1 Introduction
The strategy for environmental protection in industry necessitates the processes for waste treatment as well as the development of new and alternative processes and products, which have no or less harmful effects on the environment.
Electrochemistry offers promising approaches in both types of strategies. The inherent advantage is its environmental compatibility, due to the fact that the main reagent, the electron, is a ‘clean reagent’. Electrochemical processes can be used for recovery or treatment of effluents from industrial plants. Industrial electrochemistry has undergone a remarkable development towards cleaner processes and environmentally friendly products. The applications of electrochemistry for the protection of the environment have already been exclusively discussed in a number of books and reviews [1–9]. Many of the concepts discussed in early publications are still of interest today but progress in material science (new electrode materials and membranes) and aspects in electrochemical engineering (new and effective cell design) have offered possible effective and appealing solutions. The developments in electrochemistry in the last two or three decades are very stimulating and hence can be expected to handle the environmental problems posed by the modern developments in process and manufacturing industries.
Sulphur dioxide (SO2) is a colourless, non-flammable gas. The most significant anthropogenic emission sources of SO2 are from combustion of sulphur-containing fossil fuels, smelting sulphide ores, and petroleum refining. Other less significant sources include chemical and allied product manufacturing, metal processing, other industrial processes, and vehicle emissions.
Based on data of 2008, annual mean SO2 concentrations in Tunisia cities range from approximately 4 ppb in Manouba and El Ghazela to as high as 50 ppb in Gabès.
The removal of sulphur dioxide or nitrogen oxides from industrial waste gas represents a large domain of investigations. Electrochemical processes, which do not require the continuous use of chemical reagents, can bring a helpful contribution in the proposal or development of depollution processes.
This present study has been planned with the aim to design, optimize and evaluate a new depollution process for sulphur dioxide removal; the idea consists in coupling the electrolysis phenomenon upstream to the sulphuric acid plant. In other words, this proposition consists in modifying the hybrid cycle Westinghouse (Fig. 1) by the elimination of the sulphuric acid decomposition stage, which corresponds to 61% of the energy distribution of this cycle.
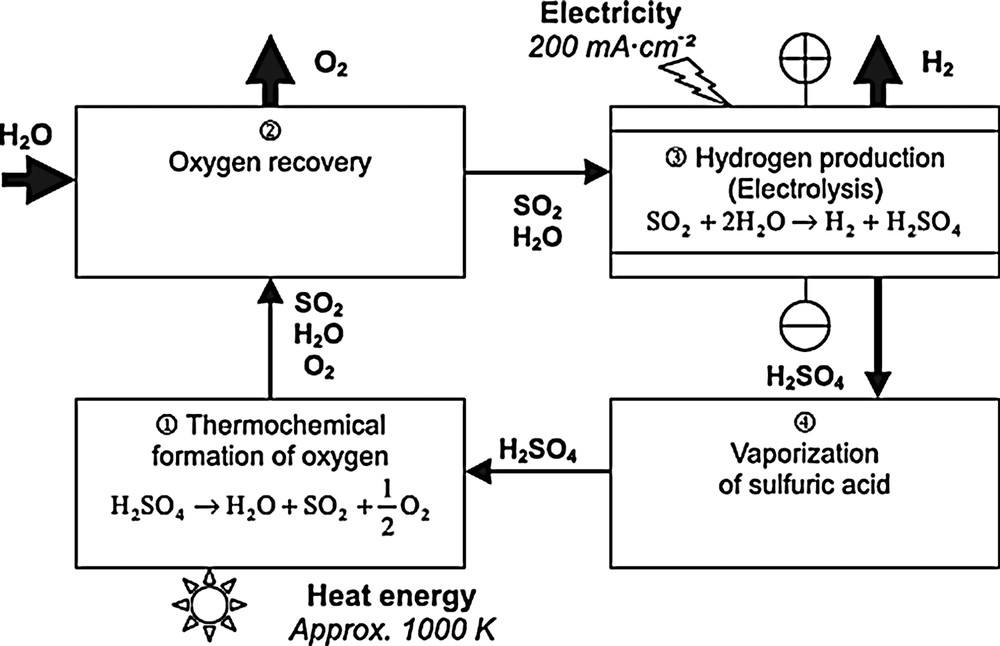
Westinghouse hybrid-sulphur cycle flowsheet schematic.
2 Sulphur dioxide removal mechanisms from flue gases
The electrochemical oxidation of sulphur dioxide has been investigated by many authors with respect to hybrid processes for hydrogen production by water-splitting at low cell voltage levels. The rate of this reaction is relatively slow and two possible ways of overcoming this problem exist. The first is the direct electrochemical oxidation of sulphur dioxide using noble metal electrocatalysts as electrode materials. This is realized by the Westinghouse Process for hydrogen production [10,11]. A second possibility is by the indirect electrochemical sulphur dioxide oxidation using suitable redox mediators. For this purpose, the bromine-bromide system is used in the Mark-13 process [12,13]. Another version using iodine-iodide as redox mediator has also been suggested [14,15]. Stimulated by the increasing importance of sulphur dioxide pollution control, many attempts have been made to develop electrochemical processes for removal of sulphur dioxide from flue gas. Thermal/electrochemical hybrid cycles such as the Mark-13 and the iodine sulphuric acid cycle can be opened in principle to sulphur dioxide consuming processes producing sulphuric acid.
Direct electrochemical oxidation using electrocatalytically active electrodes is very difficult due to catalyst poisoning by flue gas impurities.
Therefore a direct electrochemical gas purification process has been developed using an absorption packed bed column with particles working as a three-dimensional electrode [16–19].
The packed bed absorption column provides a high specific electrode area which is necessary to compensate the low microkinetic current density of sulphur dioxide oxidation. A literature survey of various proposals for electrochemical flue gas desulphurization. Both direct and indirect electrochemical processes are possible.
Some further processes have been suggested which are in principal chemical absorption processes using alkaline and acid solutions which are produced electrochemically [20–22].
