1 Introduction
The FeII–III hydroxycarbonate, that is the carbonated form of green rusts,
The estimation of the standard Gibbs free energy of formation of GRs allowed us to draw potential–pH equilibrium Pourbaix diagrams, where the GR compounds are included [11,13,15,33]. It was the first step towards the full understanding of the importance of GRs in corrosion processes. It predicted that in solutions with moderate concentrations (
The oxidation of GRs can lead to the most common constituents of rust, that is goethite, lepidocrocite, akaganeite and magnetite, depending on pH, temperature, oxygen flow, dissolved FeII concentration and, more generally, composition of the electrolyte [10–13,15,28,29,32,38,40]. But FeII cations can also be completely oxidised in situ, by leaving essentially unchanged the initial layered structure and leading to what was called ‘ferric green rust’, as obtained by deprotonation of OH− ions that surround Fe cations [34,41]. This new compound was discovered as the result of the action of hydrogen peroxide upon GRs, but was also obtained by oxidation of a dry GR layer [1] or anodic polarisation of steel [22].
In this article, the mechanisms of formation of GRs from steel are discussed. Two main types of aqueous media are considered, the carbonated media representing freshwaters, and the chloro-sulfated media representing seawater. In the first case, the competition between
2 Methodology
When a steel electrode is corroding in an aerated electrolyte, the potential, called open-circuit potential (OCP), reaches a value somewhere between the potential of FeII/Fe equilibrium and that of O2/H2O equilibrium. The corrosion process can be accelerated electrochemically by increasing either the potential of the electrode, i.e. the potentiostatic procedure, or the current flowing through the electrode, i.e. the galvanostatic procedure. Such experiments can be devised in the laboratory for monitoring the early stages of the corrosion process. In this article, experiments performed at OCP using E24 steel (98.2% Fe, 0.122% C, 0.206% Si, 0.641% Mn, 0.016% P, 0.131% S, 0.118% Cr, 0.02% Mo, 0.105% Ni and 0.451% Cu) are described. The steel surfaces were polished with silicon carbide (particle size 25 μm), rinsed thoroughly with Milli-Q water and carefully dried. The potential was measured using an Ametek (Princeton Applied Research) 263/A potentiostat system. A saturated calomel electrode (SCE) was used as a reference, but the potential is expressed with respect to the standard hydrogen electrode (SHE) in order to facilitate the comparison with potential–pH equilibrium Pourbaix diagrams.
The kinetics of degradation of steel tends to decrease as the metal is covered by a rust layer and the behaviour of a steel structure dipped in water for years is governed by the properties of this several-millimetre-thick layer. The understanding of the mechanisms at such late stages of the corrosion process requires a detailed analysis of the morphology and composition of the rust layers. The case of a steel structure left for 25 years in the Atlantic Ocean is detailed. The identification of transient unstable phases such as GRs is only made possible if the samples are sheltered immediately from oxygen. Therefore, the corrosion layers, about 10–15-mm thick, scrapped from the metal in the permanently immersed zone, 1 m above the mud line, were immediately placed in acetone, preventing any chemical evolution of the samples for 3–4 months. They were coated with epoxy resin (Struers Epofix®), sawed up into 2-mm-thick slices, and again coated with resin. Cuts were achieved so that slices were perpendicular to the steel/rust layer interface. More details concerning this procedure can be found elsewhere [25].
Additional information about the mechanisms of formation and transformation of rust can be obtained via the study of the oxidation of a Fe(II) precipitate in aqueous suspension [10–13,15,33,38,40]. The oxidation processes involved in chloro-sulfated media were then studied using the following methodology. FeCl2⋅4 H2O and FeSO4⋅7 H2O were dissolved in a 100-ml flask of milliQ water. The
3 Rust layer characterisation
Different characterisation methods must be combined to identify unambiguously the various components of a rust layer. X-ray diffraction (XRD) can be used along with Raman and/or Mössbauer spectroscopy. Here, analyses performed by XRD, conversion electron Mössbauer spectroscopy (CEMS) and micro-Raman spectroscopy are presented.
