1 Introduction
Nowadays aromas are essential ingredients that find widespread use in the food and perfume industries. The use of petroleum-based aromas in the modern food and perfume industries is a common practice, but there is a growing concern about their actual or potential effect on human health, resulting in an increasing demand of consumers for natural aromas. This concern has led to an increasing interest and use of natural products as alternative food aromas. It is therefore not surprising that the global market value for aromas was estimated to be US $26 billion in 2015 and is projected to reach nearly US $30 billion in 2020, with a compound annual growth rate of 5% [1,2].
Extraction of aromas from natural products could be considered as a “clean process” in comparison with extraction processes currently used in other industries; however, recent studies have shown that their environmental impact is greater than what appeared at first [3]. As the raw extraction yields are often very low (<1%), the production of aromas requires huge amounts of plant materials and solvents, mainly hexane as the most consumed petroleum-based solvent for the production of concrete. Other solvents could be used such as toluene, pentane, or dichloromethane. After this first extraction, ethanol (bio-based solvent) is needed for a second step in this process, for production of the absolute from the concrete. Aromas could also be obtained in the form of essential oils by steam or hydrodistillation (HD) of fresh aromatic herbs or dry spices. Evaporation of such amounts of solvents is known to be very energy intensive, such that the extraction and evaporation step is often responsible for more than 50% of the overall process energy consumption. Moreover, the traditional extraction techniques (steam distillation and solvent extraction) generally involve high process temperatures that may greatly affect the product quality, in particular in the case of sensitive flowers that contain thermos-sensitive compounds (rose and jasmine).
To promote eco-friendly extraction processes in the industry, Chemat et al. [4] established the “six principles of green extraction of natural products”, inspired from the principles of green chemistry. By definition, green extraction “is based on the discovery and design of extraction processes which will reduce energy consumption, allows use of alternative solvents and renewable natural products, and ensure a safe and high quality extract/product”. The application of these principles already led to several success stories, with the emergence of new innovative green extraction processes based on innovative techniques and alternative solvents [5,6].
Still, more work needs to be done to find viable alternatives to conventional toxic solvents, in particular n-hexane, which is still commonly used for the extraction of lipophilic compounds. This constant search for alternative solvents revived the interest of scientists for liquefied gases, in particular propane, n-butane, dimethyl ether (DME), 1,1,1,2-tetrafluoroethane (R134a), 1,3,3,3-tetrafluoropropene (HFO-1234ze), and 2,3,3,3-tetrafluoropropene (HFO-1234yf). Indeed, these gases require only gentle pressure (<1 MPa) to remain in a liquid state and they can be very easily evaporated at low temperature. Therefore, liquefied gas extraction processes can be performed at room temperature, with low energy consumption and very few traces of residual solvent. Therefore, liquefied gas extraction preserves the quality of both the raw material and extract and reduces the number of post-treatment steps. Moreover, their chemical structures make them suitable for the extraction of lipophilic compounds in replacement of existing toxic solvents. In that sense, liquefied gas extractions offer a potential alternative technology in accordance with the principles of green extraction of natural products.
Recently, many experimental studies have been carried out to evaluate their potential. In particular, propane, n-butane, and DME have been extensively investigated for the extraction of fats and oil from seeds [7–12] or microorganisms [13–18]. Surprisingly, despite the potential of liquefied gases for the extraction of volatile and sensitive molecules, only a few studies on aromatic compounds can be found in the literature [19–22].
To fill this gap, we tried to compare in this article the performance of three liquefied gases (n-butane, DME, and HFO-1234ze) as potential alternative solvents for the extraction of aromatic compounds from two plant materials: dry lavender flowers (Lavandula angustifolia Mill.) and fresh orange peels (Citrus sinensis (L.) Osbeck). The solvent evaluation was performed using distinct approaches (Fig. 1). First, a predictive approach was conducted using the conductor-like screening model for real solvents (COSMO-RS) to predict the relative solubility of some selected target components in the liquefied gases. This theoretical approach was coupled with laboratory-scale experiments to assess the quantitative (extraction yields) and qualitative (chemical composition and sensorial analysis) aspects of the extracts to compare the efficiency of liquefied gases with n-hexane, chosen as a reference conventional solvent. Finally, their industrial applicability was evaluated in terms of safety, regulation, and environmental impacts.

Theoretical and experimental procedures.
2 Materials and methods
2.1 Chemicals
The liquefied gases used for pilot-scale extractions, that is, n-butane 95% purity, DME 99.9% purity, and trans-1,3,3,3-tetrafluoroprop-1-ene (HFO-1234ze) 99.5% purity, were purchased from Inventec Performance Chemical (St. Priest, France), whereas n-hexane of analytical grade was purchased from VWR International (Radnor, USA).
2.2 Plant materials
Dried lavender flowers (L. angustifolia Mill.; water content, 7.5%) and frozen orange peels (C. sinensis (L.) Osbeck; water content, 72%) were purchased from local suppliers.
2.3 Liquefied gases apparatus and extraction procedure
Extractions were performed using a 1-L pilot plant (NECTACEL, Celsius sarl, Villette-de-Vienne, France) shown in Fig. 2 and described in previous works [8,9].

Process diagram of a laboratory-scale unit designed for extractions using liquefied gases as a solvent. (a) 0, liquefied gas bottle; 1, valve; 2, manometer; 3, safety valve; 4, solvent storage tank; 5, double jacketed stainless steel extractor; 6, thermometer; 7, double jacketed stainless steel evaporator; 8, stainless steel condenser; 9, heated bath circulator; 10, cooling bath circulator. (b) NECTACEL 1-L extraction unit manufactured by Celsius Sarl (Villette-de-Vienne, France) filled with lavender flowers.
Liquefied n-butane extractions were performed using the following general procedure: first, 100 g of a plant material is introduced in a cellulose sock (porosity 50 μm) placed inside the extractor (5) and the entire unit is put under vacuum to remove air. Next, 0.9 L of liquefied gas is transferred from the gas bottle (0) to the storage tank (4). The solvent is then flowed to the extractor (5) containing the plant material. The mixture is maintained at 25 °C via the double jacket. After 1 h of maceration, the solvent containing the extract is transferred to the evaporator (7) where the solvent is evaporated. The solvent vapors naturally rise to the condenser (8) for recycling whereas the extract remains at the bottom of the evaporator. The plant material is then re-extracted three times, using the recycled solvent, for a maximum extraction yield. In the end, the total duration is four times 1 h. The remaining extract is finally collected in a flask and inner walls are washed with 100 mL of n-hexane for maximum recovery. Each extraction was made in duplicate.
2.4 Hexane macerations of lavender flowers and orange peels
As the liquefied gases chosen in this study are mostly lipophilic, n-hexane was chosen as a reference conventional extraction solvent. Extractions were performed in the NECTACEL extraction vessel (5) using the following procedure: 100 g of a plant material is introduced in a cellulose sock (porosity 50 μm) placed inside the extractor. Next 0.9 L of n-hexane is added and the mixture is thermostated at 25 °C via the double jacket. After 1 h of static solid–liquid contact, the solvent containing the extract is collected and 0.9 L of a fresh solvent is introduced in the extractor. The operation is renewed three times for a total extraction duration of four times 1 h. Each extraction was made in duplicate.
2.5 HD of lavender flowers and orange peels
To get a base point for chemical composition and sensory analysis, essential oils were made using the following procedure: 430 g of a plant material (lavender flowers or orange peels) is soaked in 4.3 L of water and hydrodistilled using a Clevenger-type apparatus for 2 h. The essential oil is then collected, dried under anhydrous sodium sulfate, and weighed. Each distillation was made in duplicate.
2.6 Extract processing
The raw extracts obtained from lavender flowers and orange peels are centrifuged (10,000 rpm; 20 min; 20 °C) to separate the organic phase from the aqueous phase and solids particles. Each organic phase is then evaporated using a rotary vacuum evaporator (40 °C; 25 kPa) and the resulting extracts are stored at −20 °C before analysis.
