1 Introduction
Reduction is one of the most fundamental and useful reactions in organic chemistry. There must be few organic syntheses, of any complexity, that do not involve a reduction at some stage. Reduction by hydride transferring agents has been used widely in organic synthesis by the well-known alkali metal borohydrides, NaBH4, LiBH4, and their modified forms [1–4]. There are few reports in the literature on the use of the covalent transition-metal borohydride complexes as reducing agents because such compounds are volatile unstable solids and as such cannot be used in organic synthesis [5]. The modified stable forms of such compounds were reported as (Ph3P)2CuBH4 [6], [(Ph3P)2CuBH3CN]2 [7], and (C5H5)2Zr(Cl)BH4 [8]. Zinc borohydride and the stable modified complex forms of this reagent have been reported as being used frequently in reduction reactions [9].
The immobilization of reagents on the polymeric backbone has been investigated extensively [10,11]. This is primarily because insoluble polymeric reagents expand the range of the applicable solvents, increase the easiness of work-up and product purification and isolation and in most cases provide for recovery and regeneration of the supported reagent.
Pyridine borane has been introduced into organic chemistry years ago [12]. Hallensleben reported the preparation of poly(4-vinylpyridine borane) and its action as a polymeric reducing reagent [13]. Polymer-supported borohydride resins (PSBR) have received considerable attention in recent years and some of them have been used in the mild and selective reduction of organic compounds [14]. These reagents have been used in a number of organic transformations [15]. Tamami et al. reported the stabilization of chloroaluminum borohydride [16,17], zinc borohydride [18,19], and zirconium borohydride [20] on poly(4-vinylpyridine) and their uses as new stable polymeric reducing agents. Very recently, in continuation of our studies on the development of new catalysts and methods for organic transformations [21–24], we wish to report the preparation and characterization of the poly(1,4-butyl-bis-vinylpyridinium) borohydride and the uses of this new polymeric reducing agent for a variety of carbonyl reductive transformations.
2 Experimental
2.1 General
The chemicals were purchased from Fluka AG, Merck and Synthetic Chemicals Ltd. Poly(4-vinylpyridine) cross-linked with 2% divinylbenzene was purchased from Fluka AG. All reduction products were known compounds and they were identified by comparison of their spectra and physical data with those of the authentic samples [25]. Reaction monitoring and purity determination of the products were accomplished by TLC or GC-MS on an Agilent GC-Mass-6890 instrument under 70 eV conditions. IR and FTIR Spectra were obtained using a PerkinElmer spectrometer 781 and a Bruker Equinox 55 using KBr pellets (for solids) or neat liquid samples in the 4000–400 cm−1 range. The UV spectra were recorded with an Agilent 8453 UV–vis spectrophotometer at room temperature. In all cases, the 1H NMR spectra were recorded with a Bruker Avance 400 or 300 MHz instrument. 13C NMR data were collected with a Bruker Avance 100 or 75 MHz instrument. All chemical shifts are quoted in parts per million (ppm) relative to TMS using a deuterated solvent. Microanalyses were performed on a PerkinElmer 240-B microanalyzer. The melting points were recorded on a Büchi B-545 apparatus in open capillary tubes.
2.2 Preparation of poly(1,4-butyl-bis-vinylpyridinium) chloride
Cross-linked poly(4-vinylpyridine) [poly(4-vinylpyridine) cross-linked with 2% DVB ∼ 60 mesh, MW: 60,000; Fluka Chemicals] (5.0 g) was suspended in sulpholane (50 mL) and allowed to swell for about 24 h at room temperature (Scheme 1). To this suspension, freshly distilled 1,4-dichlorobutane (DCB) (4 mL) was slowly added and the reaction mixture was stirred under a stream of N2 at 50 °C for 48 h. An additional portion of DCB (2 mL) was added and stirred at the same temperature for 24 h. The precipitate was then filtered, washed with distilled water (5 × 10 mL) and diethyl ether (3 × 5 mL) to remove the unreacted DCB, and then was dried in the presence of P4O10 under vacuum at 50 °C overnight to give the product (6.88 g). The amount of chloride was determined by gravimetric and potentiometric titration methods [26], and was 5.9 mmol Cl per gram of polymer.
