1 Introduction
Depuis la nuit des temps, l’énergie a constitué la principale force motrice pour le progrès du monde [1–3]. À l’aube de notre siècle, les nouvelles formes d’énergie sont en plein essor, mais l’économie mondiale repose encore sur l’industrie pétrochimique [4–9]. De plus, avec les réglementations environnementales et économiques de plus en plus strictes, le principal défi dans tous les domaines de recherche et dans tous les secteurs économiques est de trouver des procédés plus écologiques, avec une meilleure économie d’atome [10–15]. En particulier, l’industrie pétrochimique a mis l’accent sur la recherche de nouveaux matériaux, afin d’améliorer l’indice d’octane ou de cétane par différentes réactions [16–21].
En termes d’usage de catalyseurs et de valeur en produits, le craquage catalytique est la plus importante opération de l’industrie de raffinage [22]. La valorisation des fractions lourdes en essences et diesel à haut indice d’octane et de cétane est un point stratégique sur le plan géopolitique [1,3,21]. Si la production de pétrole est de l’ordre de 87 millions de tonnes de barils par jour, environ 35 % sont destinés pour les transports, alimentant 800 millions de voitures, dont 80 % se trouvent dans les pays développés [23]. De ce fait, le craquage catalytique a fait l’objet de nombreux travaux et a surtout porté sur la valorisation de coupes moyennes et lourdes, telles que les gasoils et les résidus atmosphériques pour l’obtention d’essence [24]. Sur une unité classique de craquage, l’huile est vaporisée dans une chambre à lit fluidisé au contact du catalyseur entre 480 et 520 °C. Le catalyseur est régénéré après séparation et traitement à la vapeur pour retirer le coke à une température comprise entre 600 et 700 °C. Les résistances mécaniques et hygrothermique sont essentielles pour la détermination d’un catalyseur industriel en raison de cette étape de régénération.
Les argiles ont été utilisées comme catalyseurs de craquage industriel. Les argiles de type montmorillonite, traitées à l’acide ont perdu leur rôle comme catalyseurs vers 1964 avec l’introduction d’aluminosilicates naturels et synthétiques (comme le sont les zéolites) pour ce procédé [25]. Cependant, l’intérêt des argiles n’a pas diminué et les applications existent dans de nombreux domaines, y compris en catalyse pour la chimie organique fine. La publication de Chen résume cette évolution dans le cadre de la catalyse hétérogène [26]. Les évolutions sur les argiles concernent principalement les argiles à feuillets avec les quatre modifications principales : acidification, échange ionique, dépôt métallique et introduction de piliers. Ce dernier point a permis l’obtention de matériaux poreux de diamètres plus importants que ceux des zéolites et d’acidité supérieure. Malheureusement, d’une part, ces matériaux nécessitent une préparation assez longue et, d’autre part, ils restent insuffisamment intéressants en raison de leur manque de résistance hydrothermale [27,28].
Dans le cadre de la recherche sur les produits naturels, cette étude s’est construite autour de la constitution de charges catalytiques de faible coût et ayant de meilleures propriétés mécaniques tout en conservant de bonnes propriétés catalytiques. Le kieselguhr est une roche sédimentaire, principalement formée de squelettes siliciques issus de diatomées [29,30]. Un mélange de bentonite avec du kieselguhr semble être un nouveau matériau adsorbant pour l’industrie [31]. De simples mélanges de ces composés permettent de préparer des catalyseurs sans métaux nobles. L’obtention de mélanges bentonite/kieselguhr constitue la première phase de cette étude, suivie par l’analyse de son comportement catalytique. Les charges sont activées par l’acide chlorhydrique et imprégnées par des sels métalliques (chrome et fer). Elles sont caractérisées pour connaître leur acidité et leur surface spécifique BET. Les propriétés de craquage des charges sont évaluées sur trois molécules représentatives des trois familles d’hydrocarbures contenues dans le brut puis sur un gasoil complet. Une distillation ASTM (American Society for Testing and Materials) complète l’étude afin d’élargir le champ des fractions pétrolières. Les rendements et la performance de ces essences ont été déterminés et comparés aux résultats obtenus à partir du craquage du gasoil.