3 Methodology: description of the new process
The idea is defined as follows:
- • integration of the phenomenon of electrolysis upstream of the sulphuric acid process;
- • elimination of the sulphuric acid decomposition stage in the hybrid cycle Westinghouse which corresponds to 61% of the energy distribution of the process.
3.1 Cycle hybrid-sulphur (Westinghouse)
The Westinghouse process in 1967, Juda and Moulton [10] demonstrated the advantages of using sulphur dioxide in solution to diminish the activation overpotential during water electrolysis. The “Westinghouse process” was patented by Brecher in 1975 [11].
The Westinghouse sulphur process decomposes water into hydrogen and oxygen in several steps. This process requires a high-temperature thermal source, which could ideally be a fourth-generation nuclear reactor for recycling compounds. The process consists of producing hydrogen in a specific electrolyser where protons are reduced at the cathode while an oxidation reaction, in which sulphur dioxide forms sulphuric acid, takes place in the anode compartment. This type of reaction enables mass hydrogen production at a very low cell voltage because the standard redox potential of H2SO4/SO2 is 0.17 V versus SHE, compared with 1.23 V for the common electrolysis of water by H2O/O2 oxidation.
The Westinghouse process is based on a hybrid-sulphur redox cycle involving an electrochemical reaction to produce hydrogen and a thermochemical stage to produce oxygen.
The complete cycle shown in Fig. 2 (a) comprises an electrolyser stage and three blocks corresponding to conventional chemical processes. Oxygen is produced by high-temperature thermal cracking of sulphuric acid:
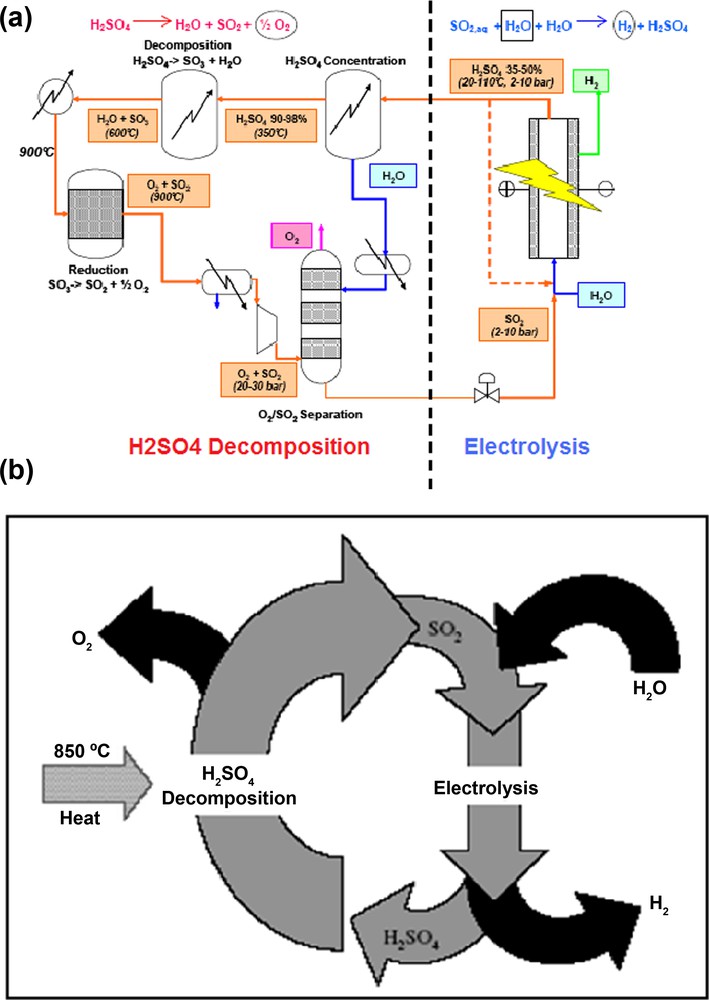
a and b: cycle hybrid-sulphur (Westinghouse).
For a sulphur dioxide pressure of 1 bar (almost all the studies were carried out at this pressure) the sulphuric acid concentration should be about 50wt% at temperatures between 25 and 90 °C [22,23] (Fig. 2 a and b).
3.2 Basic knowledge: sulphuric acid plant
For an overview of the production of H2SO4, see Fig. 3; H2SO4 is produced from SO2, which is derived from various sources, such as combustion of elemental sulphur or roasting of metal sulphides. SO2 is then converted into SO3 in a gas phase chemical equilibrium reaction, using a catalyst. Finally, sulphuric acid is obtained from the absorption of SO3 and water into H2SO4 (with a concentration of at least 98%).
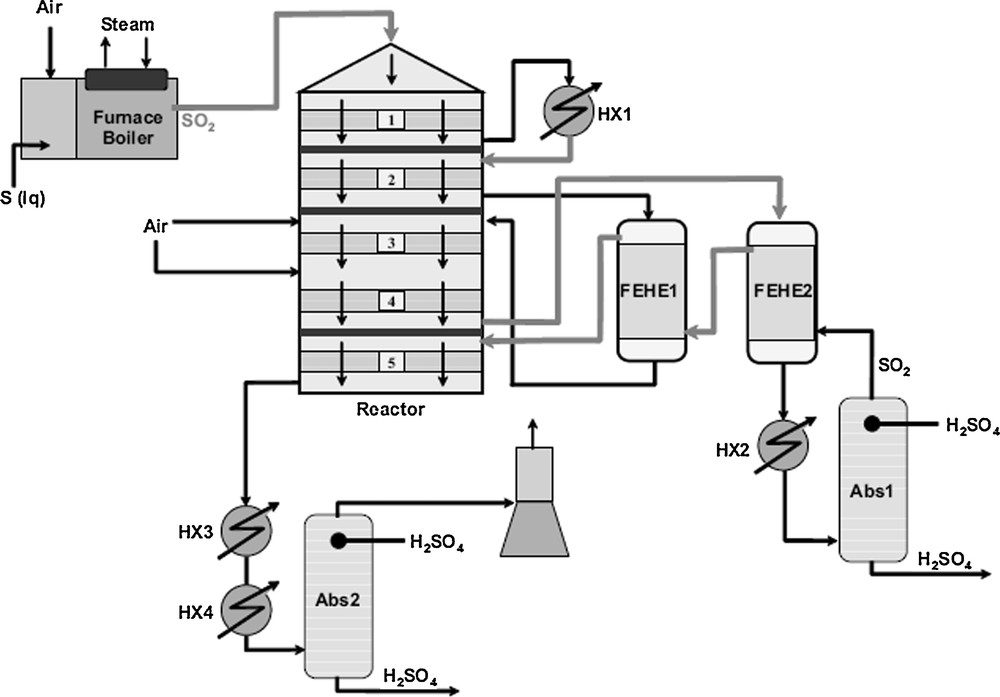
Simplified flowsheet of sulphuric acid production plant.