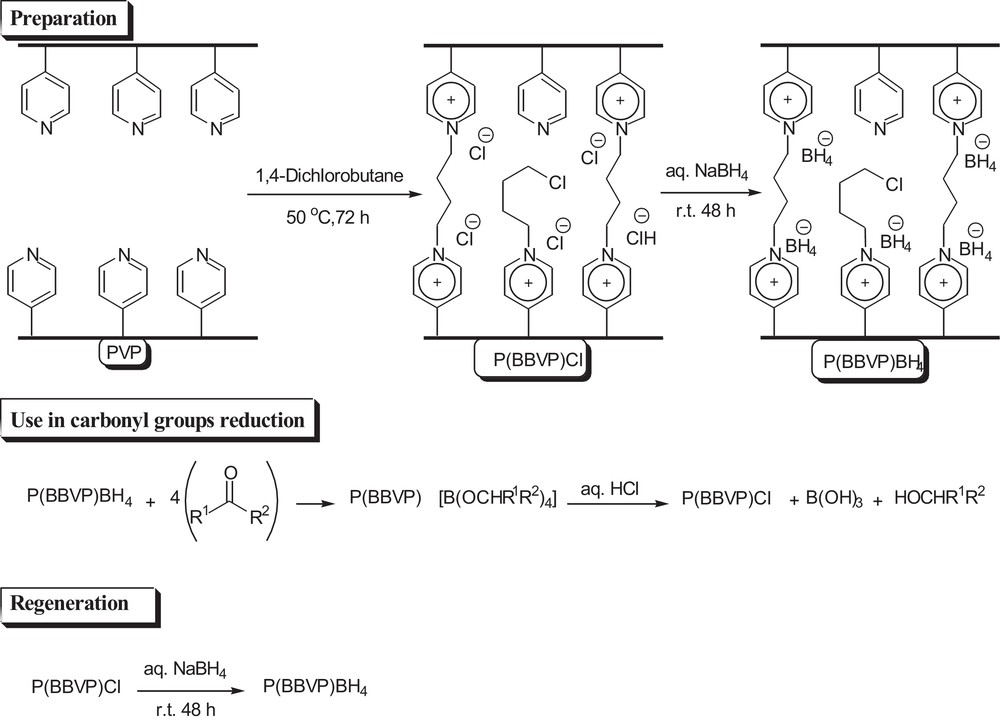
Preparation, use, and regeneration of poly(1,4-butyl-bis-vinylpyridinium) borohydride.
2.3 Preparation of poly(1,4-butyl-bis-vinylpyridinium) borohydride P(BBVP)BH4 (Scheme 1)
To a solution of NaBH4 (4.25 g, 112 mmol) in water (100 mL), P(BBVP)Cl (5.0 g) was added portionwise at room temperature and stirred for 48 h. The resulting material was separated and washed with distilled water (5 × 10 mL) and diethyl ether (2 × 10 mL), then dried in a vacuum desiccator in the presence of P4O10 at 50 °C overnight to obtain the powder of P(BBVP)BH4 (4.39 g). The average capacity of the reagent, determined by hydrogen evolution on acidification with 1.0 M hydrochloric acid in a suitable hermetic apparatus, was found to be 5.8 mmol of borohydride per gram of polymeric reagent.
2.4 General procedure for the reduction of carbonyl compounds with P(BBVP)BH4 (Scheme 1)
To a solution of the substrate (1 mmol) in ethanol as a solvent (5 mL) in a round-bottom flask (25 mL) equipped with a magnetic stirrer, P(BBVP)BH4 (50 mg ∼ 0.29 mmol BH4) was added and stirred at room temperature. The progress of the reaction was monitored by TLC. On completion of the reaction, the mixture was filtered and the used reagent was washed with ethanol (2 × 5 mL). The combined filtrates were evaporated and the pure product was obtained in moderate to excellent yield. In a few cases, when the reaction was not complete, the crude product was purified on silica gel with an appropriate eluent.
