1 Introduction
Gaseous SOx emissions mainly originate from fossil fuel-fired combustion plants used for electricity and/or heat production, for instance gas turbines burning liquid fossil fuels. Besides their corrosive effect, SOx are harmful to human health and the environment since they are a primary cause of acid rain [1] and a major precursor of secondary aerosols in the atmosphere. The long-standing concern regarding air pollution has led to more stringent SOx emissions regulations, which have been made possible thanks to the development and the implementation of various flue gas desulfurization (FGD) processes. Nowadays, wet and dry scrubbing [2] are the main technologies implemented in industrial processes and in combustion plants. Wet scrubbing consists in spraying an aqueous solution of alkali or alkali earth metal base (NaOH; Ca(OH)2, etc.) in the flue gas stream, which reacts with SOx to form the corresponding sulfates, while the dry process is mainly performed by injecting a dry alkali earth salt such as CaCO3. Despite their proven performance in terms of SOx removal, these technologies suffer from several disadvantages, including significant energy consumption, the use of large amounts of reagents, the production of large amounts of wastes (CaSO4, Na2SO4) and their non-regenerability.
Dry regenerative processes consisting in adsorbing SOx on metal oxides are being investigated as an alternative to wet and dry scrubbing technologies. Such processes are based on bifunctional materials that first oxidize SO2 to SO3 (Eq. (1)) then chemisorb SO3 as metal sulfate (Eq. (2)). Moreover, to make the process economically and environmentally sustainable, these adsorbents must be regenerable without any significant loss in SOx trapping performances along multiple adsorption-regeneration cycles. The regeneration of the sulfated adsorbent is usually performed by thermal decomposition of the metal sulfate (Eq. (3)).
SO2 + ½ O2 → SO3 | (1) |
x SO3 + MOx → M(SO4)x | (2) |
M(SO4)x → x SO3 + MOx | (3) |
Over the past decades, numerous studies dealing with SOx chemisorption using dry regenerative processes were reported in the literature [2]. As reviewed by Mathieu et al., numerous materials were tested as adsorbents including single oxides (CaO, MgO, TiO2, MnO2, CeO2, Al2O3), supported oxides on carbonaceous materials or on alumina, zeolites, clays, as well as mixed oxides, etc. [2]. Among all these material candidates, supported copper oxide has emerged as a good performer since it boasts:
- • a high catalytic activity for the oxidation of SO2 to SO3;
- • good SO3 chemisorption as CuSO4 [3–6];
- • is regenerable at a moderate temperature (600 °C) that keeps intact its textural and morphological properties and limits the energy consumption.
Nevertheless, as already observed in previous studies [3], sulfation of copper oxide is affected by diffusion effects and is mainly limited to superficial copper atoms. Thus, in view of maximizing the sulfation degree, optimizing the dispersion of copper oxide has become “the heart of the matter”. In this context, the strategy followed in the present study has consisted in dispersing copper oxide on a silica-based mesoporous support likely to ensure a high dispersion of the active phase thanks to its high surface area. Indeed, since their discovery, mesoporous silica materials have been widely employed as hosts for different metal oxides including copper oxide [7–15]. Several considerations led to select SBA-15 as support in this work. Firstly, silica is inert towards SOx which prevents the support from sulfating and the mesoporous structure from collapsing. Secondly, SBA-15 enjoys very high porous volume and surface area properties. Additionally, its pore size lies in the range of 5–10 nm and thus enables the transport of reactants such as SOx in the mesoporous channels. It has been reported that the dispersion of the active phase depends on the impregnation method [16–19], the metal precursor [19,20], the support [17,19] and the solvent used [21], as well as the drying [18,22] and calcination conditions [17,23–32]. Previous works dealing with the synthesis of supported metals or metal oxides on mesoporous silica have indicated that the growth of metal oxide particles during calcination may lead to pore plugging [16,26,29,33] and/or the migration of metal oxide outside the porous structure [16,29,31]. In this study, the dispersion of CuO on SBA-15 was investigated through different impregnation methods consisting in:
- • wet impregnation;
- • incipient wetness impregnation;
- • ion exchange.
This latter method is not really an impregnation method but rather a deposit method for addition of active phase. However in the following of the text, this spelling will be kept. The choice of these impregnation methods was done to be compatible with a potential industrial application. The influence of the solvent, as well as the drying and calcination conditions was also studied. The resulting adsorbents were characterized by nitrogen physisorption, X-Ray Diffraction (XRD), X-ray Fluorescence (XRF), Scanning (SEM) and Transmission Electron Microscopy (TEM). The SOx storage capacity of the adsorbents was determined using a fixed bed reactor using a Gas Hourly Space Velocity (GHSV) as high as 25,000 h−1, to be representative of gas turbine applications that are characterized by high flue gas flow rates.
2 Experimental part
2.1 Synthesis of SBA-15
The SBA-15 mesoporous silica was synthesized as follows: 210 g of pluronic 123 (Sigma-Aldrich) were dissolved in a solution containing 1000 mL of HCl (37%, Sigma-Aldrich) and 6600 mL of distilled water, at 55 °C in a 10 L container. After complete dissolution, 450 g of tetraethylorthosilicate (Sigma-Aldrich) were added and the solution was kept under stirring for 24 h at 55 °C. The temperature was then increased until 90 °C for 24 h. The precipitate obtained was filtered, washed with distilled water, dried at 90 °C overnight and calcined at 300 °C for 6 h (ramp of 1 °C·min−1) in order to remove the organic template.
2.2 Preparation of the CuO/SBA-15 adsorbents
Three impregnation methods consisting in Wet Impregnation (WI), Incipient Wetness Impregnation (IWI) and Ion Exchange (IE) were investigated. For the WI method, two solvents (water or methanol) were used. Methanol has been used as a solvent since its polar character allows a good solubility of copper nitrate and its low boiling point (65 °C) makes its evaporation fast and easy at ambient pressure. For each impregnation method, several drying and calcination conditions were evaluated. The drying step lasted 24 h and was performed:
- • at room temperature;
- • in an oven at 45 °C or 90 °C or;
- • by lyophilization.
Two calcination (in muffle furnace) conditions were used: the “ramp calcination” consisted in heating the sample at 500 °C for 6 h after a ramp of 1 °C·min−1; the “flash calcination” consisted in introducing and keeping for 6 h the sample in a furnace preheated at 500 °C.
2.2.1 Preparation of CuO/SBA-15 by Wet Impregnation in methanol (WIm) or water (WIw)
The impregnation was performed by dissolving 622 mg of Cu(NO3)2.3H2O (Sigma-Aldrich) in a beaker containing 60 mL of (i) methanol (Sigma-Aldrich) or (ii) water. 1.0 g of calcined SBA-15 was added to this solution and the mixture was stirred at room temperature for 2 h. The methanol-based solution was then introduced in a bath at 60 °C under stirring until the methanol was completely evaporated. The water based solution was evaporated in 2 h using a rotary evaporator at 30 °C under reduced pressure (20 mbar). Both resulting powders were dried and calcined to obtain copper oxide.
2.2.2 Preparation of CuO/SBA-15 by Incipient Wetness Impregnation in water (IWIw)
The general IWI consists in impregnating the porous material with a volume of a precursor-laden solution which corresponds exactly to its porous volume previously determined by N2 physisorption. This general procedure was slightly modified, the volume of the solution being twice the one of the porous volume of the SBA-15 in order to impregnate both internal and external surfaces. Thus, 610 mg of Cu(NO3)2.3H2O were dissolved in 2.4 mL of distillated water and put in contact with 1.0 g of calcined SBA-15 (porous volume of 1.2 g·cm−3). The resulting powder was dried and calcined yielding the CuO/SBA-15 adsorbent.
2.2.3 Preparation of CuO/SBA-15 by Ion Exchange (IE)
The adsorbents obtained by IE were prepared as follows: 800 mg of Cu(NO3)2.3H2O were dissolved in 25 mL of distillated water and the pH was adjusted to 10.5 by adding a 30 wt. % of ammonia solution. The solution was then cooled at 0 °C in an ice/water bath in order to limit the hydrolysis of silica. Then 1.0 g of calcined SBA-15 was added to the solution and the mixture was kept for 30 min at 0 °C under stirring. The solid was then recovered by filtration, washed two times for 30 min in 30 mL of distillated water, dried and calcined.
2.3 Samples nomenclature
In this work, samples are named according to: (i) their Impregnation Method (IM), (ii) the solvent used (s), (iii) the drying conditions (dc) and (iv) the calcination procedure (cp), resulting in the following notation: “IMs-dc-cp”. In the case of wet impregnation, the samples impregnated with methanol are designated by the prefix “WIm” and those impregnated with water by “WIw”. The samples designation further includes an infix which is: “no” for undried samples; “20”, “45”, “90” and “lyo” for the samples dried at 20 °C, 45 °C, 90 °C and by lyophilization, respectively. The two calcination procedures are distinguished by a suffix which is “r” (ramp calcination) or “f” (flash calcination). As an example, the sample obtained by wet impregnation in methanol, dried at 45 °C and calcined with a ramp is named “WIm-45-r”.
2.4 Characterization techniques
X-Ray powder Diffraction (XRD) patterns were obtained in the reflection mode with a PANalytical X’Pert diffractometer (Cu Kα radiation, λ = 1.5418 Å) equipped with a X’Celerator detector. Measurements were achieved for 2θ angles in the 3–70° range, by step of 0.02° (220 s by step). The same diffractometer was used to record the XRD patterns at low angles (2θ range: 0.5–3°). In that case, a glass support was used as sample holder. Transmission Electron Microscopy (TEM) micrographs were taken with a Philips CM200 microscope equipped with a LaB6 filament. The accelerating voltage was 200 kV. Samples were previously dispersed in water and sonicated during 10 min. Then five to ten drops of the solution were deposited onto Cu grids coated with a thin (5 nm thickness) holey carbon support film. Copper analyses were performed using a X-Ray Fluorescence (XRF) spectrometer (Philips MagiX) on samples compacted in 13 mm diameter pellets. Nitrogen physisorption were carried out on a Micromeritics Tristar apparatus. Prior to the measurements, the samples were outgassed at 150 °C for 15 h under primary vacuum. Specific surface areas and pore size distributions were determined by the BET and BJH methods respectively. Scanning Electron Microscopy (SEM) micrographs were obtained with a Philips XL 30 FEG microscope. Cu X-ray mappings were obtained from the EDX analyzer Oxford Inca Si(Li) integrated in the same microscope.
