1 Introduction
Amphiphilic macromonomers usually consist of hydrophilic polymer chains and hydrophobic (co)polymerizable end groups as tails and heads, contrary to the conventional surfactants, and find useful application to emulsion and dispersion polymerization of hydrophobic monomers in water and alcoholic media, respectively [1]. The macromonomers copolymerize in situ with the hydrophobic monomers to afford graft copolymers that serve as effective stabilizers firmly (covalently) attached on the particle surfaces, well represented by the name ‘surfmer’ [2]. Thus the hydrophobic heads of the copolymerized macromonomers act as anchors while the hydrophilic macromonomer tails work as steric stabilizers against flocculation. So far a lot of macromonomers or surfmers have been reported for design of various kinds of polymer microspheres [1–5].
In general, emulsion and dispersion polymerizations produce polymer microspheres of submicron to micron in size. While we have proposed a kinetic model of particle size control in dispersion polymerization using macromonomers [6,7], there has been still not enough information about the mechanism of particle formation and the effects of the macromonomer structure or composition in heterogeneous polymerization system in general. Among others poly(ethylene oxide) (PEO) macromonomers have been of increasing concern in view of relatively easy design of the tail-head structure coupled with a variety of potential applications [1,8,9]. Therefore we have been interested in the project of experimental exploitation of the particle size control by using a systematically structure-designed PEO macromonomers [10]. In this paper we are intended to present some fundamental information about the effect of the tail-head composition of the styryl-ended macromonomers, 1, which have been recently prepared by initiation method as given in Fig. 1 [11].
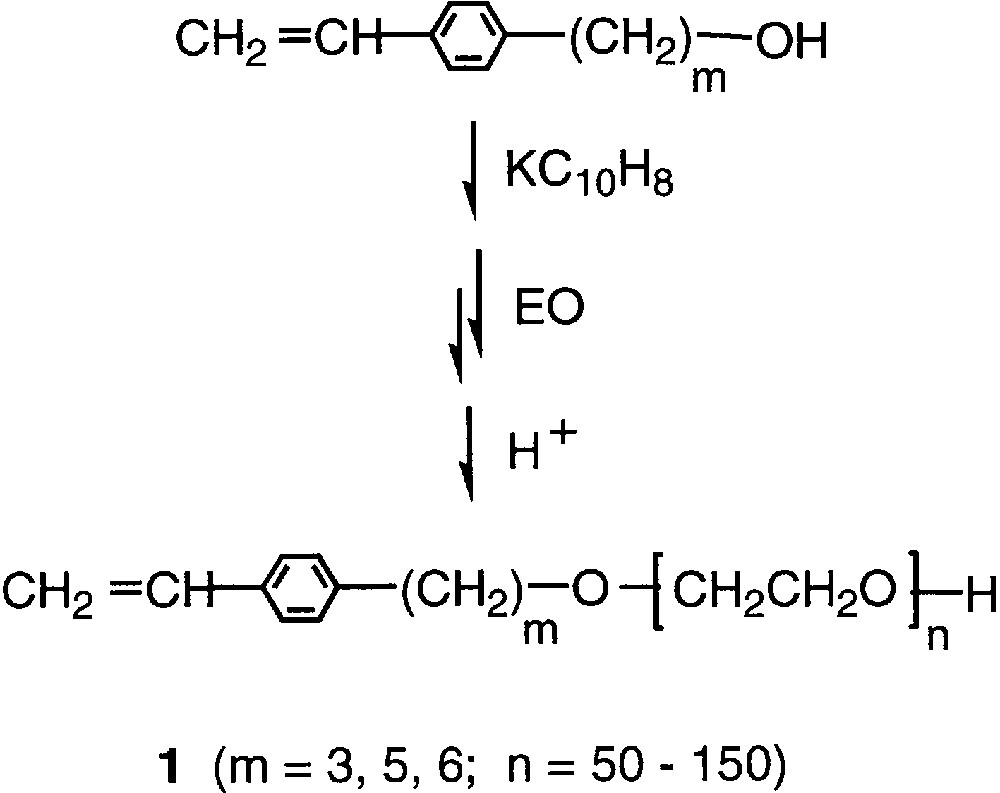
Synthesis of PEO macromonomers by initiation method.