2.5 Regeneration of cross-linked P(BBVP)BH4 (Scheme 1)
The utilized polymeric reagents (5.00 g) collected from different experiments were washed successively with hydrochloric acid (1.0 M, 2 × 10 mL), NaHCO3 (2.0 M, 4 × 10 mL), distilled water (2 × 10 mL) and ether (2 × mL). The solid was dried under vacuum at 50 °C to give the original polymer (4.87 g) as a powder precipitate, which was stirred with sodium borohydride to provide the initial polymeric reducing reagent.
3 Results and discussion
The structure of poly(1,4-butyl-bis-vinylpyridinium) borohydride was identified by IR [27] and elemental analysis. Fig. 1 presents the FTIR spectra of poly(4-vinylpyridine) (PVP) and poly(1,4-butyl-bis-vinylpyridinium) borohydride P(BBVP)BH4. The characteristic absorption bands observed in the reagent's spectra in the range between 2923 and 2858 cm−1 could be ascribed to methyl (CH) stretching vibration absorption peaks, due to the 1,4-dichlorobetane cross-linking agent. P(BBVP)BH4 shows a strong vibration frequency at about 2380–2227 cm−1, attributed to the BH stretching (νBH), and another distinctive vibration at 1126 cm−1 assigned to the HBH deformation (δHBH), and characteristic of the BH4− group [14a,b,28]. The νBH bands are split into three peaks, around 2380, 2293 and 2227 cm−1 respectively, which have been assigned to the stretching of the terminal hydrogen–B. In all spectra, a CN band of pyridine, usually at 1600 cm−1, is displaced to higher wave numbers (1650 cm−1) due to quaternisation [27]. Other vibrations of interest are at 1451 cm−1 and 1419 cm−1 respectively; they have been assigned to CC/NC.

FTIR spectra of poly(4-vinylpyridine) (top) and poly(n-butyl-4-vinylpyridinium) borohydride (bottom).
P(BBVP)BH4 was subjected to elemental analysis (Table 1). According to elemental analysis, it can be seen that the exchange of chloride ions with BH4− was done with 100% conversion.
Data of elemental analysis of the initial polymer and modified poly(4-vinylpyridine).
Entry | Compounds | Calcd% | Found% | Conversion% | ||||||
C | H | N | Cl | C | H | N | Cl | |||
1 | PVP | 80.28 | 6.71 | 13.01 | – | 80.14 | 6.64 | 13.22 | – | – |
2 | P(BBVP)Cl | 64.52 | 6.54 | 8.18 | 20.75 | 68.48 | 6.58 | 9.39 | 15.54 | 64 |
3 | P(BBVP)BH4 | 73.30 | 10.09 | 9.29 | – | 75.34 | 9.21 | 10.32 | – | 63 |
We believe it is very unlikely that all the dihalides react at both ends; therefore, we suppose that three types of the reducing agents can be existing in the final polymer-supported borohydride resin (Scheme 2).

The proposed reducing agents in this polymer-supported borohydride resin.
It is known that solvents can play an important role in the stability, reducing power, and selectivity of borohydride reagents in reduction reactions [4,29]. It is also known that for using a polymeric reagent in an organic reaction, a solvent should be chosen in which it can swell to a considerable extent [10]. The degree of swelling was as follows: 1.0 g dried reagent was swollen in 100 mL solvent at 25 °C for 1 h. The degree of swelling, S, was estimated as S = (Ms − Mi)/(ρMi), where Mi is the weight of initial dry reagent, Ms is the weight of the swollen reagent, and ρ is the density of solvent.