2.5 SO2 adsorption tests
The SO2 adsorption tests were performed in a fixed bed reactor. The CuO/SBA adsorbents were previously pelletized (2 min at 0.25 ton·cm−2), crushed and sieved to retain the 225–450 μm portion. Samples were introduced in a vertical quartz reactor (6 mm inner diameter) fitted with a fused silica layer. The adsorption experiments were performed at 400 °C using a gas mixture containing 250 ppm of SO2 and 10 vol. % of O2 in nitrogen. The gas flow rate equalling 13 NL·h−1, was adjusted by BROOKS 5850 mass flow controllers. The height of the adsorbent bed in the reactor was set at 2 cm in order to reach the high GHSV value of 25,000 h−1 which is representative of gas turbine exhaust conditions. The SO2 outlet concentration was continuously measured by an UV absorption analyzer (Rosemount NGA 2000; range: 0–1000 ppm). The accuracy of the measurements, given by the manufacturer, is better than 1% of full scale. Before the SO2 adsorption phase, the adsorbent was heated from 25 to 400 °C at a 5 °C·min−1 rate under pure N2 and the temperature was maintained at 400 °C during 1 h. The dynamic SO2 adsorption capacity (Cads) expressed in mg of SO2 per gram of adsorbent (adsorbent = active phase + support SBA-15) () was calculated by integration of the SO2 breakthrough curve until the SO2 concentration reaches the 75 ppm (vol.) threshold value at the outlet of the reactor. This value has been chosen in order to match the SOx emission limit enacted by the European legislation. The calculation is performed as follows:
3 Results
3.1 Wet Impregnation in methanol (WIm)
The chemical composition, color, textural properties and SO2 uptake capacities of the adsorbents obtained by Wet Impregnation in methanol (WIm) are given in Table 1. Methanol has been used as a solvent since its polar character allows a good solubility of copper nitrate and its low boiling point (65 °C) makes its evaporation fast and easy at ambient pressure.
Synthesis conditions, textural properties, chemical composition and SO2 uptake capacities of the adsorbents prepared by Wet Impregnation in methanol (WIm).
Sample | SBA-15 | WIm-no-r | WIm-no-f | WIm-20-r | WIm-45-r | WIm-45-f | WIm-90-r | WIm-lyo-r | WIm-lyo-f |
Drying (24 h) | – | No | No | 20 °C | 45 °C | 45 °C | 90 °C | Lyoph. | Lyoph. |
Calcination | Ramp | Ramp | Flash | Ramp | Ramp | Flash | Ramp | Ramp | Flash |
Color | White | Green-grey | Green + blue | Green | Green | Green + blue | Dark blue + green | Green + blue | Green |
CuO content (wt. %) | 0 | – | – | 17.4 | 18.2 | 17.9 | – | – | – |
SBET (m2·g−1) | 938 | 591 | 625 | 554 | 553 | 591 | 556 | 576 | 637 |
Vp (cm3·g−1) | 1.2 | 0.8 | 0.8 | 0.7 | 0.7 | 0.8 | 0.7 | 0.8 | 0.8 |
Pore size (nm) | 7.5 | 7.6 | 7.7 | 7.7 | 7.5 | 7.6 | 7.5 | 7.6 | 7.7 |
SO2 uptake () | / | 15 | 27 | 9 | 12 | 30 | 2 | 15 | 27 |
All samples have a copper oxide loading around 17–18 wt. %. Five distinct drying conditions (no drying, drying at 20 °C, 45 °C, 90 °C and lyophilization) and two calcination conditions (ramp and flash) are compared.
It can be observed that the color of the obtained adsorbents is closely related to the drying and calcination conditions. It is noteworthy that samples WIm-no-f, WIm-45-f, WIm-90-r and WIm-lyo-r are heterogeneous as they present some green and blue areas in the crucible after calcination. This suggests that different copper species are formed during the impregnation, drying and calcination steps. Indeed, XRD analysis (not reported here) of the blue particles reveals the presence of crystalline CuO phase (PDF4+ 00-005-0661) while for the green ones, no peaks are observed suggesting either the formation of a very thin CuO film as reported by Tian et al. [34] or the presence of copper species in strong interaction with the support, e.g., Cu–O–Si species [25,35]. Since all SBA-15 samples were impregnated under stirring and further homogenized by crushing before the drying and calcination steps, this heterogeneity must come from the drying and/or calcination steps. After a number of tests of drying and calcination, we observed that when the powder is laid as a fine, homogeneous layered in the calcination vessel, the resulting adsorbent is generally homogenous. In contrast, when the impregnated material is laid as a thick layer, heterogeneous samples are preferentially formed. A similar phenomenon was observed by Sun et al. [32] who reported the strong effect of that they called “container effect” by comparing the adsorbents obtained by calcination of mesoporous silica (KIT-6) impregnated with metal nitrate precursor, in closed or open reactors. They observed that in a closed reactor, the formation of large metal oxide particles was favored. This effect was attributed to the slow escape rate of the hydration water vapor and decomposition gases (NO, NO2, O2) of the nitrate precursor. Indeed, these gases (H2O, NO, NO2, O2) were reported to significantly increase the size of the metal oxide particles by accelerating their sintering [23,24,26,29,32]. Except for the lyophilized samples, the flash calcination tends to lead to the formation of heterogeneous materials (with and without drying at 45 °C: WIm-no-f and WIm-45-f, respectively). On the contrary the calcination with a ramp seems to favor homogenous materials (WIm-no-r, WIm-20-r, WIm-45-r), except for the adsorbents dried by lyophilization (WIm-lyo-r) and at 90 °C (WIm-90-r). For the latter, the predominant dark blue color suggests the formation of substantial amount of large CuO particles as confirmed by the corresponding XRD pattern that show the most intense CuO peaks (Fig. 1). Indeed, it was reported that the drying at “high temperature” (∼ 100 °C) favors the formation of large CuO crystallites compared to the drying at 25 °C [18,25]. This effect might be assigned to the formation of nitrate hydroxide (Cu2(OH)3(NO3)) which tends to concentrate in the wet spots that remain during the last vaporization stages, resulting in large CuO particles after calcination. In contrast, for the sample dried at 25 °C, a green color and no diffraction peaks are observed [18].
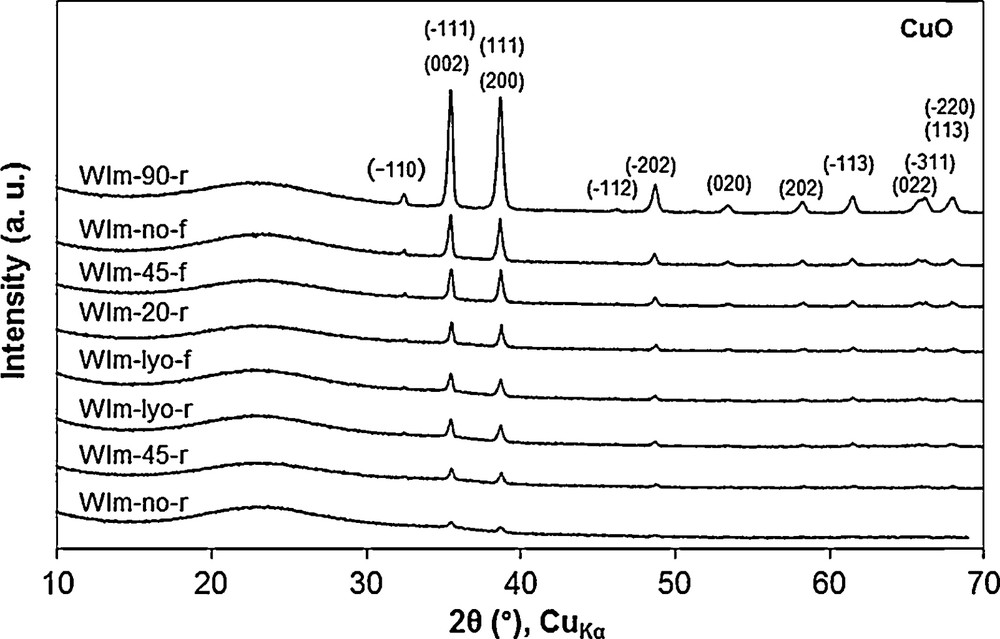
XRD patterns of CuO/SBA-15 adsorbents prepared by Wet Impregnation in methanol (WIm). For a better visibility, the diffraction patterns are shifted along the Y-axis.
It can be noticed that although the copper loading is in the same order of magnitude for all samples, there are strong differences in the peak intensity. Moreover, similarly to the results of Munnik et al. [25], peak broadening is observed for none of samples. This result suggests a bimodal distribution of the copper species which seems to form either large crystalline CuO particles (detected by XRD) or XRD-undetected copper species. As discussed below, the SEM micrographs and X-ray mappings suggest that the undetected copper species are very homogeneously dispersed on the mesoporous support. The samples dried in different conditions and calcined with a ramp show the smaller XRD peak intensities with the ranking: WIm-no-r < WIm-45-r < WIm-lyo-r < WIm-20-r. The sample WIm-lyo-f shows comparably low peak intensities although it was obtained by flash calcination. The other adsorbents obtained by flash calcination (WIm-no-f and WIm-45-f) show intense CuO peaks. As discussed above, the highest intensity is observed for the sample WIm-90-r which has been dried at 90 °C. In summary, as a general trend, the combination of a calcination step with a ramp and a low drying temperature step (especially the drying by lyophilization) seems to favor the formation of undetected copper species rather than large CuO particles.
The nitrogen physisorption isotherms of the SBA-15 adsorbent and those of representative sorbents obtained for each impregnation method (WIm, WIw, IWIw, and IEw) are reported in the Fig. 2. The isotherms of the SBA-15 shows parallel adsorption and desorption branches and a well-defined hysteresis loop in the relative pressure range p/p0 = 0.7–0.8. It corresponds to the type IV according to the IUPAC classification and is characteristic of mesoporous material with well-ordered cylindrical pores [36]. As it will be discussed below, the shape of the adsorption-desorption branches of the adsorbents differs in function of the impregnation method. However, given an impregnation method, whatever the drying or calcination treatment, the samples display similar isotherms (for the sake of concision, this result is not illustrated by a figure). The N2 isotherms corresponding to the adsorbent WIm-lyo-r reported in Fig. 2 suggest that the mesoporous structure of SBA-15 is not altered by the WIm method. The pore volumes and specific surface areas are indicated in Table 1. As expected, the pore volumes of the CuO/SBA-15 adsorbents (0.7 to 0.8 cm3·g−1) are smaller than that of the SBA-15 calcined at 500 °C (1.2 cm3·g−1); this is mainly attributed to the densification of the mesoporous support due to the incorporation of copper oxide. A partial pore plugging of the mesoporous support by CuO particles is also possible and also could explain this pore shrinkage effect. The same trend is observed for the specific surface areas that range from 553 to 637 m2·g−1 for the CuO/SBA-15 versus 938 m2·g−1 for unloaded SBA-15. However, the incorporation of copper does not influence significantly the pore size distribution (determined by applying the BJH method on the desorption branch) which is centered between 7.5 and 7.7 nm for all samples, including the non-impregnated adsorbent. When comparing the CuO/SBA-15 adsorbents, it is noteworthy that the flash-calcined samples exhibit slightly higher specific BET surface areas (590 to 640 m2·g−1) as compared to those calcined with a ramp (553 to 591 m2·g−1). In contrast, the preparation method does not significantly impact on the pore volume which ranges between 0.7 and 0.8 cm3·g−1 for all samples.
