1 Introduction
Catalysts have a great effect on chemical reactions because they enhance the efficiency of reactions and decrease process temperatures [1]. Homogeneous catalyst particles dissolve easily in a reaction mixture, whereas heterogeneous catalyst particles do not [2]. High activity and good selectivity are benefits of homogeneous catalysts [3], as opposed to the restricted activity of heterogeneous catalysts. A major difficulty in processing of homogeneous catalysts is that after the reaction has completed, separation of the dissolved catalyst from the final mixture is difficult [4]. Unlike homogeneous catalysts, heterogeneous catalysts separate easily from the reaction mixture and thus do not cause product impurity [5]. Nanoparticles can be used to exploit both the high surface activity of homogeneous catalysts and the capability of separation of the catalyst at the end of the reaction found in heterogeneous catalysts [1]. Nanoparticles, especially metallic and metal oxide nanoparticles, are the most effective nanostructures for supporting catalysts [6]. Nanoparticles do not present a problem in recycling the used catalyst, but they do present a problem with separation of the catalyst from the reaction mixture. A proper technique for facilitating separation is magnetic separation [2]. Recently, magnetic nanoparticles (MNPs) have been broadly used as catalyst supports because of their highly active surface, which causes high loading capacity of the catalyst, high dispersion, remarkable stability, and ease of recovery [7]. Moreover, magnetic particles can withstand virtually all except highly acidic chemical environments. Because MNPs are highly susceptible to oxidation and agglomeration, they are best configured as a core–shell structure making use of either organic or inorganic shells [8]. Among different coatings, silica supports have the advantage of stability and inertness, facilitating functionalization, low cost, and high surface area [9]. The method of using metal–ligand grafting on silica-coated magnetite leads to higher loading than straight grafting of metals onto the same type of surface. Moreover, amine-functionalized nanoparticles have more catalytic activity than metal catalysts with silica coating. Among different metals, nickel and especially zinc are good choices because of their Lewis acid property, which helps the oxidation reaction [10]. Conventionally, oxidation has been performed without any catalyst by using an oxidant alongside mineral acids. This procedure is, however, harmful because it produces high amounts of dangerous wastes. To reduce this hazard to the environment, scientists have attempted to discover and enhance reactions that follow the doctrines of green chemistry [11]. The oxidation of aldehydes is a widely used reaction in organic chemistry [12]. Following the procedure used by Sharma and Monga [13], magnetite nanoparticles were coated with silica and then functionalized with (3-aminopropyl)triethoxysilane (APTES). Acetanilide was introduced to these particles, and finally zinc acetate and nickel chloride were used to prepare two different nanocatalysts. These were used for oxidation of aldehydes. Their easy separation from the reaction mixture was possible because of their magnetic characteristic [6].
High efficiency of the catalyst (with Zn as the metal) was exhibited. Significant conversion of different aldehydes to their acids was yielded (4-methoxybenzoic acid 98.3%, 3-nitrobenzoic acid 97.5%, and 3-hydroxybenzoic acid 97.2%) during the reactions performed under optimal conditions, even after six runs the magnetic nanocatalyst remained recyclable.
2 Materials and methods
2.1 Materials
APTES and tetraethyl orthosilicate were purchased from Merck, Germany. Hydrochloric acid (36.5%), acetanilide, zinc acetate, nickel chloride, ethanol, acetone, dichloromethane, acetonitrile, and hydrogen peroxide were obtained from Research Laboratory.
2.2 Characterizations
Perusal of nanocatalyst morphology was performed by scanning electron microscopy (SEM) on a KYKY-EM3200 scanning electron microscope. The phases of the products were assayed by X-ray diffraction (XRD) on a powder diffractometer using Cu Kα radiation (λ = 1.54060 Å) in the 2θ interval. Fourier transform infrared spectroscopy (FT-IR) were recorded using a Thermo Scientific Nicolet 8700 FT-IR spectrometer. The product of oxidation was analyzed and validated using gas chromatography–mass spectrometry (GC–MS).