The swelling behavior of P(BBVP)BH4 was revealed by the degree of swelling in Table 2. The quaternarization of the pyridyl ring enabled the polymer to swell in ethanol, besides water. The order of swelling was water > methanol > ethanol > diethyl ether, the degree of swelling increased with the polarity of solvent. The high degree of swelling in water shortened the time of ion-exchange for the preparation and regeneration of P(BBVP)BH4. The difference of swelling behavior in different solvents helped to select solvent or mixed solvent so as to control the pore size and the rate of the reaction, and increase chemoselectivity. It seems that the cross-linking of the reagent reduces mobility and swelling.
The degree of swelling of P(BBVP)BH4 in different solvents.
Solvent | H2O | EtOH | MeOH | Et2O |
Degree of Swelling (%) | 4.5 | 0.8 | 1.1 | 0.07 |
As it can be seen in Fig. 2, the P(BBVP)BH4 resin was substantially more stable solvolytically than either sodium or tetraethylammonium borohydride in 100% ethanol (pH = 5.1) and water (pH ∼ 6.8). The final pH values were greater than the initial one.

Stability of P(BBVP)BH4 resin, NaBH4 and Et4NBH4 in 100% ethanol (top graph) and in water at pH = 7 (bottom graph) at room temperature.
Considering these facts, the solvent optimization for each carbonyl group reduction was attempted using different solvents and ethanol proved to be the best one. In ethanol, the polymeric reagent was completely insoluble and boron moieties before and after the reduction remained firmly bound to the insoluble polymeric support. Product isolation and purification were performed simply by filtration of the reaction mixture, evaporation of the solvent, and if necessary, further separation of the starting material by column chromatography.
Table 3 shows the reduction of various carbonyl compounds with P(BBVP)BH4. This reagent reduced aldehydes (1 mmol) into their corresponding alcohols in high yields (50 mg ∼ 0.29 mmol) in the mentioned times. The ketones were also reduced into their corresponding alcohols in good yields using higher amounts of the reducing agent (70–100 mg ∼ 0.40–0.58 mmol) and longer reaction times. Therefore, the reagent was chemoselective towards the reduction of aldehydes with respect to ketones. The selective 1,2-reduction of α,β-unsaturated carbonyl compounds without disturbing the carboncarbon double bond is a frequent problem encountered in synthesis and it has stimulated considerable interest in the development of new reagents and methods [4]. As shown in Table 3, the polymeric reagent showed a complete regioselectivity in the reduction of α,β-unsaturated aldehydes as well as of ketones.
The reduction of different types of carbonyl compounds with P(BBVP)BH4a.
Entry | Substrate | Product | Time (min) | Yield (%)b |