2 Partie expérimentale
2.1 Préparation des catalyseurs
Quatre catalyseurs ont été préparés avec un support constitué de bentonite (noté B) et de kieselguhr (noté K) dans le rapport massique B/K = 30/70. La bentonite provient du gisement de Mostaganem et le kieselguhr de la mine de Sig (Ouest de l’Algérie). Le kieselguhr de la même mine a été étudié par Hadjar et al. [31], qui ont montré que ce matériau est amorphe jusqu’à une température de 800 °C et que sa structure est macroporeuse, avec une surface spécifique BET de 22 m2/g.
Les catalyseurs sont obtenus par un broyage de ces deux roches séparément, sans prétraitement préalable, à l’aide d’un broyeur à boulets tournant à 250 tours par minute suivi d’un tamisage, de façon à ne retenir que la fraction ayant un diamètre de particules inférieur à 140 μm. Les fractions recueillies sont mélangées par agitation des deux roches dans le rapport B/K. Un séchage est effectué à 110 °C pendant 12 h. À ce stade, le mélange est noté BK. Une activation est effectuée sur la charge avec de l’acide chlorhydrique à 20 % pendant 48 h suivie d’une filtration et de lavages à l’eau distillée. Ce traitement a pour but la substitution des ions Na+ ou Ca2+ par des protons dans l’interfeuillet de l’argile ; l’ensemble des sites du kieselguhr est déjà protonné.
Pour tester la faisabilité catalytique avec un rendement optimal, nous avons choisi de les doper avec différents métaux : Fe, Cu, Co, Cr, Ni. Nous présenterons ici le cas des dopages au Cr et au Fe, car ils se sont avérés très prometteurs.
Les solutions aqueuses des sels de chrome Cr2(SO4)3·15 H2O et de fer Fe(NO3)3·9 H2O sont ajoutées au mélange B/K après traitement acide (noté BKA) ; cet ajout conduit au système catalytique BKA–Cr et BKA–Fe en rapport avec la nature de l’ajout métallique. La quantité de métal introduite dans la solution correspond à 10 g pour 100 g de support.
2.2 Méthodes de caractérisation
L’indice d’acidité est déterminé par une technique classique qui consiste à mettre la poudre de catalyseur en présence d’une base (la n-butylamine) [32]. L’activation par échange cationique consiste à disperser l’ion métallique sur la partie argile du mélange. La quantité de métal échangée est déterminée par colorimétrie en retour. La charge ayant un caractère acide réagit avec la n-butylamine, l’excès de base est dosé par l’acide hypochlorique (HClO4). La surface spécifique des catalyseurs est calculée à partir de l’équation BET.
2.3 Tests catalytiques
Le craquage catalytique transforme, en présence d’un catalyseur acide, les coupes lourdes à longues chaînes d’hydrocarbures en coupes légères. Ces coupes lourdes sont formées d’hydrocarbures saturés, de cycloalcanes et d’aromatiques. Pour cette raison, on s’est intéressé à trois molécules modèles appartenant chacune à une famille contenue dans la coupe, le n-dodécane, la décaline et le cumène, pour étudier leur réactivité avec les catalyseurs préparés. Le craquage catalytique fournit un ensemble de produits très variés : des hydrocarbures très légers C1 et C2, des « GPL » (C3 et C4), une fraction essence et une fraction lourde (aromatiques + résidu chargé d’impuretés et de coke). Les produits obtenus sont essentiellement de nature oléfinique pour les fractions légères et aromatique pour les fractions lourdes.
Les tests de performance des catalyseurs pour la conversion d’hydrocarbures modèles et de la charge de gasoil ont été réalisés dans un réacteur tubulaire en acier inoxydable. Les conditions opératoires optimales sont :
- • température de réaction : 500 °C ;
- • volume de catalyseur : 20 cm3 ;
- • vitesse spatiale horaire des hydrocarbures liquides injectés à l’aide d’une pompe : 1 h−1.