2.3 Amino-functionalized SiO2-coated Fe3O4 nanoparticle preparation
We prepared MNPs using a coprecipitation approach. To this end, we dissolved 6.0 g of ferric sulfate and 4.2 g of ferrous chloride in 250 mL of water and stirred the mixture at 60 °C to obtain an orange solution. Next, we subjoined 15 mL of ammonium hydroxide (25%) by stirring, which turned the color of the solution to black, and continued stirring for 30 min. We separated the MNPs and washed them with deionized water and ethanol. We carried out coating of the MNPs by the sol–gel method. We sonicated the solution of activated MNPs in 0.5 g of HCl (0.1 M) combined with 200 mL of ethanol and 50 mL of water, and then added 5 mL of ammonium hydroxide (25%) and 1 mL of tetraethyl orthosilicate to the suspension. We continued stirring at a temperature of 60 °C for 6 h. We separated the resulting SiO2-coated MNPs (SMNPs) and washed them with ethanol. Finally, we sonicated 1.0 g of SMNPs in 700 mL of ethanol and charged the flask containing dispersed SMNPs with 5 mL of APTES, refluxing for 6 h at 80 °C to produce amino-functionalized SMNPs (ASMNPs). Separation and washing of the ASMNPs with ethanol were performed to remove the unreacted silylating agent.
2.4 Synthesis of Zn(II)–acetanilide complex anchored to ASMNPs
To anchor acetanilide onto the ASMNPs, we refluxed 3.0 g of ASMNPs and 6.0 mmol of acetanilide in 375 mL of ethanol at 80 °C for 3 h. To synthesize the nanocatalyst, we stirred 2.0 g of anchored ASMNPs in a solution of 8.0 mmol of zinc acetate in acetone for 4 h. Finally, we separated the obtained Zn(II)–acetanilide@ASMNP nanocatalyst and washed it completely with water.
2.5 Synthesis of Ni(II)–acetanilide complex anchored to ASMNPs
The above-mentioned procedure was repeated to prepare the Ni(II)–acetanilide complex nanocatalyst, with only two differences: nickel chloride was used instead of zinc acetate and methanol instead of acetone (Scheme 1).
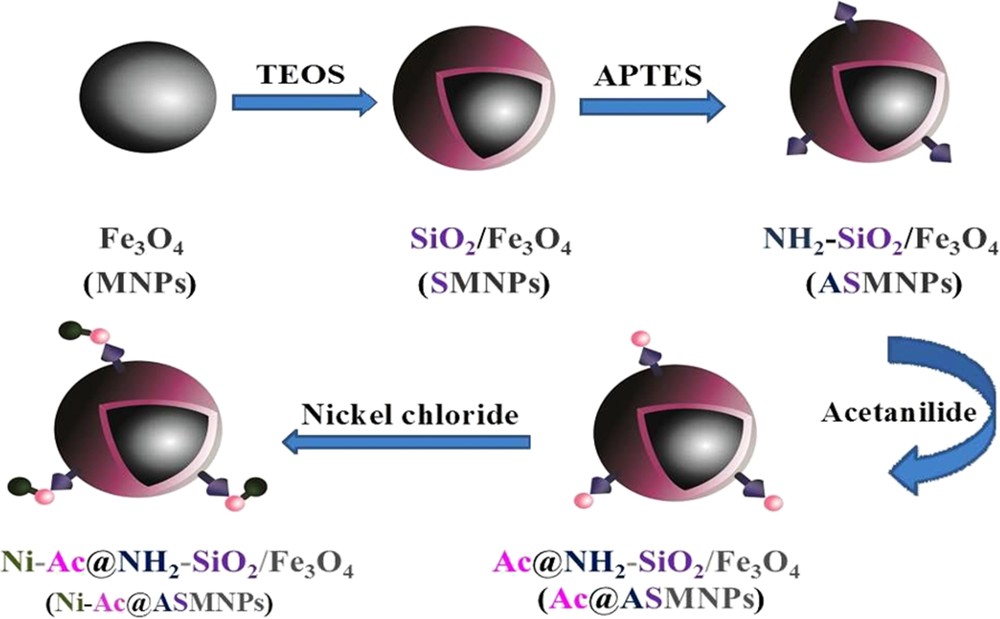
Route for the synthesis of magnetic nanocatalyst with Ni as the metal.
2.6 Evaluation of catalyst activity in oxidation of aldehydes
We poured 10 mmol of benzaldehyde and 200 mg of a nanocatalyst into 10 mL of acetonitrile and refluxed the mixture at 80 °C for 3 h, adding 1.5 mL hydrogen peroxide (30%) dropwise to the reaction mixture during the reflux. After 3 h, we allowed the reaction mixture to cool and aggregated the nanocatalyst using a magnet at the side of the flask. The residual solution was collected with a pipette and extracted using dichloromethane and 10% sodium bicarbonate. The organic layer was dried with sodium sulfate and the solvent removed under vacuum at 66 °C to obtain the final product. GC–MS was used to validate the structure of the product.
