1 Introduction
Nanocrystalline zirconium oxide (zirconia, ZrO2) is one of the most important ceramic materials, shock- and corrosion-resistant, with wide variety of potential applications such as a structural and biomaterial, solid-state electrolyte, gas sensor and thermal barrier coating [1]. It also attracts a great attention as a catalyst or as a support for many reactions [2,3]. Moreover, the application of the nanosized metastable tetragonal zirconia particles, as a dispersed phase in ceramic materials, leads to the increase in their fracture toughness, strength and hardness [4]. Those unique properties of ZrO2 have become a driving force for the development of alternative techniques for its preparation, among them the aqueous combustion synthesis [5]. It is a versatile, simple, safe, energy- and time-saving process, with capability to produce homogeneous, high purity and nanocrystalline ceramic powders [6]. The aqueous combustion synthesis involves the formation of a homogeneous oxidant-fuel precursor and its redox exothermic reaction, accompanied with a quick evolution of large volume of the gaseous products. The nature of the combustion and the properties of the resulting powder depend on the type and the amount of the fuel used in the process. According to Toniolo et al. [7], a good fuel should react non-violently, produce non-toxic gases and act as complexing agent to form metal cations. Glycine, one of the cheapest amino acids, is known to act as a complexing agent due to its carboxylic acid group at one end and amino group at the other. Such types of zwitterionic character of a glycine molecule can effectively complex metal ions of different ionic size, which helps in preventing their selective precipitation to maintain compositional homogeneity among the constituents. On the other hand, it can also serve as a fuel in the combustion reaction, being oxidized by nitrate ions [8]. Therefore, glycine was chosen as a fuel for the preparation of nanocrystalline zirconia powders in this study.
Several papers have already discussed the role of the fuel in controlling the morphology of the synthesized powders [7–11]. A zirconia nanosized single crystal has already been prepared by the combustion of an aqueous solution of metal nitrate and glycine [12]. Zirconia nanocrystalline powders were also synthesized using sucrose [13], glycine [9] and citric acid [14] as a fuel. However, in the most of these researches, the amount of the fuel and/or complexing agent has been fixed according to the concept of propellant chemistry [15]. Scarce systematic studies on the effect of the fuel-to-oxidant molar ratio on the nature of combustion and properties of zirconia nanocrystalline powders have been reported. As far as we know, the effect of calcination temperature on zirconia's properties [16,17], obtained by combustion method, has not also been presented. Moreover, in view of beneficial properties of metastable tetragonal zirconia particles, in the area of ceramic materials, we consider important to review its formation by different techniques: XRD, FTIR and Raman Spectroscopy. This is due to the fact that it is very difficult to distinguish between tetragonal and cubic phases of zirconia by a qualitative XRD analysis, as a result of both (400) and (004) lines splitting and (112) line broadening, as made by the most of researches.
Here, the combustion synthesis of nanocrystalline zirconia powders using glycine as a fuel and zirconyl nitrate as an oxidizer is reported. The study is focused on the effect of:
- • the fuel-to-oxidant molar ratio on the properties (such as: specific surface area, crystalline structure, crystallite size, extent and nature of agglomerates) of nanocrystalline zirconia powders;
- • sample morphology on tetragonal zirconia stabilization;
- • calcination temperature on the microstructural evolution of zirconia powders.
For these purposes, the synthesized powders have been characterized by: TGA, specific surface area measurements, SEM-EDS, XRD, FTIR and Raman Spectroscopy. The thermodynamic modeling of the combustion reaction was carried out in order to study the role of the fuel-to-oxidant molar ratio on the heat of combustion, theoretical combustion temperature, number of moles of gases evolved in the reaction and the nature of combustion process. The results of thermodynamic modeling were correlated with powders properties.
2 Experimental
2.1 Synthesis
Zirconyl nitrate hydrate [ZrO(NO3)2·xH2O, Aldrich, purity 99%, ZN] and glycine [NH2CH2COOH, Mallinckrodt, purity 99.5%, Gly] were used as the starting materials. The different compositions of the redox mixtures (Gly:ZN) for the combustion were calculated using the total reducing (+9) and oxidizing (−10) valences of the starting materials: Gly and ZN, respectively. According to the principle of propellant chemistry [15], for stoichiometric redox reaction, the ratio of the net reducing valency of the fuel net to the oxidizing valency of the metal nitrate should be unity (maximum quantity of energy released in the combustion process). Therefore, the Gly:ZN molar ratio for the stoichiometric combustion should be 1.11. Moreover, fuel-lean (0.5 and 0.75) and fuel-rich (2) Gly:ZN precursors were applied for sample preparation. The studied range of the Gly:ZN molar ratio was chosen experimentally to guarantee the auto-ignition of the combustion process, considering that it takes place only in a limited range of the fuel-to-oxidant molar ratio (above and below the stoichiometric one). The amounts of fuel as well as of oxidant were taken to obtain approximately 3 g of the final product. The required amounts of starting materials were dissolved in the minimum amount of deionized water and mixed to obtain transparent aqueous solution of oxidant-fuel precursor. After its thermal dehydration at ca. 80 °C, as soon as a viscous liquid was formed, the temperature was increased up to ca. 250 °C. It led to the auto-ignited, fast, self-sustaining, flameless and non-explosive combustion of the liquid, accompanied with a rapid evolution of large amount of gases and formation of an amorphous powder (as confirmed by XRD, not shown here), indicating the incomplete combustion. The nature of the ignition and the aspect of the obtained powders depended on the fuel-to-oxidant molar ratio. Henceforth, these samples are indicated as raw powders. Subsequently, they were calcined in air, at 600 °C, with a ramp rate 3 °C·min−1, for 4 hours at atmospheric conditions, in order to remove traces of unreacted starting materials (if any) and/or products of their decomposition and obtain pure and well-crystallized zirconia oxides. Moreover, some representative samples were calcined at 800 and 1000 °C with the purpose of studying the effect of calcination temperature on their physicochemical properties. Before calcination, the raw powders were hand ground in an agate mortar. For all Gly:ZN molar ratios, a similar quantity of ZrO2 powder after calcination process was obtained. An average efficiency of 75% of yield was achieved.