2.7 GC–MS analysis of aromatic compounds
The chemical composition of each extract was determined by GC–MS analysis. Sample solutions were prepared with 33 g/L in ethanol. Liquid injection was conducted with a CTC installed on an Agilent 6890GC using a 5973N simple quadrupole mass spectrometer (Agilent Technologies, USA). The injection volume was set as 1.5 μL. The following parameters were used for GC–MS analyses: column Supelcowax 10 (SUPELCO) (30 m × 0.25 mm × 0.25 μm); temperature, from 40 °C (2 min) to 240 °C at 3 °C/min and maintained for 5 min; carrier gas, helium; flow rate, 1.3 mL/min. A simple quadrupole mass spectrometer was used for detection. Mass spectra were recorded in electron ionization mode at 70 eV. The transfer line and the ion source were set at 250 and 230 °C, respectively. Mass spectra were scanned in the range m/z 30–450 amu. Compound identification was carried out by comparison of mass spectra recorded and mass spectra from several libraries (Adams, ISIPCA, and NIST 11 libraries). Each analysis was performed in triplicate.
2.8 Sensory analysis of lavender and orange extracts
To compare the olfactory perception of each extract, a sensory analysis was performed by seven highly trained panelists (only women aged between 53 and 67 years) in olfaction, with at least one training session per week for 2.5 years.
2.8.1 Products
Two percent solution from orange and lavender extracts was prepared in ethanol. Scent cards coded with three random digits were dipped inside and then presented to panelists. The samples were coded with three random digits and served in sequential monadic order to avoid carryover effects.
2.8.2 ISIPCA's odor wheel
The panelists have been involved in creating a tool named as “ISIPCA' smell” (odor wheel). To do so, they have generated their own terms to describe odors in different categories (e.g., floral and woody). Then, subcategories (e.g., white flowers and dry wood) were defined by means of sorting tasks on olfactory raw materials. A reference raw material is therefore designated to each subcategory. The underdevelopment ISIPCA' smell contains already 82 items divided in 10 categories and 21 subcategories. Ten panelists have participated in the development of this tool, among which seven participated in sensory evaluation of our products.
2.8.3 Descriptive analysis (Check-all-that-apply via ISIPCA' smell tool)
Seven experts answered “Check-all-that-apply” (CATA) questions containing descriptors within ISIPCA' smell tool. The presentation of the terms of the CATA question is in the form of a hierarchical tree. This hierarchical presentation includes the following headings: main categories, subcategories, and olfactory notes. Panelists were asked to check all attributes they considered appropriate to describe each sample in digital forms using Fizz Sensory Analysis Software (Biosystèmes, France). The samples were coded with three random digits and served in sequential monadic order, taking care to avoid carryover effects. Sensory evaluation was carried out during two different days, with one session for each product (one session for orange extracts and one session for lavender extracts) and a 1-week interval between sessions.
2.8.4 Evaluation conditions
The tests were conducted in individual booths with the temperature of 20 °C and white lighting. Panelists were allowed to take pauses whenever needed. The sessions were conducted in the Sensory Analysis Laboratory of the ISIPCA.
2.8.5 Data analysis
Frequency of use of each CATA term was determined by counting the number of experts who used that term to describe each sample. Correspondence analysis (CA) was performed on the frequency table of terms most frequently cited for each type of the product. CA was performed considering Euclidean distances. A hierarchical cluster analysis (HCA) with the Ward criteria was finally applied to all CA dimensions. All statistical analyses were performed using XLSTAT (version 2015).
2.9 Observation of lavender flowers using scanning electron microscopy
Scanning electron microscopy (SEM) was used to examine the physical aspect of the lavender flowers after being extracted by HFO-1234ze, n-butane, DME, n-hexane, and water. For each sample, some flowers have been randomly selected and stuck using double-face adhesive tape on an aluminum plate before they were sputter-coated in gold using an SCD 004 sputter (Balzers, Switzerland). Finally, the samples were observed at 10 kV using an XL30 scanning electron microscope (FEI-Philips, USA).
2.10 Computational method: COSMO-RS calculations
COSMO-RS is a calculation method developed by Klamt [23] using a quantum chemistry model based on the prediction of chemical potential of a substance in the liquid phase. COSMO-RS has been used, among other things, as a powerful prediction tool for solvent screening [24–26].
The COSMO-RS procedure comprised two steps performed at different scales: a microscopic scale step followed by a macroscopic scale step. First, the COSMO is used to apply a virtual conductor environment for the molecule, inducing a polarization charge density on its surface: the σ-surface (Fig. 3).
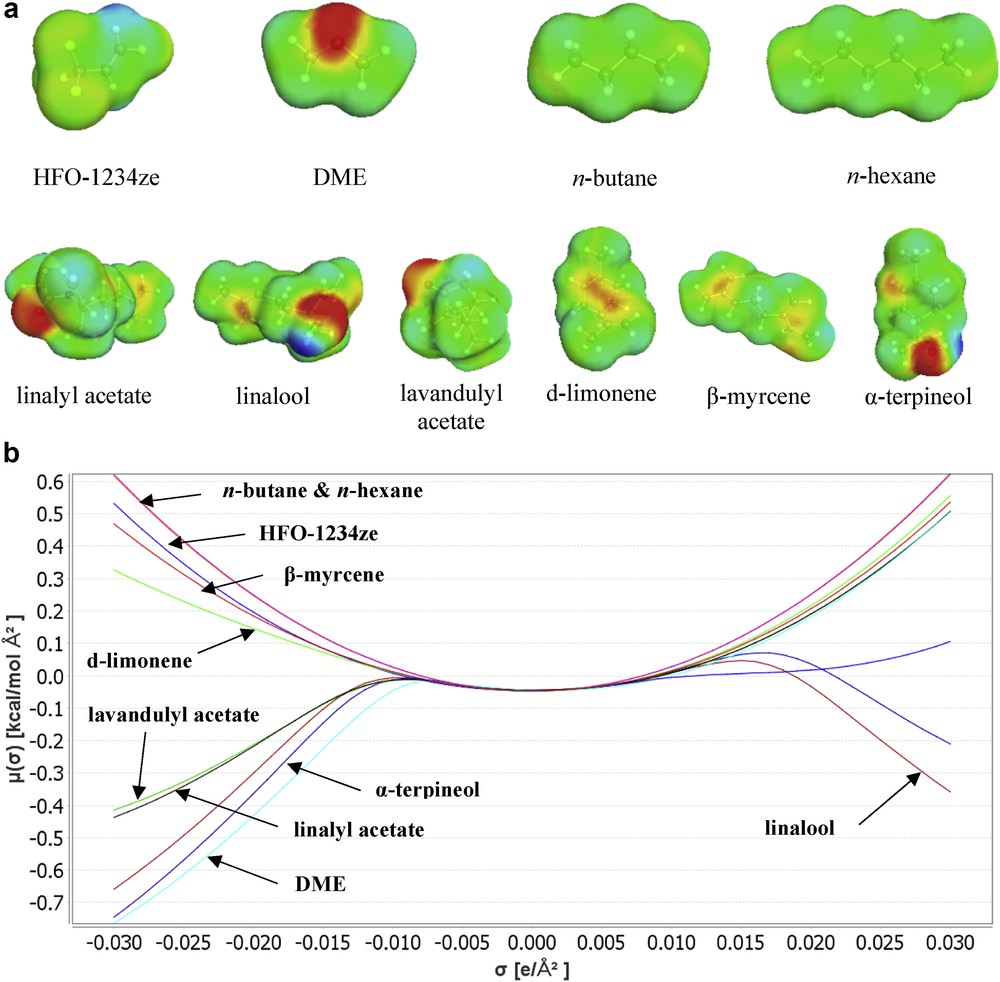
σ-Surfaces (a) and σ-potentials (b) of selected solutes and solvents calculated using COSMO-RS.
On the basis of the obtained polarization charge density, the solute interaction energy is quantified using a statistical thermodynamic calculation. The spatial distribution of the polarization charge is converted into a composition function: the σ-profile. This σ-profile provides information about the molecular polarity distribution and is then integrated to calculate the chemical potential of the surface (σ-potential) using COSMOthermX program (version C30, release 16.02).