2 Experimental
The PEO macromonomers, 1, listed in Table 1, were prepared by polymerization of ethylene oxide with corresponding p-vinylphenylalkanols partially alkoxidated with potassium naphthalene in tetrahydrofuran, as described in detail [11]. 2,2′-Azobis(isobutyronitrile) (AIBN) and 4,4′-azobis(4-cyanovaleric acid) (AVA) from Aldrich were recrystallized from methanol. Styrene was distilled over calcium hydride under a reduced pressure.
PEO macromonomers used
Entry code a | Mn b | Mw/Mn c |
m3n50 | 2340 | 1.07 |
m3n80 | 3660 | 1.16 |
m3n150 | 6740 | 1.12 |
m5n64 | 2990 | 1.10 |
m6n50 | 2430 | 1.24 |
a The numbers following m and n stand for the alkylene and PEO chain lengths, respectively in structure 1.
b Number-average molecular weight determined by 1H NMR.
c Determined by SEC calibrated with standard poly(ethylene glycol)s.
Emulsion polymerization of styrene in the presence of the PEO macromonomers was conducted at 65 °C in water with AVA as an initiator. Typically, 1 g of styrene, 10 mg of AVA, 10 ml of water, and a desired amount of the macromonomer were charged into a round-bottomed glass tube with a magnetic stirrer tip. The tube was degassed three times by freeze-thaw in vacuum, sealed off, and placed in a heated bath and stirred magnetically for one day. The average size and distribution were analyzed for one hundred particles in the SEM (scanning electron microscopy) photograph taken after dilution with methanol. Conversion of styrene was determined by gravimetry [12]. The particles were purified by centrifugal separation with methanol to remove the unreacted monomers, together with, if any, homopolymers of the PEO macromonomers. Removal of the unreacted macromonomers was confirmed by SEC (size-exclusion chromatography). Their composition was estimated by 1H NMR measured in CDCl3 from the peak intensity ratio of the phenyl to oxyethylene protons. Dispersion polymerization was similarly conducted but at 60 °C in methanol-water mixture (9:1 v/v) with AIBN as an initiator.
Measurements of 1H NMR (Mercury Varian 300), SEC (JASCO), and SEM (Hitachi S-2300) were carried out as described before [11–13].
3 Results and discussion
3.1 Theoretical consideration
We assume a core-shell structure for the polymer microspheres obtained by polymerization of excessive amount of a substrate monomer in the presence of small amount of a macromonomer [6,7]. Then the core should essentially consist of the substrate monomer polymerized and its volume in average is given by:
(1) |
(2) |
(3) |
As expected, Eq. (3) predicts that the particle size decreases with increasing coverage of the macromonomers on the particle surfaces, i.e., with an increase in the ratio of the macromonomer to the substrate monomer polymerized, (WDo θD)/(WSo θS) or mD/mS, and in the specific surface coverage of the macromonomer chain, S, on the surface. A problem is that S is not constant but varies with conversion according to the conformation change of the macromonomer chains tethered to the particle surface. Based on the kinetic simulation together with the homogeneous nucleation mechanism by Paine [14], we proposed an equation for the particle size in dispersion copolymerization [6,7]:
(4) |
3.2 Emulsion polymerization
Styrene plus 1 to 10 wt% PEO macromonomers, 1, with an initiator, AVA, could be readily emulsified in water under magnetic stirring. Heating to 65 °C quickly afforded polystyrene latex nearly quantitatively in weight after one day. Typical SEM photographs, recipe, and result of characterization are given in Figs. 2a and b , and Table 2. Particle size (radius, R) as a function of the macromonomer concentration, WDo, is shown in double logarithmic plots in Fig. 3 .