3.1 CEMS
The decay of the nuclear excited state of 57Fe leads to the emission and subsequent resonant absorption of 14.4-keV photons. These are the photons that are not detected in the Mössbauer effect transmission measurements and correspond to the usual negative peaks of the Mössbauer spectra. The principle of CEMS is based upon the detection of the internally converted electrons emitted after the resonant absorption of γ-rays has taken place. This emission of K-conversion electrons with 7.3-keV energy is detected in backscattering experiments and is adequate for a non-destructive surface analysis. The analysed depth is about 300 nm. A room-temperature spectrum presented here was recorded using a gas flow proportional counter. The constant-acceleration Mössbauer spectrometer was calibrated with an α-Fe disk. The spectra were computer-fitted with a sum of Lorentzian shape lines. Errors on the Mössbauer parameters are about
3.2 XRD
Products were also analysed by XRD using Co K
3.3 Raman spectroscopy
The Raman study of the marine corrosion products of steel was performed using a multichannel DILOR OMARS 89 spectrometer®. The apparatus is fitted with a diode array detection system, which enables a 500-cm−1 broad spectrum to be analysed for a typical acquisition time of 30 s. Excitation of the samples was carried out with 514.5-nm radiation from a Spectra Physics 2017® argon ion laser. The power of the source was 20 mW and the spectral resolution was
4 Fresh water and
E–pH Pourbaix diagrams are maps that summarise the thermodynamic information describing the possible routes followed during the corrosion of steels in carbonated aqueous media (Fig. 1). Values of the standard Gibbs energy of formation