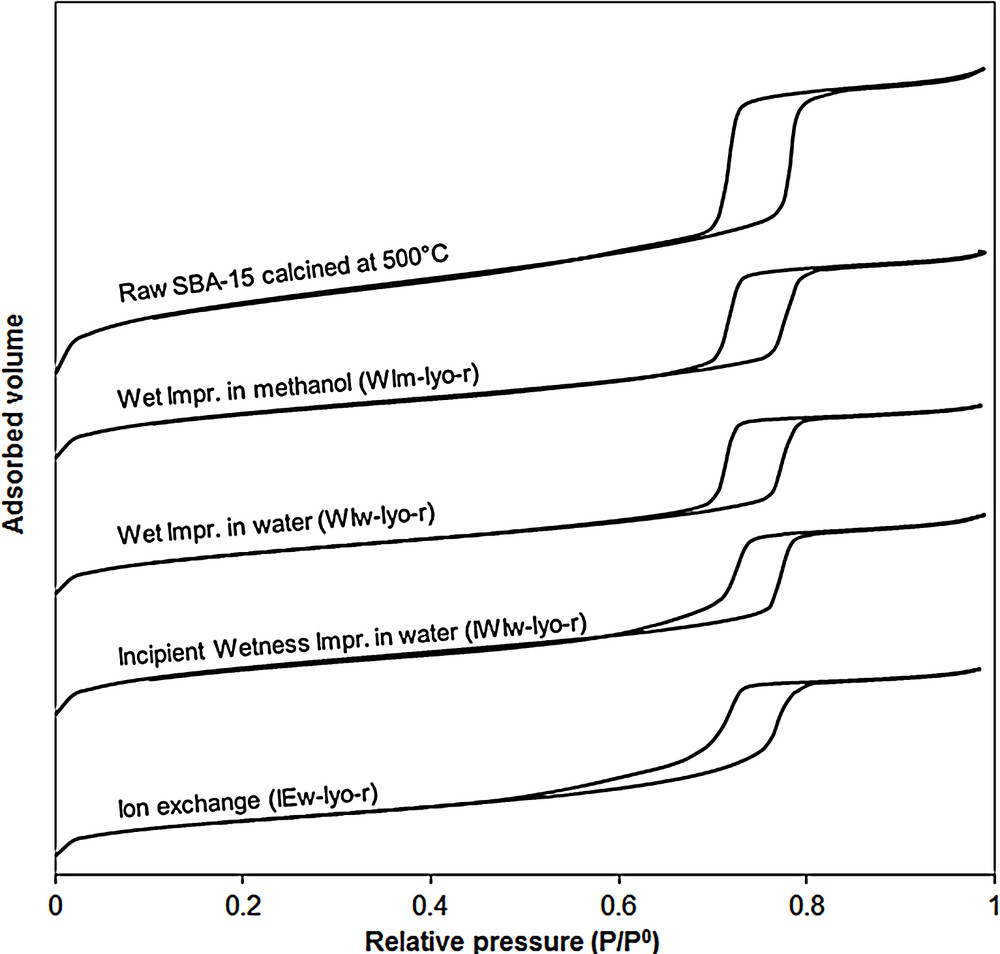
Nitrogen adsorption-desorption isotherms of raw SBA-15 and CuO/SBA-15 adsorbents obtained by: Wet Impregnation in methanol (WIm-lyo-r) or in water (WIw-lyo-r); Incipient Wetness Impregnation in water (IWIw-lyo-r) and Ion Exchange in water (IEw-lyo-r). For a better visibility, the isotherms are shifted along the Y-axis.
The SEM micrographs and the corresponding X-ray mappings of samples WIm-90-r, WIm-no-r and WIm-no-f are shown in Fig. 3. As expected from the XRD pattern (Fig. 1), the X-ray mapping (EDX) of WIm-90-r (Fig. 3B) shows copper mainly distributed in large CuO particles that are also visible on the corresponding micrograph (Fig. 3A). On the contrary, no large CuO particles are detected for the sample WIm-no-r (Fig. 3C) and the corresponding X-ray mapping (Fig. 3D) shows instead a homogeneous distribution of copper species on the support. This result fits well with the XRD patterns that exhibit very weak CuO peaks for this adsorbent (Fig. 1). The X-ray mapping (Fig. 3F) of the adsorbent WIm-no-f shows large CuO particles similar to those of WIm-90-r but a greater fraction of copper remains homogeneously dispersed on the support. This is also in agreement with the corresponding XRD patterns of Fig. 1.
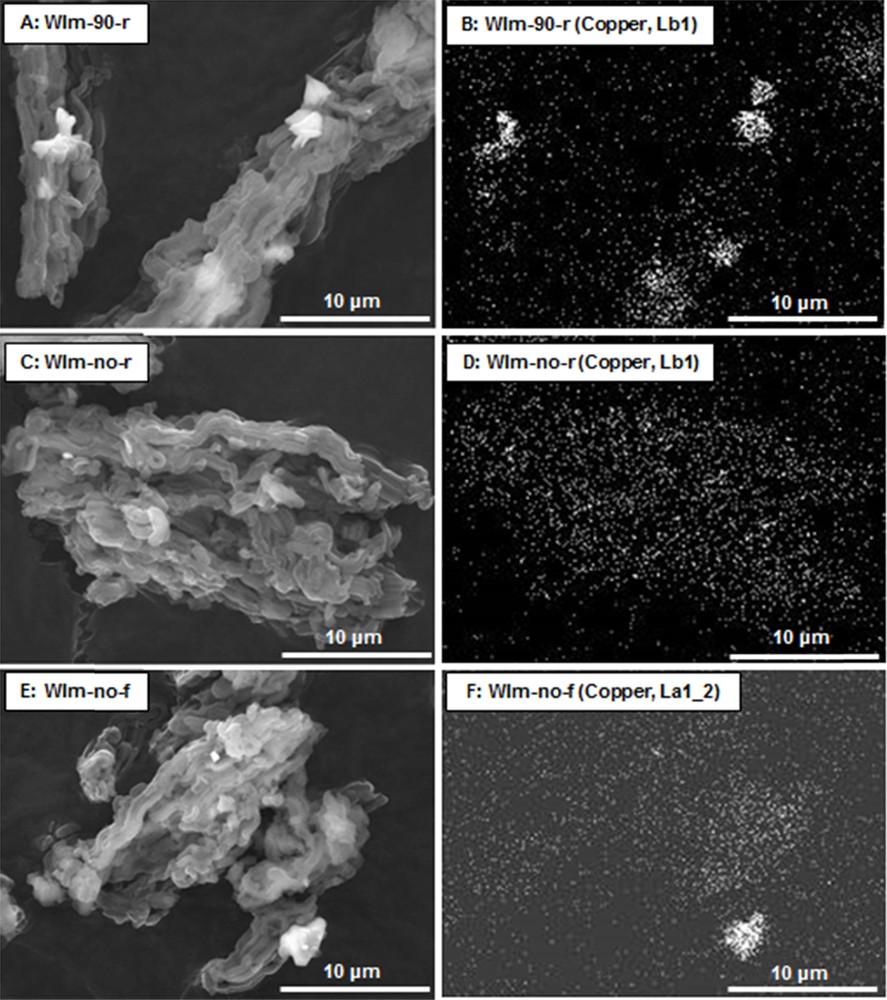
SEM micrographs (A, C and E) and corresponding X-ray mappings of copper (B, D and F) of samples WIm-90-r, WIm-no-r and WIm-no-f, respectively.
The TEM micrographs of samples WIm-90-r, WIm-no-r, WIm-no-f, WIm-lyo-r, WIm-lyo-f are reported in Fig. 4. In accordance with the XRD, SEM and X-ray mapping analyses, large CuO crystallites (∼ 2 μm), are evidenced for the sample WIm-90-r (Fig. 4A). These particles are found outside the pores while the porous structure of the SBA-15 support is fairly conserved after the impregnation, drying and calcination steps (Fig. 4B). This is in accordance with the adsorption-desorption isotherms (Fig. 2). The micrographs C–J (Fig. 4) of the other samples confirm the conservation of the porous structure of the support but do not reveal the presence of copper particles, suggesting the formation of either a thin, homogeneously dispersed CuO film or superficial Cu–O–Si species, as discussed above.
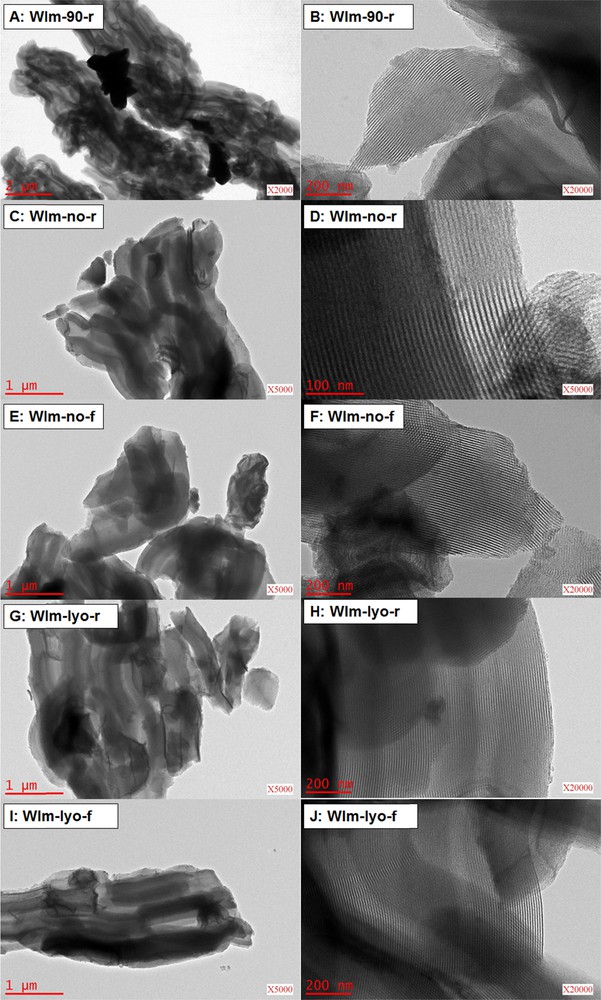
(Color online.) TEM micrographs of samples WIm-90-r (A and B), WIm-no-r (C and D), WIm-no-f (E and F), WIm-lyo-r (G and H) and WIm-lyo-f (I and J), obtained by Wet Impregnation in methanol (WIm).