2.2 Characterization methods
The standard enthalpy of combustion (ΔH0) and theoretical adiabatic flame temperature (combustion temperature) (T), as a function of the Gly:ZN molar ratio, were calculated using the following thermodynamic expressions:
(1) |
(2) |
Relevant thermodynamic data for various reactants and products [18,19].
Compound | Cp (J·mol−1·K−1) | |
ZrO(NO3)2H2O(c) | –1820 | – |
NH2CH2COOH(c) | –333 | – |
ZrO2(c) | –1101.3 | 69.668 + (7.53·10−3·T) − (1.406·106·T−2) |
CO2(g) | –393.8 | (19.8·T) + (7.344·10−2·T2) − (5.602·10−5·T3) + (1.715·10−8·T4) |
H2O(g) | –242 | (32.24·T) + (1.92·10−3·T2) + (1.055·10−5·T3) − (3.59·10−9·T4) |
N2(g) | 0 | (31.1·T) − (1.357·10−2·T2) + (2.68·10−5·T3) − (1.168·10−8·T4) |
O2(g) | 0 | (28.11·T) − (3.68·10−6·T2) + (1.746·10−5·T3) − (1.065·10−8·T4) |
The thermal stability of raw zirconia powders was characterized by thermogravimetric analysis (TGA), using a Setsys 16/18 thermogravimetric analyzer (Setaram). The crucible containing about 10 mg of sample was heated from room temperature (r.t.) to 800 °C in air, with a ramp rate of 3 °C·min−1.
The morphology of ZrO2 powders was studied using a scanning electron microscopy–energy dispersive spectroscopy (SEM-EDS) technique. SEM measurements were performed by JSM-5910LV microscope (JEOL, Japan), using an acceleration voltage of 15 kV, equipped with energy dispersive spectrometer (EDS) (Thermo Noran, USA). Images were recorded at several magnifications. The elemental analysis in the studied microarea of the oxide surface layer was determined by the EDS method, basing on the obtained characteristic X-ray spectra. The examined samples were placed in a holder and before analyzing were coated with a carbon monolayer, using Cressington 208 HR system (Cressington Scientific Instruments Ltd., UK), in order to reduce the charge build-up on the samples.
The crystalline structure identification and crystallite size determination of ZrO2 powders was carried out using X-ray diffraction (XRD). Approximately 300 mg of sample, which had been hand ground in an agate mortar, was packed in the sample holder. XRD patterns were obtained at room temperature using a PANalytical's X’Pert-Pro MPD X-ray diffractometer (equipped with X’Celerator) with nickel-filtered Cu Kα radiation (λ = 1.5406 Å), operating at 40 kV and 30 mA. Divergent optics were used in a Bragg-Brentano (flat-plate sample) geometry, with the following slits: Soller (0.04 rad)–on incident and diffracted beams, fixed divergence (0.5°), antiscatter (1°). Data were collected in the 2θ range of 20–80°, with a step size of 0.0167° and step time of 10 s. Phase analysis was performed using X’Pert HighScore Plus software and JCPDS-ICDD PDF–2 database (International Centre for Diffraction Data-The Powder Diffraction File) in order to identify the crystalline phases. The quantitative phase analysis has been performed by the Rietveld refinement technique, via Hill and Howard's [20,21] procedure, using the following formula:
(3) |
The crystallite size (DXRD) of ZrO2 powders was determined by means of the X-ray line broadening method [22], according to the Scherrer equation (4).
(4) |
The specific surface area was measured with Sorptomatic 1900 apparatus (Carlo Erba), at −196 °C, by determining the amount of nitrogen gas adsorbed as a monomolecular layer on the sample. Prior to the measurement, all samples were degassed for 4 h at 250 °C. The specific surface area, SBET was calculated using BET equation [23]. Using the SBET value, the geometrical mean particle size (DBET) was calculated, assuming the presence of spherical particles, according to the following expression:
(5) |
Fourier-transform infrared (FTIR) spectra of ZrO2 powders were recorded by a Nicolet 6700 FT-IR spectrometer (Thermo Scientific, USA) with MCT detector (photoconductive detector HgCdTe), in the region of 4000–400 cm−1, at room temperature, using the KBr (5 wt.%) pellet technique for functional group analysis.
Raman spectra were obtained using FT-Raman spectrometer MultiRAM (Bruker, Germany) with a YAG laser source of wavelength 1064 nm, laser power of 500 mW, and the spectrum resolution of 1 cm−1.
3 Results and discussion
3.1 Thermodynamic modeling
The majority of solution combustion reactions are known as exothermic enough to provide high reaction temperatures, which are adequate for the combustion wave propagation and can also lead to the explosion if not appropriately controlled. In the present work, the combustion of glycine (Gly) – zirconyl nitrate hydrate (ZN) redox mixture was auto-ignited, self-propagated, flameless and non-explosive exothermic process for all studied Gly:ZN molar ratios. This reaction can be represented as follows:
Stoichiometric coefficients of the combustion reaction (α–γ), standard enthalpy of combustion (ΔH0), theoretical (T) and measured (Tm) adiabatic flame temperatures, as a function of the Gly:ZN molar ratio.