On the basis of this σ-potential (Fig. 3), the software COSMOthermX calculates the theoretical affinity between a solute and the solvent. The results are expressed as the log10 of the mole fraction of the solute: log10(xsolub). The logarithm of the best solubility is set to zero and all the results with the other solvents of the list are given relatively to the best solvent. As an example, a solute with log10(xsolub) = −1 in a solvent S has, in theory, a solubility 10 times lower than the same solute in the best solvent (log10(xsolub) = 0).
All the calculations were performed at 25 °C, considering that both solutes and solvents are pure and in a liquid state.
2.11 Liquefied gases versus n-hexane: determination of technical properties
Table 1 reports some physicochemical properties of liquefied HFO-1234ze, n-butane, DME, and n-hexane. Technical data were obtained from ACD laboratories and from suppliers (VWR International, Inventec Performance Chemicals). The global energy of evaporation for 1 kg of a liquid solvent was calculated using Eq. (1), considering the following initial state: pure incompressible liquid at 25 °C and 101 kPa for n-hexane, 499 kPa for HFO-1234ze, 590 kPa for DME, and 243 kPa for n-butane.
(1) |
Comparison of technical properties of liquefied gases versus n-hexane.
Properties | Unit | HFO-1234ze | DME | n-Butane | n-Hexane |
Chemical structure | |||||
Molecular formula | C3H2F4 | C2H6O | C4H10 | C6H14 | |
Molecular weight | g/mol | 114.04 | 46.07 | 58.12 | 86.18 |
Boiling point (101.3 kPa) | °C | −18.9 | −24.8 | −0.5 | 68.5 |
Vapor pressure (25 °C) | kPa | 499 | 590 | 243 | 21 |
Specific heat (25 °C) | kJ/kg K | 1.39 | 2.43 | 2.43 | 2.23 |
Latent heat of vaporization | kJ/kg | 163a | 400a | 361a | 334 |
Energy to evaporate 1 kg from 25 °C | kW h | 0.05a | 0.11a | 0.10a | 0.12 |
Liquid phase density (25 °C) | kg/m3 | 1163 | 661 | 573 | 650 |
Liquid phase viscosity (25 °C) | mPa s | 0.20 | 0.12 | 0.16 | 0.32 |
Log10 P | 1.3 | −0.1 | 2.9 | 3.9 | |
Solubility in water (25 °C) | kg/m3 | 0.37 | 515a | 0.07 | 0.01 |
ODPb | CFC-11 equivalent | 0 | 0 | 0 | n.a. |
GWP100c | CO2 equivalent | 6 | 1 | 20 | n.a. |
GHSd labels | |||||
Hansen solubility parameters | MPa½ | ||||
δd | 13.9 | 15.2 | 14.1 | 14.9 | |
δp | 3.3 | 6.1 | 0 | 0 | |
δh | 2.8 | 5.7 | 0 | 0 |
a Values at 25 °C, under vapor pressure.
b Ozone depletion potential.
c Global warming potential (100 years).
d Globally harmonized system of classification and labeling of chemicals.
3 Results and discussion
3.1 Liquefied gases as alternative solvents to n-hexane: comparison of properties
To evaluate if liquefied gases can be alternatives to n-hexane, technical properties of each solvent were compared. As shown in Table 1, HFO-1234ze, DME, and n-butane exhibit very specific properties, most of them are unusual as compared to conventional solvents, in particular boiling points and vapor pressures. HFO-1234ze, DME, and n-butane have a boiling point lower than 0 °C at atmospheric pressures, respectively, −18.9,−24.8, and −0.5 °C and they generate vapor pressures of, respectively, 499, 590, and 243 kPa at 25 °C. Even if these relatively high vapor pressures have an impact on the cost of industrial extraction units (higher is the operating pressure, higher is the investment cost), they also make the solvent much easier to separate from the extract and from the raw material and limit the number of purification steps. Liquefied gases also exhibit interesting physical properties that make them good candidate as alternative solvents.
Indeed, in a previous work we calculated that HFO-1234ze requires much less energy to be evaporated (0.05 kW h for 1 kg) as compared with conventional solvents, such as n-hexane, ethanol, acetone, and water [9]. Because of higher latent heat of vaporization caused by high van der Waals interactions, the energy required to evaporate 1 kg of DME and n-butane resulted in similar values with n-hexane with 0.11, 0.10, and 0.12 kW h, respectively. As a comparison, evaporation of 1 kg of water at 25 °C requires about 0.71 kW h.
Like most halogenated solvents, HFO-1234ze exhibits a high density (1163 kg/m3) as compared to DME, n-butane, or n-hexane (661, 573, or 650 kg/m3, respectively). Interestingly, liquefied gases also have very low viscosities (0.20, 0.12, and 0.16 mPa s, respectively) as compared to n-hexane (0.32 mPa s) such that they can easily flow throughout the plant material, resulting in higher internal mass transfer [27]. Regarding the Hansen solubility parameters and log10 P values, DME can be defined as neither polar nor apolar (log10 P = −0.1), whereas HFO-1234ze (log10 P = 1.3) and n-butane (log10 P = 2.9) can be defined as lipophilic, making them potential alternative to n-hexane (log10 P = 3.9).
Among liquefied gases, DME is the only one being quantitatively miscible with water (solubility in water = 515 kg/m3 at 25 °C). This specificity makes it suitable for direct extraction of a highly wet material contrary to HFO-1234ze, n-butane, and n-hexane that are more efficient on the dry material.
Considering chemical reactivity, the liquefied gases considered in this study are assumed chemically inert at gentle temperature as they are currently used as propellant gases and solvents in aerosol formulations containing a wide range of chemicals. To our knowledge, no evidence of side reactions has been reported in the literature.
3.2 Evaluation of target compounds predicted solubility in liquefied gases and n-hexane using COSMO-RS
The COSMO-RS was used as a prediction tool to assess the ability of liquefied gases to dissolve major components found in lavender flower and orange peel extracts, relatively to n-hexane. For the calculations, six representative compounds of lavender (linalool, linalyl acetate, caryophyllene, terpinen-4-ol, lavendulyl acetate, and caryophyllene oxide) and orange (β-pinene, limonene, α-terpineol, n-decanal, valencene, and nerol) essential oils were selected as target components to be solubilized in HFO-1234ze, DME, n-butane, and n-hexane, the reference solvent. Table 2 reports the relative solubility results expressed in log10(xsolub).
COMSO-RS relative solubility values—log10(xsolub)— at 25 °C for major compounds found in lavender and orange peel extracts.
The results of COSMO-RS simulations show that DME is the best solvent among the list, with values of log10(xsolub) = 0 for all solutes. In particular, for nerol and linalool, DME is a significantly better solvent than n-hexane, with log10(xsolub) values of 0 against −1.089 and −1.227, respectively, meaning that solutes are considered as, respectively, about 10 and 20 times more soluble in DME. In the case of n-butane, values of log10(xsolub) are almost equal to n-hexane, because of the chemical structure similarity, meaning that COSMO-RS logically predicts a similar behavior. Both solvents resulted in good solubilization of aromatic compounds (values of log10(xsolub) > −0.500), except for terpene alcohols such as nerol, linalool, terpinene-4-ol, and α-terpineol. On the contrary, HFO-1234ze calculations resulted in rather good results for all compounds except for sesquiterpenes (caryophyllene and valencene).
In conclusion, the COSMO-RS simulations suggest that DME is expected to be the best solvent among the list for the solubilization of all the aromatic compounds of lavender flowers and orange peels. Simulations also indicate that HFO-1234ze has an average solvent power, whereas n-butane has a solubilization profile very similar to n-hexane.
3.3 Quantitative and qualitative comparison of extracts from lavender flowers
3.3.1 Extraction yields
Table 3 shows the extraction yields obtained from lavender flowers. Under similar temperature and time conditions, extraction by solvent maceration resulted in green oleoresins with yields from 0.9% (HFO-1234ze) to 2.8% (DME). The initial studies showed that HFOs have only a limited solubilization power, it was expected to be less efficient than the other solvents. On the contrary, DME has shown its capabilities to extract a wide range of lipophilic compounds and also the in situ water; therefore, it is not surprising that it resulted in the highest extraction yield. Between these two solvents, n-butane and n-hexane showed close extraction yields with 1.9% and 1.3%, respectively, in accordance with COSMO-RS simulations. HD was chosen as a reference method and yielded 1.2% of essential oil, in agreement with the literature [28]. In comparison with HD, all the four solvents (except HFO-1234ze) gave better extraction yields, although it should be borne in mind that they have the ability to extract not only aromatic compounds but also fats and waxes.