The SO2 adsorption performances of the adsorbents impregnated by WI using methanol were evaluated. The SO2 breakthrough curves of samples WIm-90-r, WIm-lyo-r and WIm-lyo-f are shown for example in Fig. 5, the SO2 uptake capacities of all adsorbents being summarized in Table 1.
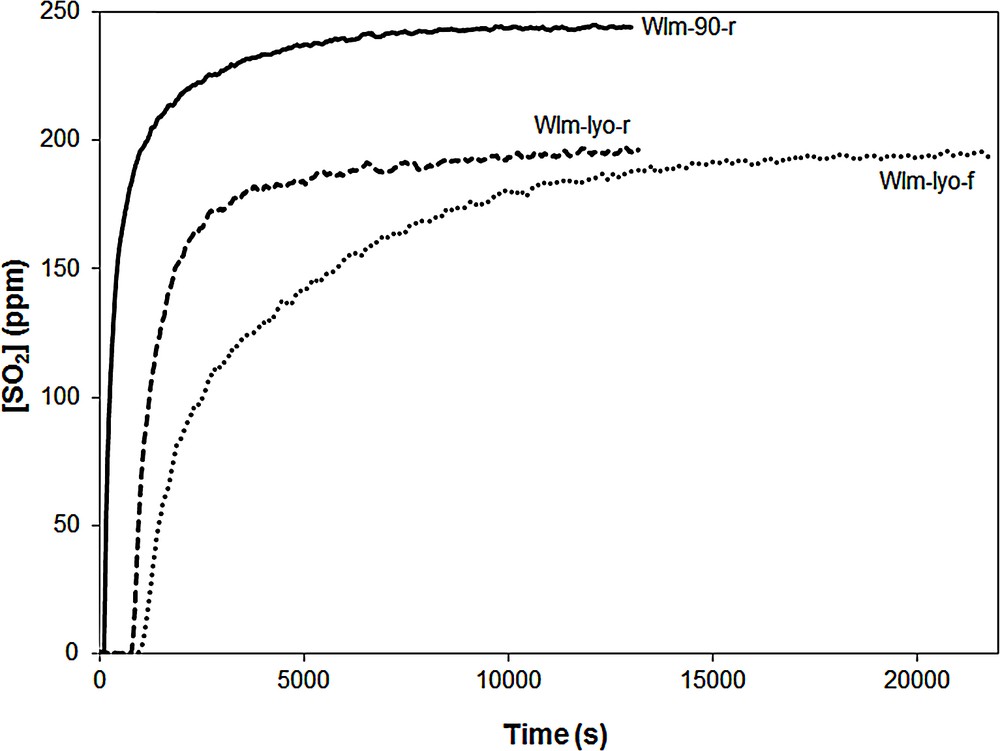
SO2 Breakthrough curves of samples WIm-90-r, WIm-lyo-r and WIm-lyo-f.
The SOx saturation of the WIm-90-r sample occurs very quickly meaning a small SO2 adsorption capacity (), which can be attributed reasonably to the formation of large CuO particles as shown above. Indeed Centi et al. have observed that sulfation of pure CuO occurs very slowly and they assumed that there is a rapid formation of superficial sulfate species, which, because of the higher cell volume of CuSO4 compared to that of CuO, slow down the formation of subsurface sulfate species [3]. The adsorbents WIm-lyo-r and WIm-lyo-f exhibit a significantly higher SO2 uptake capacity with SO2 adsorption curves showing similar breakthroughs, at around 800 s, but different shapes. Indeed, the SO2 saturation profile of the WIm-lyo-r adsorbent is sharper than that of the WIm-lyo-f, suggesting that the chemisorption of SO2 in the latter suffers from kinetic limitations. At [SO2]out = 75 ppm, the measured SO2 uptake capacity of WIm-lyo-f is higher than that of WIm-lyo-r ( versus ). Fig. 5 shows that, at the saturation of the three adsorbents, the SO2 concentration at the outlet of the reactor is around 200–240 ppm of SO2 whereas the concentration of injected SO2 is 250 ppm. This means that a fraction of the injected SO2 is still oxidized by the adsorbent, yielding SO3 which is not detected by the UV analyzer.
From Table 1, it appears that the adsorbents that underwent a flash calcination, WIm-no-f, WIm-45-f and WIm-lyo-f are surprisingly the most efficient ones, with SO2 uptake capacities of 27, 30 and , respectively, although they show fairly high XRD peaks of copper oxide (Fig. 1). The adsorbents calcined with a ramp of temperature exhibit the lower SO2 chemisorption capacities. Therefore, it is rather difficult to correlate the SO2 uptake capacities with the XRD patterns. In summary, the overall set of investigations suggests that copper exhibits a bimodal distribution consisting on one hand in large CuO particles and on the other hand, in homogeneously dispersed XRD-undetected copper species. The predominance of one kind of species over the other seems to be closely related to the drying and calcination steps. According to the work of Centi et al. and in agreement with results obtained in this work for sample WIm-90-r, it seems reasonable to assume that large crystalline CuO particles are poorly active in the DeSOx reaction and the efficiency of the adsorbent is mainly due to the undetected copper species. According to the SO2 uptake capacity data reported in Table 1, it seems that the flash calcination enhances the formation of efficient copper species for the DeSOx reaction.
3.2 Wet Impregnation in water (WIw)
In order to evaluate the influence of the solvent, the same batch of SBA-15 was impregnated following the same protocol but using water instead of methanol according to the WIw protocol. The characterization of the resulting adsorbents is summarized in Table 2 that aims at comparing two distinct drying methods (no drying and lyophilization) and two calcination methods (ramp and flash).
Synthesis conditions, textural properties, chemical composition and SO2 uptake capacities of the adsorbents prepared by Wet Impregnation in water (WIw).
Sample | WIw-no-r | WIw-no-f | WIw-lyo-r | WIw-lyo-f |
Drying (24 h) | No | No | Lyoph. | Lyoph. |
Calcination | Ramp | Flash | Ramp | Flash |
Color | Grey-green | Green + blue | Green | Green + blue |
CuO content (wt. %) | 18.0 | 18.2 | 18.3 | 17.7 |
SBET (m2·g−1) | 509 | 485 | 502 | 520 |
Vp (cm3·g−1) | 0.7 | 0.7 | 0.7 | 0.7 |
Pore size (nm) | 7.6 | 7.6 | 7.5 | 7.6 |
SO2 uptake () | 49 | 27 | 13 | 18 |
The four samples have a copper loading close to 18 wt. %. Observations similar to the case of impregnation with methanol can be made in terms of sample heterogeneity, XRD patterns (Fig. 6) and inferable CuO dispersion status.
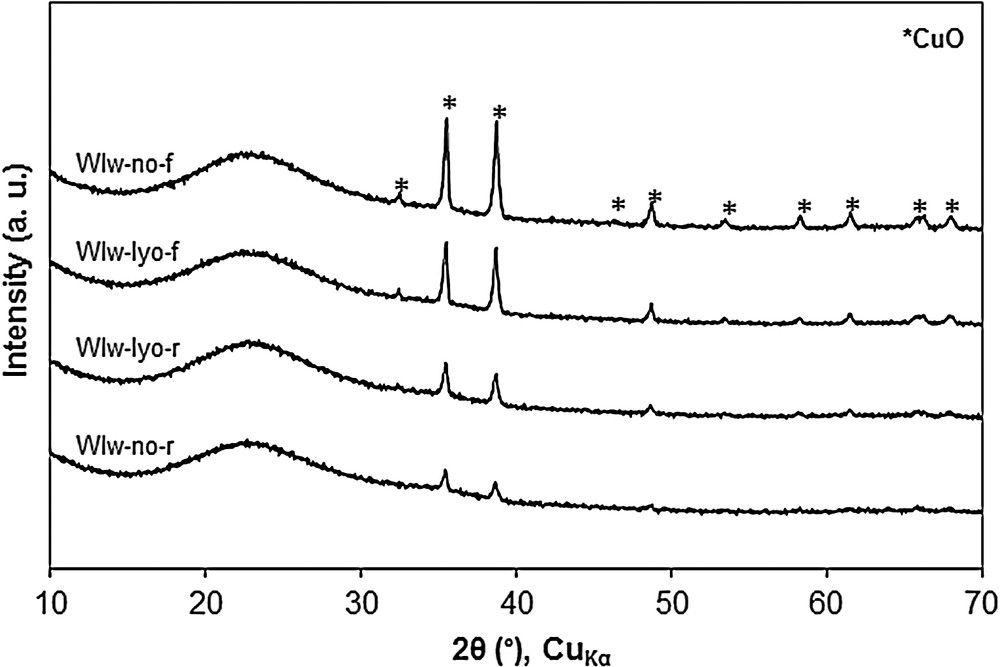
XRD patterns of CuO/SBA-15 samples prepared by Wet Impregnation in water (WIw). For a better visibility, the diffraction patterns are shifted along the Y-axis.
Here also, the shape of the N2 physisorption isotherms of the adsorbent WIw-lyo-r (Fig. 2) is similar to that of the original SBA-15, suggesting the absence of alterations caused by the solvent on the mesoporous structure. The pore size distributions (7.5–7.6 nm) and pore volumes (0.7 cm3·g−1) reported in Table 2 are close to those reported for the WIm samples but the specific surface areas of the WIw samples are this time much less dependent from the synthesis procedure. The SEM micrographs of samples WIw-no-r, WIw-no-f and WIw-lyo-r and their corresponding X-ray mappings are reported in Fig. 7. For the adsorbents calcined with a ramp, i.e. WIw-no-r (Fig. 7 A and B) and WIw-lyo-r (Fig. 7 E and F), the copper seems to be mainly homogeneously distributed with no detected large CuO particles, which is in good agreement with the weak intensity of the CuO peaks of the corresponding XRD patterns (Fig. 6). On the contrary, the WIw-no-f adsorbent (Fig. 7C and D) exhibits a fraction of copper that is homogeneously dispersed on the support; one sees also large (∼ 1 μm) CuO particles, as expected from the intense signal observed on the XRD pattern.