Gly:ZN molar ratio | α | β | χ | δ | ɛ | ϕ | φ | γ | Moles of gaseous product/Moles of ZrO2 | –ΔH0 (kJ·mol−1) | T (°C) | Tm (°C) |
0.5 | 1 | 0.5 | 0 | 1 | 1 | 2.25 | 1.25 | 1.38 | 5.88 | 53.1 | 192 | 135 |
0.75 | 1 | 0.75 | 0 | 1 | 1.5 | 2.87 | 1.37 | 0.82 | 6.56 | 316.8 | 978 | 730 |
1.11 | 1 | 1.11 | 0 | 1 | 2.22 | 3.78 | 1.55 | 0 | 7.55 | 700.7 | 1725 | 1305 |
2 | 1 | 2 | 2 | 1 | 4 | 6 | 2 | 0 | 12 | 1642.5 | 2461 | 1210 |
One can see that the increase in the Gly:ZN molar ratio, leads to the increase in the amount of gaseous products (ɛ–γ), which could be an important factor controlling the specific surface area of the obtained ZrO2. Moreover, if the amount of oxygen in the Gly:ZN mixture is in excess of that required for the complete combustion of the fuel (fuel-lean mixture), a portion of oxygen does not react and appears in the exhausts (γ), as previously reported in the case of glycine-cerium nitrate [8] and glycine-aluminum nitrate [7] combustion reactions. On the other hand, in the case of the oxygen shortage in the Gly:ZN mixture (fuel-rich mixture), the extra amount of atmospheric oxygen (χ) for the complete combustion of the fuel is needed.
Fig. 1 presents the heat of combustion (–ΔH0) and theoretical combustion temperature (T, theoretical adiabatic flame temperature), as a function of the Gly:ZN molar ratio, which were calculated by Matlab® using the relevant thermodynamic data (Table 1) for various reactants and products.
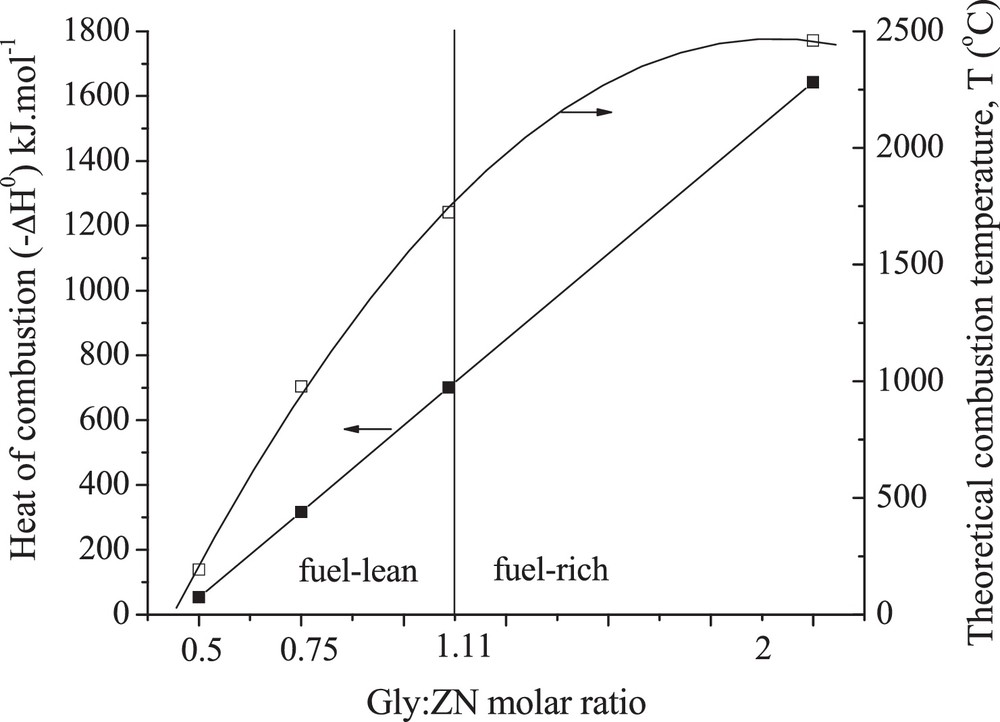
Variation of heat of combustion () and theoretical combustion temperature () as a function of the Gly:ZNmolar ratio.
For Gly:ZN combustion reaction, the heat of combustion and theoretical combustion temperature significantly increase with an increase in the amount of fuel used for the combustion (Gly:ZN molar ratio). For both stoichiometric and fuel-rich Gly:ZN mixtures, the theoretical adiabatic flame temperature is significantly higher than 1170 °C, the temperature above which tetragonal ZrO2 is stable, suggesting the effect of this parameter on the structural properties of ZrO2. However, it should be emphasized that the measured combustion temperatures (Tm) were much lower than the calculated one, especially in the case of the sample prepared using fuel-rich Gly:ZN mixture, probably due to incomplete combustion reaction, radiative losses, and heating of air (Table 2). It should be also noted that these measurements can be characterized with some inaccuracy due to the very spontaneous character of the combustion process as well as thermocouple inertia and its punctual form of temperature measuring. The theoretical combustion temperature of Gly:ZrO(NO3)2·H2O stoichiometric mixture, calculated in this work (ca. 2270 °C), is much higher than those reported in the literature for Ce(NO3)3·6H2O:Gly (ca. 1740 °C) [8] and Fe(NO3)3·9H2O:Gly (ca. 1520 °C) stoichiometric mixtures [24]. One can see that this temperature decreases when increasing the amount of molecules of water attached to the metal precursor. It suggests that water remaining in the metal nitrate-glycine solution at the temperature of auto-ignition strongly influences the adiabatic flame temperature. More hydrated metal precursors probably can ignite at relatively lower temperatures than water-free systems. Moreover, considering that this residual liquid must be transformed to the vapor and finally be heated as other combustion products, lower values of the resulting (real) combustion temperatures can be expected.