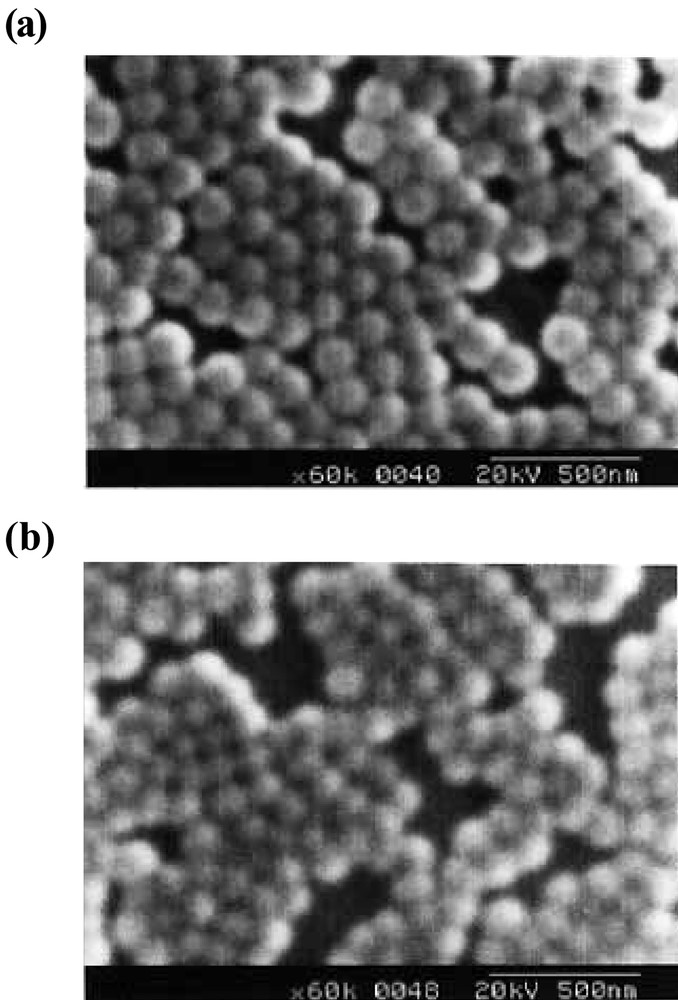
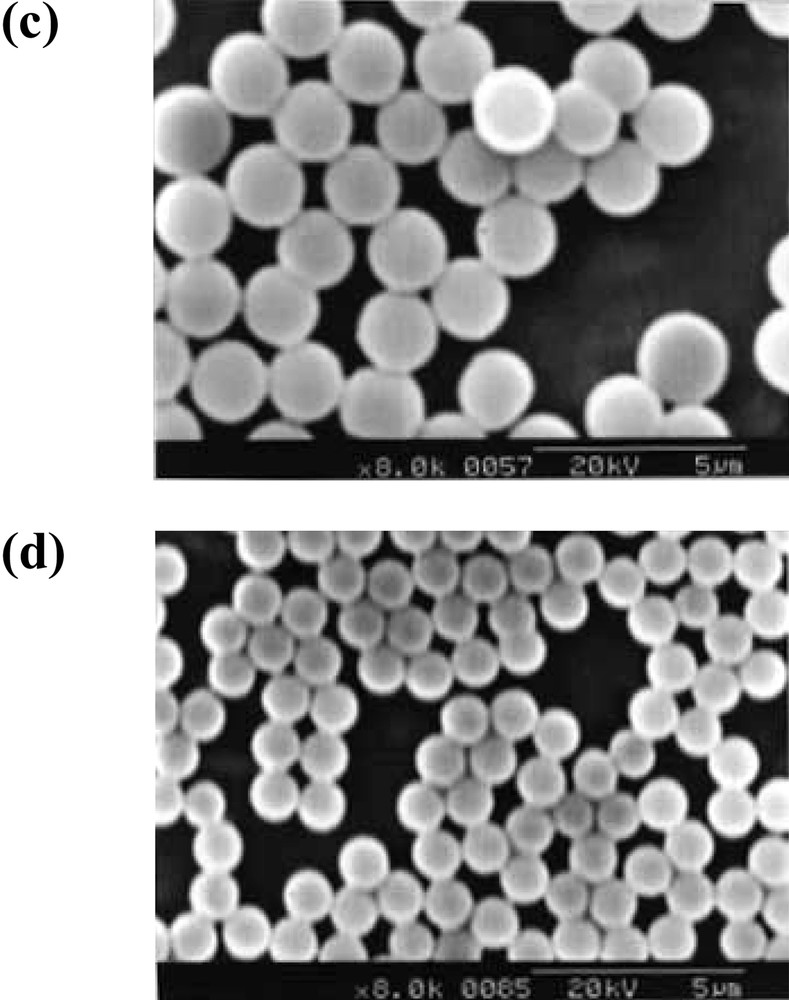
Typical SEM photographs of the polystyrene microspheres obtained by emulsion (a, b) and dispersion (c, d) copolymerization with m3n50. WSo/WDo: (a) 14.3, (b) 10.0, (c) 19.8, (d) 10.0.