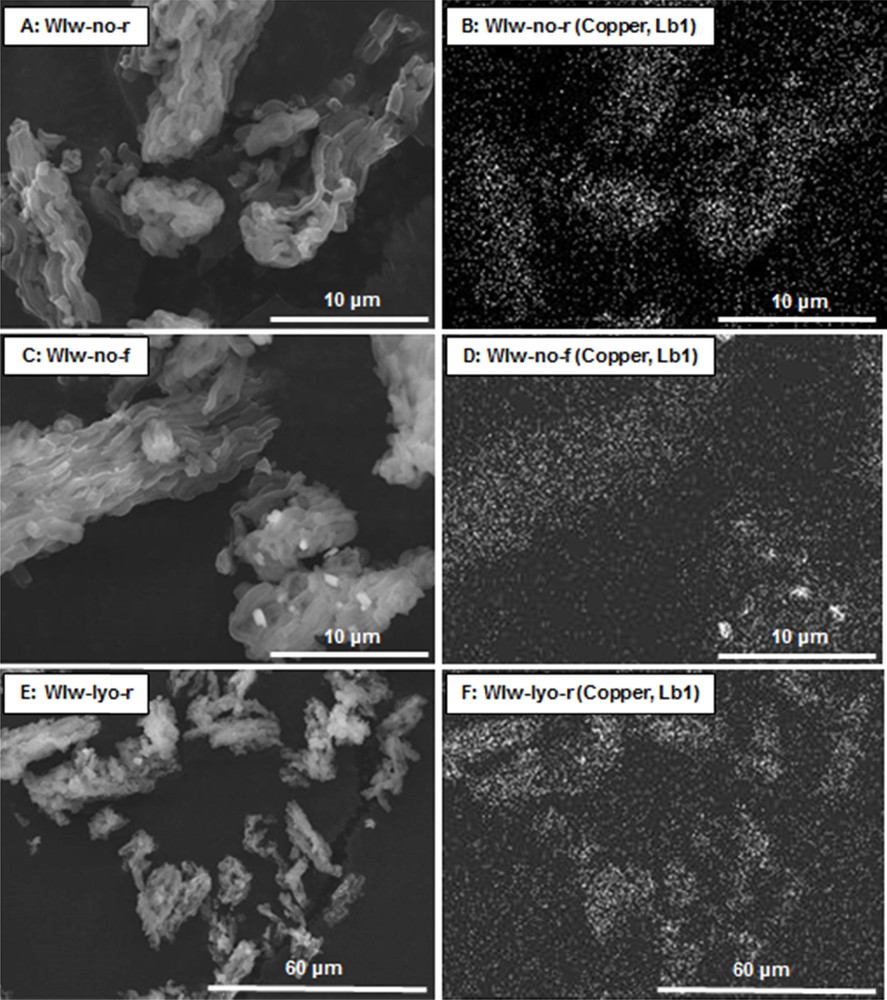
SEM micrographs (A, C and E) and corresponding X-ray mappings (B, D and F) of samples WIw-no-r, WIw-no-f and WIw-lyo-r.
TEM micrographs of WIw-no-r (A and B), WIw-no-f (C and D) and WIw-lyo-r (E and F) are shown in Fig. 8. They do not reveal CuO particles in the porous structure. In accordance with N2 physisorption isotherms (Fig. 2), the SBA-15 support does not seem to be altered by the impregnation, drying and calcination steps. These results support the bimodal distribution of the copper species; the ratio of large CuO particles to homogeneously dispersed copper species being closely dependent on the drying and calcination conditions.
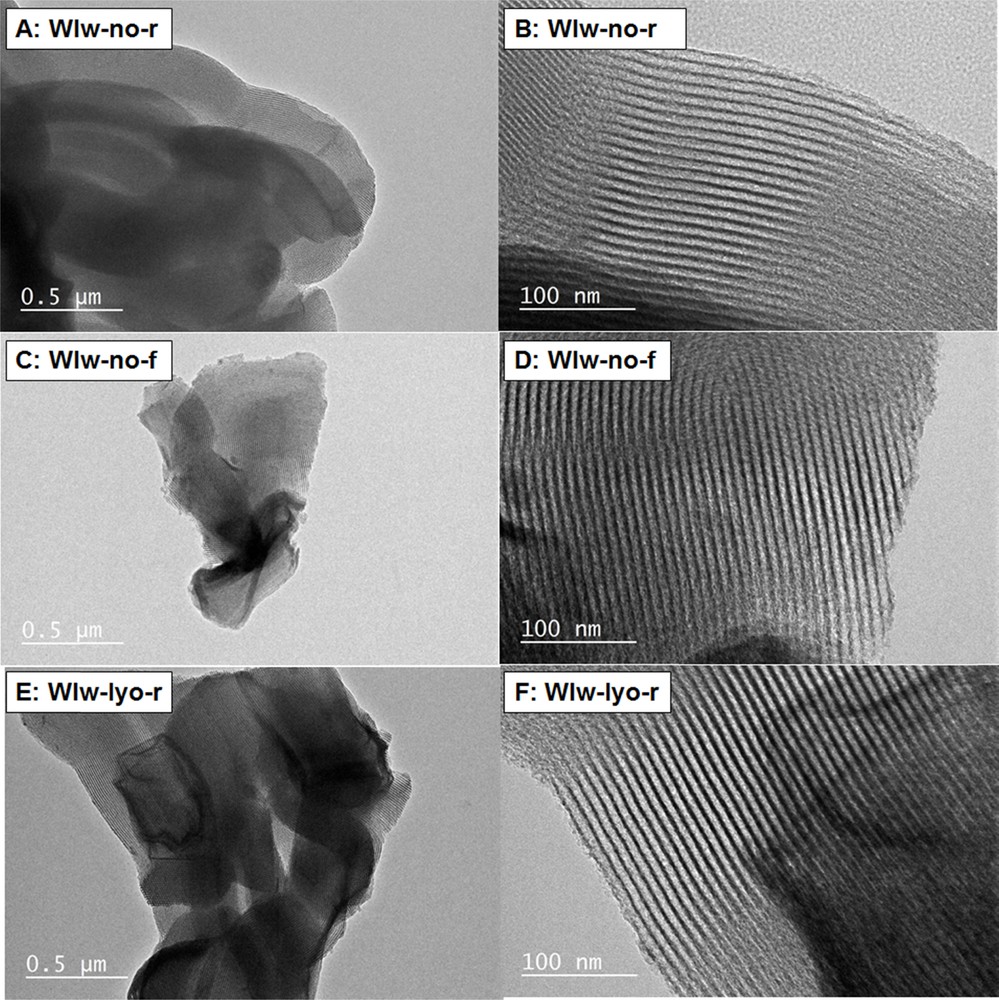
TEM micrographs of samples WIw-no-r (A and B), WIw-no-f (C and D) and WIw-lyo-r (E and F) obtained by Wet Impregnation in water (WIw).
The SO2 breakthrough curves of the CuO/SBA-15 samples impregnated in water are shown in Fig. 9.
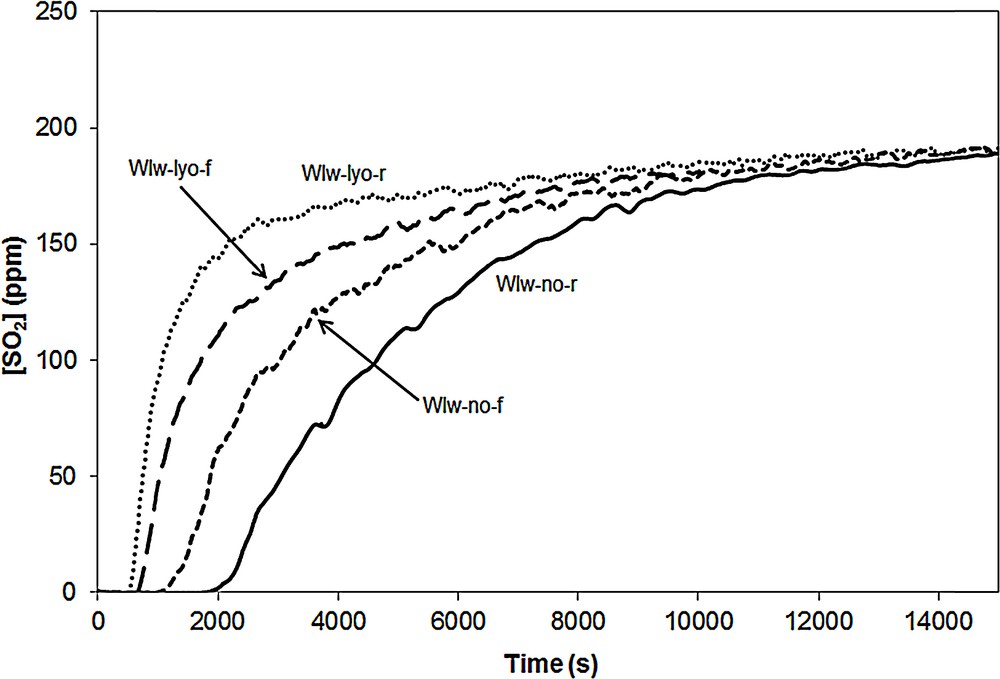
SO2 breakthrough curves of samples WIw-no-r, WIw-no-f, WIw-lyo-r and WIw-lyo-f.
The highest SO2 uptake capacities are obtained with adsorbents which were not dried before the calcination step: 49 and for WIw-no-r and WIw-no-f, respectively which accordingly have the smallest XRD diffraction peaks. The lyophilized samples (WIw-lyo-r and WIw-lyo-f) are less efficient (SOx storage capacities equal to 13 and , respectively). As mentioned for the samples impregnated in methanol, it is difficult to correlate the SOx storage capacity data of these four adsorbents with their corresponding XRD patterns. Indeed, the adsorbent having the highest XRD CuO peaks (sample WIw-no-f) displays a SOx trapping capacity () higher than that of the lyophilized adsorbents (13 and ) that display nevertheless lower XRD peaks. The efficiency of these adsorbents impregnated with water, is related to the calcination and still more to the drying steps. It seems that the presence of water adsorbed on the material before the calcination step plays a crucial role in regard to the SOx trapping efficiency. Moreover, the use of water rather than methanol as a solvent seems to favor the formation of efficient copper species for the DeSOx if one compares the SO2 uptake capacity data with water; (maximal capacity) with methanol and for the WIm-no-r sample. Here again, the results obtained with water suggest that the DeSOx efficiency is related to the nature of the XRD-undetected copper species.