Trois familles de produits sont récupérées à l’issue de cette transformation : une phase gazeuse (C1–C4), une phase liquide (à partir du C5–C12) et une phase solide (coke) en rapport avec les procédés de craquage catalytique industriel.
2.3.1 Craquage d’une coupe pétrolière
La conversion du gasoil ainsi que le rendement en essence ont été calculés sur la base de l’analyse chromatographique des produits obtenus, en considérant la somme des pourcentages des composés éluant avant le n-dodécane (n-C12). La composition par famille d’hydrocarbures Ci a été déterminée par la méthode chromatographique et par la méthode n d PA :%Ci = ni di PAi [33], avec ni l’indice de réfraction d’une famille i, di la densité d’une famille i et PAi le point d’aniline d’une famille i. La composition des familles CA, CN, et CP, représentant respectivement les pourcentages en carbone aromatiques, naphténiques et paraffiniques, sont calculés de la façon suivante :
La distillation ASTM s’est faite dans un appareil normalisé. Elle représente l’évolution de la fraction distillée en volume, à pression atmosphérique, en fonction de la température, en notant plus particulièrement le point initial et le point final. Le point initial est la température repérée au moment où apparaît la première goutte de distillat. Le point final est la température à laquelle on récupère la dernière goutte.
3 Résultats et discussion
3.1 Caractérisation des catalyseurs
Les roches tamisées (B et K) et le mélange (BK) ainsi que les charges acidifiées BKA, BKA–Cr et BKA–Fe ont été analysés pour mesurer l’indice d’acidité, le taux d’imprégnation et la surface spécifique. Ces valeurs sont présentées dans le Tableau 1.
Caractérisation physique des catalyseurs et de leurs précurseurs.
B | K | BK | BKA | BKA–Cr | BKA–Fe | |
Indice d’acidité (mequiv H+ g−1) | 0,19 | 0,21 | 0,19 | 3,81 | 2,96 | 3,20 |
Surface BET (m2 g−1) | 50,00 | 22,00 | 75,0 | 91,30 | 118,0 | 249,20 |
Taux d’imprégnation (%) | — | — | — | — | 44,50 | 52,0 |
Le traitement acide ainsi que l’imprégnation par la solution de sel métallique ont conduit à une amélioration de l’acidité et de la surface spécifique. Ces propriétés sont recherchées dans les réactions de craquage catalytique.
3.2 Le craquage catalytique
L’approche du craquage catalytique d’un gasoil est très difficile à cause du grand nombre de composés obtenus et de réactions possibles [34]. Quann et Jaffe ont détaillé l’ensemble des réactions pouvant se produire lors d’une réaction de craquage d’une coupe pétrolière [35]. Sept types de réactions sont décrits lors du craquage, en fonction de la taille de la molécule, de ses fonctions et de son caractère aromatique ou non. L’ensemble de ces réactions a lieu simultanément dans le cas du craquage d’un gasoil. Les molécules choisies sont représentatives des familles contenues dans une charge pétrolière. Chacune d’elles subira un nombre limité de type de réactions.
3.2.1 Craquage des molécules modèles
Les propriétés physiques des molécules modèles testées : n-dodécane, décaline et cumène sont données dans le Tableau 2.
Propriétés physiques des molécules modèles testées.
Hydrocarbures utilisés | M (g/mol) | Teb (°C) | Densité (d) | Indice de réfraction (n) | PA |
n-Dodécane | 170,00 | 216,3 | 0,748 | 1,4132 | 81 |
Décaline | 148,00 | 186 | 0,870 | 1,4753 | 65 |
Cumène | 120,20 | 150 | 0,862 | 1,4091 | 20 |
3.2.1.1 Craquage du n-dodécane
Les résultats de la conversion et la nature des produits obtenus à partir du n-dodécane sont donnés dans les Tableaux 3 et 4.
Craquage du n-dodécane.