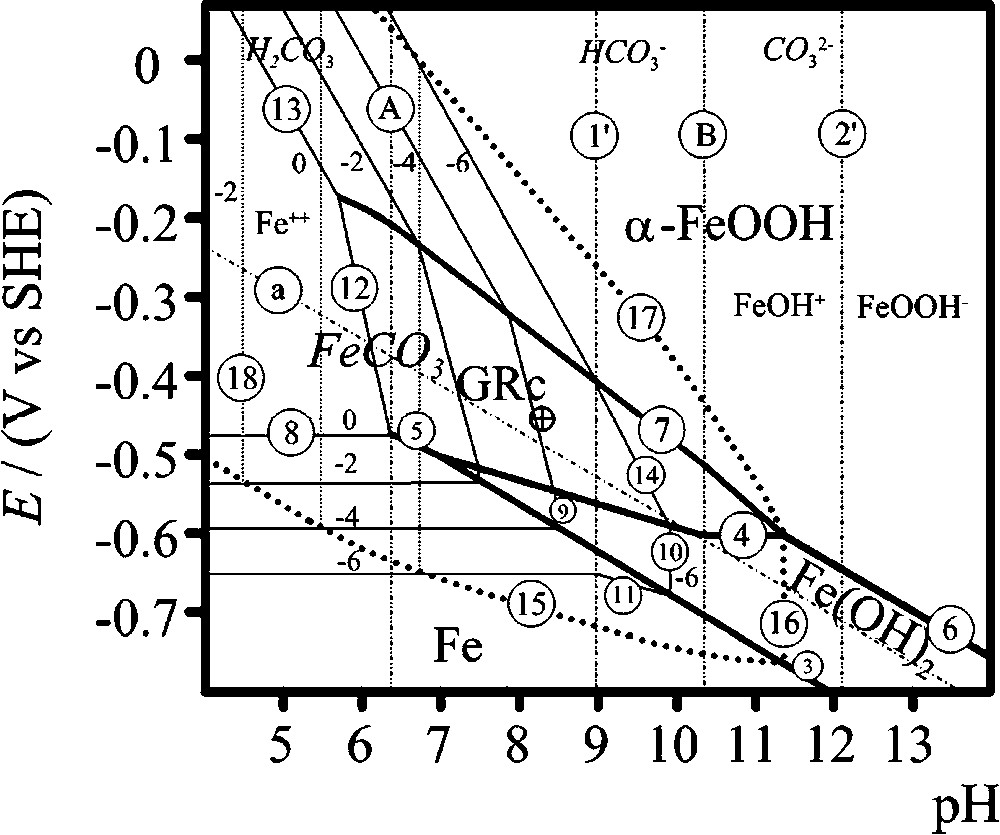
Superimposition of Pourbaix diagrams of iron in carbonate-containing aqueous solution at 25 °C, for an activity of carbonate species of 0.1. GRc designates
Superposition des diagrammes de Pourbaix du fer en solution aqueuse carbonatée à 25 °C, pour une activité des espèces carbonate de 0,1. GRc désigne
Gibbs free energies of formation used for calculations in standard temperature and pressure conditions
Enthalpies libres de formation utilisées pour les calculs dans les conditions standard de température et de pression
Species | Average oxidation number of Fe | References | |
Solid species | |||
α-Fe | 0 | 0 | |
Fe(OH)2(s) | +2 | −492 | [5,20] |
FeCO3(s) | +2 | −681 | Computed from [8] |
+7/3 | −4076 | Computed from [13] using |
|
|
|||
α-FeOOH(s) | +3 | −485.3 | [5] |
Liquid and dissolved species | |||
H2O | — | −237.18 | [5,20] |
|
+2 | −91.5 | [5,20] |
FeOH+ | +2 | −277.4 | [5,20] |
FeOOH− | +2 | −376.4 | [5,20] |
H2CO3 | — | −623.2 | [48] |
|
— | −586.8 | [48] |
|
— | −527.9 | [48] |
Equilibrium equations of E–pH Pourbaix diagrams drawn in Fig. 1
Équations d'équilibre des diagrammes de Pourbaix E–pH de la Fig. 1
Water and carbonate system |
|
Fe–H2O system |
|
|
However, it was reported that homogeneous
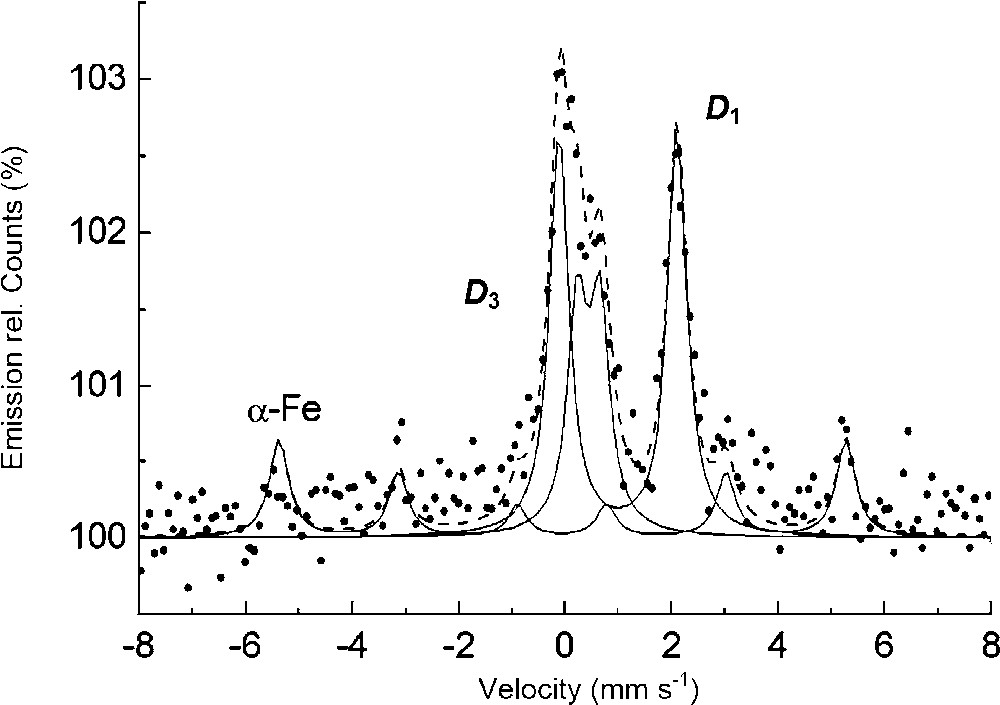
CEMS spectrum at room temperature of a steel disk dipped during 24 h in a 0.1 M NaHCO3 solution. ⋅⋅⋅⋅⋅⋅⋅: Experimental curve, - - - - -: global computed curve, ------: components of the spectra.