Extraction yields obtained with HFO-1234ze, DME, n-butane, and n-hexane from lavender flowers.
Solvent | T (°C) | Time | Extraction yield (g/100 g SM) | SD |
HFO-1234ze | 25 | 4 × 1 h | 0.9 | 0.1 |
DME | 25 | 4 × 1 h | 2.8 | 0.2 |
n-Butane | 25 | 4 × 1 h | 1.9 | 0.2 |
n-Hexane | 25 | 4 × 1 h | 1.3 | 0.2 |
Water | 100 | 2 h | 1.2 | 0.1 |
To understand further these differences, the physical impact of the extractions on the lavender flowers was assessed using SEM. In particular, the possible influence of the pressure generated by liquefied gases was investigated.
3.3.2 Structural impacts of extraction processes
The SEM observation on untreated lavender inflorescences (Fig. 4a) confirmed the presence of numerous glandular trichomes with a balloon shape, protected by bifurcated nonglandular trichomes, in agreement with the literature [29].
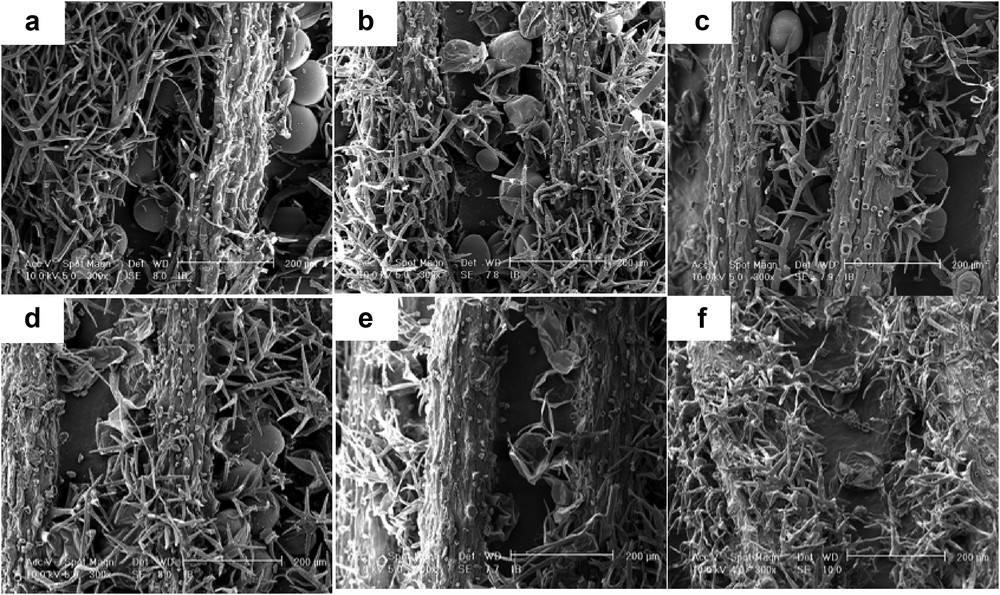
Lavender flowers observed by SEM (magnification, 300x): (a) raw material, (b) after extraction with HFO-1234ze, (c) after extraction with n-butane, (d) after extraction with n-hexane, (e) after extraction with DME, and (f) after HD.
The SEM images of the samples extracted using HFO-1234 (Fig. 4b), n-butane (Fig. 4c), and n-hexane (Fig. 4d) showed a similar feature, despite different working pressures: some glandular trichomes are disrupted but most of them appeared only partially drained. This observation tends to show that the pressure generated at 25 °C by HFO-1234ze (499 kPa) and n-butane (243 kPa) did not improve gland draining. On the contrary, all the glandular trichomes appeared almost empty on SEM picture of flowers treated using DME (Fig. 4e). A similar impact was observed after HD at 100 °C (Fig. 4f). Despite that vapor pressure of DME at 25 °C is higher than other liquefied gases (590 kPa), it seems unlikely that this limited overpressure is responsible for the gland draining. Considering that the cuticles seem still intact, the use of DME should have enhanced the mass transfer through the cell membrane because of (1) a better solute solubilization due to DME ability to be a hydrogen bond acceptor and (2) the miscibility of DME with cellular water. Even if these hypotheses will have to be confirmed by extensive investigations, the ability of DME to pass the cellular membranes has already been observed by Kanda and co-workers [13,30]. Moreover, Chen and Spiro [31] have also observed similar phenomenon during the extraction of rosemary using ethanol, and they hypothesized that the water miscibility of the solvent greatly enhanced the solvent penetration into the cells, compared with n-hexane.
3.3.3 Chemical compositions
In light of the differences in terms of chemical properties, COSMO-RS results, and extraction yields, the HD and the solvent macerations should result in significant variations in the chemical composition of the extracts.
Chromatographic profiles of each of extract samples were analyzed and peaks were identified by NIST and ISIPCA mass spectral libraries. In total 34 compounds were identified (Table 4), with 31 compounds detected in the essential oil, 16 in n-butane and n-hexane extracts, 14 in DME extract, and 13 in HFO-1234ze extract.
Relative abundances of compounds found in lavender flower extracts recovered with different solvents.
Compounds | RIa | HD (%) | n-Butane (%) | DME (%) | HFO-1234ze (%) | n-Hexane (%) |
Monoterpenes | 4.0 | – | – | – | – | |
α-Pinene | 1032 | 0.1 | – | – | – | – |
Camphene | 1075 | 0.1 | – | – | – | – |
β-Myrcene | 1145 | 0.7 | – | – | – | – |
3-Carene | 1148 | 0.2 | – | – | – | – |
d-Limonene | 1178 | 0.4 | – | – | – | – |
(E)-β-Ocimene | 1242 | 0.9 | – | – | – | – |
(Z)-β-Ocimene | 1245 | 1.2 | – | – | – | – |
o-Cymene | 1274 | 0.2 | – | – | – | – |
Terpinolene | 1286 | 0.2 | – | – | – | – |
Oxygenated monoterpenes | 88.5 | 80.0 | 81.9 | 80.0 | 78.0 | |
Eucalyptol | 1213 | 1.8 | 1.8 | 0.9 | – | 2.1 |
cis-Linalool oxide | 1420 | 1.5 | 1.1 | 1.5 | 0.7 | 0.9 |
trans-Linalool oxide | 1449 | 2.1 | 1.3 | 1.8 | 0.8 | 0.9 |
Camphor | 1491 | 0.4 | 0.5 | – | – | 0.5 |
Linalool | 1537 | 36.3 | 14.5 | 14.6 | 17.3 | 14.8 |
Linalyl acetate | 1569 | 18.2 | 45.6 | 49.6 | 44.3 | 42.5 |
Terpinen-4-ol | 1591 | 4.5 | 2.9 | 3.4 | 4.4 | 3.4 |
Bornyl acetate | 1620 | 0.2 | – | – | – | – |
Lavandulyl acetate | 1609 | 7.9 | 6.2 | 7.1 | 5.8 | 5.2 |
Lavandulol | 1677 | 2.2 | 2.0 | 0.9 | 4.0 | 2.8 |
Borneol | 1677 | – | 4.1 | 2.1 | 2.7 | 4.9 |
α-Terpineol | 1680 | 8.3 | – | – | – | – |
Geranyl acetate | 1711 | 1.3 | – | – | – | – |
Neryl acetate | 1742 | 1.1 | – | – | – | – |
Nerol | 1770 | 0.7 | – | – | – | – |
Geraniol | 1847 | 2.0 | – | – | – | – |
Sesquiterpenes | 1.4 | 7.0 | 7.1 | 6.3 | 7.4 | |
(E)-Caryophyllene | 1594 | 1.4 | 4.6 | 5.1 | 4.5 | 5.0 |
α-Santalene | 1644 | – | 2.4 | 2.0 | 1.8 | 2.4 |
Oxygenated sesquiterpenes | 4.1 | 10.6 | 9.0 | 10.7 | 12.3 | |
Caryophyllene oxide | 1962 | 3.8 | 9.1 | 7.9 | 9.3 | 10.8 |
τ-Cadinol | 2134 | 0.3 | 1.5 | 1.1 | 1.4 | 1.5 |
Other compounds | 2.1 | 2.4 | 1.9 | 2.9 | 2.3 | |
3-Octanone | 1270 | 0.3 | – | – | – | – |
Octenyl acetate | 1380 | 1.0 | – | – | – | – |
Cryptone | 1645 | 0.6 | 1.0 | – | – | 1.1 |
Cuminaldehyde | 1814 | 0.2 | – | – | – | – |
2,6-Dimethyl-3,7-octadiene-2,6-diol | 1940 | – | 1.4 | 1.9 | 2.9 | 1.2 |
a Kovats retention index.