Catalyseur | Conversion (%) | Liquide collecté (%) | Pertes dont gaz (%) | Coke (%) |
BK | 57,00 | 64,90 | 31,30 | 3,80 |
BKA | 79,60 | 66,70 | 29,22 | 4,08 |
BKA–Cr | 69,70 | 70,00 | 26,32 | 3,70 |
BKA–Fe | 50,30 | 70,00 | 27,78 | 2,10 |
Analyse chromatographique de la phase liquide obtenue lors du craquage du n-dodécane.
Catalyseurs | Sélectivité en paraffines (%) | Sélectivité en oléfines (%) | Sélectivité en aromatiques (%) |
BK | 92,40 | 7,60 | 0 |
BKA | 92,47 | 7,53 | 0 |
BKA–Cr | 85,00 | 15,00 | 0 |
BKA–Fe | 93,59 | 6,41 | 0 |
Les réactions attendues sont : le craquage, la déshydrogénation des paraffines et la formation d’oléfines. La conversion la plus élevée est obtenue avec le catalyseur le plus acide BKA, à l’opposé du catalyseur BK, n’ayant subi aucun traitement, qui présente la valeur la plus faible. Lors du craquage catalytique du n-dodécane, les principaux produits formés dans la phase liquide sont des paraffines et des oléfines avec un nombre de carbone compris entre 5 et12. Les hydrocarbures en C1, C2, C3 et C4 vont apparaître dans la phase gazeuse et sont « perdus » pour l’obtention d’essence.
En présence de KBA–Cr, les produits majoritairement obtenus dans la phase liquide sont des alcanes ramifiés (43 %) dont 34 % de diméthyl-3,4-heptane, des alcènes (15 %) et des n-alcanes (11,5 %) quasiment exclusivement formés de n-hexane, le reste étant du n-dodécane n’ayant pas réagi.
Dans la phase gazeuse, ce catalyseur donne des quantités importantes en C3 (propane + propène) et en C4, l’acidité favoriserait particulièrement la coupure en C8 et C9.
Avec le système catalytique BKA, on retrouve autant d’isoparaffines (40 %) avec les mêmes proportions en diméthyl-3,4-heptane, mais avec trois fois plus de n-paraffines (30 %), soit 25 % de n-hexane et très peu d’oléfines (7,5 %), les produits formés dans la phase gazeuse sont surtout des C3 et des C4, comme en présence du BKA–Cr.
Le catalyseur BKA–Fe favorise la formation du méthyl-4-octane par rapport au diméthyl-3,4-heptane, mais, dans tous les cas, les isoparaffines représentent le pourcentage le plus élevé. La formation importante, pour l’ensemble des systèmes d’oléfines liquides et des isoparaffines, est en faveur de l’augmentation de l’indice d’octane, ce qui est souhaitable pour l’application attendue.
3.2.1.2 Craquage de la décaline
Le craquage catalytique de la décaline conduit aux réactions de déshydrogénation avec formation d’aromatiques et d’ouverture de cycle. Les produits présents dans toutes les phases liquides obtenues sont des aromatiques, des oléfines, des naphtènes et des isoparaffines. Les normales paraffines sont pratiquement absentes.
Les résultats des conversions et des distributions par famille d’hydrocarbures obtenus sur les différentes charges catalytiques sont donnés dans les Tableaux 5 et 6.
Craquage de la décaline sur les charges catalytiques.
Catalyseur | Conversion (%) | Liquide collecté (%) | Pertes (dont gaz) (%) | Coke (%) |
BK | 83,50 | 44,91 | 39,27 | 15,80 |
BKA | 71,30 | 36,10 | 40,23 | 23,67 |
BKA–Cr | 85,30 | 75,25 | 18,65 | 6,10 |
BKA–Fe | 94,80 | 11,86 | 63,84 | 24,97 |
Analyse chromatographique de la phase liquide obtenue par craquage de la décaline.