3.2 Sample synthesis
The color of the as-synthesized powders was found to change, from brownish to blackish, with an increase in the Gly:ZN molar ratio used for the synthesis. It could be related to:
- • the presence of carbonaceous residue arising from un-reacted glycine, especially evident in the case of the sample prepared using fuel-rich mixture due to insufficient amount of oxidizer specimen (ZrO(NO3)2·H2O);
- • and lower real temperature of combustion, comparing to theoretical one necessary for a complete reaction. As it was expected, after calcination all powders were white.
During the combustion of the fuel-lean mixtures, the amount of gaseous products was much higher than that of the fuel-rich one, leading to the formation of more voluminous and apparently highly porous powders. This observation is contrary to the expected one, made on the basis of the reaction stoichiometry (Table 2, number of moles of gaseous products/moles of ZrO2). We believe that the reason for this contradiction is related to much lower real temperature of combustion, comparing to the theoretical one necessary for a complete reaction, especially evident for the sample prepared by fuel-rich mixture. The change in the color of the released fumes, from dark yellow (reddish) to white, with an increase in the Gly:ZN molar ratio was also observed. This remark is in the discrepancy with the statement made by Reddy et al. [12] who reported that the color of the fumes during smoldering combustion changed from white-brown to brown with an increase in the Gly:ZN molar ratio. We believe that this inconsistency can be clarified as follows. According to the literature [7], self-sustaining nature of the combustion is a result of the following steps:
- • the formation of the precursor mixture containing metal nitrate and glycine, used as combustible fuel;
- • its dehydration which leads to nitrate decomposition giving oxides of nitrogen (NOx) as a product;
- • the reaction between the gaseous NOx and the fuel generating heat and higher amount of gases;
- • the homogeneous gas-phase, exothermic oxidation-reduction which increases the temperature of the intact viscous mixture at once adjoining the combustion zone;
- • the quick reaction which is sustained until the entire intact zone will be consumed.
Considering those statements, we believe that the formation of NOx can be the reason for the different colors of fumes released during the combustion realized using different ZN:Gly molar ratios. NOx is a generic term for nitric oxide (NO, colorless gas) and nitrogen dioxide (NO2, vivid orange gas). In the presence of air, the ratio between NO and NO2 can change due to thermodynamic equilibrium, as proposed by Gómez-García et al. [25]. At lower temperatures (< 230 °C), the formation of NO2 is favorable, at higher ones (> 630 °C) the formation of NO occurs. If a fuel-lean mixture was used for synthesis, a lower temperature for its complete combustion was required, leading to the formation of mostly NO2 and related to it the reddish color of the fumes. In the case of synthesis using fuel-rich mixture, higher temperature for its complete combustion was necessary, leading to the formation of mostly colorless NO and related to it change in the color of the fumes to white.
3.3 Sample characterization
Fig. 2 presents the TG-DTG curves, in a stream of air, of raw powders synthesized using different Gly:ZN molar ratio. The TG thermograms of fuel-lean and stoichiometric samples exhibit two main regions of weight loss. The first one (ca. 3–17%, depending on the Gly:ZN molar ratio), continous and in general mayor, in the temperature range of 15–500 °C, with maximum at at ca. 330 °C, relates to the main decomposition and/or combustion of the raw powders, resulting in the formation of zirconium oxide. The second one, subsidiary (ca. 5%) takes place in the temperature range of 500–620 °C, presumably due to the oxidation of some carbonaceous residues to CO2. One can see a slight shift of the maximum of the DTG curve, related to the carbonaceous residues oxidation, to the higher temperatures with an increase in the Gly:ZN molar ratio. For fuel-rich powder four main regions of weight loss are observed. The first one (ca. 30%), continuous in the temperature range of 15–260 °C, with the maximum at ca. 200 °C, relates to the unreacted glycine decomposition; the second one (ca.16%) in the temperature range of 260–320 °C, with the maximum at ca. 290 °C, and the third one (ca. 20%) in the temperature range of 320–500 °C, with the maximum at ca. 360 °C, can represent the main decomposition and/or combustion of the raw powders, resulting in the formation of zirconium oxide. The fourth one (ca. 2%) in the temperature range of 320–620 °C, with the maximum at ca. 565 °C, probably takes place due to the oxidation of some carbonaceous residues to CO2. The total weight loss of the studied samples increases with an increasing amount of the glycine in the combustion mixture, according to the Gly:ZN molar ratio: 1:0.5 < 1:0.75 < 1:1.11 < 1:2. Moreover, one can see that in the case of the fuel-rich sample (the darkest one) the weight loss related to the carbonaceous residues oxidation was the lowest one and took place at lower temperature than in the case of the rest of the studied powders. We consider that the un-reacted glycine decomposition took place at much lower temperature (ca. 200 °C), hence lower amount of carbonaceous residue was present in the sample. One can see that independently of the Gly:ZN molar ratio, at temperature above 600 °C, all raw ZrO2 powders presented constant weight. We believe that thermal treatment at 600 °C is going to ensure their total decomposition, therefore, it was chosen as calcination temperature for further investigation.
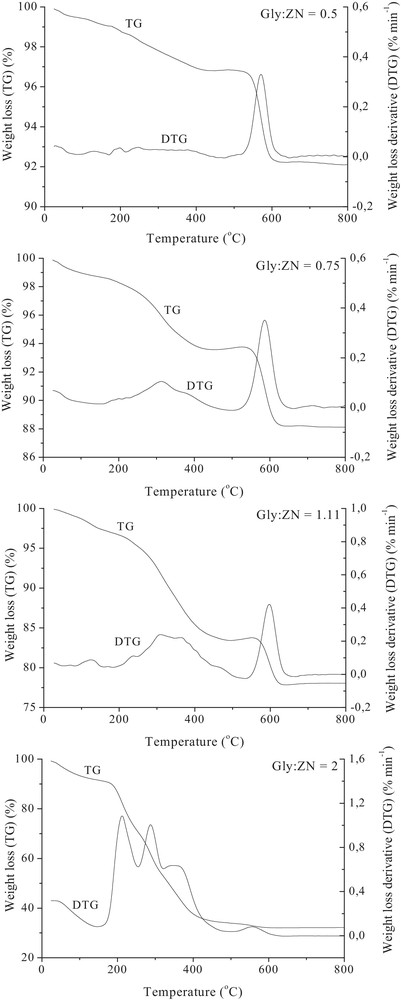
TG-DTG curves depicting thermal decomposition of raw ZrO2 powders in the air.
