1 Introduction
In order to obtain polymers containing phosphorus in the main chain, international level researches are playing, at the present moment, a very important role. These are following the extending synthesis and characterization of polymers containing phosphorus area taking into account the manifold applications such as well known flame retardants properties [1,2] to new applications in biologic domain [3,4].
In responding to the need of developing polymers that contain phosphorus in the main chain as biodegradable and flame retardant materials, systematic studies on these polymers must be performed. Among the main routes of obtaining phosphorus-containing polymers, interfacial polycondensation has been frequently used in the synthesis of these polymers, due to its simplicity, low reaction temperatures and the linearity of the resulting polymers [5–7].
In recent years, the concept of green chemistry has attracted considerable attention [8]. The aim of green chemistry is to explore chemistry techniques and methodologies that reduce or eliminate the use or generation of feedstock, products, by-products, solvents, reagents, etc., that are hazardous to human health or the environment [9].
Solvent-free organic reactions are an important part of green chemistry and make it possible to reduce the consumption of environmentally unfriendly solvents and utilize scaled down reaction vessels. Avoiding a solvent reduces the number of components in a reaction, stops any solvent emission problems, and gets around any solvent recycling requirements.
It is known that the best solvent is no solvent but if a solvent is needed then water has a lot to recommend it and catalysis in aqueous biphasic systems is an industrially attractive methodology, which has found broad application [10]. Moreover, the use of a catalyst for solvent-free reactions can achieve energy savings. While homogeneous catalysts offer many advantages, including high activity, they generally present problems at the separation stage of a process, both in terms of product purification and catalyst recovery. Biphasic systems present one way to deal with these problems and this article is a nice illustration of this approach. Due to the specific features of interfacial polycondensation and its advantages it should be considered as a most efficient and generally green technology [11].
Therefore, we developed an efficient solvent and catalyst-free synthesis method for the synthesis of phosphorus-containing polymers by the gas–liquid technique [12–14].
The advantages of the green chemical method, in simplicity, absence of organic solvent and catalyst, have made us try to use this method in getting new polymers containing phosphorus in the main chain by a solvent and catalyst-free gas–liquid interfacial polycondensation of phenylphosphonic dichloride (PPD) and 4,4’-(1,3-phenylenediisopropylidene)bisphenol (bisphenol M).
Highly polar conventional solvents, which have been used in interfacial polycondensation, such as N,N’-dimethylformamide, N,N’-dimethylacetamide, pyridine, N-methylpyrrolidone and chlorinated solvents are volatile, most of them flammable, toxic, quite hazardous and harmful. Hence, there is a great demand for the advancement of new methodologies for polycondensation using environmentally friendly media, which could replace the traditional solvents and give adequate solubility to polymerization. In this article, we present also a new method for the synthesis of phosphorus-containing polymers, respectively interfacial polycondensation in solid–liquid system, when potassium phosphate is used as base and 2-methyltetrahydrofuran (2-MeTHF) as a green solvent. 2-MeTHF is derived from renewable resources such as corncobs and bagasse. It is an alternative to dichloromethane or to tetrahydrofuran for biphasic reactions having next advantages: low heat of vaporization; saves energy during distillation and recovery; lower peroxide formation than THF [15].
This method is used for a rigorous correlation of reaction parameters for avoiding the unwanted secondary reactions, which can reduce the polymer quality.
2 Experimental
2.1 Materials
Reagents: phenylphosphonic dichloride (PPD), 4,4’-(1,3-phenylenediisopropylidene)bisphenol (bisphenol M), NaOH, K3PO4 from Aldrich were used as received and solvent 2-methyltetrahydrofuran (2-MeTHF – from Aldrich) was used without purification.
2.2 Instruments
The IR spectra were recorded on a JASCO–FT/IR-4200 spectrophotometer and 1H-NMR and 31P-NMR spectra on a Bruker DRX 400 MHz spectrometer. All NMR spectra were recorded in CDCl3 using TMS as internal standard, at 25 °C. The polymer was characterized by viscosity, on an Ubbelohde suspended level viscometer, at 30 °C. Molecular weights were determined by gel permeation chromatography, using an Evaporative Light Scattering Detector, PL-EMD 950 (2x PL gel MIXEDC 300 x 7.5 mm columns; T = 35 °C; DMF as solvent; flow 1 ml/min; calibration with KIT polystyrene as standard). The thermoanalytical curves TG, DTG and DTA (as heat flow) were drawn up by a TGA/SDTA 851-LF 1100-Mettler Toledo device, in dynamic air atmosphere and heating rates of 10 °C/min. The glass-transition temperature (Tg) was measured with DSC 823e Mettler Toledo apparatus. Limiting oxygen index (LOI) was determinate by Limiting Oxygen Index Chamber 340AJH0038.