Catalyseurs | Sélectivité en paraffines (%) | Sélectivité en oléfines (%) | Sélectivité en naphtènes (%) | Sélectivité en aromatiques (%) |
BK | 22,00 | 18,00 | 19,00 | 41,00 |
BKA | 5,50 | 22,00 | 28,00 | 44,50 |
BKA–Cr | 15,50 | 6,00 | 14,00 | 64,50 |
BKA–Fe | 1,35 | 36,34 | 3,38 | 58,05 |
Les taux de conversion sont importants pour toutes les charges catalytiques. Le catalyseur dopé au chrome est celui qui donne les meilleures performances, avec un rendement en liquide très élevé, formé majoritairement de produits aromatiques (27 % de triméthylbenzène, 17 % de tetraméthylbenzène et 6 % de méthyl benzène). Les quantités de gaz (18 %) et de coke (6 %) produites lors du craquage de la décaline en présence de BKA–Cr sont également beaucoup plus faibles comparativement aux autres systèmes.
En présence des autres catalyseurs, le craquage de la décaline conduit essentiellement à la formation d’aromatiques comme le benzène (15,6 % pour BK, 17,5 % pour BKA et 50 % pour BKA–Fe), le triméthyl-1,2,3-benzène (12 % dans le cas du BK, 23 % pour BKA) et des oléfines, notamment le diméthyl-2,4-hexène (16,5 % dans le cas du BK, 20,8 % pour BKA et 35 % pour BKA–Fe).
3.2.1.3 Craquage du cumène
Le craquage catalytique de cette molécule, représentant la famille des aromatiques, montre qu’il n’y a pas pratiquement pas de différence entre les résultats obtenus avec ces catalyseurs, en ce qui concerne aussi bien la conversion que les proportions de produits formés en termes de rendement de liquide, de pertes en gaz et de formation de coke [36] (Tableaux 7 et 8).
Craquage du cumène sur les charges catalytiques.
Catalyseur | Conversion% | Liquide collecté % | Pertes (dont gaz)% | Coke % |
BK | 80,49 | 70,30 | 26,50 | 3,20 |
BKA | 82,58 | 71,30 | 24,20 | 4,50 |
BKA–Cr | 82,63 | 74,20 | 21,65 | 4,15 |
BKA–Fe | 79,32 | 63,72 | 30,10 | 6,17 |
Analyse chromatographique de la phase liquide obtenue par craquage du cumène sur les charges catalytiques.
Catalyseurs | Sélectivité en paraffines (%) | Sélectivité en oléfines (%) | Sélectivité en aromatiques (%) |
BK | 6,62 | 1,20 | 92,18 |
BKA | 25,98 | 2,80 | 71,22 |
BKA–Cr | 16,46 | 4,65 | 78,89 |
BKA–Fe | 21,40 | 2,11 | 76,49 |
Le craquage du cumène donne, pour l’ensemble des charges catalytiques, de fortes proportions en benzène (37 % dans le cas du BKA–Fe, 40 % pour le BKA–Cr et 9 % pour le BKA) et en toluène (41 % pour le BK, 22 % pour le BKA, 7 à 9 %). Il se forme également des quantités importantes en dérivés benzéniques, tels que l’isobutylbenzène et les diéthylbenzène ; ceci laisse supposer que la scission de la molécule se produit en priorité au niveau de la chaine latérale. Les oléfines présentes dans la phase liquide proviennent des réactions de désalkylation.
3.2.2 Craquage des coupes pétrolières
3.2.2.1 Examen de la charge brute
La charge de gasoil issue du brut de Hassi Messaoud (Algérie) a été caractérisée, d’une part, par ses propriétés physiques et, d’autre part, par ses fractions de distillation. Les premières caractéristiques sont regroupées dans le Tableau 9. Les résultats de la distillation ASTM de la charge gasoil sont donnés dans le Tableau 10. Le point initial correspond à la température de 186 °C et le point final à celle de 360 °C. Ce sont des valeurs élevées par rapport aux points initial et final de l’essence commerciale, qui sont respectivement d’environ 40 °C et 220 °C. L’ensemble des fractions de distillation sommées pour le gasoil est donné sur la Fig. 1.