Emulsion copolymerization of styrene with PEO macromonomers a
Macromonomer code | WSo/WDo (g g–1) | Dnb (nm) | Dw/Dnb | mS/mDc (mol mol–1) | Sd (nm2) | <Rg>e (nm) | θS/θDf |
m3n50 | 91.0 | 1370 | 1.008 | 2200 | 1.7 | 0.73 | 1.1 |
m3n50 | 14.3 | 220 | 1.025 | 570 | 2.7 | 0.93 | 1.8 |
m3n50 | 10.0 | 181 | 1.015 | 440 | 2.6 | 0.90 | 1.9 |
m3n80 | 97.3 | 1450 | 1.052 | 8100 | 5.8 | 1.4 | 2.3 |
m3n80 | 25.3 | 292 | 1.011 | 1410 | 5.0 | 1.3 | 1.5 |
m3n150 | 104.0 | 1405 | 1.045 | 10500 | 7.8 | 1.6 | 1.5 |
m3n150 | 14.1 | 169 | 1.014 | 1390 | 7.6 | 1.7 | 1.5 |
a Feed: styrene (WSo) = 1 g, AVA = 10 mg, water = 10 ml. Temperature: 65 °C. Polymerization time: 24 h. Styrene conversion: nearly quantitative (θS = 1).
b Dn and Dw: number- and weight-average particle diameter from SEM.
c Styrene/macromonomer mole ratio in particle from 1H NMR.
d Cross-sectional area per macromonomer chain on particle surface from R = Dn/2 and mS/mD with Eq. (3), with MS = 104 and assuming ρ = 1 g cm–3.
e Average radius of gyration of each macromonomer chain occupying the cross-sectional area on particle surface: <Rg> = (S/π)1/2.
f Ratio of conversion of styrene to macromonomer: θS/θD = (mS MS/mD MD) (WDo/WSo).
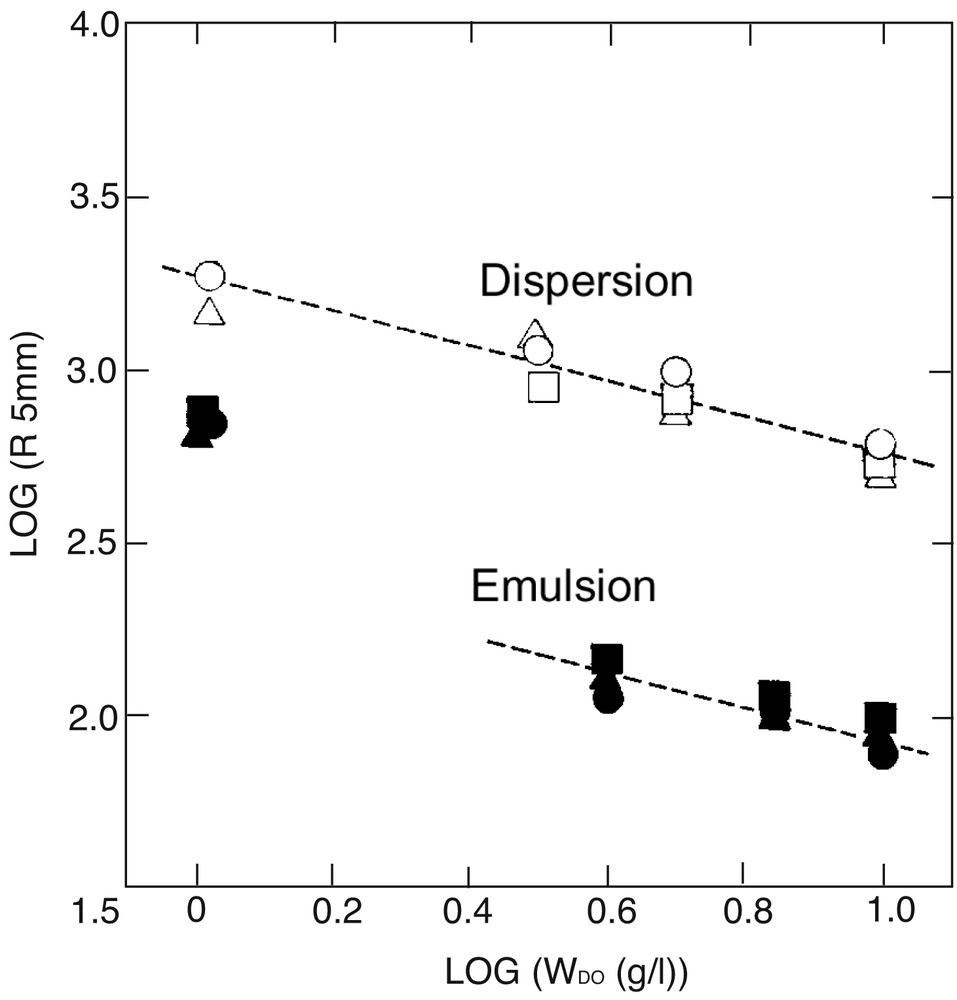
Double logarithmic plots of particle radius vs macromonomer concentration in dispersion (○,▵,□) and emulsion (●,▴,■) copolymerization of styrene with PEO macromonomers with various chain lengths: (○,•) m3n50, (□,■) m3n80, (▵,▴) m3n150. Broken lines are reference with a slope of –1/2.
Nearly mono-sized microparticles were obtained in the range of micron to submicron in diameter depending on the increasing macromonomer level from 1 to 10 wt%. Fig. 3 clearly shows that the size is almost one or half-order of magnitude smaller than that in dispersion copolymerization in methanol-water mixture (9:1 v/v), when compared at the same macromonomer concentration in weight. Also it appears that the size decreases according to inverse root of the macromonomer concentration (WDo–1/2), just like Eq. (4) in dispersion copolymerization, except for the data at the lowest one (1 wt %). The last fact suggests a homogeneous nucleation mechanism, as assumed previously for such a rather hydrophilic PEO macromonomer [10].