The main components detected in all extracts were linalool and linalyl acetate, known to be mostly responsible for the lavender smell [32]. Interestingly, an inversion of the area ratio between linalool and linalyl acetate can be noted, comparing essential oil and other extracts, with a ratio of 2.00 after HD, 0.32 using n-butane, 0.29 using DME, 0.39 using HFO-1234ze, and 0.35 using n-hexane. As this compound is listed as an allergen in cosmetics and perfume field [33], producing extracts with lower linalool content can be advantageous.
Filly et al. [3] showed that HD has an impact on the chemical composition of lavender essential oil. In particular, linalyl acetate is likely to be degraded into linalool and also into nerol and geraniol during maceration in boiling water [34]. Because the degradation of linalyl acetate is due to an excess of water at high temperature, it is not likely to happen during extractions using organic solvents such as n-hexane, n-butane, and HFO-1234ze. The case of DME is more uncertain, as the solvent has the ability to solubilize both reactants (linalyl acetate + in situ water). However, GC–MS results only showed limited amounts of linalool or others degradation products (nerol, geraniol, α-terpineol, etc.) in the extracts. Therefore, even using DME, the low water content and the gentle extraction temperature prevented the reaction from happening quantitatively.
It must be also noted that no volatile monoterpenes have been detected in maceration extracts (n-hexane or liquefied gases), whereas less volatile sesquiterpenes, such as (E)-caryophyllene, were more efficiently extracted as observed in several studies [35,36]. Interestingly, some known aromatic compounds have been quantitatively found only using solvent macerations such as borneol, associated with balsam, camphor, herbal, woody smells, and α-santalene associated with woody smell. Some known aroma precursors such as 2,6-dimethyl-3,7-octadien-2,6-diol [37] have also been found.
Still, a sensorial analysis is necessary to assess if these variations in the chemical composition have led to differences in the sensorial perception.
3.3.4 Sensory analysis
After the sensorial analysis of the lavender flower extracts, the seven experts checked in total 33 different terms. Thirty percent of these terms were related to “fruity” category, 18% to “aromatic” category, and 15% to “spicy” category. In addition, 12 terms (36%) were cited only once.
Ten terms frequently cited by experts to characterize the set of six lavender extracts were “lavender”, “thyme”, “dry grass/hay”, “pepper”, “food alcohol”, “lemon”, “alcohol solvent/ethanol” and “cut grass”, “menthol”, “greenmenth”. These 10 terms corresponded to 59% of the checked terms. Among these terms, five terms were checked by more than three experts over seven to describe following products: “lavender”, “thyme”, “dry grass/hay”, “pepper”, and “lemon”.
These five terms most frequently checked by more than three olfactory experts were then used to discriminate the products based on their main common characteristics. CA on the frequency-based table (frequencies × products × six most frequently cited terms) shows that the first three dimensions accounted for 97% of the information, from which, the first two dimensions accounted for almost 91% of the variance (73% and 18%, respectively).
Axis one represents the term cut grass and it discriminates the product n-hexane. Axis two represents the term lemon and it opposes the product HFO-1234ze versus HD. The characteristics “pepper” figure is in the third dimension (Fig. 5).
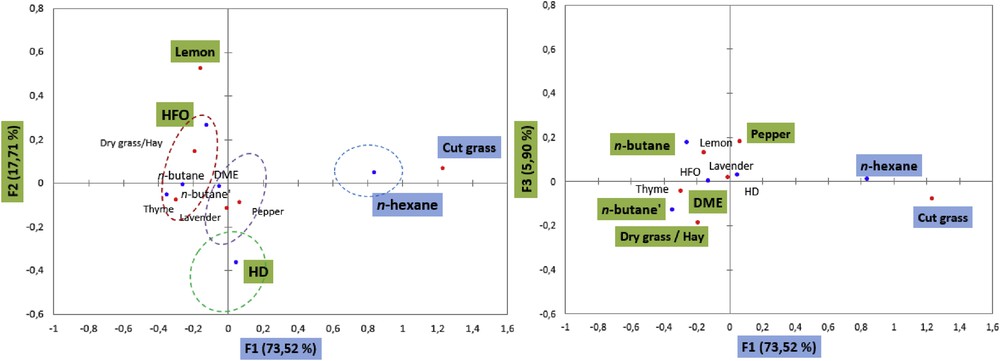
Sensory map for CA of lavender extracts.
An HCA was performed after a CA on the χ2 distance table to help the identification of groups with similar/different sensory profiles and give an idea of product discrimination. Four main groups, G1, G2, G3, and G4, were obtained as shown in Fig. 6. These groups are also shown on the CA plots in Fig. 5. The groups of products were separated mainly along the first dimension of CA, mostly based on odor “grass”. HCA resulted in the same groups of products as CA.
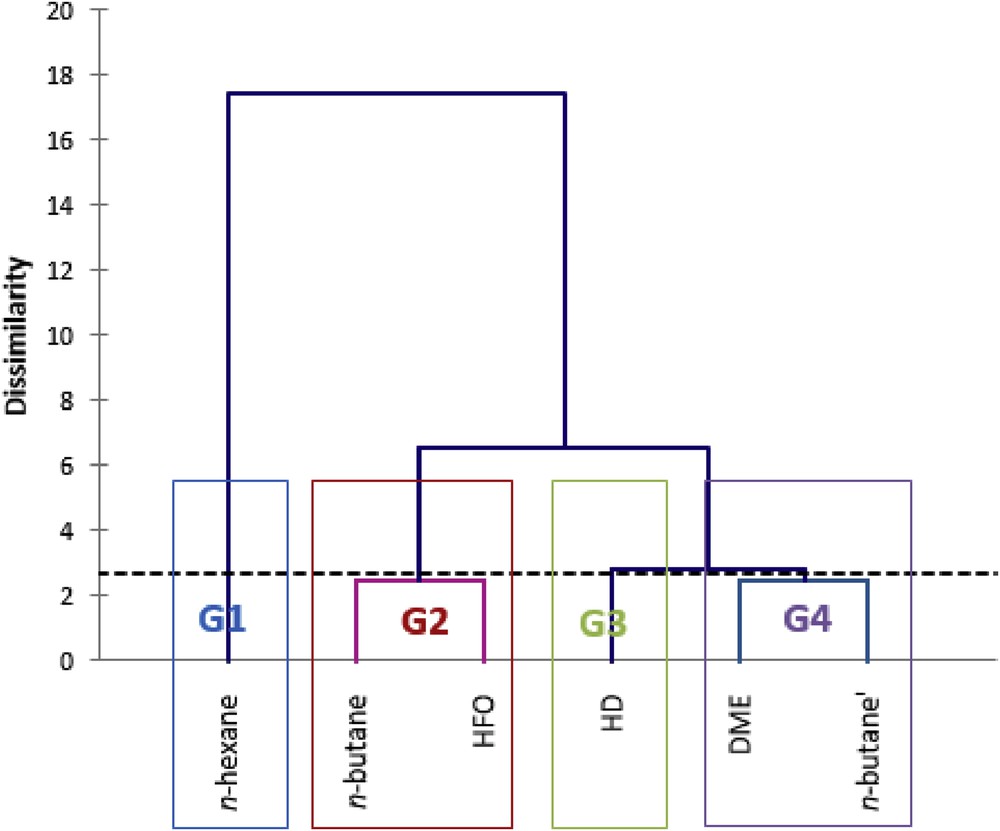
Dendrogram of the HCA after CA.