3.3 Incipient Wetness Impregnation with water (IWIw)
Since the best performances have been obtained by wet impregnation with water, the IWI was also performed with water. For this series of adsorbents, three drying conditions have been compared (45 °C, 90 °C and lyophilization) with the two calcination methods (ramp and flash). All adsorbents have a copper oxide loading in the range of 15–18 wt. % (Table 3).
Synthesis conditions, textural properties, chemical composition and SO2 uptake capacities of the adsorbents prepared by Incipient Wetness Impregnation with water (IWIw).
Sample | IWIw-45-r | IWIw-90-r | IWIw-lyo-r | IWIw-lyo-f |
Drying (24 h) | 45 °C | 90 °C | Lyoph. | Lyoph. |
Calcination | Ramp | Ramp | Ramp | Flash |
Color | Green + blue | Dark blue | Blue + green | Green + blue |
CuO content (wt. %) | 17.3 | 16.0 | 15.3 | 17.6 |
SBET (m2·g−1) | 532 | 552 | 634 | 518 |
Vp (cm3·g−1) | 0.7 | 0.7 | 0.8 | 0.7 |
Pore size (nm) | 7.4 | 7.5 | 7.7 | 7.4 |
SO2 uptake () | 13 | 4 | 8 | 24 |
As for the sample WIm-90-r obtained by wet impregnation in methanol and dried at 90 °C, the adsorbent IWIw-90-r presents a dark blue color and the XRD pattern exhibits peaks of strong intensity (Fig. 10). This adsorbent is also inefficient for DeSOx. In contrast with the wet impregnation method, the adsorbents calcined with the ramp calcination (IWIw-lyo-r and IWIw-45-r) are heterogeneous in color. Moreover, according to the XRD patterns, it seems that the flash calcination (sample IWIw-lyo-f) limits the formation of large CuO particles (Fig. 10).
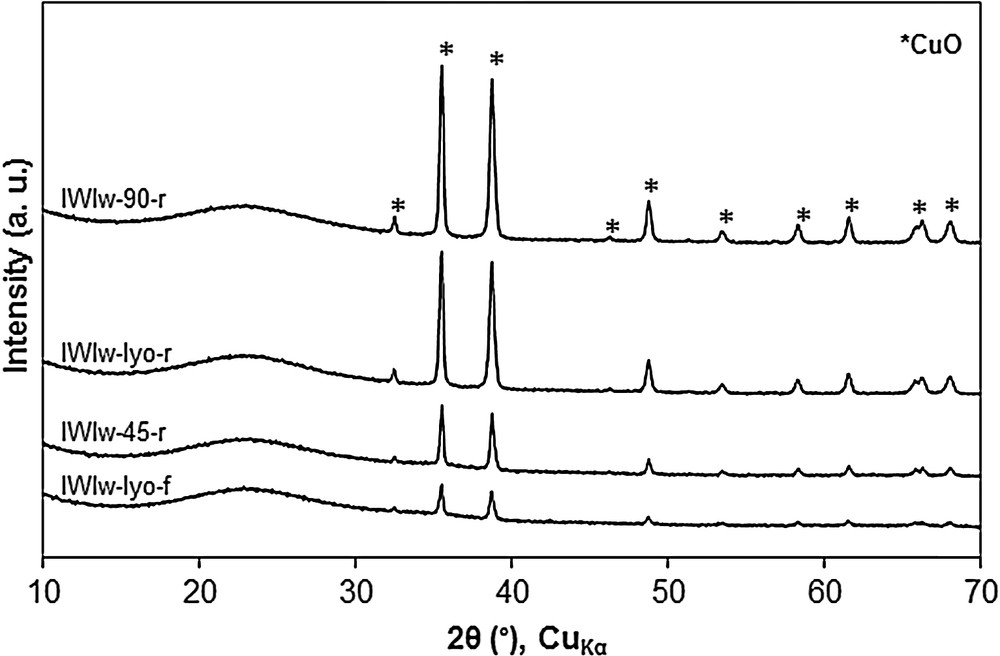
XRD patterns of CuO/SBA-15 adsorbents prepared by Incipient Wetness Impregnation with water (IWIw). For a better visibility, the diffraction patterns are shifted along the Y-axis.
The N2 physisorption isotherms of the IWIw-lyo-r are reported in Fig. 2. It can be seen that the desorption branch is slightly shifted towards higher pressures, an effect usually attributed to cavitation phenomena resulting from pore blocking [37–40]. This phenomenon might be due to the formation of CuO particles in the channels of the SBA-15 structure. Nevertheless, TEM micrographs (Fig. 12) do not evidence the presence of such particles. The pore volumes and BET specific surface areas of the adsorbents prepared by the IWI are similar to those obtained with the wet impregnation method.
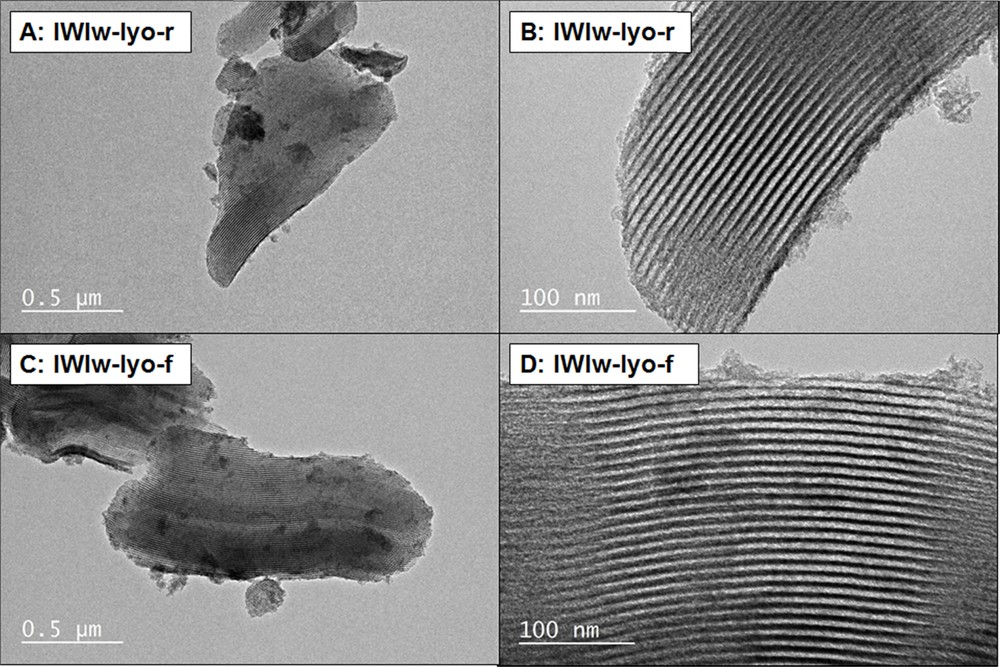
TEM micrographs of samples IWIw-lyo-r (A and B) and IWIw-lyo-f (C and D) obtained by Incipient Wetness Impregnation in water (IWIw).
The SEM micrographs and the corresponding X-ray mappings of samples IWIw-90-r, IWIw-lyo-r and IWIw-lyo-f are reported in Fig. 11. Similarly to the trend observed above for the sample WIm-90-r, the X-ray mapping of the adsorbent IWIw-90-r (micrograph B) evidences the formation of large CuO particles which is attributed to the drying at “high temperature” (90 °C). The X-ray mappings of samples IWIw-lyo-r (Fig. 11D) and IWIw-lyo-f (Fig. 11F) show the formation of large CuO particles in the former while the latter exhibits a homogenous distribution of copper. This result is also in good agreement with the XRD patterns since the IWIw-lyo-r sample exhibits a higher CuO peak intensity (Fig. 10).
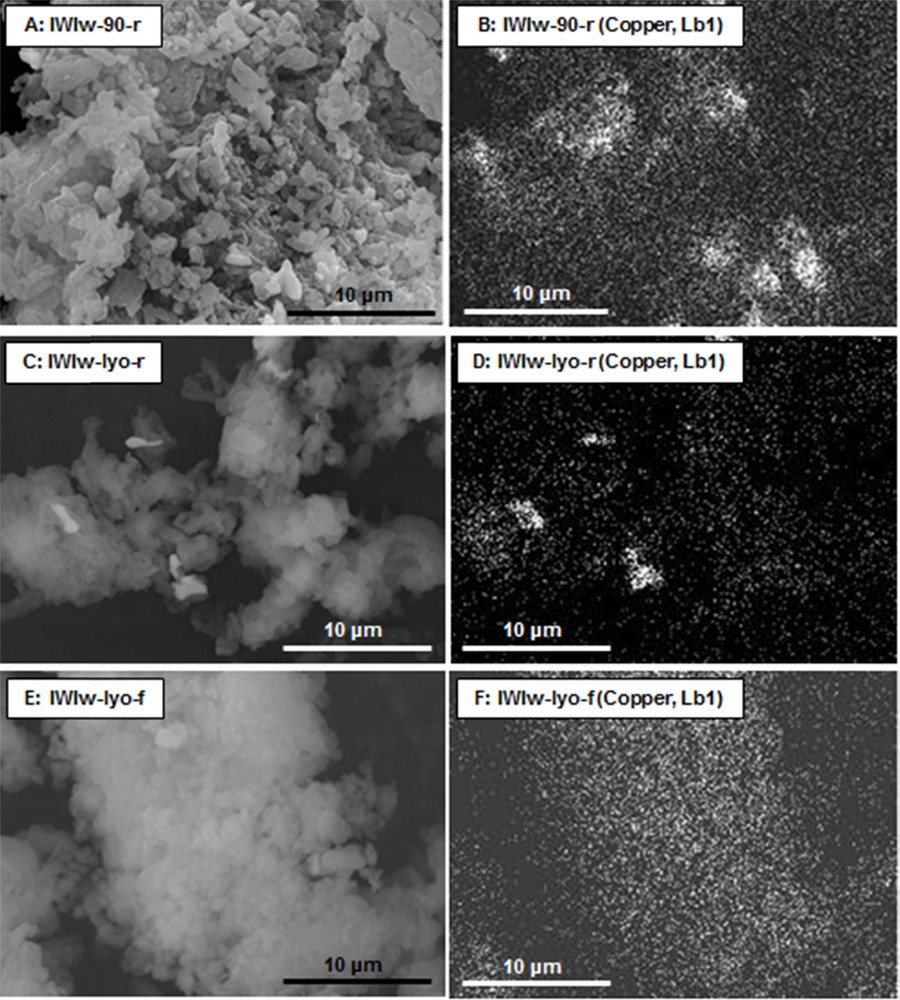
SEM micrographs (A, C and E) and corresponding X-ray mappings (B, D and F) of samples IWIw-90-r, IWIw-lyo-r and IWIw-lyo-f.