To be noted in Fig. 3, the particle size appears to be controlled almost consistently by the weight, not by the number (mole), of the macromonomer. Thus, the PEO chain length, n, appears to have little effects on the particle size. This result can be expected because, in Eq. (3), the increase in n or the molecular weight, MD, of the macromonomer will decrease its incorporation in molar basis, mD, and correspondingly increase the specific surface coverage, S, occupied by that chain on the surface, as can be seen in Table 2.
The values of S or its corresponding radius, <Rg>, reflect the size of each macromonomer chain tethered on the particle surface. These values are significantly smaller as compared to those of the free PEO chains with the corresponding molecular weights. Thus for a random coil conformation in water at 25 °C [16], a PEO chain with a weight-average molecular weight, Mw, will have the square-root radius of gyration:
(5) |
The conversion ratio of styrene to the macromonomer, θS/θD in Table 2, estimated from the particle composition, reveals that θD is much higher than that in dispersion system (Table 3). Indeed, roughly azeotropic incorporation (θS/θD = 1) was observed in case of micellar and emulsion copolymerization with a more hydrophobic PEO macromonomer (m = 7 and n = 17 with ω-end group = OCH3) [10,12]. Such a behavior may even suggest a type of ‘mini-emulsion’ mechanism [18,19] for the present emulsion copolymerization, since almost all the macromonomers charged not only effectively emulsified the initial styrene droplets but also appear to continue to stabilize the final polystyrene particles as such by covering with the graft copolymers produced in situ. Further study including the droplet size measurements is needed to confirm a clear mechanism. Anyway the macromonomers may appear to work as effective steric stabilizers throughout to protect the droplets and the so produced particles against flocculation.
