1 Introduction
1.1 Polyphosphate glasses
Polyphosphate glasses are interesting for different applications because of their low glass transition (Tg) and devitrification and melting temperature (Td and Tm) and their high coefficients of thermal expansion (CTE) 〚1, 2〛. On the other hand, their chemical durability in non-aqueous liquids compounds such as molten metals or aggressive inorganic and organic compounds may be of practical interest 〚1〛. Other applications derive from their chemical reactivity in the liquid phase. For example, it is possible to use them as sealing or coating agents (glazing and enamelling) 〚2〛. Therefore, two industrial fields may be considered for applications: the high-temperature range between 800 and 1000 °C and the low-temperature range below 400 °C. This later case corresponds to the P2O5–Na2O–ZnO glasses, for which Tg < 300 °C and even smaller when Ag2O enters glass composition 〚3〛.
Usually polyphosphates glasses are obtained through polycondensation reactions between hydrogenophosphates powders 〚1, 4, 5〛. Nevertheless, this route starting from metaphosphate glasses present some disadvantages for sealing or coating processes in an industrial site for pieces with a complex shape. For this reason, a sol–gel-like approach may be more appropriate to obtain these glasses: the coacervation.
1.2 Coacervates
Bungenberg De Jong and Kruit introduced the term of coacervate in 1929 〚6〛. It means that polymer particles may come together in a heap. Polyphosphates are non-soluble in inorganic or organic solvent, and sodium salt is the only salt soluble in water. Furthermore, polyphosphates do not give polycondensation reactions in aqueous solution.
So the initial products are the Graham salts, which are sodium compounds that may be described as a mixture of glasses with different chains length distributions. By changing the chemical characteristics of the sodium polyphosphate solution – electrolyte addition or modifications of solvent properties – miscibility gap appears leading to a two-phase system. It is a simple coacervation phenomenon. The denser phase, rich in colloid, is called coacervate. It contains water, long polyphosphate chains and cations, including sodium, coming from the Graham salts. The DLVO theory provides the first and limited explanation of their formation 〚7, 8〛. On heating, coacervates lose most of their water 〚9〛, leading after several steps to a glass 〚10〛.
The first works dealing with coacervates 〚5, 11–13〛 concern calcium and magnesium polyphosphates. Draoui obtains polyphosphate coacervates with transition metals in 1992, in particular with zinc salts 〚14〛. More recently, zinc–sodium polyphosphate coacervates have also been reported 〚15〛.
1.3 Coacervates as precursors for zinc polyphosphate glasses
In order to obtain polyphosphate glasses suitable for industrial application, the chemical and physical characteristics of the coacervates precursors must be controlled. For example the chains lengths, the ratio Na/M2+ (e.g., Zn2+) directly influences viscosity, surface tension, wettability, and reactivity of coacervate 〚16〛, and evidently the properties of the glasses obtained after firing. The water content and its exhaust during the curing step is also an important parameter for industrial applications. In a same way the vitrification of the coacervate may be obtained after encapsulation of ceramic particles or fibres 〚17–19〛. In this last case, the coacervate may be generated directly around of fibres or particles during formation stage 〚17, 19〛. Finally, the pH of the initial solutions has also to be controlled.
Usually, preparation of polyphosphate coacervate is made in the following way. We start from two solutions. The first is a concentrate solution of Graham salt (Merck), and we put slowly drop-by-drop inside a zinc salt solution, with an important stirring. After 15 to 30 min, depending on the viscosity of the mixture, the coacervate is obtained as the consequence of the miscibility gap.
In aqueous solution, coacervate formation is observed with different zinc salts, for example, with fluoride, chloride, iodide, nitrate and acetate. When other salts, such as sulphate and gluconate, are used, the method described by Umegaki et al. 〚20〛 is recommended. An addition of ethanol or methanol allows one to form the coacervate phase from the mixing of the two solutions.
This work will present our results for the coacervate formation from three zinc salts: chloride, nitrate and sulphate.
1.4 Experimental
Sodium polyphosphate was selected from Merck because its chain is long, about of 15 PO3 units.
The chemical analysis of sodium, phosphorus and zinc was implemented by ICP–AES. Differential Thermal analysis (DTA) and ThermoGravimetric analysis (TGA) were made using a simultaneous DTA–TGA equipment (Setaram TG92). Powdered samples were heated at 5 K min–1 from ambient temperature to 1000 °C, under a 60 ml min–1-flowing argon. Thermal expansion (CTE) was measured using a dilatometer Netzch DIL 402 under static atmosphere. Scanning Electron Microscope (SEM) pictures were obtained with a JEOL-T330A set-up. Chain lengths of polyphosphate was checked by Nuclear Magnetic Resonance (NMR AM300 Bruker.). Viscosity data of coacervates were obtained at 20 °C, with a Rheometer Carri-Med CSL using a 4-cm steel plate with 7.850-μN m s2 inertia.