2.3 Procedure
Method I: synthesis of polyphosphonate P1 by interfacial polycondensation in gas–liquid system, without an organic solvent and a catalyst.
Gas–liquid polycondensation utilizes pairs of highly reactive components with one of them in the gaseous state and the other one in the solution. A typical gas–liquid polycondensation procedure was presented in a previously paper [12]. Since phosphonic dichlorides are more volatile than diols, they are preferentially employed in the gas phase. 15.3 ml phenylphosphonic dichloride (0.108 mol) was heated (80–90 °C) and by a stream of nitrogen was carried out into a flask, which contains 220 ml aqueous 1 mol sodium hydroxide solution and 13.8 g (0.040 mol) bisphenol M. The solvent for diols is water since it readily dissolves the phenolate formed. The nitrogen stream acts as carrier gas for the phosphonic dichloride, and for agitation of the reaction mixture. The reaction rate can be controlled by the nitrogen flow rate. In order to prevent the possibility of condensation of the vapors on apparatus walls, the vapor mixture is overheated or is diluted so that the partial pressure of the vapor reagent in the gas mixture is lower than its saturated vapor pressure. The carrier gas flow, which produced bubbles in the formed product that expanded and burst at the top of the reaction flask, was continued 15 min after the entire quantity of phosphonic dichloride, is trained. The polymer separates after 30 min from solution as tacky, coherent mass, adhering to the container surface. The solid polymer was washed with distilled water until free of chloride ion and dried at 50 °C, in vacuum. The obtained polymer shows wide ranges of consistency and softening.
P1: IR (KBr, cm-1): 1237 (P=O), 1145;960 (P-O-Carom), 1490 (P-Carom), 3028;1606;1380 (Ph); 1H-NMR (400 MHz, CDCl3, TMS) 7.2-8.5(m,C6H5);1.8 (s, isopropylidene); 31P-NMR (400 MHz, CDCl3, TMS): 15.2 (P at chain end), 12.3 (P in the repeat unit).
Method II: synthesis of polyphosphonate P2 by PTC polycondensation in solid–liquid system, without a catalyst and using a green solvent.
In a flask fitted with stirrer, 1.73 g (0.005 mol) of bisphenol M, 2.1 g (0.012 mol) of K3PO4, and 20 ml of 2-MeTHF were introduced. A solution of 0.71 ml (0.005 mol) PPD in 10 ml 2-MeTHF was added at once under stirring. During the addition, an exothermic reaction occurred. The mixture was still stirred for 2 h at 40–45 °C. Following polycondensation, polymer (P2) was purified by precipitation into excess hexane (200 ml) and isolated as a white solid, which is dried under vacuum, at 50 °C, redissolved in chloroform (20% solid), reprecipitated into hexane (200 ml) again, dried under the same conditions and characterized.
P2: IR (KBr, cm-1): 1244 (P = O), 1140; 954 (P-O-Carom), 1500 (P-Carom), 3028;1606;1380 (Ph); 1H-NMR (400 MHz, CDCl3, TMS) 7.3-8.2(m,C6H5); 1.7 (s, isopropylidene);31P-NMR (400 MHz, CDCl3, TMS): 15.2 (P at chain end), 12.0 (P in the repeat unit).
3 Results and discussion
The advantages of green chemical methods in respect of simplicity, absence of organic solvent and catalyst have made us try to use this method in getting new polymer materials, too.
A new polyphosphonate was synthesized from PPD and bisphenol M by an eco-friendly procedure in a solventless and catalyst-free gas–liquid and in a solid–liquid interfacial polycondensation (Reaction (1)).