In conclusion, all the products were very similar in terms of the olfactory profile. The term lavender was checked most frequently and for the entire product set. However, this descriptor was not significant to discriminate the products. The lavender extracted using the n-hexane solvent is the product that differentiates the most from the rest of the products presenting a cut grass odor.
3.4 Quantitative and qualitative comparison of extracts from orange peels
3.4.1 Extraction yields
Table 5 shows the extraction yields obtained from orange peels using liquefied gases, n-hexane, and HD. As orange peels are wet materials, the extracts contained an upper organic phase containing the aromatic compounds and an aqueous phase with hydrophilic compounds. Although HFO-1234ze and n-butane only coextracted a little amount (some milliliters) of in situ water, DME almost fully dried the orange peels. In this study, only organic phases were taken into account in the extraction yield. As observed with lavender flower extracts, HFO-1234ze extraction only resulted in low yield (0.3%); DME gave the best yield (1.1%), whereas n-butane and n-hexane macerations yielded 0.7% and 0.9%, respectively.
Extraction yields obtained with HFO-1234ze, DME, n-butane, and n-hexane from wet orange peels.
Solvent | T (°C) | Time | Extraction yielda (g/100 g SM) | SD |
HFO-1234ze | 25 | 4 × 1 h | 0.3 | 0.1 |
DME | 25 | 4 × 1 h | 1.1 | 0.2 |
n-Butane | 25 | 4 × 1 h | 0.7 | 0.2 |
n-Hexane | 25 | 4 × 1 h | 0.9 | 0.1 |
Water | 100 | 2 h | 0.6 | 0.1 |
a Excluding aqueous phase, if any.
3.4.2 Chemical composition
The repartition of the main compounds of the orange extracts is presented in Table 6. In total 134 compounds were identified with 73 compounds detected in the essential oil, 71 in the n-butane extract, 75 in the n-hexane extract, 80 in the DME extract, and 59 in the HFO-1234ze extract.
Relative abundances of main compounds found in orange peel extracts recovered with different methods.
Compounds | RIa | HD (%) | n-Butane (%) | DME (%) | HFO-1234ze (%) | n-Hexane (%) |
Monoterpenes | 83.2 | 14.4 | 75.5 | 1.9 | 1.1 | |
β-Myrcene | 1145 | 1.9 | 0.2 | 1.5 | – | – |
d-Limonene | 1178 | 80.3 | 13.5 | 73.2 | 1.6 | 0.7 |
β-Phellandrene | 1209 | 0.8 | – | 0.7 | – | – |
Citronellal | 1488 | 0.2 | 0.7 | 0.1 | 0.3 | 0.4 |
Oxygenated monoterpenes | 4.4 | 25.7 | 1.7 | 36.0 | 28.0 | |
Linalool | 1646 | 1.9 | 12.3 | 1.1 | 12.4 | 9.5 |
Neral | 1667 | 0.3 | 0.4 | – | 1.2 | 1.2 |
α-Terpineol | 1688 | 0.8 | 4.5 | 0.1 | 7.0 | 5.1 |
Geranial | 1715 | 0.4 | 0.4 | 0.1 | 1.7 | 2.0 |
Geranyl acetate | 1711 | 0.1 | 1.0 | – | – | 0.2 |
Citronellol | 1762 | 0.2 | 1.3 | – | 2.6 | 2.0 |
Perillaldehyde | 1818 | 0.1 | 1.2 | 0.2 | 0.3 | 0.3 |
Nerol | 1770 | 0.2 | 1.5 | – | 3.6 | 2.7 |
trans-Carveol | 1839 | 0.1 | 0.9 | – | 1.1 | 0.9 |
cis-Carveol | 1846 | – | – | – | 0.8 | 0.6 |
Geraniol | 1847 | 0.2 | 1.3 | – | 2.5 | 1.8 |
Limonen-10-ol | 1996 | 0.1 | 0.9 | – | 1.6 | 1.2 |
8-Hydroxylinalool | 2251 | – | – | 0.2 | 1.2 | 0.5 |
Sesquiterpenes | 1.0 | 3.4 | 2.1 | 1.8 | 1.4 | |
Isocaryophyllene | 1570 | – | – | 1.9 | – | – |
Valencene | 1726 | 1.0 | 3.4 | 0.2 | 1.8 | 1.4 |
Oxygenated sesquiterpenes | 0.4 | 2.4 | 1.1 | 4.6 | 5.2 | |
Caryophyllene oxide | 1971 | 0.1 | 0.6 | – | – | 0.8 |
Intermedeol | 2222 | 0.1 | – | 0.1 | 1.3 | 1.1 |
α-Sinensal | 2268 | – | 0.4 | 1.0 | – | 0.4 |
Nootkatone | 2527 | 0.2 | 1.4 | – | 3.3 | 2.9 |
Triterpenes | – | 4.8 | – | 8.9 | 6.9 | |
Squalene | 2865 | – | 4.8 | – | 8.9 | 6.9 |
Fatty acids | 0.2 | 12.8 | 0.5 | 10.1 | 12.2 | |
Linoleic acid | 3157 | – | 8.1 | – | 6.2 | 8.4 |
Ethyl oleate | 2445 | – | 1.0 | 0.1 | – | 0.2 |
Methyl Linoleate | 2485 | 0.2 | 0.9 | 0.1 | 2.5 | 2.1 |
Methyl linolenate | 2590 | – | 1.0 | – | 0.4 | 0.5 |
Linoleic acid ethyl ester | 2519 | – | 1.8 | 0.3 | 1.0 | 1.0 |
Other oxygenated compounds | 2.0 | 6.0 | 1.0 | 7.4 | 6.1 | |
n-Decanal | 1484 | 1.5 | 2.6 | 0.8 | 1.1 | 1.8 |
1-Octanol | 1553 | 0.4 | – | 0.1 | 2.3 | 1.5 |
Dodecanal | 1710 | – | – | – | 0.8 | 0.9 |
1-Decanol | 1765 | 0.1 | 0.6 | – | 0.9 | 0.9 |
Octyl formate | 1554 | – | 2.4 | – | – | – |
Limonene glycol | 2268 | – | 0.4 | 0.1 | 2.3 | 1.0 |
Other hydrocarbons | – | 3.5 | 4.5 | 6.3 | 6.9 | |
Heptacosane | 2700 | – | 1.1 | 4.5 | 2.1 | 2.6 |
Pentacosane | 2500 | – | 2.4 | – | 4.2 | 4.3 |
a Kovats retention index.
Essential oil obtained by HD is mostly composed of monoterpenes (83.2%) with d-limonene being the major constituent (80.3%) followed by β-myrcene (1.9%) and linalool (1.9%), which are known to be the most important contributors of the orange essential oil aroma [38].
DME extractions also resulted in extracts mainly composed of monoterpenes (75.5%), in particular d-limonene (73.2%), and also long-chain alkanes (4.5%) were found, such as heptacosane (C27H56), usually found on the surface of fruit peels [39]. Major aroma contributors are found in significant amounts (1.5% of β-myrcene and 1.1% of linalool) and also more unusual compounds such as isocaryophyllene (1.9%) or α-sinensal (1.0%).
HFO-1234ze and n-hexane macerations gave similar relative compositions with a very low amount of d-limonene (<2%). Therefore, extracts were composed mainly of terpenoids including oxygenated monoterpenes (36.0% and 28.0%, respectively), oxygenated sesquiterpenes (4.6% and 5.2%), and triterpenes (8.9% and 6.9%). Fatty compounds were also coextracted in significant amounts in particular fatty acids and fatty acid esters (10.1% and 12.2%) and also in long-chain alkanes (6.3% and 6.9%).
Finally, extracts obtained using n-butane resulted in a higher relative amount of monoterpenes as compared with n-hexane extracts, in particular d-limonene (13.5% vs 0.7%).
The low relative abundances of d-limonene observed in extracts obtained using HFO-1234ze and n-butane as compared to the DME extract and essential oil are in accordance with COSMO-RS calculations.
3.4.3 Sensory analysis
After the sensory analysis of the orange peel extracts, the seven experts checked in total 40 different terms. Forty-five percent of these terms were related to fruity category, 10% to spicy category, and 10% to woody category. In addition, 19 terms (35%) were cited only once.