2 Coacervation in the NaPO3–ZnCl2–H2O system
2.1 Concentration conditions
To define the conditions of coacervation, in this system, several solutions of Graham’s salts of various concentrations are prepared. One of these is placed in a thermostatic vessel at room temperature. The solution is continuously stirred while a ZnCl2 solution, of known concentration is added, until coacervation begins. Molar concentrations of water, sodium polyphosphate, and ZnCl2 are calculated. The corresponding results are reported in a usual graphical representation 〚21〛. The beginning of the coacervation phenomenon has been characterised by a direct visualisation of the cloudiness of the mixture. It is further confirmed by the observation of the phase separation with a binocular microscope. Our results are displayed in Fig. 1. In this figure, concentrations are expressed in moles and the line of the diagram links indicates the two-phase system (coacervate/equilibrium liquid) when starting from a sodium polyphosphate solution 〚22〛.The limit of coacervation for a mixture with a too high ZnCl2/NaPO3 ratio is given by the points in the right part of Fig. 1. Thus, the coacervate conditions of formation are easily checked. It is possible for industrial application to start directly from ZnCl2 and NaPO3 in a powder state 〚2〛. Their addition to a convenient quantity of water (as defined by the point chosen on the diagram of Fig. 1) with an important stirring gives the same result as the one obtained by mixing two solutions.
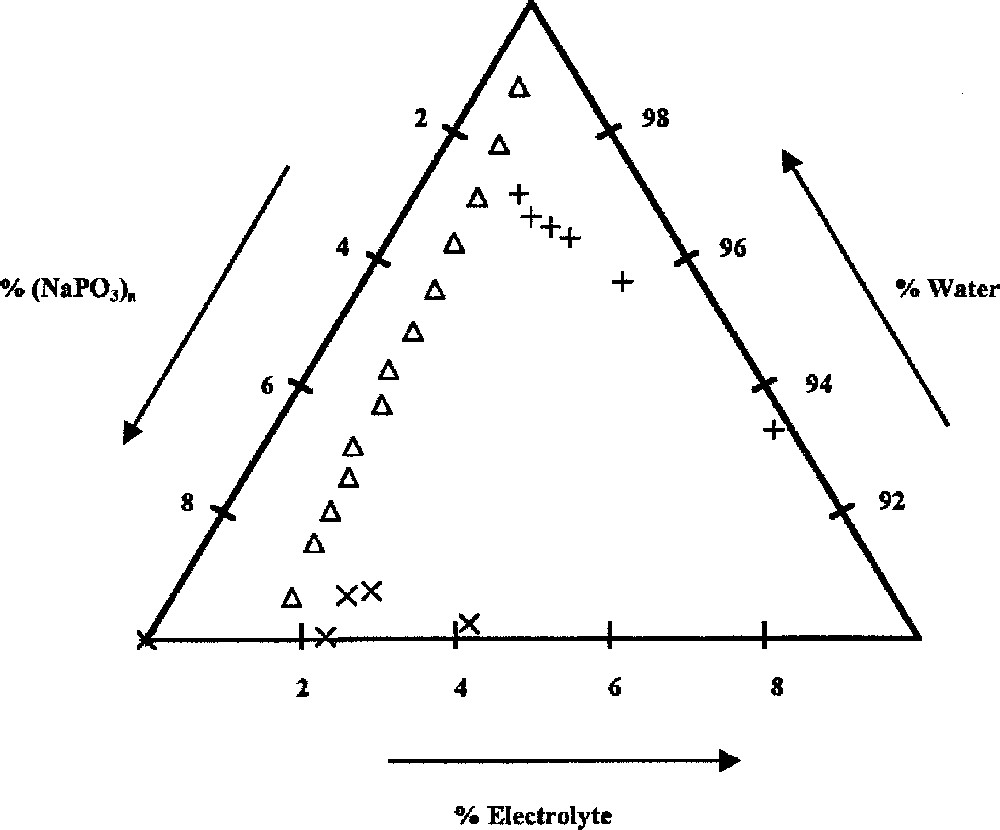
Determination of the limits of coacervate formation from solutions rich in sodium polyphosphate (▵) or rich in zinc chloride (+). The × characterise the area of coarcevate formation by zinc nitrate addition to sodium polyphosphate.
These coacervates are glass precursors; so it is important to know beforehand the ratio of Zn/Na in the glass. Fig. 2 shows the continuous proportionality between the initial ratio Zn/Na of the solutions and the Zn/Na ratio in the coacervate, which is also that of the glass. This allows us to control the glass composition using coacervate formation.