Similarly to the preceding results, the TEM micrographs of samples IWIw-lyo-r (A and B) and IWIw-lyo-f (C and D) shown in Fig. 12 confirm that the structure of the mesoporous support is preserved and that no CuO particles are observed, probably due to the formation of Cu–O–Si species or of a thin CuO film.
The SO2 breakthrough curves of samples IWIw-45-r, IWIw-90-r, IWIw-lyo-r and IWIw-lyo-f are shown in Fig. 13. It is noteworthy that the SO2 adsorption capacities of the adsorbents prepared by the IWI method are in the same order of magnitude than those of the adsorbents obtained by wet impregnation in methanol. Here also, the sample prepared with a flash calcination leads to the best SO2 uptake capacity () and the one dried at 90 °C the lowest adsorption capacity () due to the presence of large CuO particles. For this series of IWI samples, the SO2 uptake efficiency can be correlated with the XRD patterns since the SOx adsorption capacity decreases with the increase of the intensity of the XRD peaks of CuO.
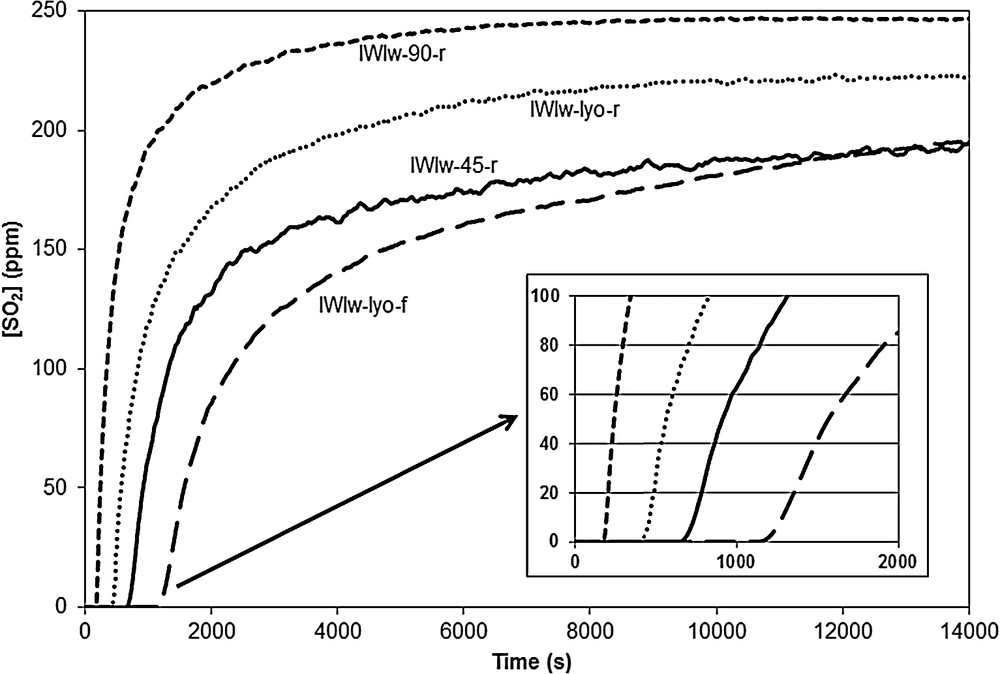
SO2 breakthrough curves of samples IWIw-45-r, IWIw-90-r, IWIw-lyo-r and IWIw-lyo-f.
3.4 Ion Exchange in water (IEw)
The ion exchange method is well-known to yield well dispersed copper oxide particles due to strong interactions between copper species and the silica support, which prevent the sintering during calcination [41–43]. For this series of adsorbents, four drying conditions were compared (20 °C, 45 °C, 90 °C and lyophilization) and two calcination methods (ramp and flash). The adsorbents had a copper oxide loading in the range of 14–15 wt. % (Table 4), which is smaller than for the previous adsorbents (15–18 wt. %). Contrary to the adsorbents prepared by the other methods, the six adsorbents display the same pale green color, whatever the drying or calcination conditions.
Synthesis conditions, textural properties, chemical composition and SO2 uptake capacities of the adsorbents prepared by Ion Exchange in water (IEw).
Sample | SBA15 | IEw-20-r | IEw-20-f | IEw-45-r | IEw-90-r | IEw-lyo-r | IEw-lyo-f |
Drying (24 h) | – | 20 °C | 20 °C | 45 °C | 90 °C | Tamb. + Lyoph. | Tamb. + Lyoph. |
Calcination | Ramp | Ramp | Flash | Ramp | Ramp | Ramp | Flash |
Color | White | Pale green | Pale green | Pale green | Pale green | Pale green | Pale green |
CuO content (wt. %) | 0 | 14.7 | 15.0 | 15.0 | 14.4 | 14.5 | 14.4 |
SBET (m2·g−1) | 938 | 496 | 485 | 395 | 451 | 452 | 393 |
Vp (cm3·g−1) | 1.2 | 0.7 | 0.7 | 0.6 | 0.7 | 0.7 | 0.7 |
Pore size (nm) | 7.5 | 7.7 | 7.4 | 7.6 | 7.5 | 7.5 | 7.5 |
SO2 uptake () | / | 20 | 14 | 13 | 12 | 27 | 22 |
As shown by the XRD patterns of Fig. 14, whatever the drying and calcination conditions, no diffraction peaks of copper oxide are observed, suggesting a strong CuO/SBA-15 interaction. Remarkably, this happens even after a drying at 90 °C.
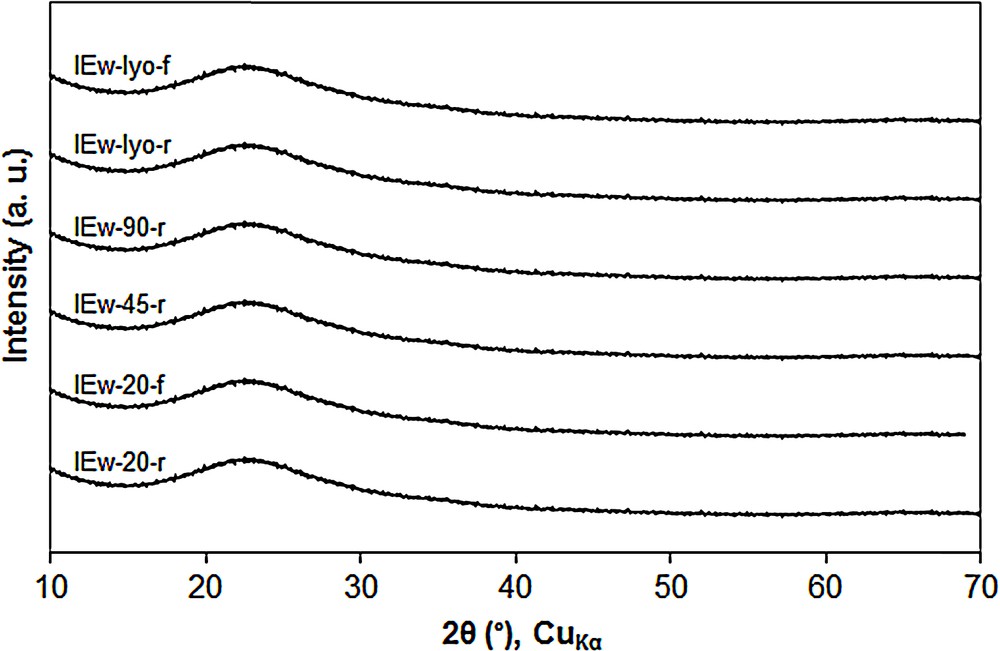
XRD patterns of CuO/SBA-15 adsorbents prepared by Ion Exchange in water (IEw). For a better visibility, the diffraction patterns are shifted along the Y-axis.
The N2 physisorption isotherms of sample IEw-lyo-r reported in Fig. 2 exhibit a stretching of both adsorption and desorption branches in the capillary condensation zone i.e. toward lower pressures (hysteresis loop for P/P0 from 0.7 to 0.8 for pure SBA-15 versus 0.5 to 0.8 for IEw samples). This suggests that a secondary porosity involving pores smaller than in the starting adsorbent is generated during the ion exchange, which may be due to a partial hydrolysis of silica in the alkaline medium. Probably for the same reason, although the BET specific surface areas (393 to 496 m2·g−1) are smaller than those reported for the impregnated adsorbents (485 to 637 m2·g−1), the pore volumes stay in the same order of magnitude (0.7 cm3·g−1). In spite of the modification of the pore size distribution evidenced by the N2 isotherms, the pore size remains virtually centered around 7.5 nm.
The SEM micrographs and the corresponding X-ray mappings (Fig. 15) of the adsorbents IEw-90-r, IEw-lyo-r and IEw-lyo-f confirm that the copper species are homogeneously dispersed regardless of the drying and calcination conditions.
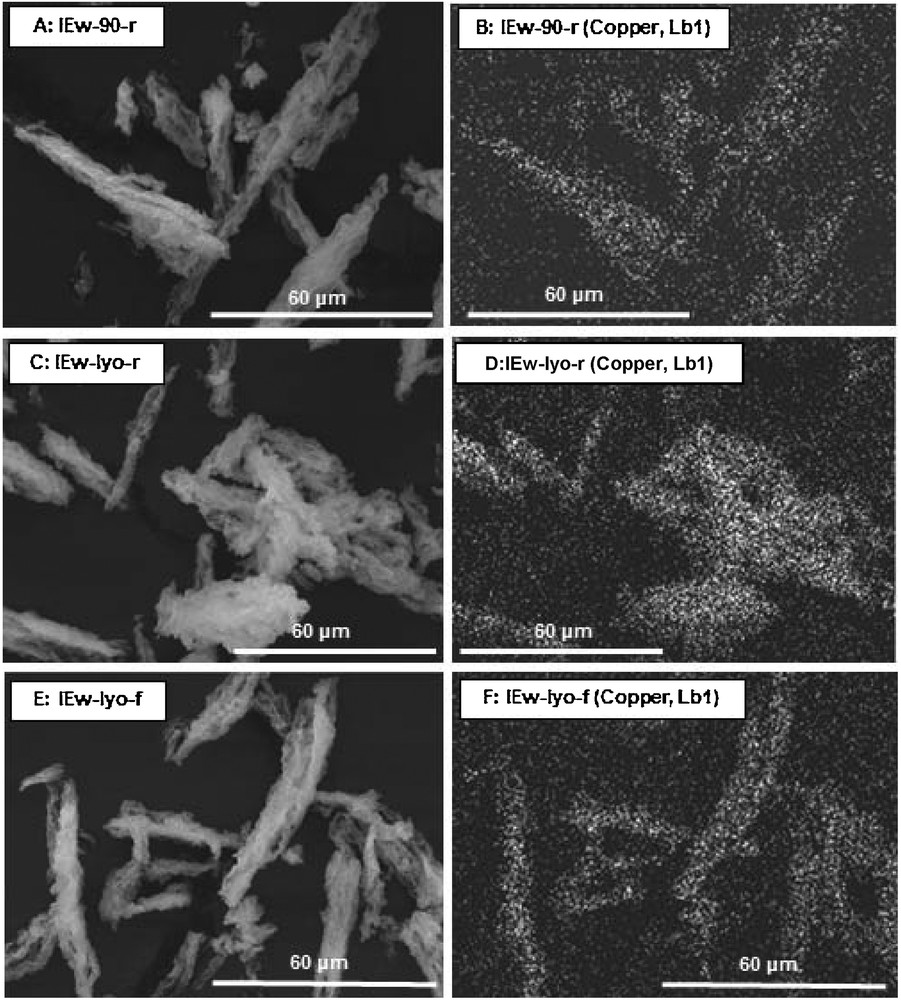
SEM micrographs (A, C and E) and corresponding X-ray mappings (B, D and F) of samples IEw-90-r, IEw-lyo-r and IEw-lyo-f.