3 Results and discussion
3.1 Characterization of Zn(II)–acetanilide@NH2–SiO2–Fe3O4 and Ni(II)–acetanilide@NH2–SiO2–Fe3O4
The SEM image in Fig. 1 shows the monotonic scattering of zinc complex upon the surface of the silica-coated magnetite nanoparticles and is further documented by comparison of the SEM image gained in this study with a previous study [13]. Measurements of the crystalline structures for MNPs and ASMNPs were performed by powder XRD (Fig. 2), which shows the peaks of a cubic inverse spinel structure. The spacings and relative intensities in the diffractogram are consistent with the Joint Committee on Powder Diffraction Standards XRD data (Card No. 19-06291) for Fe3O4. Previous study has validated coating of MNPs for widening of XRD peaks of SMNPs [14]. In our study, synthesis of MNPs, SMNPs, and ASMNPs is evident.
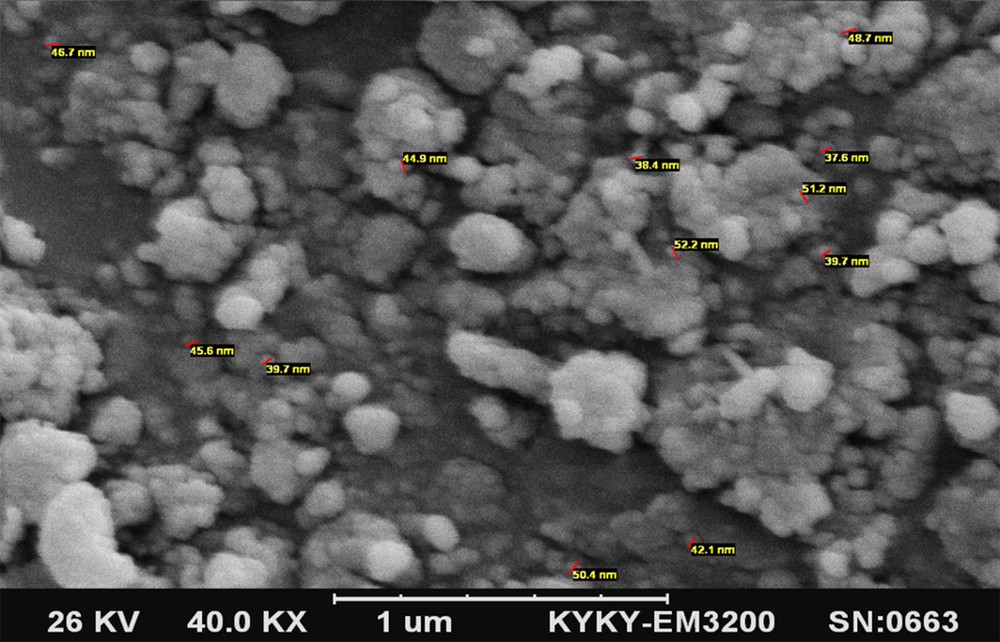
SEM image of a nanocatalyst with Zn as the metal.

XRD pattern of (a) MNPs and (b) ASMNPs.
In FT-IR studies (Fig. 3), a peak at 1632 cm−1 in Fig. 3d indicates anchoring of acetanilide as a ligand on NH2–Si–Fe3O4. This peak is characteristic of the CN stretching vibration. The absorption peak at 1636 cm−1 in Fig. 3e corresponds to binding of zinc as a metal to the ligand, which is confirmed in comparison with previous research [15].