In the first variant the volatile reagent (phenylphosphonic dichloride) is used in the vapor phase and the second reagent (bisphenol M) is present in aqueous phase. The carrier for phenylphosphonic dichloride is an inert gas such as N2 and also allowed the reagents to be mixed. As it can be seen the difference between gas–liquid system and liquid–liquid system consists only in the presence of water beside the reagents. So, this method permits the use of readily hydrolyzing monomers (phenylphosphonic dichloride). Also, the reaction time is short (30 min) Solvent and catalyst are not required in the first variant and for this reason gas–liquid interfacial polycondensation can be considered to be green. The possible environmental benefits are obvious with no concerns over solvent emissions.
Only ionic impurities (i.e., NaCl) need to be washed from the polymer. After completion of the reaction, the obtained polymer separates from aqueous phase without complicated purification and washed. The polymer obtained in this way contains strongly adsorbed water, which should be removed prior to further polymer characterization or processing. This can be achieved by drying under vacuum (yield 88%).
Also, another aim of this work was to apply the solid–liquid system, as an eco-friendly procedure for a new phosphorus-containing polymer when potassium phosphate is used as a high performance base.
The potassium phosphate [16] acts as acid scavenger without water formation (HCl + K3PO4 = KCl + K2HPO4).
This method requires no product purification and affords the desired compound in a reasonable yield without the formation of any by-products. The polymer was prepared without catalysts and toxic solvents. 2-methyltetrahydrofuran is a green alternative to dichloromethane for biphasic reactions [15] and was used as solvent in this synthesis. The reaction proceeded very easily without catalyst in 2-MeTHF at 45–50 °C for 2 h to give polyphosphonate P2 with 90% yield and 3.2 dl/g inherent viscosity.
The conversion of liquid–liquid into solid–liquid proves to be advantageous from the point of view of suppression of side reactions, such as hydrolysis of the P-chloride reagent or of the chain end-groups of the polymer. Polymer with higher molecular weights has been prepared compared with that obtained by the gas–liquid method.
Table 1 shows the yield, inherent viscosities, molecular weights and phosphorus content for polyphosphonate P1 obtained by gas–liquid interfacial polycondensation and as a comparison for polymer P2 obtained by solid–liquid interfacial polycondensation.
Results of gas–liquid interfacial polycondensation (P1) and solid–liquid interfacial polycondensation (P2) of PPD with bisphenol M.
Polym. | Yield (%) | ηinhb (dl/g) | %Pexpc | Mne | Mwf | Polydisp. Mw/Mn | Tg (°C) | LOI |
P1a | 88 | 2.2 | 5.8 | 57 600 | 128 500 | 2.23 | 98 | 40 |
P2d | 90 | 3.2 | 6.2 | 114 400 | 245 600 | 2.15 | 98 | 40 |
a Reaction conditions [12]: 0.108 mol PPD, 0.040 mol bisphenol M, 0.220 mol NaOH 1 mol, 30 min, reaction temperature 50 °C.
b The inherent viscosities were determined for solutions of 0.5 g/100 ml in tetrachloroethane, at 30 °C.
c Determined by Schöniger method.
d Reaction conditions: 0.005 mol bisphenol M, 0.01 mol K3PO4 in 20 ml 2-MeTHF, 0.005 mol PPD in 10 ml 2-MeTHF, 2 h, 600 rpm, 45 °C.
e Mn: Number Average Molecular Weight. It represents the total weight of all the polymer molecules in a sample, divided by the total number of polymer molecules in a sample.
f Mw: Weight Average Molecular Weight. It is done as follows: weigh a number of polymer molecules, add the squares of these weights, and then divide by the total weight of the molecules.
The structure of the polymers was confirmed by IR, 1H-NMR and 31P-NMR spectroscopy. Representative 31P-NMR spectra for the polymer P1 and P2 are shown in Figs. 1 and 2.