1 | C6H5CHO | C6H5CH2OH | 50 | 96 |
2 | 4-CH3O-C6H4CHO | 4-CH3O-C6H4CH2OH | 45 | 98 |
3 | 4-(CH3)2N-C6H4CHO | 4-(CH3)2N-C6H4CHO | 45 | 98 |
4 | 1,2-C6H4(CHO)2 | 1,2-C6H4(CH2OH)2 | 45 | 88 |
5 | 1,3-C6H4(CHO)2 | 1,3-C6H4(CH2OH)2 | 40 | 94 |
6 | 1,4-C6H4(CHO)2 | 1,4-C6H4(CH2OH)2 | 35 | 95 |
7 | 4-NO2-C6H5CHO | 4-NO2-C6H5CH2OH | 30 | 94 |
8 | 2-NO2-C6H5CHO | 2-NO2-C6H5CH2OH | 30 | 95 |
9 | 2-HO-C6H5CHO | 2-HO-C6H5CH2OH | 60 | 80 |
10 | C6H5CH2CHO | C6H5CH2CH2OH | 60 | 85 |
10 | CH3(CH2)3CHO | CH3(CH2)3CH2OH | 60 | 80 |
11 | CH3(CH2)5CHO | CH3(CH2)5CH2OH | 70 | 82 |
12 | 4-CH3O-C6H4CH2CH2COCH3 | 4-CH3O-C6H4CH2CH2CHOHCH3 | 50 | 88 |
13 | CH3(CH2)5COCH3 | CH3(CH2)5CHOHCH3 | 50 | 90 |
14 | (CH2)5CO | (CH2)5CHOH | 40 | 95 |
15 | C6H5COCH3 | C6H5CHOHCH3 | 50 | 90 |
16 | C6H5COC6H5 | C6H5CHOHC6H5 | 50 | 89 |
17 | 50 | 95 | ||
18 | C6H5CHCHCHO | C6H5CHCHCH2OH | 40 | 85 |
19 | C6H5CHCHCOCH3 | C6H5CHCHCHOHCH3 | 50 | 86 |
20 | C6H5CH=CHCOC6H5 | C6H5CHCHCHOHC6H5 | 50 | 87 |
21 | 50 | 82 | ||
22 | 60 | 85 | ||
23 | C6H5CO(CO)C6H5 | C6H5CHOH(CHOH)C6H5 | 50 | 98 |
24 | 80 | 96 | ||
25 | 60 | 98 | ||
26 | C6H5CHOH(CO)C6H5 | C6H5CHOH(CHOH)C6H5 | 40 | 95 |
27 | 45 | 91 |
a The products were identified by comparison of their IR, and NMR spectra and physical data with those of the authentic samples [25].
b Isolated yield.
Regeneration of the polymeric reagent was accomplished by a simple washing reactivation procedure, in which the spent reagent was first washed with hydrochloric acid and then, with NaHCO3, distilled water, and ether, to obtain the original polymer, followed by an activation reaction. No change in the capacity of the regenerated reagent was observed and the loss of the original polymer during this process was negligible. The dried resin was stored at room temperature for more than 1 month without significant loss in the hydride content (Table 4).
Stability of the hydride content of poly(1,4-butyl-bis-vinylpyridinium) borohydride over a 6-week period.
Weeks | First | Second | Third | Fourth | Fifth | Sixth |
Borohydride content of polymeric reagent (mmol/g) | 5.8 | 5.8 | 5.7 | 5.7 | 5.6 | 5.4 |
Table 5 shows the comparison of the efficiency of P(BBVP)BH4 with that of the other reported polymer-supported borohydrides in the reduction of various organic functional groups. As shown in many reduction reactions, the efficiency of P(BBVP)BH4 is higher than those of poly(4-vinylpyridine)-supported chloroaluminum borohydride [PVP-Al(BH4)Cl2], of poly(4-vinylpyridine)-supported zinc borohydride [PVP-Zn(BH4)2], and of poly(4-vinylpyridine)-supported zirconium borohydride [PVP-Zr(BH4)4].
Comparison of polymer-supported poly(1,4-butyl-bis-vinylpyridinium), chloroaluminum, zinc and zirconium borohydrides in the reduction of different organic functional groups.