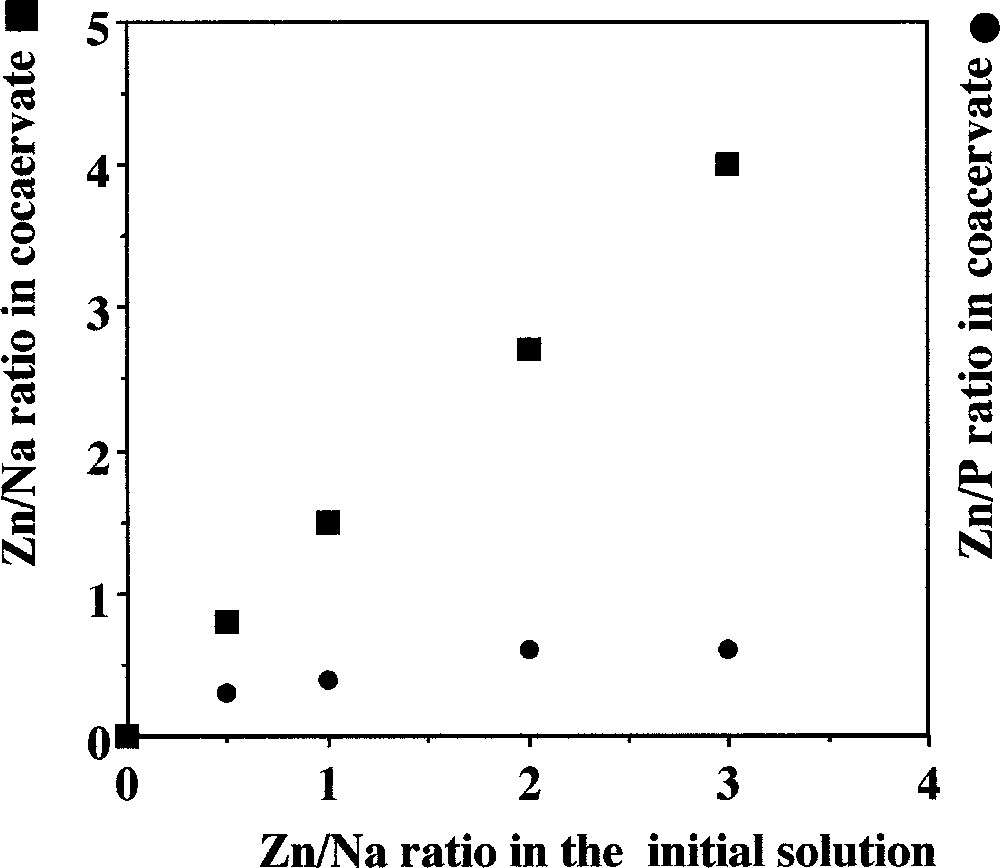
Evolution of the Zn/Na and Zn/P ratios in the coacervate in relation with the Zn/Na ratio in the initial mixture for the sodium polyphosphate–zinc chloride system.
2.2 Influence of pH
It is useful to control the pH during the formation of coacervates, when they are used for joining or coating applications, because acidity may interfere with the chemical properties of the substrates. The formation of coacervate needs the proton releases of the P–OH groups at the ends of the polyphosphate chains 〚7, 8〛. For this reason, the pH of the solution decreases during the coacervate formation. In this way, it is possible to obtain polyphosphate coacervates based on calcium salt, even at basic pH 〚8〛. For the polyphosphate coacervates based on zinc, we start from sodium polyphosphate solutions at different pH values, which are adjusted by adding solid soda. The evolution of the pH of the supernatant solution during this experimentation has been measured (Table 1). For example, if we start from a 3-M solution of sodium polyphosphate and a 2-M solution of zinc chloride, the final pH is below 3, while the pH of the two initial solutions is around 4.4. This result confirms the proton exhaust from the terminal P–OH groups.
Evolution of the pH of the solution in the system sodium polyphosphate–zinc chloride during coacervate formation.
pH NaPO3 | pH of coacervate formation | pH of supernatant liquid after 30 min | pH of supernatant liquid after 15 h |
4.4 | 1.69 | 1.68 | 1.54 |
5.15 | 2.18 | 1.95 | 1.81 |
5.96 | 2.9 | 2.4 | 2.35 |
6.57 | 3.53 | 3.15 | 2.97 |
6.95 | 4.23 | 3.66 | 3.44 |
8.63 | 5.42 | 4.81 | 3.74 |
10.42 | 5.49 | 4.87 | 3.75 |
12.42 | 5.76 | 4.95 | 3.83 |
We have confirmed that coacervate formation is a kinetic phenomenon 〚8〛. Table 1 also reports the pH of the beginning of the coacervation phenomenon, and the evolution of the pH of the supernatant liquid after 30 min and 15 h, as the field of coacervate formation. In each case, we can see that the coacervate formation induces the pH decrease.
2.3 The chain length
As pointed out previously, the average chain length of the Merck Graham’s salt coacervate, as measured by phosphorus NMR, is around 15 PO3 units. Fig. 3 shows that chain length increases with the Zn/Na ratio. We have also seen that, at basic pHs, the lengths of the long chains are stabilised during a longer time than for acidic pHs, for which the kinetics of the chain cutting is increased.