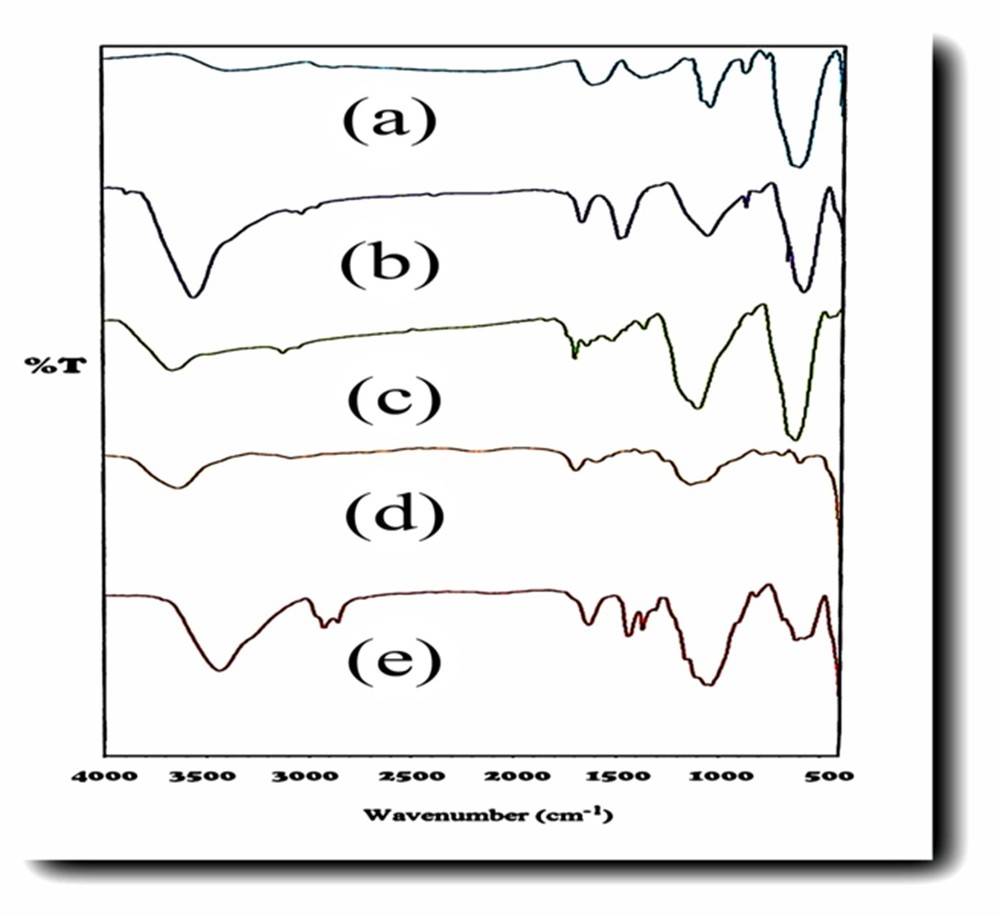
FT-IR spectra of (a) MNPs, (b) SMNPs, (c) ASMNPs, (d) Zn@ASMNPs, and (e) acetanilide–Zn@ASMNPs.
Fig. 4 displays the magnetization curves of the MNPs [16] and the two magnetic nanocatalysts. They exhibited no hysteresis at room temperature. The saturation magnetization of three samples was 60, 30, and 18 emu/g, respectively. In comparing the vibrating sample magnetometry of magnetic nanocatalysts with Zn as the metal in this study with previous research [13], higher magnetization of our catalyst is obvious; the other nanocatalyst with Ni as the metal (which to the best of our knowledge has not been synthesized before) had equal magnetization to the Zn magnetic nanocatalyst in the previous study [13]. The decreased saturation magnetization seen in the nanocatalysts compared with the MNPs is because of the existence of nonmagnetic elements (such as SiO2, Zn/Ni, and acetanilide) in the nanocatalysts. Despite this reduction in saturation magnetization, these particles were separated from the reaction medium with an external magnet.
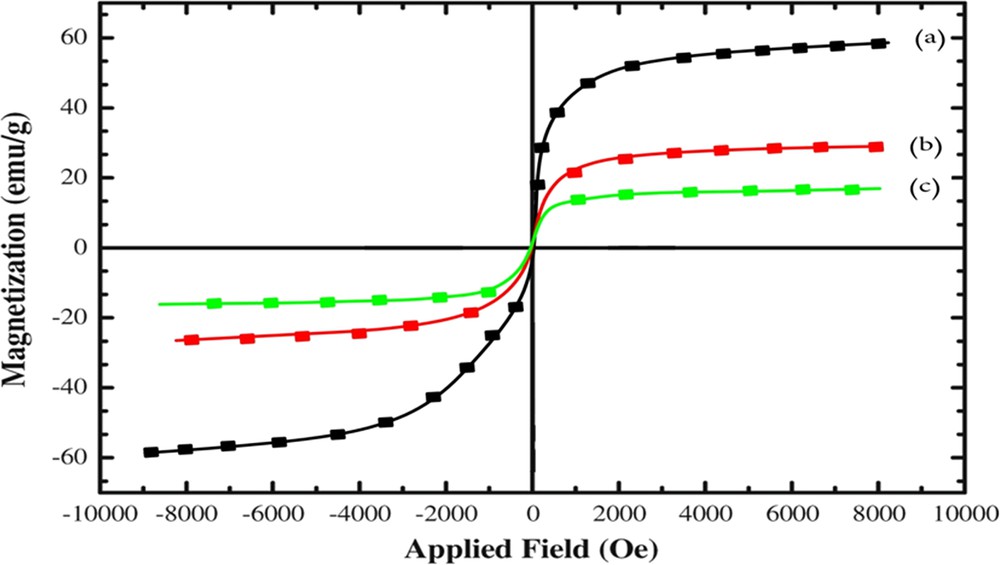
Magnetization curves of (a) MNPs, (b) acetanilide–Zn@ASMNPs, and (c) acetanilide–Ni@ASMNPs.