Fig. 3a presents typical SEM micrographs of ZrO2 obtained using different Gly:ZN molar ratios, calcined at 600 °C. The results show that all powders are uniform, voluminous and spongy in nature. They exhibited foamy and agglomerated particles with a wide distribution, strongly dependent on the Gly:ZN molar ratio. One can see that the registered agglomeration tendency increases as the Gly:ZN molar ratio increases. The samples prepared using Gly:ZN molar ratios ≤ 1.11 are loosely agglomerated and present a high amount of characteristic voids with typical sizes of 0.5–5 μm. The formation of these features can be attributed to the fast evolution of large amount of gases during the combustion process. Quick gaseous products formation disperses the heat of combustion, limiting the rise of temperature and reducing the possibility of premature, partial and local sintering of primary particles. Their size increases with an increase in the Gly:ZN molar ratio due to the increasing number of moles of gaseous products during the synthesis process (Table 2), with the maximum observed for stoichiometric Gly:ZN mixture. The powder prepared using excess of Gly presents lower degree of uniformity. It consists of mostly spherical particles with typical sizes of 1–5 μm, much bigger than those obtained using fuel-lean and stoichiometric Gly:ZN mixtures. Moreover, lower quantity of characteristic voids in its structure is observed probably due to the lower amount of gaseous products evolved during the combustion as well as high adiabatic flame temperature, as we mentioned above. For all samples, the EDS analysis showed the presence of zirconia and confirmed low concentration of impurities after calcination at 600 °C. On further increase in calcination temperature, more agglomerated and compact powders are formed (Fig. 3b). Moreover, the amount and the size of characteristic voids observed for the sample calcined at 600 °C decreases gradually. The uniform, voluminous and spongy nature of the samples is reduced after calcination at high temperature.

Secondary electron (SE) photomicrographs of ZrO2 powders prepared using: a: different Gly:ZN molar ratios, calcined at 600 °C; b: Gly:ZN = 0.5, calcined at different temperatures. Magnifications: × 2000.
X-ray diffraction patterns of ZrO2 powders, synthesized using different Gly:ZN molar ratio, calcined at 600 °C are presented in Fig. 4a.

X-ray diffraction of ZrO2 powders prepared using: a: different Gly:ZN molar ratios, calcined at 600 °C; b: Gly:ZN = 0.5, calcined at different temperatures; the peak marked as m and t corresponds to monoclinic (JCPDS No. 00-037-1484) and tetragonal (JCPDS No. 00-050-1089) structures, respectively.
Crystalline phases were identified by a comparison with the corresponding JCPDS files. XRD patterns of all ZrO2 powders, calcined at 600 °C correspond to both monoclinic (JCPDS card no.: 00-037-1484) and tetragonal (JCPDS card no.: 00-050-1089) structures. For all samples, the tetragonal phase is a principal one (Table 3).
Characterization of ZrO2 powders prepared using different Gly:ZN molar ratios, calcined at 600 °C.
Gly:ZN molar ratio | Relative amount of crystalline phases (%) | DXRD (nm) | SBET (m2·g−1) | Vp (cm3·g−1) | Dp (nm) | DBET (nm) | ψ | ||
T | M | T | M | T | T | ||||
0.5 | 95.5 | 4.5 | 13.4 | 11.7 | 45.8 | 0.190 | 13.4 | 21.4 | 1.60 |
0.75 | 96.1 | 3.9 | 14.9 | 11.7 | 40.7 | 0.180 | 14.1 | 24.3 | 1.62 |
1.11 | 96.1 | 3.9 | 15.0 | 11.7 | 40.2 | 0.198 | 14.0 | 24.4 | 1.63 |
2 | 96.8 | 3.2 | 15.5 | 11.1 | 23.3 | 0.054 | 6.5 | 42.1 | 2.72 |
It should be noticed that both tetragonal and cubic phases produce a broad diffraction peak at 2θ = 30°, making differentiation between them difficult, especially if the sample is characterized with small particle size and/or poor crystallinity. Therefore, the XRD studies were complemented with FTIR and Raman experiments. One can see a very slight increase in the relative amount of tetragonal phase with an increase in the Gly:ZN molar ratio (Table 3). Considering that the agglomeration tendency of synthesized powders was also increasing with an increase in the Gly:ZN molar ratio (Fig. 3a), it could be suggested that the presence of hard aggregates promotes the formation of metastable-tetragonal nanocrystalline zirconia, as previously proposed by Skukla et al. [26]. The mechanism of t-zirconia stabilization can be based on the volume expansion associated with the tetragonal to monoclinic ZrO2 transformation. The presence of hard agglomerates suppresses the volume expansion, stabilizing the tetragonal zirconia. The primary crystallite size of powders calcined at 600 °C, determined using the Scherrer equation (DXRD), is presented in Table 3. The slight increase in the crystallite size with the increase in the Gly:ZN molar ratio can be attributed to an increase in flame temperature, which assists crystal growth. There is also a correlation between the increase in the crystallite size and the reduction in the specific surface area, as a function of increasing fuel content (Table 3). As similar observation has already been done by Toniolo et al. [7] in the case of alumina synthesis by the glycine-nitrate combustion. The zirconia powders obtained using fuel-lean mixture present the highest specific surface area, whose value decreases as the Gly:ZN molar ratio increases. We believe that the observed tendency is directly related to the nature of combustion process. The application of Gly shortage results in the low reaction enthalpy (Table 2), remaining low local temperature of formed particles and preventing their agglomeration. Moreover, this reaction was accompanied with the evolution of large amount of gaseous products (see Sample synthesis section) leading to the formation of more porous structure (Table 3). As the Gly:ZN molar ratio increases, higher combustion temperatures are generated (Table 2) and lower amount of gases are evolved (see Sample synthesis section), leading to the formation of a dense structure (Table 3). It should be also noted that the difference between the surface area of the powders synthesized by the fuel-lean and stoichiometric mixtures is not as significant as in the case of that between the fuel-lean and fuel-rich ones. This may be attributed to the very significant difference in the corresponding flame temperatures (Table 2), as also previously observed by Purohit et al. [8] for cerium nitrate-glycine combustion. As far as we know, the surface area of 45.8 m2·g−1, obtained in this study using stoichiometric Gly:ZN mixture, is the highest one reported in the literature for ZrO2 prepared by combustion method.