Some of these terms were cited frequently by experts. Among 40 different terms, 11 terms that were cited the most frequently to characterize the set of six orange extracts were “bitter orange”, “sweet orange”, “grapefruit”, “pepper”, “lemon”, “mandarin”, “prune/fig”, “food alcohol”, “dried apricot”, “alcohol solvent/ethanol”, and “honey”. These 11 terms corresponded to 72% of the checked terms.
Among these 11 terms, nine terms were checked by more than three experts over seven to describe a product. These terms were “bitter orange”, “sweet orange”, “grapefruit”, “pepper”, “lemon”, “mandarin”, “prune/fig”, “food alcohol”, and “alcohol solvent/ethanol”.
These nine terms were then used to discriminate the products based on their main common characteristics. CA and HCA analyses were carried out and the product profiles were obtained for each cluster resulting from HCA in the same way as the classic profiles. CA on the frequency-based table (frequencies × products × nine most frequently cited terms) shows that the first four dimensions accounted for 98% of the information, from which the first two dimensions accounted for almost 76% of the variance (47% and 28%, respectively). Further dimensions explained only a small proportion of variance (<5%).
Axis one represents the term “fig/prune” and it opposes the product HFO-1234ze to n-butane. Axis two opposes the terms “grapefruit”, “food alcohol”, and “alcohol solvent/ethanol” to “mandarin”. It opposes the product n-butane versus DME and HD. The other characteristics “pepper” figure is in the third and fourth dimensions (Fig. 7).
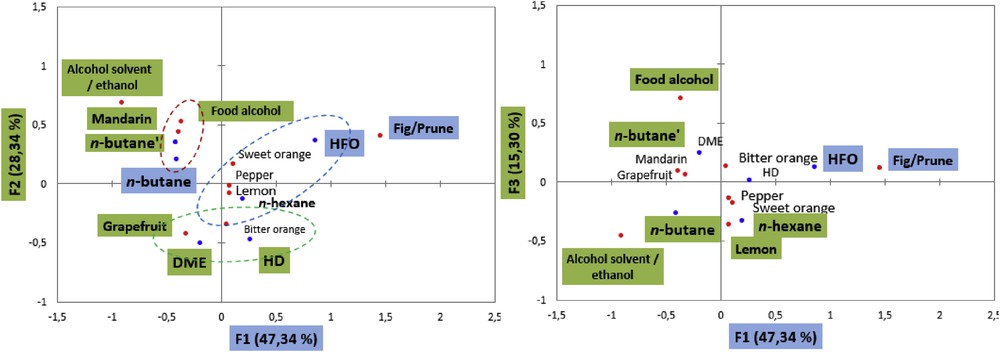
Sensory map for CA of orange peel extracts.
Hierarchical clustering analysis was performed after CA on the chi-square distance table to help the identification of groups with similar/different sensory profiles, and give an idea of product discrimination. Three main groups, G1, G2, and G3, were obtained as shown in Fig. 8. These groups are also shown on the CA plots in Fig. 7. The groups of products were separated mainly along the first dimension of CA, mostly based on odor “grass”.

Dendrogram of the HCA after CA.
The groups of products were separated mainly along the first two dimensions of CA. HCA resulted in the same groups of products as CA.
In conclusion, the products were mainly described by bitter orange and sweet orange. However, we could not discriminate the products based on this descriptor. Orange peels extracted using HFO-1234ze is opposed to the products extracted using n-butane. The panel more efficiently evaluates the duplicate product with a slight difference in the third dimension.
4 Scale-up, regulations, and safety considerations
Even if experiments at an industrial scale using liquefied gases are yet to be performed, a preliminary energetic evaluation of the extraction process was assessed. On the basis of the previously calculated evaporation energy (Table 1), using liquefied gases as solvents allows an energy saving from 8% (DME) up to 60% (HFO-1234ze) as compared to n-hexane, because of a lower vaporization enthalpy.
Considering the scale-up feasibility, which can be difficult for pressurized processes, the moderate operating pressures (<1 MPa) generated by liquefied gases at room temperature make the extraction processes much easier and cheaper to implement at an industrial scale, in comparison with existing pressurized extraction processes such as supercritical CO2. As an example, a 500-L extraction unit was built for industrial scale tests at the “Plateforme d'Eco-Extraction de Valréas” (Fig. 10) based on the same principle of the 1-L pilot unit.
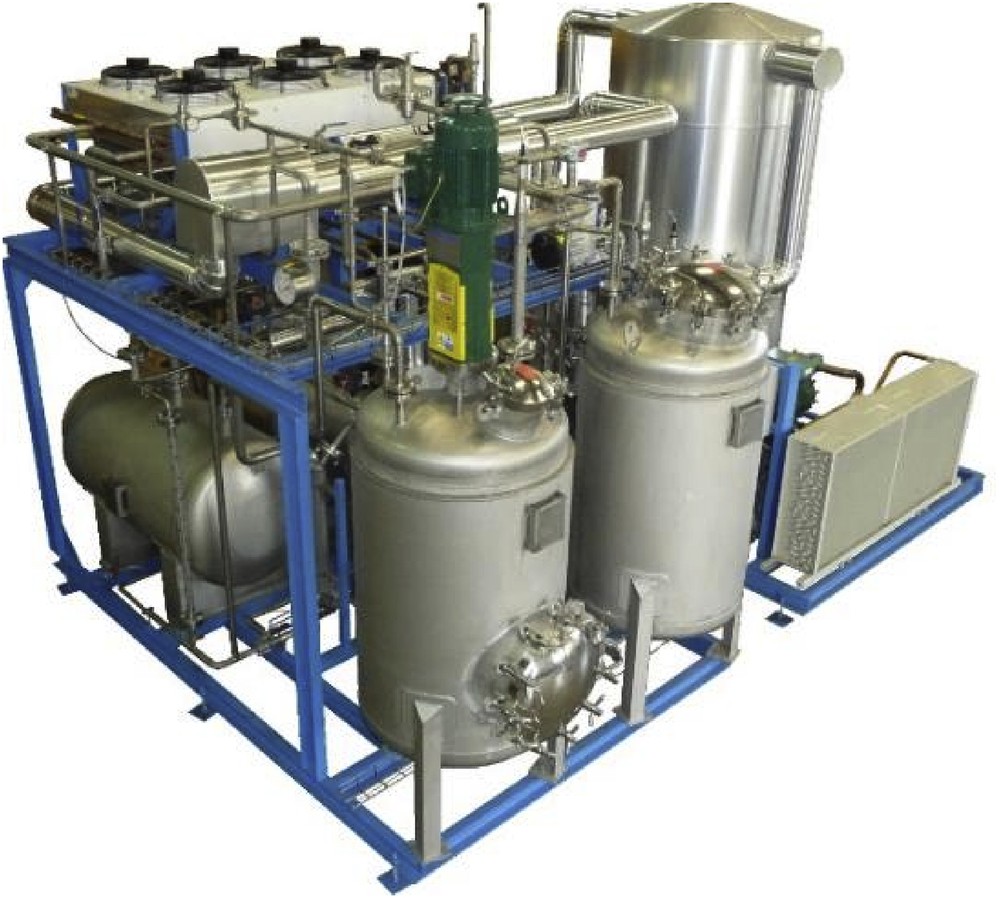
500-L liquefied gas extraction unit NECTACEL manufactured by Celsius sarl (Villette-de-Vienne, France) for the technological plateforme (Plateforme d'Eco-Extraction de Valréas, Valréas, France).
Liquefied gas extraction process is simple and can be readily understood in terms of the operating steps to be performed. Still, the use of new operating conditions generates new risks on product, equipment, and operators.
The major quality impact on the product is related to the solvent/extraction separation. Even if liquefied gases will naturally evaporate, few traces can remain in the product, thus the absence of solvent in the final product must be monitored. On the contrary, traces of extracts may contaminate the recycled solvent. The presence of these contaminants must be carefully checked before reuse and a cleaning protocol must be established to ensure a constant solvent quality.