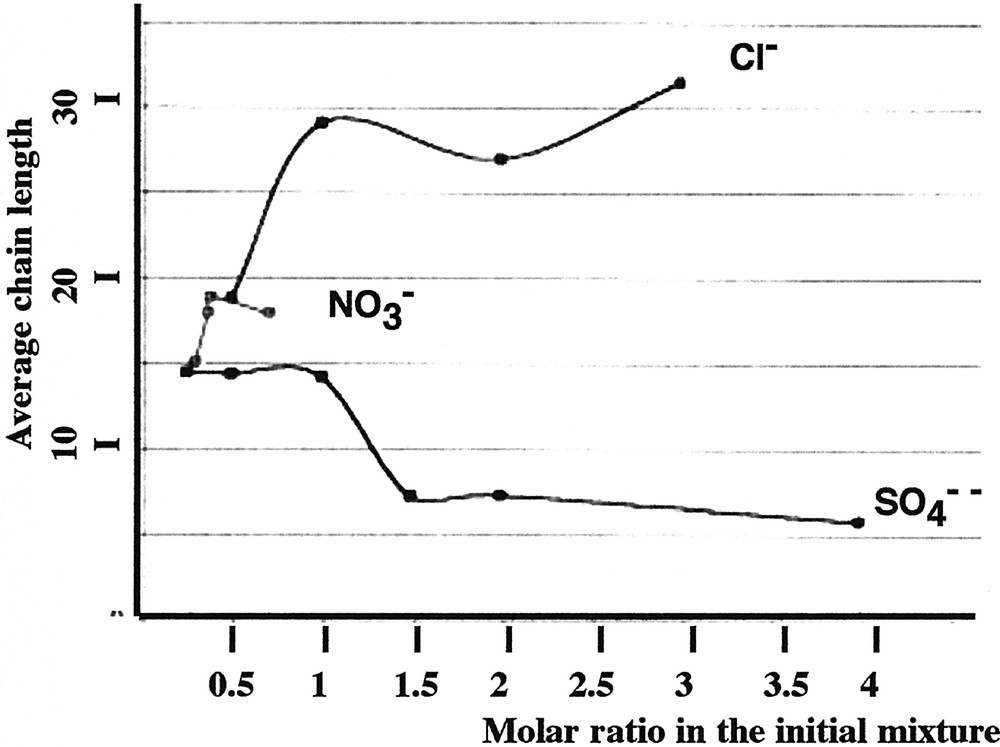
Evolution of the average chain length (determined by NMR) as a function of the molar ratio in the initial mixture for three systems: sodium polyphosphate and zinc chloride, zinc nitrate, zinc sulphate.
These results are of practical interest for the use of coacervates in dip and spray coatings, because the chain length influences viscosity. Note that coacervate viscosity exhibits a Newtonian behaviour 〚16, 23〛. This is the case of the calcium coacervates 〚16〛, for which viscosity increases during the first hour after their obtention. This is the time necessary for the release of the residual water inside the coacervate. A constant viscosity value is obtained after a few hours. This limiting value depends on composition: as in other coacervates, we observe that, after stabilisation, viscosity increases with the ratio Zn/Na (Fig. 4). However, at higher ratios, the viscosity tends towards the same value.

Evolution of the coacervate viscosity as a function of the Zn/Na ratio.
2.4 The water exhaust
Using coacervation in industrial applications also requires the control of the water exhaust during the drying step. To characterise water exhaust, we have chosen a new thermal analysis method: the CRTA (Controlled transformation Rate Thermal Analysis) 〚24〛. In a conventional thermal analysis, a physical or chemical property X is measured, while a predetermined program of heating is applied. In CRTA, the roles of ‘thermometer’ and X-meter are exchanged, so that it is now the physical property X that follows a predetermined program, such as a linear increase versus time. Then the induced changes in the heating of the sample are recorded. The final plot expresses the evolution of the required heating power as a function of the X value.
In the present case, the property X is the partial pressure of the evolved gases (that is water pressure), which is correlated to the rate of the reaction itself. The residual pressure in the close neighbourhood of the sample was kept constant at the value of 2 × 10–3 mbar during the experiment. The sample is a zinc–sodium coacervate (4% NaPO3–4% ZnCl2–92% H2O in molar ratios) partly dried at room temperature. One could expect that different types of water molecules coexist in the material, depending on the local structure or the chemical species in which they are embedded. Fig. 5 shows our result. Apart from a weak peak around 100–120 °C attributable to an exhaust of residual water, we have only a weak variation at 290–300 °C, but an important raise of temperature at the end of the experimentation. As the heated coacervate gives a glass, the first temperature peak corresponds to the Tg of the glass while the second one corresponds to dehydroxilation 〚25〛. This result confirms the lack of stable hydrate in coacervate. A similar result has been observed for polyphosphate coacervate in another system 〚26〛.

CRTA study of coacervate obtained in the system sodium polyphosphate–zinc chloride.
An important consequence of this behaviour concerns the use of coacervate for sealing applications because it is possible to control the dehydration phenomenon without foam formation.
3 Coacervation in other Na–Zn systems
3.1 Coacervation in the NaPO3–Zn(NO3)2–H2O system
3.1.1 Concentration conditions
We have used the same synthesis conditions as for zinc chloride. The conditions for coacervate formation are reported in Fig. 1 as an area in a ternary representation. Initial solutions should be more concentrated than ZnCl2 solutions. In the view of the small formation area, the choice of the possible Zn/Na ratios is limited. Nevertheless, as shown in Fig. 6, the Zn/Na ratios in initial solutions and in coacervates are strictly correlated, the proportionality coefficient being close to 1.