C6H5CH2CHO → C6H5CH2CH2OH | ||||
Reducing agent | Reagent: substrate (molar ratio) | Time (h) | Yield (%)a | Ref. |
PVP-Al(BH4)Cl2 | 2.7 | 2.5 | 90 | [16] |
PVP-Zn(BH4)2 | 1.0 | 15.0 | 75 | [18,19] |
PVP-Zr(BH4)4 | 1.0 | 6.0 | 84 | [20] |
P(BBVP)BH4 | 0.29:1.0 | 60 min | 85 | This work |
C6H5COCH3 → C6H5CHOHCH3 | ||||
Reducing agent | Reagent: substrate (molar ratio) | Time (h) | Yield (%)a | Ref. |
PVP-Al(BH4)Cl2 | 5.0 | 8.0 | 75 | [16] |
PVP-Zn(BH4)2 | 2.0 | 15.0 | 5 | [18,19] |
PVP-Zr(BH4)4 | 2.0 | 12.0 | 80 | [20] |
P(BBVP)BH4 | 0.40:1.0 | 50 min | 90 | This work |
C6H5COC6H5 → C6H5CHOHC6H5 | ||||
Reducing agent | Reagent: substrate (molar ratio) | Time (h) | Yield (%)a | Ref. |
P(4VP)BH3 | 2.6 | 2.5 | 40 | [13] |
PVP-Al(BH4)Cl2 | 5.0 | 20 | 90 | [16] |
PVP-Zn(BH4)2 | 2.0 | 45 | 0.0 | [18,19] |
PVP-Zr(BH4)4 | 2.0 | 18 | 75 | [20] |
P(BBVP)BH4 | 0.58:1.0 | 50 min | 89 | This work |
C6H5CHCHCHO → C6H5CHCHCH2OH | ||||
Reducing agent | Reagent: substrate (molar ratio) | Time (h) | Yield (%)a | Ref. |
PVP-Al(BH4)Cl2 | 5.0 | 4.0 | 98 | [16] |
PVP-Zn(BH4)2 | 1.0 | 9.0 | 90 | [18,19] |
PVP-Zr(BH4)4 | 1.0 | 6.0 | 95 | [20] |
P(BBVP)BH4 | 0.29:1.0 | 40 min | 85 | This work |
C6H5CHCHCOCH3 → C6H5CHCHCHOHCH3 | ||||
Reducing agent | Reagent: substrate (molar ratio) | Time (h) | Yield (%)a | Ref. |
PVP-Al(BH4)Cl2 | 5.0 | 4.0 | 96 | [16] |
PVP-Zn(BH4)2 | 2.0 | 15.0 | 10 | [18,19] |
PVP-Zr(BH4)4 | 2.0 | 15.0 | 85 | [20] |
P(BBVP)BH4 | 0.40:1.0 | 50 min | 86 | This work |
a Isolated yields.
We found that by purifying ethanol with P(BBVP)BH4 resin, the distillation step was no longer necessary. Passing the ethanol to be purified through a small column containing the P(BBVP)BH4 resin removes any impurities that can be reduced with the borohydride ion. We observed that a contact time of 10 min is usually sufficient to remove most impurities. This procedure can be generally effective for the purification of other solvents. However, depending on the solvent or specific impurity, it may be necessary to alter the contact time.
The most important advantages of this method over the one with NaBH4 is that the P(BBVP)BH4 resin was remarkably stable in ethanol; also, since the hydride capacity is on the order of 5.8 mmol of borohydride per gram of dry resin, a small amount of P(BBVP)BH4 resin will remove trace carbonyl impurities from a substantial volume of ethanol; the most importantly, no new contaminants, such as Na+ and BO2−, are added to ethanol, since the borate ion remains bonded to the resin.
4 Conclusion
Sodium borohydride stabilized on poly(1,4-butyl-bis-vinylpyridinium) chloride is used as an efficient and regenerable polymer-supported borohydride reagent for the reduction of a variety of carbonyl compounds. The regioselectivity, easy reaction work-up with no boron moiety in the final product solution, and good to high reaction yields make this new polymer-supported borohydride reagent useful in the field of organic synthesis. These borohydride is extremely simple to prepare and very convenient for many laboratory purifications. Based on the results of these study, we feel that P(BBVP)BH4 offers several advantages, such as its ability to be recovered quantitatively after use for regeneration and recycling, and its particular attractiveness in view of the commercial availability of poly(4-vinylpyridine) as well as of its ability to be used safely in mole-scale reactions; moreover, the isolation of products by simple filtration and evaporation is an important feature of this polymer-supported reducing agent, which might be used in columns for the reduction process. We are continuing more detailed studies on the use of poly(1,4-butyl-bis-vinylpyridinium) borohydride for the purification of ethanol and of other solvents.
Acknowledgements
The author is thankful to House Research of Professor Reza, Education Guilan, Rasht, District 1 for partial support of this work.