3.2 Catalytic efficiency
The prepared nanocatalysts Zn(II)–acetanilide@NH2–SiO2–Fe3O4 and Ni(II)–acetanilide@NH2–SiO2–Fe3O4 were used for oxidation of benzaldehyde. Although both nanocatalysts transmuted benzaldehyde into benzoic acid with high efficiency, the zinc nanocatalyst had higher transformation (100%) than the nickel nanocatalyst. The optimal time and temperature for conversion were found to be 3 h and 80 °C, respectively.
As these nanocatalysts retained their high catalytic efficiency (100% for the nanocatalyst with zinc and 55% for the nanocatalyst with nickel) after six cycles, their reusability is confirmed. Different time periods (1.5, 3, and 6 h) were tested on the zinc nanocatalyst. The highest rate of transformation (100%) was obtained at 3 h. When the time was decreased to 1.5 h, transformation decreased to 65%. When the time was increased to 6 h, transformation decreased to 36% (Fig. 5). For these time experiments, the temperature was set at 80 °C.

GC–MS results for the oxidation product of benzaldehyde by a nanocatalyst (a) with Zn after 3 h and (b) after 1.5 h and (c) with Ni after 3 h and (d) with Zn after 6 h.
The nanocatalyst with zinc was used for the oxidation of different aldehydes. Oxidation of 3-hydroxybenzaldehyde and 3-nitrobenzaldehyde was carried out under the same conditions. Acetonitrile was used as a solvent (10 mL), H2O2 (1.5 mL) as an oxidant, and dichloromethane was used for extraction of the organic phase. The reaction was continued for 3 h at 80 °C. For 4-methoxybenzaldehyde, the reaction was continued for 6 h. GC–MS was used for evaluation of the conversion. The highest conversion was obtained for the oxidation of 3-hydroxybenzaldehyde, with oxidations of 4-methoxybenzaldehyde and 3-nitrobenzaldehyde having lower conversions (Fig. 6).

GC–MS results for the oxidation product of (a) 3-hydroxylbenzaldehyde, (b) 4-methoxybenzaldehyde, and (c) 3-nitrobenzaldehyde by a nanocatalyst with Zn as the metal.
3.3 History of nanocatalysts used for the oxidation of aldehydes
Different nanocatalysts have been used for the oxidation of aldehydes. Of note is the use of Fe3O4 nanoparticles activated by ethyl acetoacetate for the oxidation of different aldehydes in solvent-free conditions and comparing two oxidants: H2O2 and tert-butyl hydroperoxide; higher conversion was achieved with tert-butyl hydroperoxide [17]. Another study used biosilica-supported Fe2O3 nanoparticles as a nanocatalyst, using H2O2 as an oxidant and acetonitrile as the solvent [18]. Other research used an iron–oxalate capped iron–copper bimetallic oxide nanomaterial for the oxidation of aldehydes to their acids and esters [19]. Other catalysts investigated for this purpose include bio-derived CuO nanoparticles [20], oxoammonium salt, Mohr's salt [21], and gold [22].
4 Conclusions
Two heterogeneous catalysts based on different metals, that is, Ni(II)–acetanilide@NH2–SiO2–Fe3O4 and Zn(II)–acetanilide@NH2–SiO2–Fe3O4, were prepared and used for the oxidation of benzaldehyde to benzoic acid. The catalytic efficiency of each nanocatalyst was evaluated. High transformations (100% for the nanocatalyst with zinc and 55% for the nanocatalyst with nickel) were obtained under the optimal conditions of 0.2 g of a nanocatalyst, 1.5 mL of H2O2, 10 mL of acetonitrile, and 1 mL of substrate (benzaldehyde) at 80 °C for 3 h. The catalyst could be isolated from the reaction medium with an external magnet. The nanocatalysts were used for six runs without losing their activity, which demonstrated their efficiency, recoverability, and reusability. The use of zinc as a metal especially increased the efficiency of the nanocatalyst because of its Lewis acid property. These features make these nanocatalysts appropriate heterogeneous catalysts for oxidation of aldehydes.
Vous devez vous connecter pour continuer.
S'authentifier