Dispersion copolymerization of styrene with PEO macromonomers a
Macromonomer code | WS0/WD0 (g g–1) | Dnb (nm) | Dw/Dnb | mS/mD (mol mol–1)c | Sd (nm2) | <Rg>e | θS/θDf |
m3n50 | 19.8 | 1940 | 1.004 | 1520 | 0.8 | 0.51 | 3.4 |
m3n50 | 10.0 | 1190 | 1.002 | 1170 | 1.0 | 0.57 | 5.2 |
m3n80 | 31.2 | 1760 | 1.004 | 5000 | 3.0 | 0.97 | 4.5 |
m3n80 | 19.8 | 1620 | 1.002 | 4700 | 3.1 | 0.98 | 6.7 |
m3n150 | 33.0 | 2500 | 1.007 | 9700 | 4.0 | 1.1 | 4.5 |
m3n150 | 20.3 | 1550 | 1.003 | 7800 | 5.2 | 1.3 | 5.9 |
a Feed: styrene (WSo) = 1 g, AIBN = 20 mg, methanol–water (9:1 v/v) = 10 ml. Temperature: 60 °C. Polymerization time: 24 h. Styrene conversion: nearly quantitative (θS = 1).
b Dn and Dw: number- and weight-average particle diameter from SEM.
c Styrene/macromonomer mole ratio in particle from 1H NMR.
d Cross-sectional area per macromonomer chain on particle surface from R = Dn/2 and mS/mD with Eq. (3), with MS = 104 and assuming ρ = 1 g cm–3.
e Average radius of gyration of each macromonomer chain occupying the cross-sectional area on particle surface: <Rg> = (S/π)1/2.
f Ratio of conversion of styrene to macromonomer: θS/θD = (mS MS/mD MD) (WDo/WSo).
As shown in Fig. 4 , the effect of the spacer alkyl length, m, in the polymerizing end group of the macromonomer on the particle size appears also insignificant in the emulsion system, though the data are somewhat scattered to say conclusively.
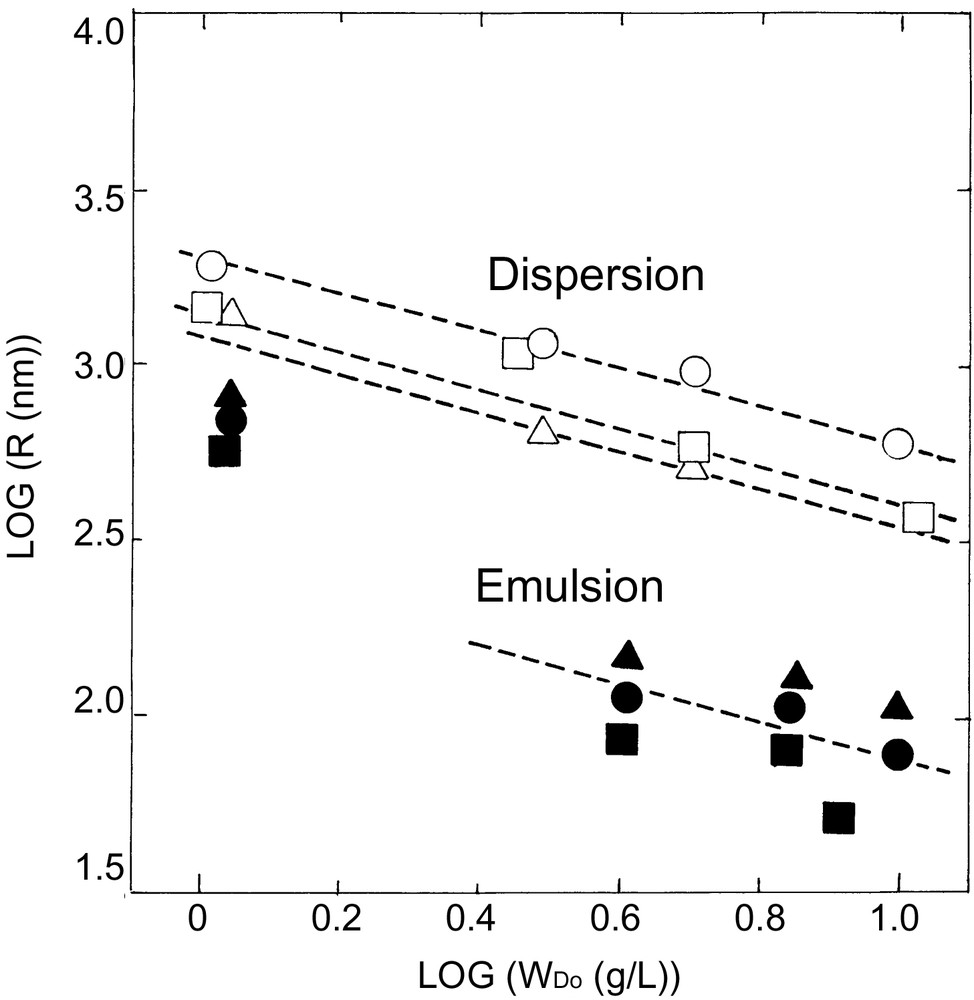
Double logarithmic plots of particle radius vs macromonomer concentration in dispersion (○,▵,□) and emulsion (●,▴,■) copolymerization of styrene with PEO macromonomers with various spacer alkyl lengths: (○,•) m3n50, (□,■) m5n63, (▵,▴) m6n50. Broken lines are reference with a slope of –1/2.