In the double contact process, a primary SO2 conversion of 85–95% is achieved in the first catalysis stage of the converter before entry into an intermediate absorber, depending on the arrangement of the converter beds and the contact time. After cooling of the gases to approximately 190 °C in a heat exchanger, the SO3 already formed is absorbed in 98.5–99.5% sulphuric acid. If necessary, an oleum absorber is installed upstream of the intermediate absorber. The absorption of SO3 shifts the reaction equilibrium significantly towards the formation of more SO3. This results in a considerably higher conversion rate, if the residual gas is passed through the following converter beds (usually one or two). The SO3 which is formed in the second catalysis stage is absorbed in the final absorber.
Fig. 3 gives an impression of a sulphuric acid plant. The example shows a double contact/double absorption plant based on sulphur combustion [23].
Sulphuric acid may be manufactured commercially by either the lead chamber process or the contact process. Because of economics, not all of the sulphuric acid produced in Tunisia is now produced by the contact process. Tunisia facilities produce approximately 42 million megagrams (Mg) (46.2 million tons) of H2SO4 annually. Growth in demand was about 1% per year from 1981 to 1991 and is projected to continue to increase at about 0.5% per year.
3.2.1 Sulphur dioxide emissions
Nearly all sulphur dioxide emissions from sulphuric acid plants are found in the exit stack gases.
Extensive testing has shown that the mass of these SO2 emissions is an inverse function of the sulphur conversion efficiency (SO2 oxidised to SO3). This conversion is always incomplete, and is affected by the number of stages in the catalytic converter, the amount of catalyst used, temperature and pressure, and the concentrations of the reactants (sulphur dioxide and oxygen). For example, if the inlet SO2 concentration to the converter were 9% by volume (a representative value), and the conversion temperature was 430 °C (806 °F), the conversion efficiency would be 98%. At this conversion, the uncontrolled emission factor for SO2 would be 13 kg [24].
3.3 Creative idea of the new process
Contrary to the cycle hybrid-sulphur (Westinghouse), the new cycle is not going to begin with the decomposition of the sulphuric acid but the double contact process of sulphuric acid production will be the new point of departure.
The acid produced by double absorption is going to be stored as finished product; on the other hand, the SO2 gas will continue the rest of the cycle, which is the electrolyser stage of the Westinghouse process (Fig. 4):
- • in the anode: SO2 + 2H2O → H2SO4 + 2e− + 2H+;
- • in the cathode: 2H+ + 2e− → H2;
- • the global reaction: SO2 + 2H2O → H2SO4 + H2.
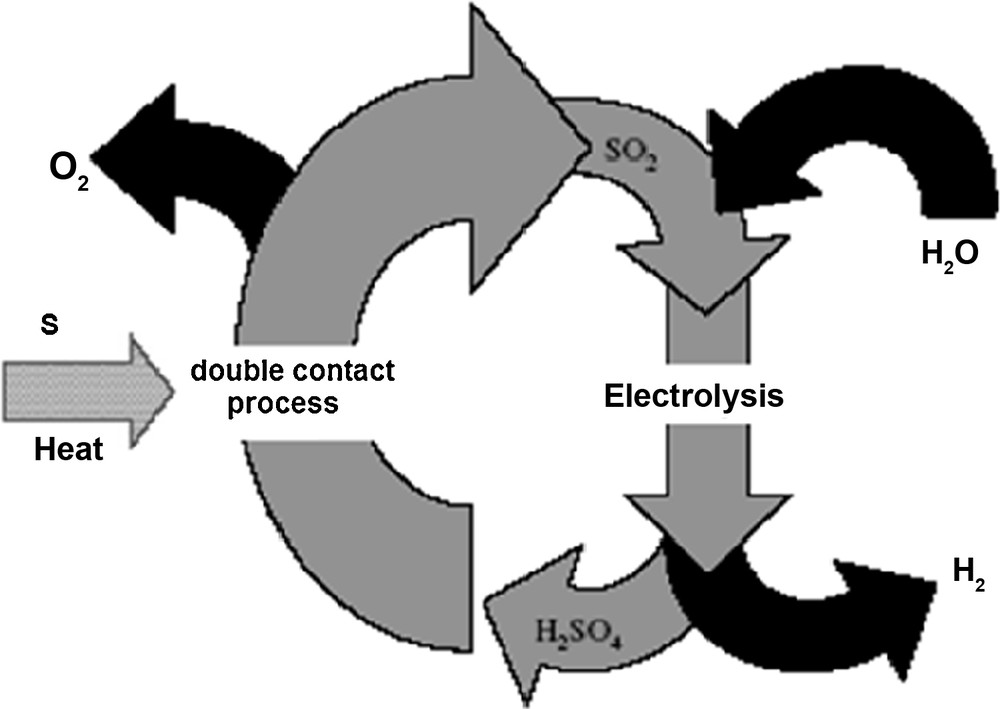
Description of the new process.