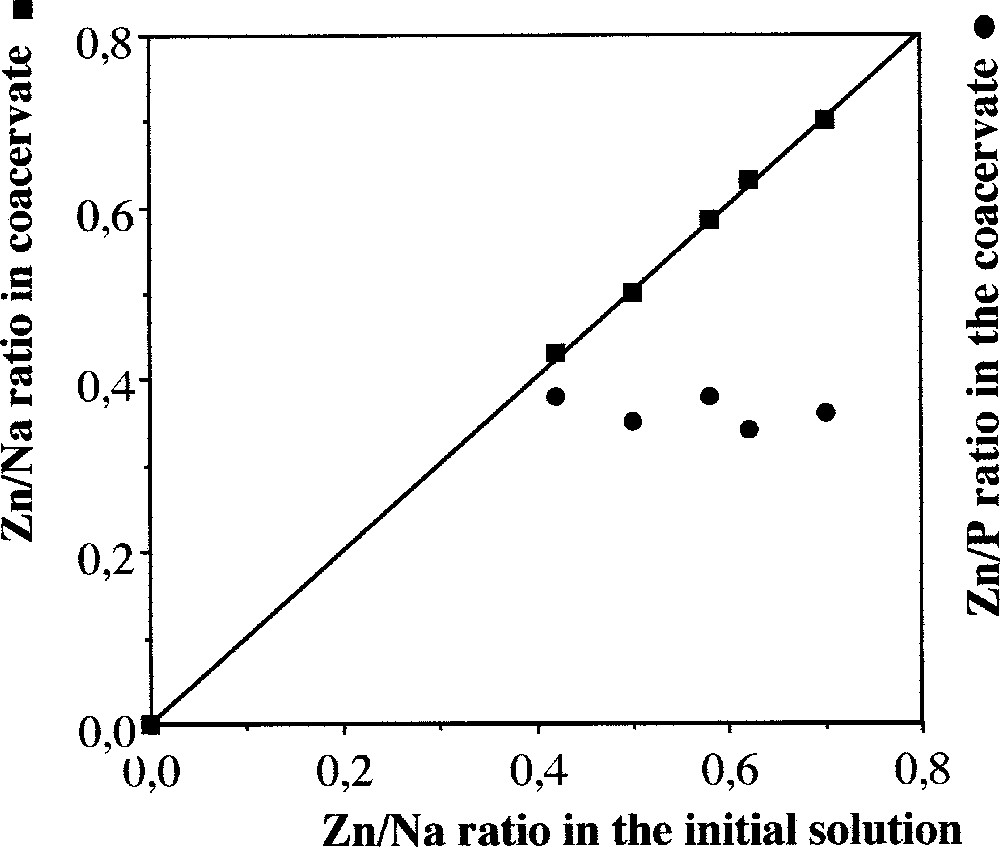
Evolution of the Zn/Na and Zn/P ratios in the coacervate as a function of the Zn/Na ratio in the initial mixture in the sodium polyphosphate–zinc nitrate system.
3.1.2 Influence of pH
The influence of the initial pH on the coacervate formation has been studied by the same method as described for ZnCl2 based system. As exemplified by two examples in Table 2, it is possible to obtain coacervates starting from high pH. As for the ZnCl2-based coacervates, the pH of the initial solution decreases because of the transformation of the chain ends 〚7〛. This pH evolution versus time is ruled by the formation kinetics of the coacervate phases 〚8〛. These results contradict previous report by Palavit et al. 〚15〛.
Evolution of the pH of the solution in the system sodium polyphosphate–zinc nitrate during coacervate formation.
pH NaPO3 | pH of coacervate formation | pH of supernatant liquid after 30 min | pH of supernatant liquid after 15 h |
5.85 | 2.5 | 1.9 | 1.75 |
8.58 | 4.55 | 2.8 | 2.4 |
3.1.3 The chain length
Some measurements of the chain lengths have been carried out. They appear in Fig. 3. In spite of the limited formation area (see Fig. 1), different Zn/Na ratios have been used.
3.2 Coacervation in the NaPO3–ZnSO4–H2O system
Adding ZnSO4 solution to sodium polyphosphate solution, even using high concentrations, does not lead to coacervate formation. But methylic alcohol addition makes it possible 〚7, 20〛. Nevertheless, for large amounts of alcohol, we often obtain a precipitate with a small quantity of coacervate.
The addition of methanol to the mixture of sodium polyphosphate solutions and zinc sulphate solutions influences the yield of the coacervate formation. Fig. 7 shows this evolution drawn as the yield evolution expressed in coacervate volume versus the relative quantity of added methanol. Results are reported for two Zn–Na ratios in the initial mixture.
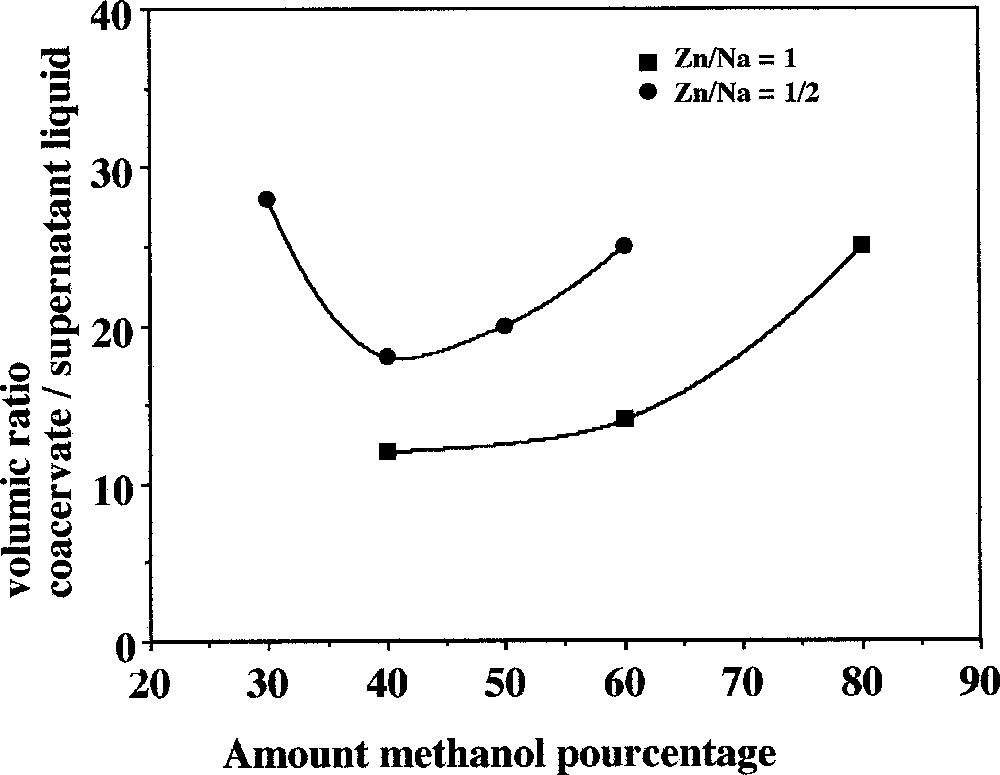
Yield of coacervate formation as a function of the added methanol in the sodium polyphosphate system.