3.3 Dispersion polymerization
Clear solution containing styrene and 1 to 10 wt% PEO macromonomers, 1, with AIBN in methanol/water mixture (9:1 v/v) quickly changed turbid upon heating to 60 °C with magnetic stirring. Polystyrene latex was obtained nearly quantitatively in weight after one day. Typical results are given in Table 3, with the SEM photographs in Fig. 1c and d, and the dependence of the particle size on macromonomer concentration in Figs. 3 and 4.
Nearly monodisperse, micron-sized microspheres were obtained while the dependence of the particle size on the macromonomer concentration, Fig. 3 and 4, is in accord with the theory in Eq. (4), i.e., R ∝ WDo–1/2 over the whole concentration range investigated, WDo = 1–10 g L–1 (1–10 wt% to styrene). The much larger size in the dispersion system, as compared to the emulsion system, can be related to the much less incorporation (smaller mD or θD) coupled with smaller surface coverage (S or <Rg>) of the macromonomers copolymerized in the particles, as can be seen by comparison of Tables 2 and 3.
We can suppose in the dispersion system [6,7] that excessive molar amounts of styrene and the macromonomers dissolved molecularly in methanol-water (9:1 v/v) mixture will polymerize and/or copolymerize to give insoluble polystyrenes and styrene-rich copolymers, which will coalesce together to originate the sterically stabilized microparticles, which will in turn grow in size by polymerization and copolymerization of the monomers. Here styrene appears to be more easily occluded in the particles because the incorporation of the macromonomers will be hindered sterically by the already grafted PEO chains covering the surface. As a consequence, the final particles characterized by small mD or θD (large mS/mD or θS/θD) will result with larger size as compared to the emulsion system. Here it is to be noted that the values of S or <Rg> in the dispersion system are appreciably smaller but substantially in the same level as compared to those in the emulsion system. In fact, free PEO polymers exhibited random conformations with the same molecular size, <Rg>random, in methanol and in water [16]. The presence of –OH end group in the present macromonomers may lead to somewhat larger <Rg> or S in the aqueous emulsion system.
Concerning the very little effect of the PEO chain length, n, of the macromonomer on the particle size, R, as observed in Fig. 3, can be explained by considering Eqs. (4) and (5), which are combined with Scrit = Srandom to give the relation: R ∝ MD–0.08.
The spacer alkyl length, m, of the macromonomer also appears to have little effects on R (Fig. 4), but some trend of smaller size with increasing m may reflect increasing copolymerizability of the macromonomer to styrene (smaller r1) in nucleation stage.
4 Conclusion
PEO macromonomers, 1, with various chain lengths, m = 3, 5, 6 and n = 50–150, were found to be effective in emulsion and dispersion copolymerization with styrene to afford nearly monodisperse microspheres of submicron to micron size. The smaller particle size in the emulsion system can be a result of higher copolymerizability and larger surface coverage of the macromonomers in water as compared to the dispersion system in methanol–water (9:1 v/v). More detailed mechanism, particularly of nucleation in the emulsion system, whether homogeneous or droplets, still remains to be studied. In the emulsion system in Figs. 3 and 4, the upward deviation (or higher slope) observed in log R vs log WDo plots at the lowest WDo may suggest possible change in nucleation mechanism, say, from homogeneous to droplets.