Let us note that the sulphuric acid produced by the electrolyser is going to be sent towards the stock in its turn but indeed to have undergone later a concentration.
3.4 Detailed flowsheet
Aspen Plus (Aspen Plus®, Aspen Technology, Inc. [AspenTech.]) was chosen as the process simulator for this work. Aspen Plus® is employed for chemical process simulation and for developing process flow sheet.
3.4.1 Advantages of this new process
The new process is shown schematically in Fig. 5. The first step is the sulphuric acid production and the sulphur dioxide emission. The second step is electrolysis of water with sulphur dioxide. Water is decomposed into hydrogen and oxygen by electrode potential in an electrolysis cell which makes sulphuric acid from sulphur dioxide and water at the anode, while simultaneously generating hydrogen at the cathode. The presence of sulphur dioxide along with water in the electrolyser reduces well the required electrode potential below the one required for pure–water electrolysis. This in turn reduces the total energy required at the electrolyser. The theoretical voltage to decompose pure water is 1.23 V, with many conventional electrolysers needing 2.0 V or higher [10]. The theoretical potential required for electrolysis with sulphur dioxide is 0.17 V at unit activity for reactants and products. This is less than 15% of the voltage needed in commercial water electrolyser. The sulphuric acid made in the electrolyser is sent to the concentrator. One important task in the framework of this project is the elimination of sulphuric acid (H2SO4) decomposition which is highly heat consuming and technically challenging, also, the presence of sulphur dioxide along with water in the electrolyser reduces well the required electrode potential below the potential required for pure–water electrolysis, thus reducing the total energy consumed by the electrolyser.

Schematic of the new process.
Fig. 6 depicts the details of the developed flow sheet. There are three major sub-systems in the process: separator, electrolyser and concentrator.
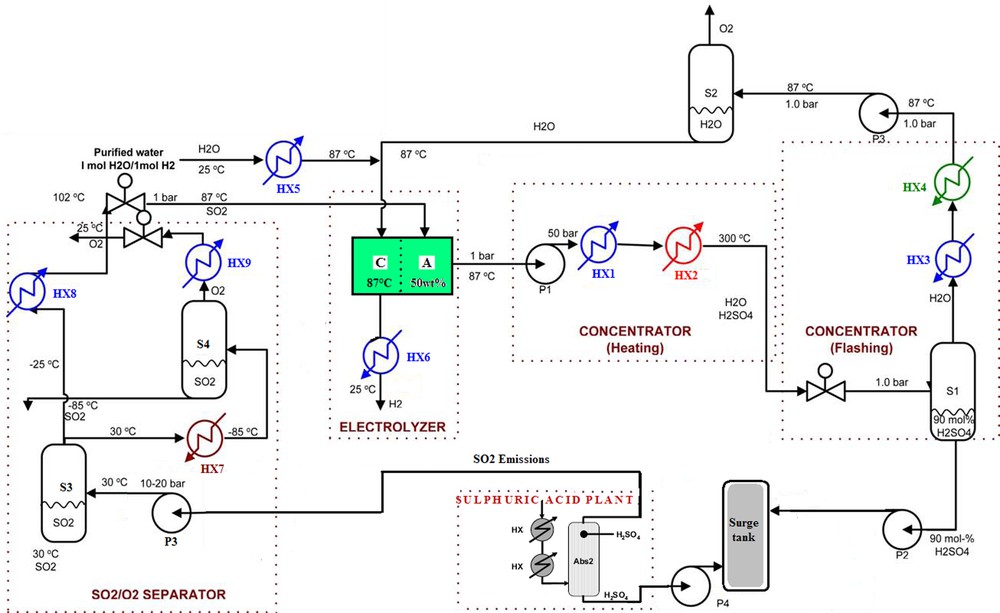
Detail flowsheet for the new process.
Water is decomposed into hydrogen and oxygen by electrode potential in an electrolysis cell which makes sulphuric acid from sulphur dioxide and water at the anode while simultaneously generating hydrogen at the cathode. The sulphuric acid made in the electrolyser is sent to the concentrator.
In the concentrator, the diluted sulphuric acid (50 w–%) is pressurized, heated and flashed to 1 bar. To achieve high temperature in the concentrator, the acid is pressurized up to a desired high pressure.
At the inlet of the concentrator, the concentrated sulphuric acid is pumped up to the storage.
At the inlet of the separator, the SO2 and O2 mixture is compressed up to the desired high pressure for efficient separation.
3.4.2 Description of the concentrator
Fig. 7 depicts the detailed flow sheet of the concentrator. The role of the concentrator is removing water form sulphuric acid by heating and flashing before the storage.
