MgO was heated and Brillouin spectra were collected at different laser powers/temperatures (Fig. 6). Signal collection times were generally about 10–60 s. We observed an increase of the Brillouin signal strength upon initial heating. At higher powers, the quality of the Brillouin spectra decreased as a result of the rapid increase of the thermal background with temperature, consistent with previous observations (Sinogeikin et al., 2004), see Fig. 6b. The sample's temperature was determined by spectroradiometry through the Brillouin collecting optics. This ensured that both Brillouin signal and temperature are derived from the same part of the MgO sample. During temperature measurements, a mirror was inserted in the collecting light path to guide the light to the spectrometer.
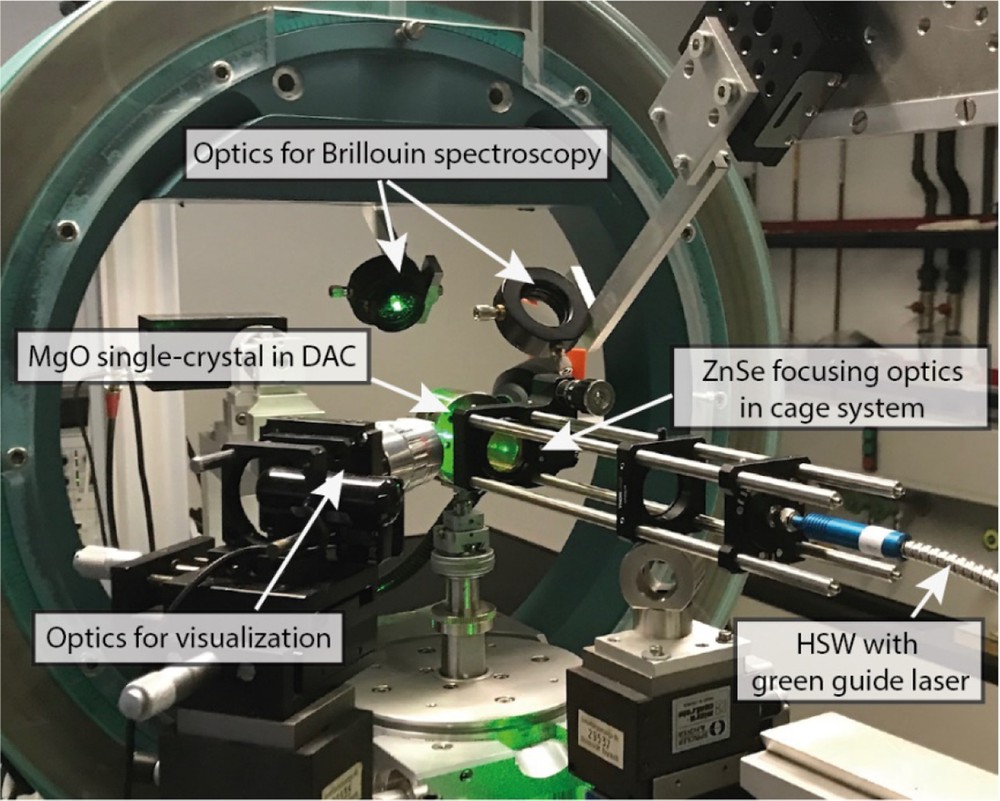
Experimental test setup. A test version of the HSW-based CO2-laser heating system mounted on the Brillouin system. The three-meter-long HSW is connected to the front of a 100-W fan-cooled CO2 laser. A visible guide laser beam is inserted into the fiber from the side and is transmitted through the waveguides cladding. In a first proof-of-concept test, a single crystal of MgO was heated to measure sound wave velocities of single-crystal MgO at high temperatures (see Fig. 6). Thermal radiation was collected through the Brillouin collecting optics. Masquer
Experimental test setup. A test version of the HSW-based CO2-laser heating system mounted on the Brillouin system. The three-meter-long HSW is connected to the front of a 100-W fan-cooled CO2 laser. A visible guide laser beam is inserted into the ... Lire la suite

Application of the flexible CO2-laser heating system for sound wave velocities using Brillouin spectroscopy. Measured acoustic wave velocities of single-crystal MgO along <110> at 2500 K (solid symbols); no temperature measurement was possible by spectroradiometry below ∼1000 K (shaded region) (a). Open symbols have been previously measured using resistive-heating (Sinogeikin et al., 2000). Brillouin spectra collected at different temperatures; note the strong increase of the background signal (signal/noise ratio) with temperature (b). The typical collection time was about 10–60 s.