Fig. 5 shows the representative N2 adsorption–desorption isotherm of ZrO2 prepared using a molar ratio Gly:ZN = 0.5. All four analysed samples showed type IV isotherms, according to the IUPAC clasification, with hysteresis loops (type A, according to de Boer, or H1) typical of mesoporous materials. The hysteresis loop is associated with the capillary condensation taking place in the mesopores signifying the preservation of the mesoporous structure even after calcination at elevated temperature. The type A hysteresis loop is attributed to the cylindrical shaped pores. A typical pore size distribution for this sample is included in Fig. 5. The sample exhibits a uninodal pore size distribution.

The representative N2 physisorption isotherm and BJH pore size distribution of ZrO2 prepared using a molar ratio Gly:ZN = 0.5.
Table 3 presents additionally the geometrical particle size (DBET) of ZrO2 powders calcined at 600 °C, estimated from BET data assuming that the particles are spherical. For all samples, the calculated DBET values are higher than those of the DXRD. This deviation can be explained by a potential presence of small agglomerates and grain boundary interfaces in ZrO2 powders, which are not available to N2 gas during the BET analysis. Moreover, the XRD technique can detect the subgrains within particles. The ψ (ψ = DBET/DXRD) factor, which reflects the extent of agglomeration of the primary crystallites, was also estimated (Table 3). The ψ value increases from ca. 1.6 for fuel-lean synthesized zirconia to 2.72 for fuel-rich one, indicating that the extent of agglomeration increases as a function of the increasing amount of the fuel used for combustion.
Fig. 4b shows the XRD patterns of one of zirconia powders (Gly:ZN = 0.5) calcined at different temperatures. On the further increase in calcination temperature, the narrowing of main diffraction peaks, in comparison to the sample calcined at 600 °C, is registered due to the formation of bigger crystallites (Table 4). Moreover, the amount of the monoclinic phase increases, probably due to the observed crystal growth. After calcination at 800 °C, almost 50% of tetragonal phase is transformed into a monoclinic one (Fig. 4b, Table 4). After calcination at 1000 °C, zirconia presents mainly monoclinic phase (98.5%). Its crystallite size is ca. 32 nm. Upon an increasing calcination temperature, a significant decrease in the surface area of ZrO2 (ca. 70%) as well as an increase in the powders crystallite size is observed (Table 4). For samples calcined at 800 and 1000 °C, the calculated DBET values are significantly higher than those of the DXRD due to the increasing amount of agglomerates (Fig. 3b). The ψ value increases by 40% with an increase in calcination temperature, confirming the extent of agglomeration.
Characterization of ZrO2 powders prepared using Gly:ZN = 0.5, calcined at different temperatures.
Calcination temperature (°C) | Relative amount of crystalline phases (%) | DXRD (nm) | SBET (m2·g−1) | Vp (cm3·g−1) | Dp (nm) | DBET (nm) | ψ | ||
T | M | T | M | T | T | ||||
600 | 95.5 | 4.5 | 13.4 | 11.7 | 45.8 | 0.190 | 13.4 | 21.4 | 1.60 |
800 | 55.5 | 44.5 | 18.1 | 17.5 | 26.5 | 0.058 | 6.8 | 37.0 | 2.04 |
1000 | 1.5 | 98.5 | 33.7 | 31.7 | 12.6 | 0.015 | 2.5 | 81.1 | 2.56 |
In tetragonal zirconia, the smallest Bravais cell contains four oxygen ions and the tetrahedral surrounding oxygen are deformed (i.e. they are expanded along the z-axis). Therefore, each movement of oxygen atoms undergoes threefold splitting. Finally, the movements of the four oxygen atoms combine giving rise to four nondegenerate modes and to four doubly degenerate ones. Four of them are IR active and four Raman active. As a result of the combining movements of oxygens with the movements of zirconium ions and subtracting the acoustical modes, three IR bands (475, 580 and 670 cm−1, each of them undergoing TO-LO splitting) and six Raman bands (145, 265, 313, 460, 600, 645 cm−1) for the spectrum of tetragonal zirconia should be observed [27].
The FTIR spectra of the samples prepared using different Gly:ZN molar ratios, calcined at 600 °C are presented in Fig. 6a. The stretching frequencies of Zr–O vibrations can be observed in the 400–1190 cm−1 frequency region. For samples calcined at 600 °C (Fig. 6a), the FTIR spectra display an intense absorption with a maximum at 475 cm−1 characteristic of tetragonal zirconia. These spectra are quite similar to those observed and described previously (see Fig. 2 in Ref. [28] and Fig. 3 in Ref. [27]). The presence of monoclinic phase is not evident since no additional bands are detected, in particular at 510 and 740 cm−1 (Fig. 6a).