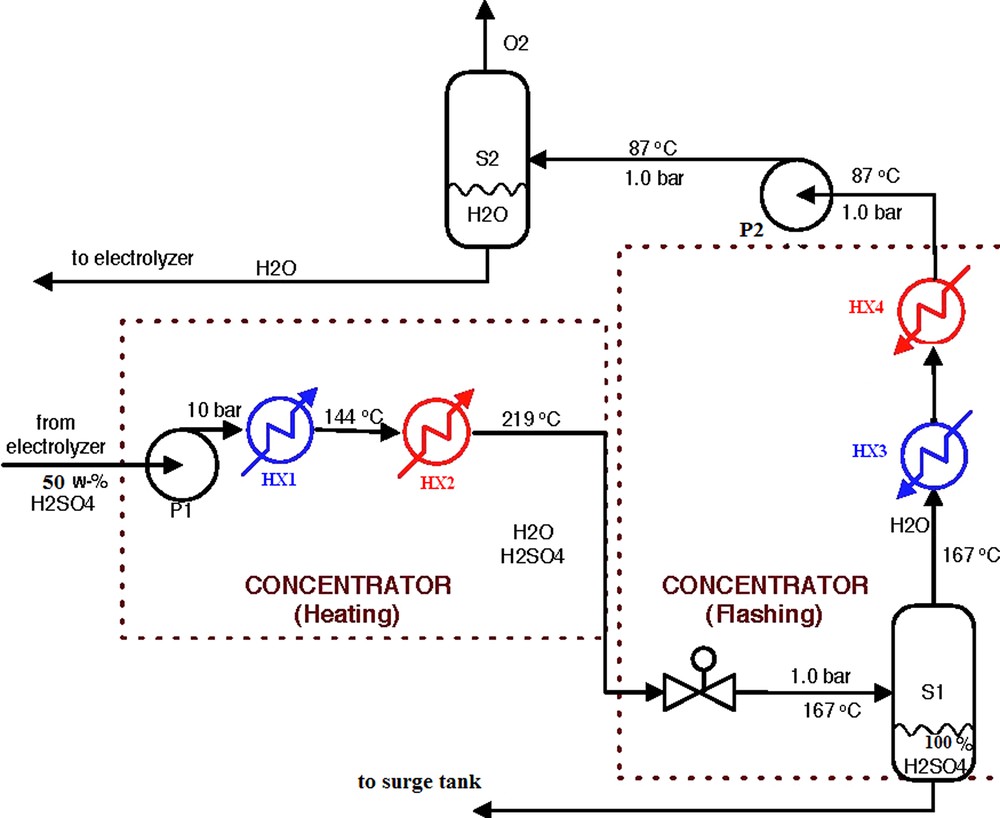
Flowsheet for the concentrator.
The boiling point of water is lower than that of H2SO4. Therefore, to separate water from the sulphuric acid, the sulphuric acid is heated until a sufficient amount of water is vaporized. It is important to indicate that this separation is not a total separation.
The temperature at which a certain amount of water vapor is generated depends on pressure.
Higher pressure needs higher temperature, and lower pressure needs lower temperature for vaporizing the same amount of water. Therefore, more thermal energy is demanded for higher operating pressure in the concentrator.
Instead of heating and separating under the same pressure, if we depressurized the heated sulphuric acid down to a very low pressure, we can get more water vapor and can effectively separate water from sulphuric acid (isentropic flash). Because of the nature of an isentropic flash, the same amount of heat is needed regardless of the heating pressure. Although we need higher temperature for higher heating pressure, the same amount of thermal energy is required for operation at all pressures. The heating temperature is lower than that of heating and separating under the same pressure case. The highest pressure would be best for the concentrator. Obviously, a pressure limitation exists due to the cost of materials that can withstand harsh conditions, such as high temperature, high pressure, and high acidity. The thermal energy demand for separating water from sulphuric acid is proportional to the fraction of water at the inlet of the concentrator. The amount of heat required is proportional to the electrolyser acid concentration.
3.4.3 Work of separation based on flowsheet
Fig. 8 shows a detailed flow sheet for the SO2/O2 separator. There are two separation tanks, S3 and S4. The pressurized SO2/O2 mixture is sent to a heat exchanger (HX10) and cooled down by cooling water (∼30 °C). A large fraction of SO2 can be condensed and removed from the gas mixture stream at the separation tank 3 (S3). For example, under 50 bar, 99% of SO2 is liquefied by the cooling water and just 1% of SO2 is sent to a chiller (HX7) for further separation of SO2 from O2. Therefore, the major separation takes place in separation tank 3 (S3, 30 °C), and further separation or purification takes place in the chiller and separation tank 4 (S4, −85 °C). By these two steps of separation, we can recover 99.9% of SO2 from the mixture. If we allow 1% of SO2 to remain in the O2 stream, the separation tank S4 can be operated at a somewhat higher temperature of −40 °C. And, if we need more pure O2 stream, a lower chiller temperature should be introduced.
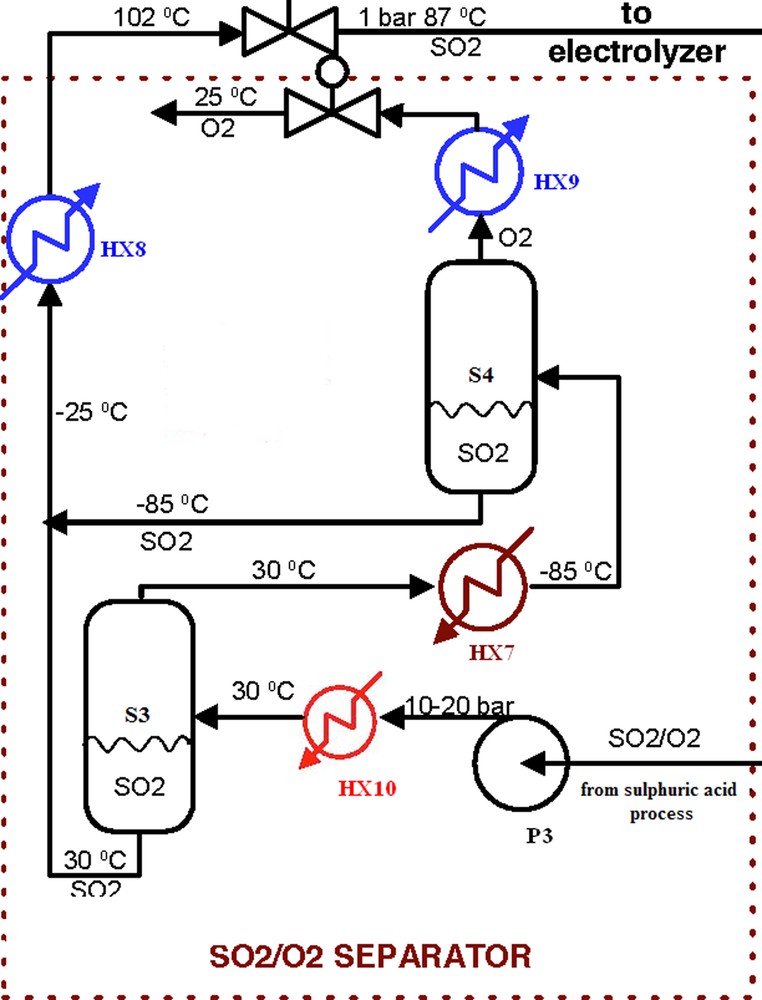
Flowsheet for the separator.