The TEM micrographs (Fig. 16) of samples IEw-90-r (A and B), IEw-lyo-r (C and D) and IEw-lyo-f (E and F) confirm that the structure of SBA-15 is preserved despite the mentioned distortion of the N2 physisorption pattern. XRD patterns, SEM and TEM micrographs show unambiguously that whatever the drying and calcination conditions, neither large nor small CuO particles are formed with the Ion Exchange method. This can be explained by the strong interaction between the copper species and the support, which prevents particles from coalescing with each other.
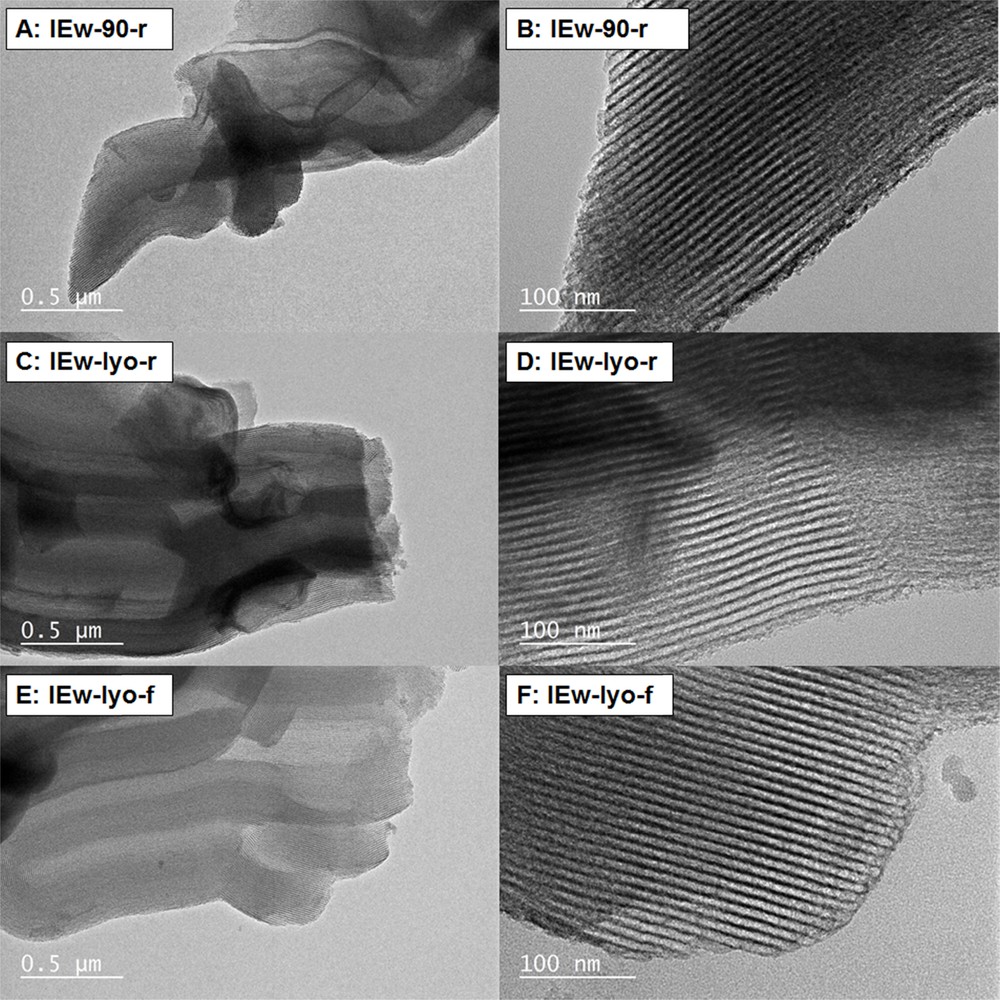
TEM micrographs of samples IEw-90-r (A and B), IEw-lyo-r (C and D) and IEw-lyo-f (E and F) obtained by Ion Exchange in water (IEw).
The SO2 breakthrough curves of samples IEw-20-r, IEw-45-r, IEw-90-r and IEw-lyo-r are given in Fig. 17. Like for the other impregnated adsorbents, despite the non-formation of large CuO particles (see XRD patterns), the drying at 90 °C leads to a degradation of the SO2 adsorption capacity . It is also the case after drying at 20 and 45 °C (14 and ). However, the adsorbent dried at 20 °C (IEw-20-r) exhibits a longer adsorption step, the better result being obtained with the lyophilized adsorbent. It seems therefore that, for the samples calcined with a ramp, the decrease of the drying temperature, leads to a better DeSOx efficiency. The same trend is observed for the adsorbents prepared with the flash calcination although their efficiency remains low.
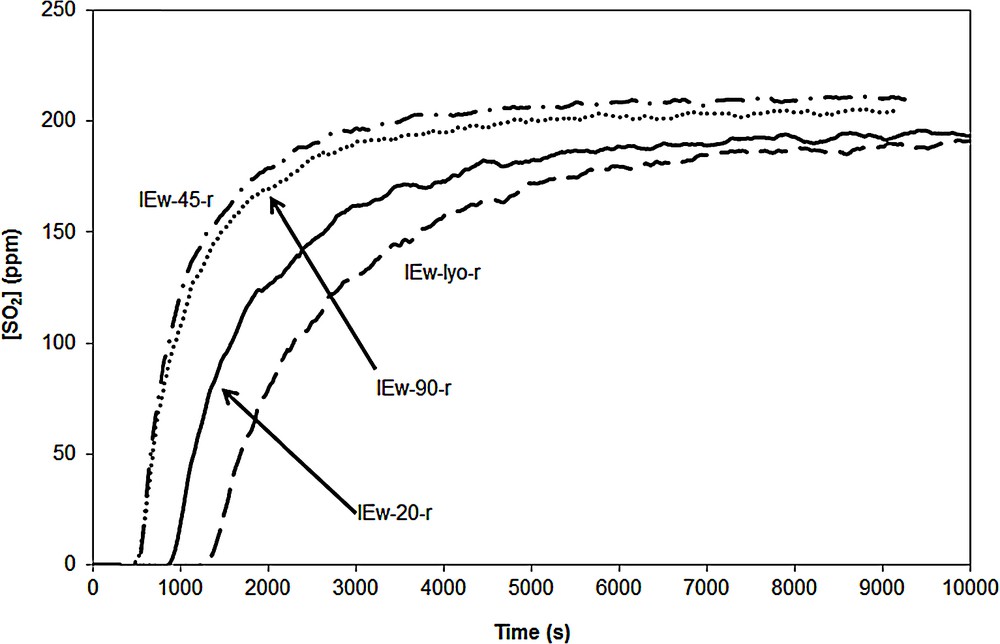
SO2 breakthrough curves of samples IEw-20-r, IEw-45-r, IEw-90-r and IE-lyo-r.
4 Conclusion
In this work, SBA-15 mesoporous silica was doped with copper oxide by three different methods consisting in wet impregnation, incipient wetness impregnation and ion exchange. The N2 physisorption data tend to show that the silica support is unaffected by the wet impregnation method, whatever the solvent used (water or methanol). On the contrary, the basic medium (ammonia) used in the ion exchange causes a modification of the porosity resulting in the broadening of the pore size distribution that is assignable to a partial hydrolysis of silica walls. The slight shift towards higher pressures of the N2 desorption branch that one observes for the incipient wetness impregnated samples is attributed to a partial pore plugging rather than to any alteration of SBA-15 structure. For all impregnated samples series, the interpretation of the XRD patterns suggests a bimodal distribution of copper with the coexistence of:
- • a population of large (∼ 1 μm) copper oxide particles;
- • a population of homogenously dispersed copper atoms that are XRD-undetectable.
The former population is assumed to come from the coalescence of copper oxide species when the drying step is performed at high temperature, whereby the hydrated copper nitrate molecules tend to concentrate in the wet spots that remain during the last vaporization stages. The latter population is assumed to correspond to a strong copper/support interaction that prevents copper oxide formation from undergoing this coalescence process. As one can expect, it is strongly favored by the ion exchange method, regardless of the drying and calcination conditions. As far as the impregnated samples, the comparison of drying and calcination steps highlights their strong influence on the copper distribution: as a general trend, the drying at low temperature and the use of a calcination ramp, favor the formation of homogenously dispersed copper atoms. On the contrary, the drying at high temperature and the flash calcination entail the formation of large copper oxide particles. The correlation between physicochemical data and DeSOx experiments is not straightforward. As expected, large CuO particles are poorly efficient, which is attributed to the slow bulk diffusion of the gaseous O2/SO2 species. The SOx trapping efficiency is most probably related to the homogenously dispersed copper atoms. The best result, with a capacity of , is obtained by wet impregnation in water, without drying and with ramp calcination. Finally, it must be stressed that the rather modest adsorption performances achieved in this study shall be considered in the light of the high GHSV value that corresponds to a contact time in the range of 0.15 s, a value that has been purposely adopted in this work to specifically address the fast exhaust gas speeds of industrial gas turbines.
Acknowledgment
This work (Project AdSOx New-Gen – contract #1281C0039) was supported by the French Agency for Environment and Energy Management (ADEME) through its funding program CORTEA. Authors want to acknowledge L. Michelin for XRD characterizations, L. Josien for SEM/EDX analyses and L. Vidal for TEM characterizations.