Composition par famille d’hydrocarbures du gasoil.
Composition chimique | CP (%) | CN (%) | CA (%) |
Par calcul | 56,50 | 28,80 | 14,70 |
Par CPG | 62,17 | 09,58 | 27,95 |
Craquage catalytique du gasoil sur les mélanges B/K.
Catalyseur | Liquide collecté (%) | Pertes (dont gaz) (%) | Coke (%) |
BKA | 62,20 | 32,77 | 5,03 |
BKA–Cr | 68,36 | 25,37 | 3,27 |
BKA–Fe | 69,95 | 28,70 | 1,35 |
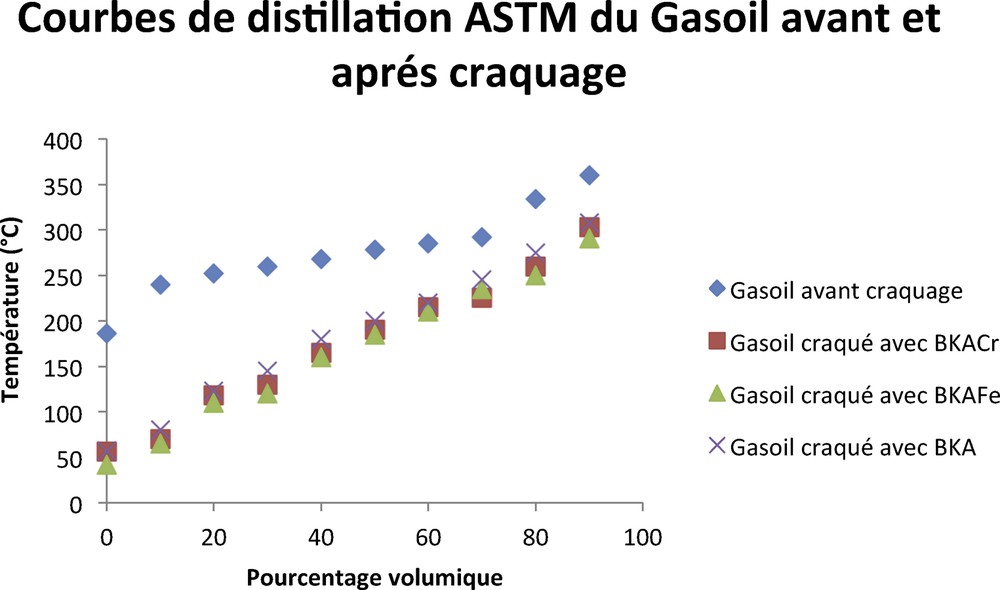
Courbes ASTM obtenues à partir de la fraction liquide du gasoil brut et après craquage sur les catalyseurs BKA, BKA–Cr et BKA–Fe.
La distillation ASTM s’est faite dans un appareil normalisé, selon la norme AFNOR NF M 07-002. Les caractéristiques de ce gasoil ont été mesurées selon ces normes. Les résultats de la distillation montrent que le pourcentage distillant avant la température désirée pour sa commercialisation, qui est de 220 °C, est inférieur à 15 % de la totalité de la charge du gasoil. Cette quantité est bien entendue insuffisante et la charge de gasoil nécessite une étape de craquage pour convenir. La composition par famille d’hydrocarbures du gasoil utilisé a été déterminée par deux méthodes : la méthode n.d.PA et la méthode par analyse chromatographique par CPG. Les pourcentages de CP élevés présentés sur le Tableau 11 montrent que, quelle que soit la méthode, ce gasoil est fortement paraffinique.
Caractéristiques du gasoil craqué en comparaison du brut.