This two steps separation permits to obtain a very pure oxygen at the inlet as the by-product. SO2/O2 separation sub-system was optimized to maximize O2 production in gas phase and SO2production in liquid phase. The maximization of SO2 has impact to the hydrogen production.
3.5 Description of the electrolyser
The role of the electrolyser is to produce hydrogen at the cathode and sulphuric acid at the anode. Hydrogen is produced by electrolysis. Sulphur dioxide SO2 and water H2O are reacted electrolytically to produce hydrogen H2 and sulphuric acid H2SO4.
Fig. 9 shows a detailed flow sheet for the electrolyser. From the Nernst equation, the cell potential is calculated as follows:

Flowsheet for the electrolyser.
As shown, the cell potential is a function of the temperature, concentrations (liquids) and partial pressures (gases).
In this process, platinum, glassy carbon, stainless steel, brass, and aluminum could be used as electrodes, due to the familiar corrosion-resistant properties of those materials. Unfortunately, stainless steel releases toxic materials as it decays, brass deposits copper onto the cathode (which accelerates rusting of steel), and aluminum quickly deteriorates.
However, there is a conductive material that can be successfully utilized as an almost non-sacrificial electrode in electrolysis step: graphite. Graphite is an electrically conductive form of solid carbon.
For the design of electrolyser, the better performances could be achieved with PEM (Proton Exchange Membrane electrolyser) that have a higher active surface and a lower ohmic drop.
4 Results
Among the whole project theoretical work is presented in this article. In fact, development of a new cleaner process for hydrogen mass production is described here.
4.1 Data sources and calculation procedures
The thermodynamic equilibrium limits the conversion of SO2 to SO3 in the sulphuric acid plant and, hence, impacts on the residual SO2 emission level.
This equilibrium very much depends on the oxygen and sulphur dioxide content of the inlet gas, and also the O2/SO2 ratio. Although, with modern sulphur burning plants operate with a feed gas of 11.8% v/v SO2 and a residual 8.9% v/v O2, resulting in an O2/SO2 ratio of 0.75. This enables the plant to match emission levels below 2–4 kg SO2 per tonne of H2SO4 produced.
To confirm the conversion efficiency of this process, the case of sulphuric acid plant, which used a double contact/double absorption process, was taken, this plant is located in the industrial complex of Gabès in south Tunisia. The data, used in the mass balance, are shown in Table 1.
Characteristics of the sulphuric acid plant.
Parameter | Value | Unit |
H2SO4 (100%) production | 1500 | t d−1 |
Return on both columns of absorption | 100 | % |
Loss in SO2 occurs only at the level of the catalytic converter | 0.4 | % |
SO2 molar fraction at the exit (release) of the oven of combustion | 10.85 | % |
Temperature of SO2 supply of the electrolyser | 70 | °C |
Temperature of water supply of the electrolyser | 187 | °C |
Rate conversion in the electrolyser | 50 | % |
4.2 Evaluation methodology: mass balance study
To confirm the importance of this process, a mass balance study was carried out to determine:
- • the quantity of sulphur dioxide treated;
- • the quantity of sulphuric acid recovered;
- • the concentration of sulphuric acid produced;
- • the quantity of hydrogen produced.
4.2.1 Mass balance of the combustion section
To determine the quantities of sulphuric acid recovered, sulphur dioxide and hydrogen treated product, we need all the product of molar flow rates leaving the contact process.
We represent the process by a Block diagram which is represented in Fig. 10.
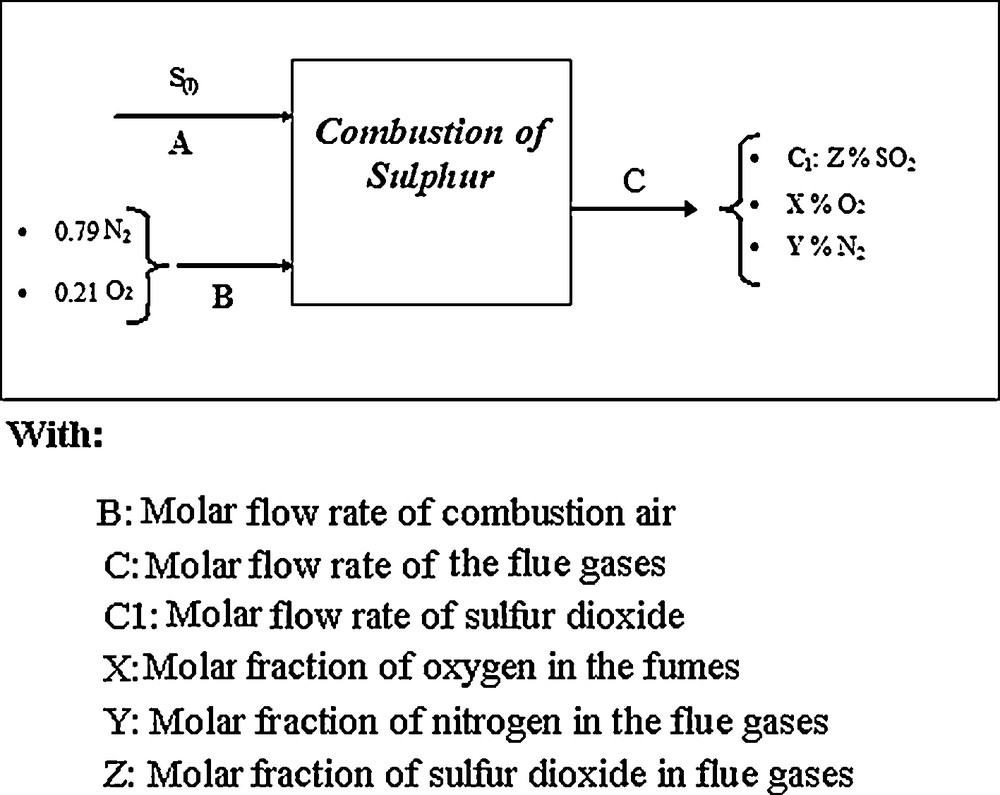
Block diagram of the combustion section.