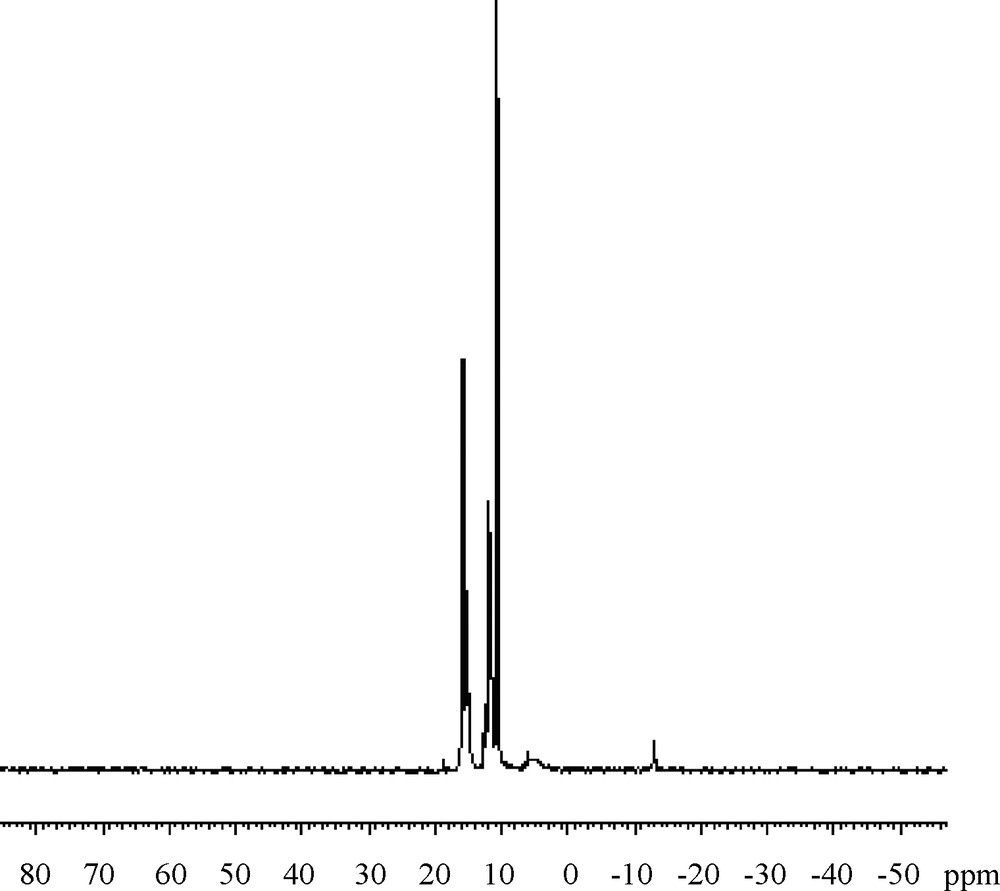
31P-NMR for P1.
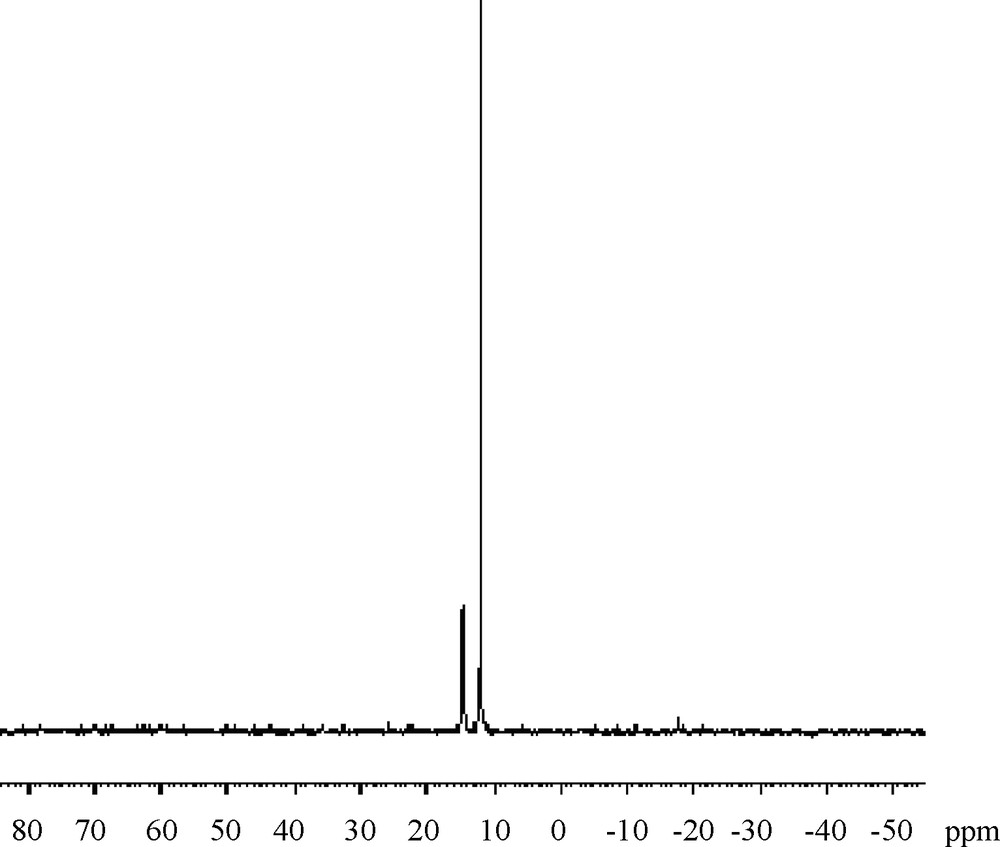
31P-NMR for P2.