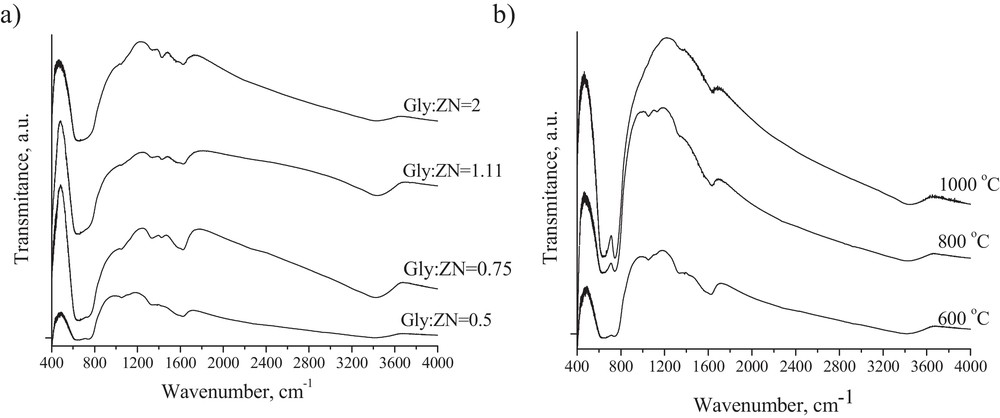
FT-IR spectra of the ZrO2 powders prepared using: a: different Gly:ZN molar ratio, calcined at 600 °C; b: Gly:ZN = 0.5 molar ratio, calcined at different temperatures.
However, under increasing calcination temperature the band at 740 cm−1 becomes visible (Fig. 6b), which intensity increases with an increase in calcination temperature, confirming the presence of monoclinic phase in these powders. In addition, the bands at 1055, 1330 and 1430 cm−1 are probably due to the presence of carbonate species, which are variable with respect to calcination temperature and crystalline structure of the oxides (Fig. 6b). The presence of a broad band in the region of 3000–3600 cm−1 is attributed to the O–H stretching of physically adsorbed water. Our observations are similar to those presented in the literature [13,29].
In order to study zirconia phase transformation and to confirm the phases present in the studied powders, Raman spectroscopy analysis was also performed with one of studied samples, calcined at different temperatures (Fig. 7). The bands at 174, 184, 215, 303, 330, 345, 380, 474, 499, 537, 559, 617 and 638 cm−1 are typical of the monoclinic phase of zirconia and those at 145, 265, 313, 460, 600, 645 cm−1 are representative of the tetragonal one. The Raman spectrum for the sample calcined at 600 °C is of a low intensity. However, the characteristic lines for both ZrO2 structures were identified in the Raman spectrum collected for the sample calcined at 600 °C.
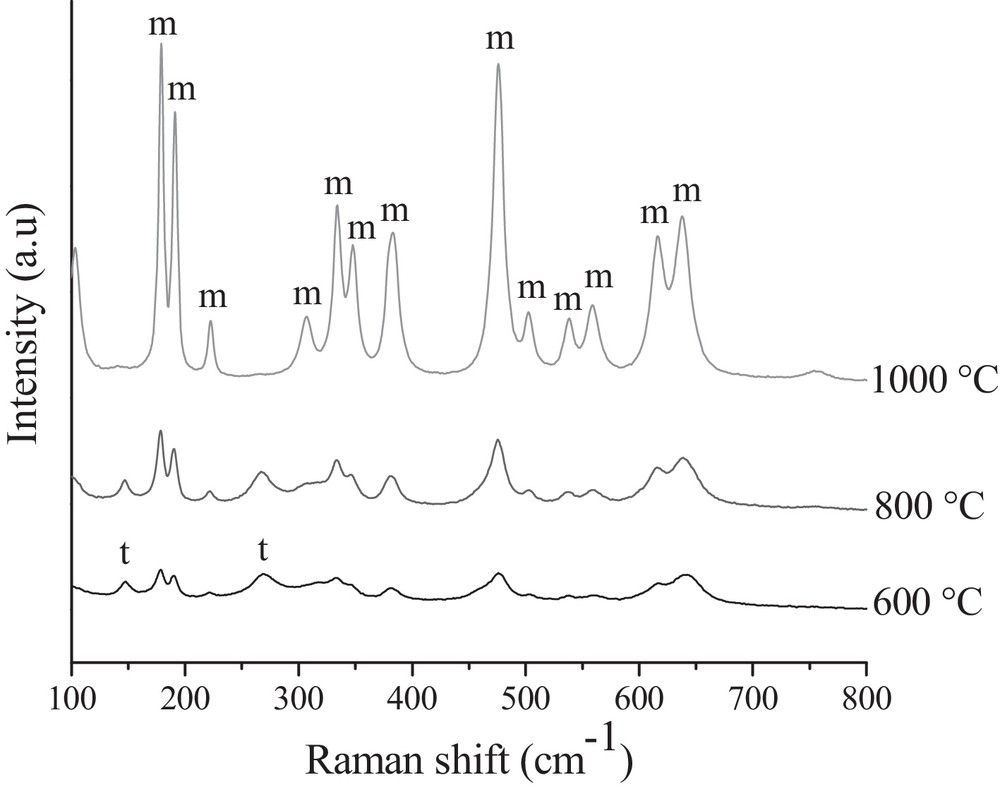
Raman spectra of the ZrO2 powders prepared using Gly:ZN = 0.5, calcined at different temperatures.