Note that we already know that the SO2 molar fraction at the exit (release) of the oven of combustion is 10.85%.
- • The partial assessment of the sulphur is given by Eq. (1):
(1) |
- • The partial assessment of oxygen is given by Eq. (2):
(2) |
- • The partial assessment of nitrogen is calculated using Eq. (3):
(3) |
The overall mass balance is written in Eq. (4):
(4) |
- • Determination of the percentage composition of flue gas.
We want to estimate the mole fractions of each compound, for that we proceed as follows:
From Eq. (2) we have the expression of B:
Since X + Y − Z = 100, the expression of B becomes as in Eq. (5):
(5) |
On the other hand Eq. (8) gives another expression of B as in Eq. (6):
(6) |
Equality between the two Eqs. (5) and (6) gives:
And (8) gives:
Knowing that:
Solving this equation gives: Z = 5.17.
Then: X = 21 − Z.
Numerical application:
- • Determination of molar flow rates.
Knowing that the sulphuric acid production is 1500 t d−1, and remembering the assumptions mentioned above, we can say that the molar flow rate of liquid sulphur is equal the molar flow rate of sulphuric acid increased loss of SO2 is:
So:
We obtain:
Because:
The two Eqs. (2) + (3) will give:
Numerical application:
A: molar flow rate of liquid sulphur = 15367.592 kmol d−1;
B: molar flow rate of combustion air = 297245.493 kmol d−1;
C: molar flow rate smoke = 297245.493 kmol d−1;
C1: molar flow rate of SO2 = 15367,592 kmol d−1.
4.2.2 Mass balance on the conversion section
We represent this converter in Fig. 11. The conversion is done with a conversion rate equal to 99.6% by the following reaction.
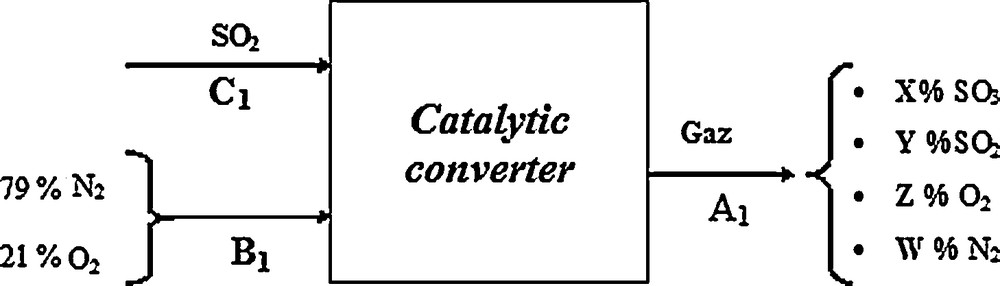
Block diagram of the conversion section.
However, loss of SO2 which occurs at the catalytic converter is equal to 0.4%; we can therefore determine the molar flow rate of sulphur dioxide leaving the catalytic reactor simply as follows:
Molar flow rate of SO2 = 0.004 C1 = 61.470 kmol d−1.
4.2.3 Mass balance on the electrolysis section
Since both absorbers have a conversion efficiency of 100%, we can say that the amount of sulphur dioxide comes out of converter can be kept until the end of the method of contact.
This means that this quantity will be the same that powers the electrolyser, which equals 61.470 kmol d−1.
Generally, the electrolysis step can be presented as can be seen in Fig. 12.
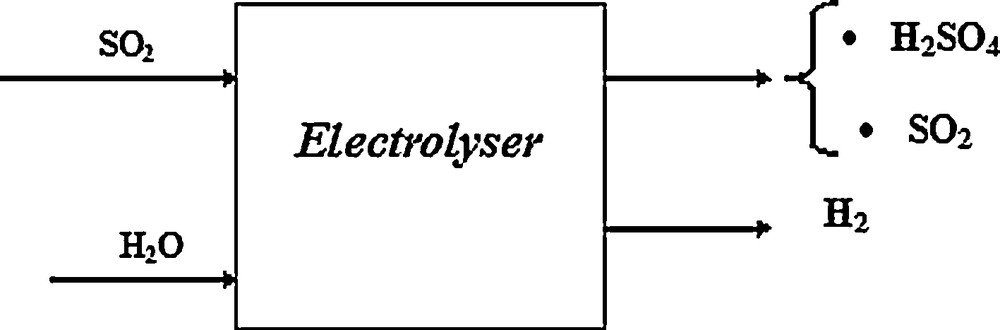
Block diagram of the electrolysis section.
Note that the oxidation reaction of sulphur dioxide into sulphuric acid which occurs in the anode is done with a low rate conversion as it is listed in the bibliography; the rate conversion in the electrolyser is about 50%. To improve the overall performance of electrolyser we propose to operate a recycling system for sulphur dioxide.
For better understanding we present all of the above by a Block diagram in Fig. 13.

Block diagram of the total electrolyser (with separator).
As data for this process we have:
- • B1: SO2 molar flow rate at the entrance of the electrolyser equal to 61.470 kmol d−1;
- • the anodic reaction yield of 50%;
- • SO2 recycling rate equal to 100.