Regarding the process safety, the main hazards for workers and equipment are mainly generated by the solvent itself. Even if the liquefied gases chosen in this study were selected because of their nontoxicity for humans and environment (Table 1), they have to be maintained under pressure, thus an overheating of the vessels could lead to an unacceptable overpressure and burst. For this reason, all pressurized vessels must be equipped with a safety valve designed to release the overpressure. In addition, because a large amount of liquefied gas is stored in the tanks, a leakage is likely to generate a large volume of asphyxiant gas in the workspace. However, this risk is greatly reduced by working in adequately ventilated rooms equipped with oxygen captors. In the case of flammable solvents (n-butane, n-hexane, and DME), the vessels and pipes containing the solvent must also be located away from any ignition sources, in compliance with existing local regulations [40].
Finally, like any other solvent, liquefied gases must comply with specific regulations when used for the production of foodstuff, cosmetic, or perfumes. In particular, solvents used to produce extracts for the European market must belong to the list of authorized solvents for foodstuff production [41] or on the contrary, must not be part of the list of prohibited substances in cosmetic products [33]. The liquefied gases selected in the present study are not considered as prohibited for cosmetic products; moreover, n-butane is authorized for foodstuff production without any particular restrictions, unlike n-hexane. However, although they are nontoxic, HFO-1234ze and DME are not fully accepted for food applications in Europe, whereas DME is currently undergoing a generally recognized as safe (GRAS) evaluation in the United States [42].
5 Eco-footprint: liquefied gases versus n-hexane
To compare the environmental impact of liquefied gas extraction processes versus a classical n-hexane extraction process, the “eco-footprint” was determined for each solvent, based on the six principles of green extraction defined by Chemat et al. [43]. Graphical representations of the eco-footprints of each liquefied gas are shown in Fig. 9.
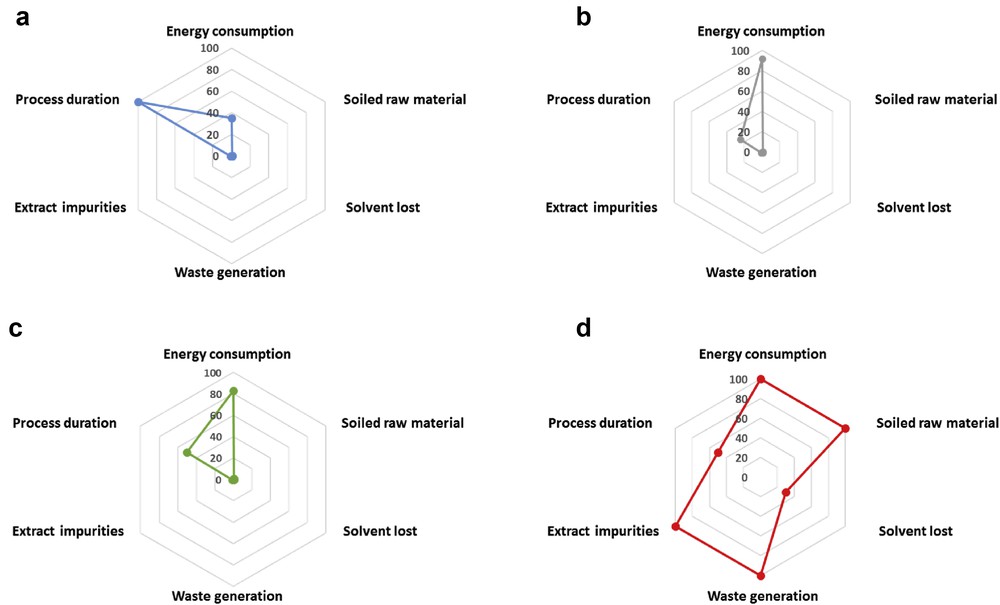
Eco-footprint of liquefied gas extractions using (a) HFO-1234ze, (b) DME, and (c) n-butane when compared with (d) n-hexane maceration.
In terms of process efficiency (principle 5), DME showed the best efficiency with the highest yields for both orange peels and lavender flowers, followed by n-butane and n-hexane. Using the same experimental conditions, extractions with HFO-1234ze resulted in the lowest extraction yields for both, in accordance with previous works [9,26]. However, it must be noted that the experiments in this study have been performed mainly in a qualitative purpose; therefore, the experimental conditions can be optimized to increase significantly the process productivity. Process intensification using ultrasounds to enhance mass transfer or microwave to enhance heat transfer could also be theoretically possible at a laboratory scale but the implementation at the industrial scale seems complex for conception and safety reasons.
Once the extraction step is over, most of the industrial extraction processes try to reuse the exhausted plant material as a coproduct, for example, as livestock feed [44]. However, the resulting plant material obtained after n-hexane extraction must be treated to remove toxic solvent traces and even more if n-hexane is forbidden in the future. Thus, waste generation (principle 4) directly after the extraction step is 100%. On the contrary, liquefied gases are not toxic and left only a few traces of solvent so that plant material can be reused as it is. Consequently, this extraction process does not generate any waste (principle 4) and similarly, the exhausted raw material can be used directly as a coproduct (principle 1). Considering the energy consumption (principle 3), we have seen that liquefied gas extractions can save a significant amount of energy as compared with conventional solvents.
Regarding the solvent (principle 2), the use of liquefied gases allows a fast and complete solvent recovery in one step (more than 99%), whereas usually up to 30% of the n-hexane remained trapped in the raw material and thus required further desolvation steps.
Finally, the extract quality (principle 6) is known to be a crucial aspect of the extraction step. Even if the solvent is supposed to be fully evaporated, traces of solvent are often found in the crude extract. Because of the difference in volatility, due to the difference in boiling point, liquefied gases evaporate more easily than n-hexane, resulting in higher extract purity. An analysis on extracts obtained with a fluorinated liquefied gases with close physicochemical properties (R134a) shows that residual R134a in vegetable extracts is often greatly lower than 1 ppm [45]. On the contrary, n-hexane content in the extracts can easily reach up to 1000 mg/kg [46].
To sum up, using liquefied gases as extraction solvents allows a lower environmental impact because of a lower energy consumption and a better extract quality, without traces of a toxic solvent. As compared with n-hexane, liquefied gases do not generate waste and leave the exhausted material safe for direct valorization. However, the process parameters of liquefied gas extractions still have to be optimized to get a sufficient productivity.
6 Conclusions and perspectives
This study was carried out to compare the performance of three liquefied gases—n-butane, DME, and HFO-1234ze—as green alternative solvents to substitute hexane for the extraction of natural aromatic products. The predictive COSMO-RS calculations showed that DME was better than n-hexane for the solubilization of many aromatic compounds. These predictions were then confirmed by experiments performed at a laboratory scale, as DME resulted in the best extraction yields for both lavender flowers and orange peels, regardless of the water amount. The chemical compositions of the extracts obtained by liquefied gases were significantly different from essential oils obtained by HD, with as expected more fatty compounds and less degradation products. As expected, DME extracted a wide variety of compounds, whereas n-butane and HFO-1234ze extractions resulted in extract compositions similar to n-hexane. Sensorial analysis performed on each extract of lavender flowers and orange peels did not reveal significant differences in the olfactory perception.
Finally, the evaluation of the industrial feasibility regarding technology, quality, safety, and economic and environmental impact tends to prove that liquefied gases could be potential alternatives to conventional toxic solvents as they greatly reduce the number of pretreatment and post-treatment steps and the overall energy consumption of the process.
As future perspectives, some crucial aspects remain to be further investigated. Are the liquefied gases truly chemically inert under the process conditions? Is the solvent recovery fully efficient in terms of quantity and purity? Moreover, this study was carried out using a well-known and easy-to-extract plant material, but further studies should be carried out with plants more difficult to extract, for example, cinnamon in which aromas are found inside the bark [47].
Finally, a life-cycle assessment should be performed on liquefied gases, in particular HFO-1234ze whose production by chemical synthesis [48] and low biodegradability [49] could be a barrier for an industrial use as a green alternative solvent.
Acknowledgments
The authors are grateful to the French organization ANRT (“Association nationale de la recherche et de la technologie”) for funding this work. They are also grateful to Maria Marco, Director of the “Plateforme d'éco-extraction de Valréas” (PEEV) for hosting the experiments.