Fig. 8 shows the results obtained for a constant quantity of methanol (40% in volume) and different Zn/Na ratios in initial solution. When this ratio is < 1, the evolution is similar to those observed with chloride and nitrate. For example, the ratio Zn/P tends toward a value of 0.6. But for higher Zn/Na ratios, the ratio Zn/P in the coacervate increases significantly. By NMR study, we have determined the average value of the chain length. As shown in Fig. 3, this value is the same as the initial one, even when Zn/Na ratio is 1, which is around 15 PO3 units. But for higher values of the initial Zn/Na ratio, the chain length decreases to an average value that does not exceed 6 to 8. This result exemplifies the shortening of the polyphosphate chains by chemical cutting. So the chemical analysis of the coacervate and the chain length determination are consistent and lead to the conclusion that the formation of coacervate requires a Zn/Na ratio not higher than 1 in the presence of 40% of methanol. For higher values, most of the coacervate is destroyed, leading to the precipitation of the zinc–sodium phosphate salts.
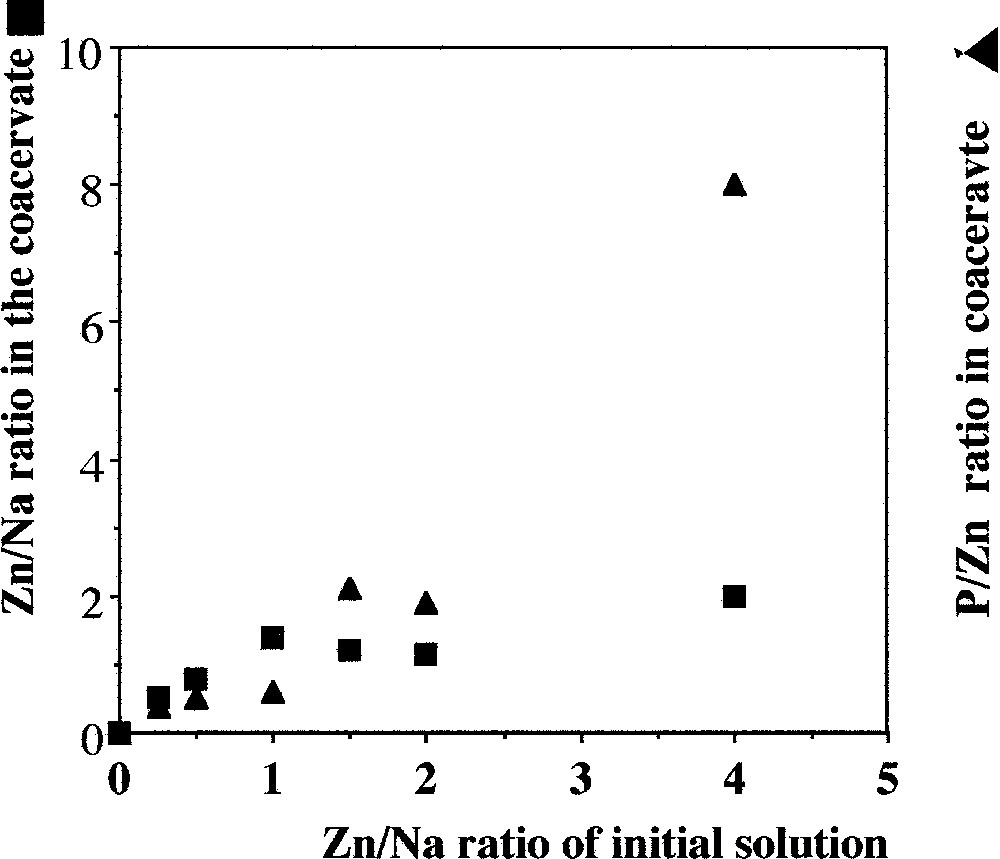
Evolution of the Zn/Na and P/Zn ratios in the coacervate in relation with the Zn/Na ratio in the initial mixture. The results are been obtained after addition of 40% of methanol in volume.
4 Discussion
This work confirms previous results about the obtention of coacervates 〚8, 22, 25〛. The assumption that the coacervation phenomenon requires an acidic pH is erroneous, although this statement was made for zinc coacervate 〚14, 15〛. The pH decrease is due to the formation of the coacervate itself (by the protonisation of the P–OH groups of the chain end). We agree with the results reported for another system 〚7, 8〛, and conclude that pH is not the important condition for coacervate obtention. On the other hand, the terminal OH groups release protons and create fresh negatively charged sites. This increases the charge density of particles, which in turn stabilizes the colloidal solution 〚7〛.