Polymeric structure was supported by the P-O-Caromatic stretching vibration. The absence of the phosphonate (P–OH) stretching at 2800–2600 cm−1 indicates that the polymer is indeed a polyphosphonate. Aromatic protons are presented as multiplet in the region 7.2–8.5 ppm for P1 and 7.3–8.2 ppm for P2. The protons of isopropylidene groups appeared at 1.8 ppm in P1 and at 1.7 ppm for P2. The presence of phosphorus is confirmed by elemental analysis and by 31P-NMR analysis. The %P (5.8% for P1 and 6.2% for P2) content of this polymer is in agreement with the calculated value. The 31P-NMR spectrum of P1 also confirms the successful incorporation of phosphonate group in the main chain of the polymer. There are two P-resonances for P1, one at 15.2 ppm, which is assigned to the P end-groups and one at 12.3 ppm, which is assigned to the repeating P atoms within the backbone. For P2 these values are 15.2 and 12.0.
The Tg values for the obtained polyphosphonates are also listed in Table 1. The polyphosphonates are, as expected from literature data, amorphous materials, which do not crystallize despite prolonged annealing (24 h) above their glass-transition temperature (Tg). When linear bisphenols (bisphenol M) are used the ordering capacity is favored. The ordering capacity is influenced by the flexibility of the chain. The low Tg found fit well the hypothesis of relatively flexible main chains. As expected, the flexible phosphonate groups enhance the segmental mobility of the polyphosphonate chains, and thus, reduce Tg.
The polyphosphate did not show significant weight loss below 300 °C. They began to decompose in the range of 315–390 °C; they showed 10% weight loss in the range of 345–400 °C. The char residue of P1 at 600 °C is 27%. The low char residue is due to the methylene groups. Char formation is important to flame retardancy because the carbonaceous char formed during degradation on top of a polymer can protect the underling polymer from exposing to the flame [17]. Limiting oxygen index (LOI) measurements indicated their potential application as fire retardant materials. LOI was determined on the powdered sample in according to modified ASTM D2863-70 and was 40 [18].
4 Conclusion
This article has applied a modern synthetic methodology, interfacial polycondensation, to produce a more efficient and cleaner preparation of polymers containing phosphorus in the main chain. New polyphosphonate structures were successfully prepared by two simple and green methods by a solvent and catalyst-free gas–liquid and a solid–liquid interfacial polycondensation without catalyst.
Gas–liquid polycondensation differs from the liquid–liquid system. In a gas–liquid system only water is usually present beside the reagents. This method permits the use of readily hydrolyzing monomers (phosphonic dichlorides). The polymer separates from aqueous phase and does not need complicated purification.
The solid–liquid method proves to be advantageous from the point of view of suppression of possible side reactions, e.g. hydrolysis of the P-chloride reagent or of the chain end-groups of the polymer. The combination of catalyst-free conditions and the use of a green solvent lead to reductions in reaction times, enhancements in yields. Higher molecular weight polymers have been prepared compared with those obtained by the gas–liquid method.
These methodologies offer improvements for the synthesis of polymers with regard to:
- • Elimination of catalysts and organic solvents or use of green solvents;
- • Elimination of dangerous, inconvenient, and expensive reactants (the use of NaOH, KOH, K3PO4, etc. instead of NaH, NaNH2, t-BuOK, R2NLi, etc.);
- • High reactivity and selectivity of the active species;
- • High yields;
- • High molecular weights;
- • Simplicity of the procedure.