3.3 Possible limitations of laser-heating operations using the HSW
The observed energy losses are mostly caused by energy dissipation at the entrance of the HSW as well as within the HSW. Particularly at the coupling unit, this leads to a significant temperature increase at high laser powers (Fig. 7a). We monitored the temperature of the coupling unit as a function of the laser output power using an infrared-sensitive camera. We observed that slight misalignments of the waveguide coupler dramatically increase the heating of the coupler. This is likely a result of the very limited acceptance angle of the HSW, requiring a careful alignment of the waveguide coupler for high-power operations. The coupler contains a focusing lens that serves to focus the light emitted from the laser into the HSW. The exact position of the focusing lens can be adjusted by three screws that are accessible from the outside of the coupler. Using the peak temperature values as shown by the infrared camera observation, we find that peak temperatures in the coupler observed after 1 min of laser exposure linearly depend on the laser output power (Fig. 7b). We performed a simple test to evaluate the improvements that can be expected from external cooling by employing a small fan to cool the waveguide coupler. It becomes clear from Fig. 7c that the installation of the cooling fan significantly decreased the amount of heating and lead to a faster stabilization of the coupler's temperature. In the test example, the laser power exciting the HSW is about 17 W, i.e. high enough for many applications, even in the diamond-anvil cell. We also monitored a possible heating at the waveguide exit, but found it to be on the order of a few degrees, even at high powers. In order to facilitate high-power applications, a water-cooling jacket could be installed around the tip of the coupling unit.
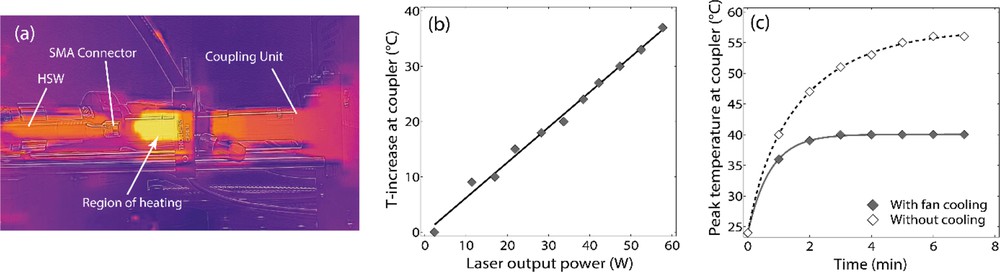
Temperature distribution observed in the HSW coupling unit (a). The temperature map shows that heating is localized to the region where the HSW enters the fiber coupler. Peak temperature of the laser coupler as a function of the laser output power measured after 1 min of lasing (b). Peak temperature evolution with time for a power at the HSW exit of 17 W and effect of using a cooling fan (c).
Other significant power losses can occur within the HSW itself. Even though the HSW offers a significant degree of flexibility, it can suffer from internal damage that lead to local heating spots within the waveguide. To monitor this, we removed the metal shielding from one of the commercial waveguides that we extensively used for high power tests and bending operations (Fig. 8). Within the waveguide, damaged areas were sometimes visible through visual inspection. In these regions, the outer polycrystalline tube is broken and the coating on the inside might be affected (Fig. 8a). Local hot spots develop around the damaged regions and energy loss during laser transmission through the HSW increases (Fig. 8b). Besides the visual inspection, minor damage to the HSW can be monitored by sending visible laser light through the waveguide (Fig. 8c).