The presence of a doublet at 170–185 cm−1, characteristic of the monoclinic zirconia phase, was registered after calcination even at 600 °C confirming that this is a sufficient temperature for the initiation of monoclinic ZrO2 formation. The band at 303 cm−1 may overlap with tetragonal and monoclinic phases [13]. The most of the tetragonal phase is transformed to the monoclinic one at a temperature of 1000 °C. This is proved by the lack of bands at 145 and 265 cm−1 assigned to tetragonal ZrO2. Moreover, the absence of the bands at 150, 250, 360, 480 and 625 cm−1 confirms that no cubic phase is present in all studied powders. The overall half-width at half-height of the bands of Raman spectrum is proportional to the inverse of the grain size [13]. The broad bands in the studied spectra indicate the presence of particles in the nanoregime. The present results agree with those obtained by XRD. Quantitative phase analysis of the obtained ZrO2 spectra (Fig. 7), estimated as proposed by Kim et al. [30], shows that the powder calcined at 600 °C is at 72.8% monoclinic, calcined at 800 °C in 82.6% and that at 1000 °C in 97.9%. One can see that these results are in disagreement with the quantitative phase analysis made basing on the XRD patterns (Table 3). We believe that it can be interpreted in the terms of:
- • phase transformation of ZrO2 which starts from the surface region, progressing to the bulk; the initial change of the phase at the surface can be sensitively detected by Raman spectroscopy rather than XRD;
- • the fact that monoclinic zirconia is a stronger scatter that tetragonal one; Raman spectroscopy is superior in discerning the monoclinic phase, particularly when the monoclinic fraction is small [30]. We have observed that the Raman peak ratio Im(184 cm−1)/It(145 cm−1) is ca. 8 times bigger than the XRD one Im(–111)/It(111).
Table 5 presents a brief comparison of some representative textural and morphological properties of ZrO2 powders obtained in this study with those reported in the open literature, prepared using different preparation techniques and calcined at different temperatures. One can see that the specific surface area of ZrO2 powders prepared by combustion method, using citric acid and sucrose as fuels, is definitively lower than that obtained in this study. Moreover, they are characterized with slightly lower amount of tetragonal phase, if reported. However, this analysis is especially difficult since, in most of the research papers, the presence of tetragonal zirconia was confirmed only on the basis of XRD data. Compared to other preparation methods, ZrO2 obtained by combustion is characterized with both the highest percentage of tetragonal phase and the highest specific surface area value. Independently of the preparation method, its sintering at high temperature due to the phase transformation accompanied with an increase in crystallite size can be seen.
Comparison of some representative textural and morphological properties of ZrO2 powders prepared using different methods and calcined at different temperatures.
Preparation method | Calcination temperature (°C) | Relative amount of T (%) | DXRD (nm) | Specific surface area (m2·g−1) | Reference |
Precipitation | 500 | 5 | n.r. | 38.3 | [31] |
Precipitation/digestion | 500 | 30 | n.r. | 75.7 | [31] |
Precipitation | 500 | n.r. | 9.5 | 74.0 | [32] |
Precipitation | 900 | n.r. | 24.9 | 16.0 | [32] |
Commercial ZrO2 | 500 | 0 | 500 | 35 | [33] |
Polymerized organometallic compound | 700 | 30 | 20 | 8 | [33] |
Precipitation | 600 | n.r. | 10.5 | n.r. | [27] |
Precipitation | 900 | n.r. | 13 | n.r. | [27] |
Sol-gel like | 550 | n.r. | 19 | 4.5 | [34] |
Combustion (sucrose as the fuel; O/F = 0.2) | 600 | 92 | n.r. | 31.1 | [13] |
Combustion (sucrose as the fuel; O/F = 0.2) | 1100 | 0 | n.r. | n.r. | [13] |
Combustion (citric acid as the fuel; O/F = 0.67) | 600 | 93 | 9 | n.r. | [14] |
Combustion (Gly:ZN = 1.11) | 400 | n.r. | 20 | 17 | [9] |
Combustion (Gly:ZN = 0.5) | 600 | 95.5 | 13.4 | 45.8 | This study |
Combustion (Gly:ZN = 0.5) | 1000 | 1.5 | 33.7 | 12.6 | This study |
4 Conclusions
Nanocrystalline tetragonal zirconia powders have been successfully prepared by aqueous combustion synthesis using glycine as a fuel and zirconyl nitrate as an oxidizer. The results of thermodynamic modeling as well as physicochemical characterization were correlated with powder properties. The most significant results can be summarized as follows:
- • Gly:ZN molar ratio vs. properties of zirconia: the increase in Gly:ZN molar ratio led to:
- ∘ the increase in agglomeration tendency and decrease in degree of sample uniformity; this due to the lower amount of gaseous products evolved during combustion reaction as well as high adiabatic flame temperature,
- ∘ the slight increase in the powders crystallite size due to the increase in flame temperature, which assists crystal growth,
- ∘ the decrease in specific surface area; Gly shortage led to low reaction enthalpy and low local temperature of formed particles, preventing their agglomeration and creating more porous structure,
- ∘ a fuel-lean ratio was found as favorable to produce specific zirconia properties,
- ∘ the detailed studies performed by Rietveld analysis, FTIR and Raman Spectroscopy confirmed the predominant presence of metastable tetragonal zirconia;
- • sample morphology vs. tetragonal zirconia stabilization: the presence of hard agglomerates (powder with Gly excess, high reaction enthalpy, high adiabatic flame temperature, low amount of evolved gases) suppresses the volume expansion, stabilizing the tetragonal zirconia;
- • calcination temperature vs. microstructural evolution of zirconia: the increase in calcination temperature led to more agglomerated, compact and less uniform powders. The nanocrystalline nature of the zirconia is the reason for bigger crystallites formation, the increase in the relative amount of monoclinic phase and sample sintering after calcination at high temperature.
Acknowledgments
Colciencias-Universidad Nacional De Colombia, Sede Manizales is gratefully acknowledged for financial support (Convocatoria 613 de 2013). The authors are also grateful to M. Sc. Eng. Ana Catalina Duque Salazar for her help in performing some experimental studies.