If we consider a charged particle, in a solution containing electrolytes, the distribution of the ionic species may be given by the Boltzmann law of arrangement 〚27〛. It is possible to adapt this law to poly-electrolytes 〚7, 8, 28, 29〛. For the coacervate, different forces are acting: electrostatic, Van der Waals and hydration forces. As we increase the electrolyte concentration in the sodium polyphosphate solution, the colloidal species aggregate and the hydration shells minimize their outer surface. In this situation, all cationic sites may take part in the ionic exchange. In this case, all the cationic sites may participate to the ion exchange. As the counter-ions are also present in the coacervate structure, they can intervene at the electrostatic and steric level 〚8〛. The addition of solvents with a low dielectric constant, such as alcohols, will also modify the characteristics of the reaction medium to the extent of their relative concentrations. A limited addition decreases the dielectric constant of the solution, which enhances the coacervate formation. Higher incorporation eliminates the solvation layer. As a consequence, cations – e.g., zinc – come into contact with polyphosphate chains and give a precipitate.
On the other hand, we have shown that the ratio between the respective zinc concentrations in initial solution and in coacervate is a constant that depends on the system. However, this ratio that expresses the power of exchange of the cation depends on the counter ion, that is the associated anion. For Cl–, the coacervate is richer in zinc than the initial solutions – slope is 1.3 in Fig. 2 – as opposed to the NO3– slope of 1 (Fig. 6). When sulphate is the counter-ion (in alcohol at 40%), the coacervate is also richer in zinc than the initial solution during the coacervate formation, at least prior to precipitation (Fig. 8). With chloride and sulphate as counter-ions, the ratio Zn/P leads to a value of 0.6, to be compared to 0.35, which is the value for nitrate as a counter-ion. But one must keep in mind that the area of obtention of coacervate is small for nitrate (Fig. 1). The limits of this ratio does not argue for a degree of complexation of the Zn2+ cations with PO3– groups that depends of the initial Zn/P ratio.
At last an important result comes from the water exhaust study. With CRTA technique, we have shown that there is only one kind of water in the coacervate, and not hydrates. This result is important for industrial applications. It also suggests that the DSC curves of coacervate based on zinc salts showing several steps for the dehydration 〚14〛 are artefacts as this was shown for other coacervates 〚9〛.
5 From coacervates to glasses
The thermal processing of the coacervates described previously gives glasses belonging to the P2O5–Na2O–ZnO system. Fig. 9 gives the main thermal characteristics of the different glasses obtained by the coacervate route using zinc chloride as a starting material. These results meet the initial goal of this study, which was to control the glasses properties ‘a priori’ through coacervate formulation. As one may predict glass properties after thermal curing, it is also possible to define the coacervate formulation that will comply with the specifications of the sealing or joining materials required in industrial processing. Our results also outline the importance of the sodium content to control the CTE value. They are consistent with previous results in another system 〚1, 2〛, which supports Balta’s theory about the role of the O=–Na+ dipoles 〚30〛. In addition, the coacervate route exhibits other attractive features. The rheologic behaviour of these glass precursors make possible to use simple deposition techniques such as dipping, brushing and spraying 〚8, 10〛. A typical example concerns the zinc-based system, which has low characteristic temperatures and is able to coat the current soda-lime glass. Zinc coacervate has a good wettability power and leads to a well adhesive and thin coating after curing at 400 °C. This is exemplified by Fig. 10, which shows the SEM picture of the interface between soda lime glass and phosphate glass. Microanalysis (Fig. 11) indicates that the diffusion layer is smaller than 3 μm.

Evolution of the thermal properties of glasses obtained by the coacervate method in the system sodium polyphosphate–zinc chloride.
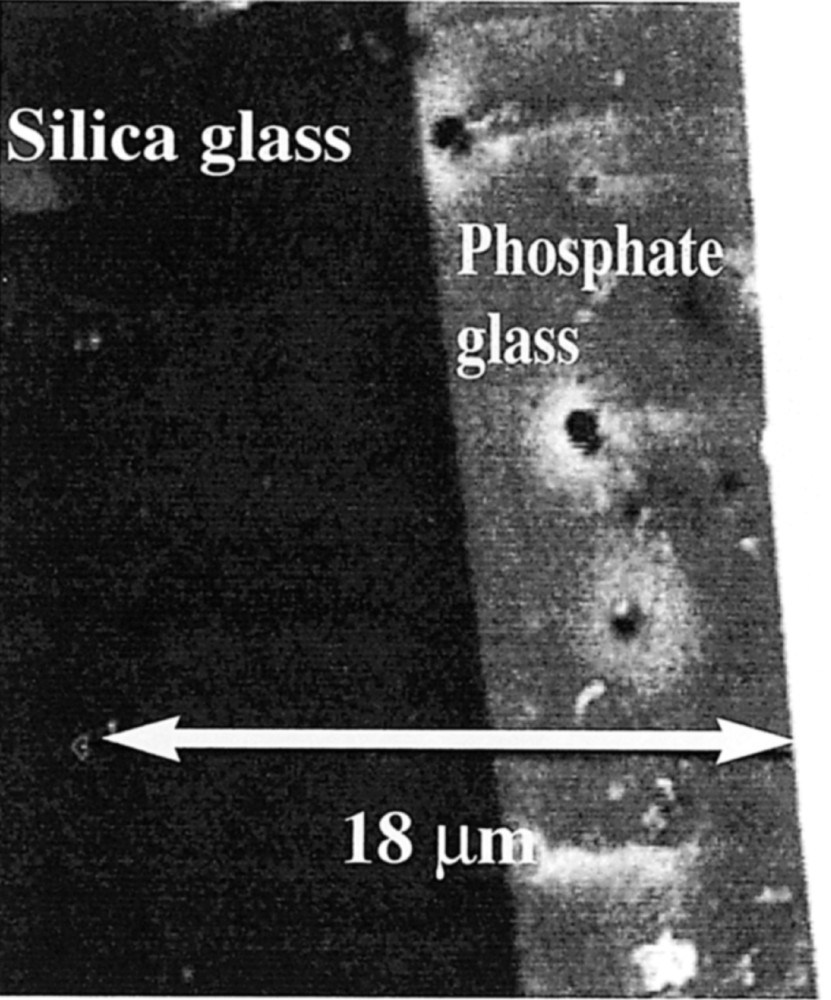
Interface between glasses in the silica system (left) and in the phosphate system (right).