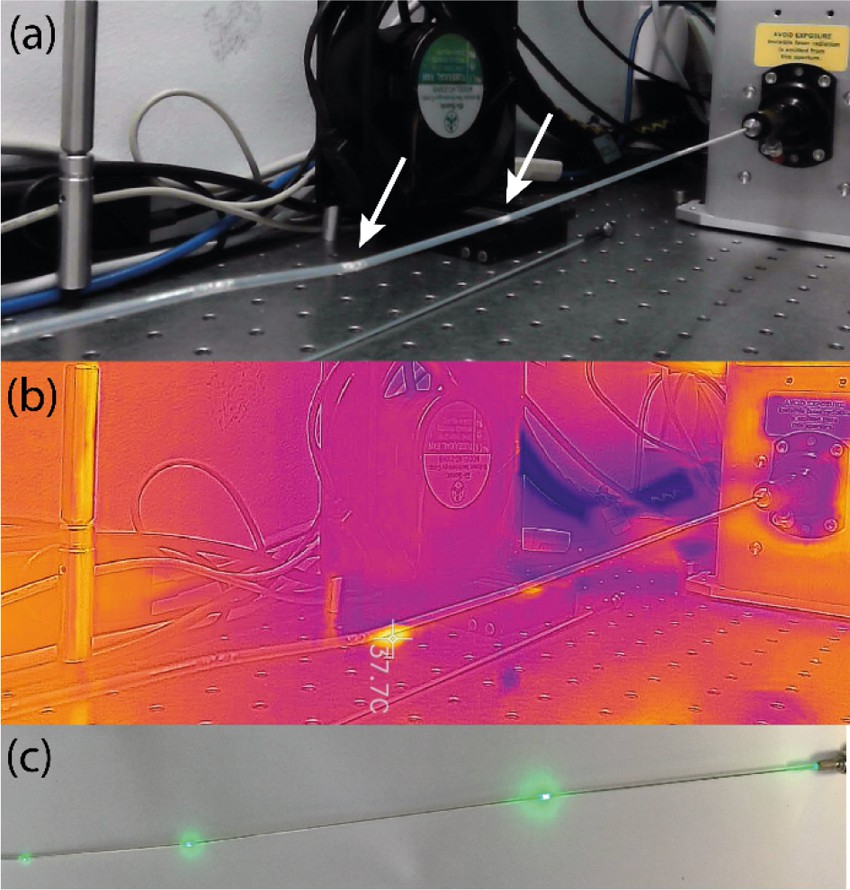
HSW with removed metal tubing to monitor local damages. High-power applications and extensive bending can lead to local damages to the HSW. Major damages can be observed visually and are indicated by arrows (a). Damaged regions lead to local hot spots within the HSW that increase power losses during laser light transmission and can cause further damage to the HSW (b). Visible laser light can be used to monitor the physical condition of the HSW (c).
4 Conclusions and outlook
We have shown that commercially available HSW facilitate flexible CO2-laser heating applications. In the first experiments, we have coupled the system with a Brillouin scattering setup and measured acoustic wave velocities of a single crystal of MgO at high temperatures and ambient pressures. We have also used the system in conjunction with a diamond-anvil cell to show the feasibility of heating samples at high pressure. Since CO2-laser heating has several advantages with respect to the more frequently employed flexible laser heating systems that employ a 1-μm wavelength laser, we expect that this study sets the basis for a number of future applications that take advantage of this new possibility. In the future, we plan to integrate both the visualization and the temperature measurement optics into the cage-based system in order to construct a fully self-standing flexible CO2 heating system. The waveguide-based CO2-laser heating system offers unique perspectives for future experimental research using diamond-anvil cells both in laboratory environments and at synchrotron facilities. We note that the combination of this new approach with the recent advance of sophisticated sample preparation techniques employing the focused ion beam offers new perspectives, particularly for single-crystal studies (Marquardt and Marquardt, 2012). Finally, we note that the HSW that we inspected after intensive high power operations (> 50 W) showed significant internal alterations. Future studies should therefore systematically test the power (and time) threshold that should not be exceeded during laser-heating experiments.
Acknowledgements
This research was supported through the projects “GeoMaX” funded under the Emmy-Noether Program of the German Science Foundation (MA4534/3-1). HM acknowledges support from the Bavarian Academy of Sciences. We acknowledge discussions with Z. Konopkova (European XFEL), W. Morgenroth and L. Bayarjargal (University of Frankfurt) as well as F. Taechl and F. Gerg from LaserComponents. We further acknowledge technical support by Sven Linhardt.