Catalyseur | N | D | PA | CP (%) | CN (%) | CA (%) | O (%) |
Gasoil brut | 1,4659 | 0,8372 | 66 | 56,50 | 28,80 | 14,70 | 0 |
BKA | 1,4698 | 0,8331 | 60 | 37,00 | 10,10 | 35,40 | 17,50 |
BKA–Cr | 1,4673 | 0,8325 | 61 | 28,90 | 9,90 | 38,90 | 22,30 |
KBA–Fe | 1,4695 | 0,8309 | 58 | 42,80 | 9,30 | 26,10 | 21,80 |
3.2.2.2 Craquage catalytique du gasoil en présence de catalyseurs à base de B/K
Le craquage catalytique du gasoil a été étudié en présence de trois catalyseurs : KBA, KBA–Cr et KBA–Fe. Le pourcentage de liquide collecté pour les trois catalyseurs est globalement le même. On note une légère différence pour le BKA : un pourcentage en liquide collecté plus faible et des quantités de gaz et de coke formées plus importantes. Comme les conditions d’expériences sont voisines de celles utilisées pour les molécules modèles et sachant que la charge de gasoil est majoritairement paraffinique, le pourcentage de liquide est à mettre en rapport avec l’étude de la molécule modèle de n-dodécane. Nous avons montré précédemment que les trois catalyseurs avaient des propriétés de craquage des paraffines en molécules oléfiniques et que la quantité de « perte » était assez élevée. Dans cette étude du gasoil, on observe également une proportion de gaz produite élevée.
L’application de la méthode n.d.PA et des analyses par chromatographie des différentes fractions obtenues conduit aux résultats donnés dans le Tableau 11. Parmi les quatre familles de produits, les familles qui sont à l’origine d’un indice d’octane élevé sont les deux familles d’hydrocarbures (CA et CO). Dans le gasoil brut, la quantité d’aromatiques est assez faible et on n’a pas de composés oléfiniques. Selon les résultats présentés dans le Tableau 11, le craquage du gasoil conduit, en présence de chacun des deux systèmes, à une augmentation des proportions en aromatiques et à la formation d’oléfines. Ceci est favorable au besoin en essence dans les deux cas. Les proportions en paraffines et naphtènes diminuent du fait de leurs transformations par craquage dans les deux autres familles, mais aussi en « légers » qui sont perdus pour le raffineur. Ces résultats sont confirmés par la mesure de la densité, qui diminue en raison de l’obtention de fractions plus légères et du point d’aniline, qui s’abaisse également du fait de l’augmentation de la proportion des aromatiques dans les produits craqués.
Les résultats de la distillation ASTM sont présentés sur la Fig. 1. Nous obtenons un faisceau de courbes de distillation caractérisé par des points initiaux et des points finaux inférieurs à ceux correspondant au gasoil avant craquage. En effet, la quantité d’essence présente dans la charge brute représente moins de 15 % ; elle passe à plus de 60 % après craquage dans le cas des systèmes BKA–Cr et BKA–Fe. Le gain en fractions légères est visible pour l’ensemble de ces systèmes ; cependant, il est plus important pour les systèmes imprégnés par un sel métallique. La coupe obtenue avec le BKA–Fe et le BKA–Cr contient des proportions importantes en C6 (entre 40 et 55 %).
4 Conclusion
Le craquage catalytique est à l’heure actuelle le procédé le plus important du raffinage en termes de tonnage de charge utilisée et de quantité de catalyseurs utilisés [37]. Les résultats obtenus montrent qu’à partir de produits naturels et respectueux de l’environnement, tels que la bentonite ou le kieselguhr, qui sont très abondants dans la nature et bon marché, nous pouvons élaborer des catalyseurs capables de convertir des hydrocarbures lourds (comme le gasoil) en fractions plus légères. Les courbes ASTM des gasoils, avant et après craquage, montrent bien un écart de température de plus de 100 °C par rapport à la courbe correspondante du gasoil testé. Ces résultats montrent que ces catalyseurs, BKA, BKA–Fe et BKA–Cr sont des catalyseurs de substitution potentielle de métaux nobles. En particulier, le catalyseur BKA–Fe présente non seulement les meilleures performances, mais aussi des avantages environnementaux et économiques.