Microanalysis of the interface between glasses in the silica system (left) and in the phosphate system (right). The diffusion layer is less than 3 μm.
Another advantage of the coacervate route is the possibility to combine different coacervates. For example, we have prepared silver coacervate by mixing sodium polyphosphate and silver nitrate 〚31〛 according to the approach used for zinc coacervates. A mixed zinc and silver coacervate has been prepared using zinc nitrate (and not zinc chloride!) as a starting material. The glass that is obtained by thermal curing exhibits lower characteristic temperatures, especially melting temperature, which is decreased by more than 100 °C.
This ‘soft chemistry’ route opens other possibilities. Fillers can be incorporated with a very good dispersion during the coacervation step 〚10〛. Thus it is possible to prepare coacervates with fillers that will be decomposed before the melting temperature of the glass matrix. As an example, a mixed zinc and silver coacervate, with an adapted pH and silver sulphide as filler, can be heated in reducing atmosphere, which results in the formation of silver aggregates. This is exemplified in Fig. 12. The silver clusters may join if the percolation threshold is reached and this makes the basis for a new brazing process at low temperature. Preliminary experiments aiming at joining galvanised steel are promising.
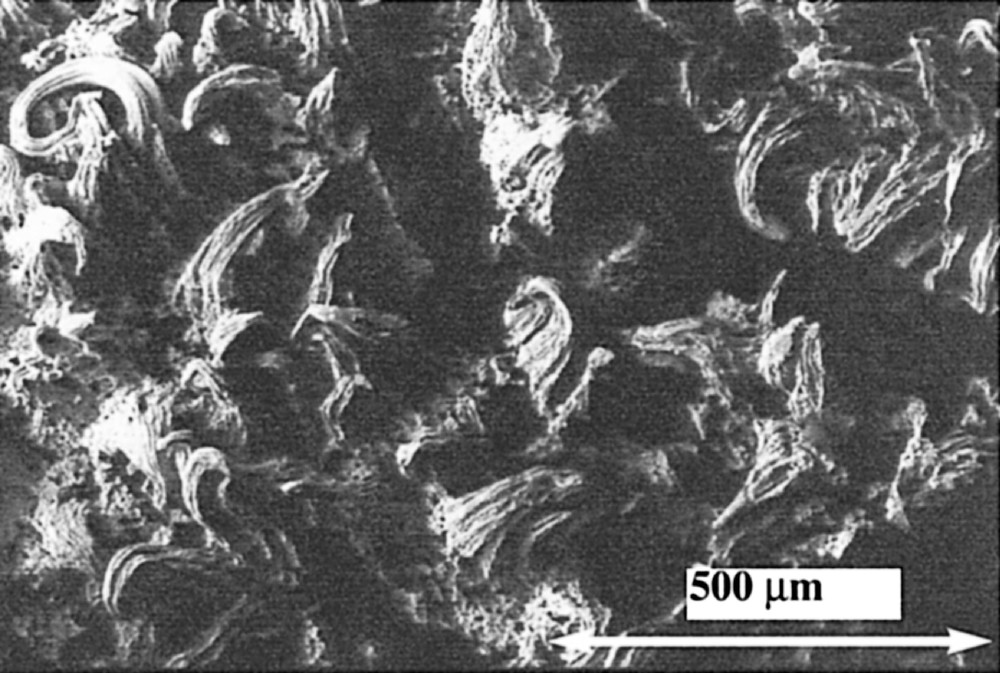
Formation of silver filaments by curing coacervates obtained by mixture of sodium polyphosphate–zinc nitrate–silver nitrate with silver sulfide as filler.
6 Conclusion
Zinc polyphosphate glasses exhibit a potential interest for industrial applications, especially for coating and joining. They may be used alone or associated to another cation such as silver. The coacervate route makes a flexible and versatile way to their synthesis. Coacervate formation can be controlled through different processing parameters: the respective concentrations of sodium polyphosphate and zinc salt, the anion associated to zinc, and the initial pH. Glass composition, and consequently glass properties, can be adjusted using this approach.