The partial assessment of the sulphur is given by Eq. (7):
(7) |
The partial assessment of oxygen is given by Eq. (8):
(8) |
The partial assessment of hydrogen is given by Eq. (9):
(9) |
But at the anode the reaction occurs with a yield of 50%, then we can write Eq. (10):
(10) |
Since SO2 recycling rate equals to 100%, so:
According to the total reaction:
SO2 + 2 H2O → H2SO4 + H2We can say that the amount of water necessary for the electrolysis is twice the sulphur dioxide:
Eq. (10) gives:
(11) |
So, A = 2 × B3 = 4 × X × E
Eq. (8) gives: 4 × B1 + 2 × B1 = 4 × X × E + 2 × Y × E
So: 6 × B1 = 4 × X × E + 2 × Y × E
(12) |
The equality of the two Eqs. (11) and (12) gives:
Hence the Eq. (10) gives:
Then the Eq. (9) leads to:
Numerical application:
A: molar flow rate of water = 245.880 kmol d−1 = 4.426 t d−1 = 5511.179 m3 d−1;
B3: SO2 molar flow = 122.940 kmol d−1 = 7.868 t d−1;
C: hydrogen molar flow rate = 307.35 kmol d−1 = 614.7 kg d−1;
E: molar flow rate of sulphuric acid = 122.940 kmol d−1 = 12.048 t d−1;
X: The concentration of sulphuric acid = 50%.
The results of this quantitative study, which applied on the sulphuric acid plant and the electrolyser, are shown in Table 2.
Results of mass balance study.
Results | Quantity (t d−1) |
Recovered of sulphuric acid H2SO4 50 w % | 12.05 |
Treatment of sulphur dioxide SO2 emissions | 7.868 |
Production of hydrogen H2 | 3.70 |
This method interests not only the industry of sulphuric acid production but also the processes of pollution control of certain gas effluents containing SO2.
In Tunisia, local air pollution in the main cities, especially in Gabès, is mostly because of emissions from the chemical industries.
Industrial complex of Gabès in south Tunisia is selected to be the case study complex. In fact, most industries are chemical oriented, the fast growing numbers of H2SO4 factories has resulted in fairly serious air pollution specially sulphur dioxide SO2 pollution (Table 3).
Description of sulphuric acid production in Gabès.
Type of process | H2SO4 (t d−1) | SO2 (t d−1) |
Simple | 2400 | 31.20 |
Double | 3000 | 15.74 |
Total (t d−1) | 5400 | 46.94 |
The information about the sulphuric acid production in Gabès (Table 3) was given by the Tunisian Chemical Group (GCT).
By using the the Rule of Three method, we can confirmed that if we applied the new process in all the production units of sulphuric acid in Industrial complex of Gabès (in GCT), we will produce 71.80 t d−1 of sulphuric acid and 3.70 t d−1 of Hydrogen (so 535.4 m3 s−1 of hydrogen H2). Table 4 shows this result.
Results of the new process application in the industrial complex of Gabès.
H2SO4 (t d−1) | SO2 (t d−1) | H2 (t d−1) |
71.80 | 46.94 | 3.70 |
A simple estimation of the financial benefits of the application of this process is summarized in Table 5.
Estimation of financial benefits.
Quantity (t d−1) | Unit price ($ t−1) | Total ($ d−1) | |
H2SO4 (t d−1) | 71.80 | 300 | 21,540 |
H2 (t d−1) | 3.70 | 100,000 | 370,000 |
Total ($ d−1) | 3.92 × 106 |
We were used the price of hydrogen gas in heavy steel cylinders containing about 0.6 kg H2 per cylinder. The price of this hydrogen has been reasonably stable at about $100/kg plus cylinder rental.
4.3 Discussions
A new method for sulphur dioxide removal and hydrogen mass production has been developed.
To confirm the conversion efficiency of this process, the case of sulphuric acid plant, which used a double contact/double absorption process, was taken, this plant is located in the industrial complex of Gabès in south Tunisia.
A mass balance study was carried out to determine:
- • the quantity of sulphur dioxide treated;
- • the quantity of sulphuric acid recovered;
- • the concentration of sulphuric acid produced;
- • the quantity of hydrogen produced.
The results of this mass balance confirmed that this process can achieve economical and environmental benefits (production of 0.615 t d−1 of hydrogen, 12.05 t d−1 of sulphuric acid and treatment of 7.868 t d−1 of sulphur dioxide).
The application of this new process in the industrial complex of Gabès in south Tunisia can significantly reduce the SO2 air pollution in Gabès city (elimination of 46.94 t d−1) and also it can produce 3.7 t d−1 of hydrogen. This quantity of hydrogen is important (154.17 kg h−1), if we compared with the quantity of hydrogen produced by the Westinghouse house cycle, which is equal to 378 kg h−1.
The results obtained after the financial estimation demonstrated that the new process can succeed in the realisation of 3.92 million dollars of gain every day. It seems that is very ambitious.
4.4 Future work
The future work for this study will involve experimental work using a micro reactor and investigating the performance of each of the reactions. A more detailed simulation of the process is planned with Aspen plus. A final feasibility analysis for the proposed process will also need to be carried out.
5 Conclusion
A new method for sulphur dioxide removal has been developed; the idea consists in coupling the phenomenon of electrolysis upstream to the sulphuric acid plant. This idea can achieve economical and environmental benefits (Production of 6888.974 m3 d−1 of hydrogen and treatment of 7.868 t d−1 of sulphur dioxide).
It is concluded that the usage of this electrochemical depollution process, can significantly reduce the SO2 air pollution in Gabès city (elimination of 46.94 t d−1).
The results obtained are ambitious for future application of the new process which can succeed in the realisation of 3.92 million dollars of gain.
The benefits of this Cleaner Process Production are:
- • improving environmental situation;
- • continuous environmental improvement;
- • gaining competitive advantage;
- • increasing productivity;
- • increasing economical benefits.
Furthermore, it is planned for a future work to conduct a detailed cost accounting and exergoeconomic analysis for this new process.
Acknowledgment
We would like to thank Mr. Urban Mayer, expert in the Centre for International Migration and Development in Germany (CIM), for his encouragement and valuable discussions about this subject.