Spectre Mössbauer en électron de conversion (CEMS) à l'ambiante d'un disque d'acier trempé 24 h dans une solution de NaHCO3 à
When NaCl is added to the 0.1 M NaHCO3 solution, the green rust layer resulting of the immersion at OCP of iron disks is still composed of the hydroxycarbonate, even for NaCl concentration of 4 M [1]. This illustrates the well-known stability of the hydroxycarbonate structure with respect to any other form of GRs and in particular those obtained with monovalent anions [26,27,37]. But the results are different if the corrosion process is accelerated electrochemically. Galvanostatic experiments were performed on iron electrodes dipped in a 0.6 M NaHCO3 + 0.5 M NaCl solution of pH about 8.3 [16]. The corrosion product was a mixture of 35%
5 Seawater, and microbially influenced corrosion
Ten- to fifteen-millimetre-thick rust layers formed on steel sheet piles during 25 years proved to be composed of three main layers [40]. The inner one, close to the metal substrate, is essentially made of magnetite. The intermediate one is composed of iron(III) oxyhydroxides. Finally, in the external one, the closest to the interface with seawater, the sulphated form of GRs proved to be the main constituent (Fig. 3). A Raman spectrum of this
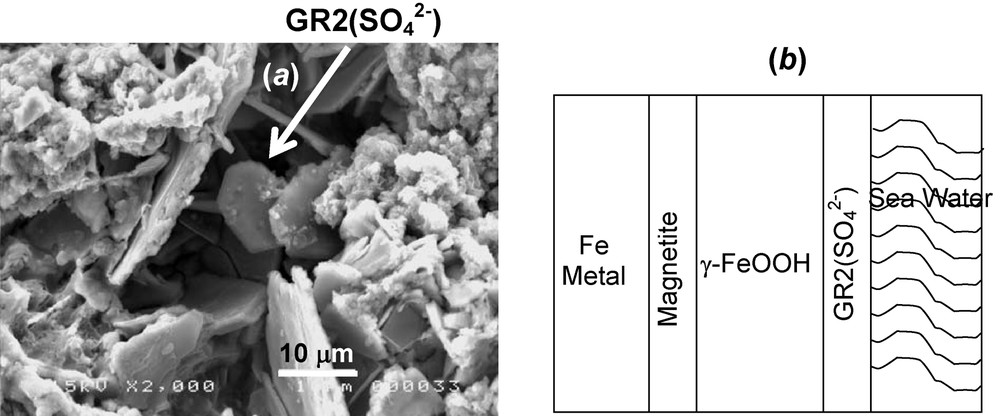
(a) SEM micrograph showing hexagonal shaped crystals of
(a) Micrographie par microscopie électronique à balayage montrant des cristaux hexagonaux de rouille verte carbonatée sur une feuille d'acier corrodé abandonnée 25 ans dans l'eau de mer et (b) séquence des couches de rouille : métal–magnétite–lépidocrocite–rouille verte sulfatée [40].

Raman spectrum of the outer part of a marine corrosion rust layer formed on steel.
Spectre Raman de la partie externe d'une couche de rouille formée par corrosion marine sur l'acier.
Additional experiments were performed in the laboratory in order to study the competition between GR(Cl−) and

Courbes
Intermediate compounds were analysed by XRD. Patterns are displayed in Fig. 6. The GR found at
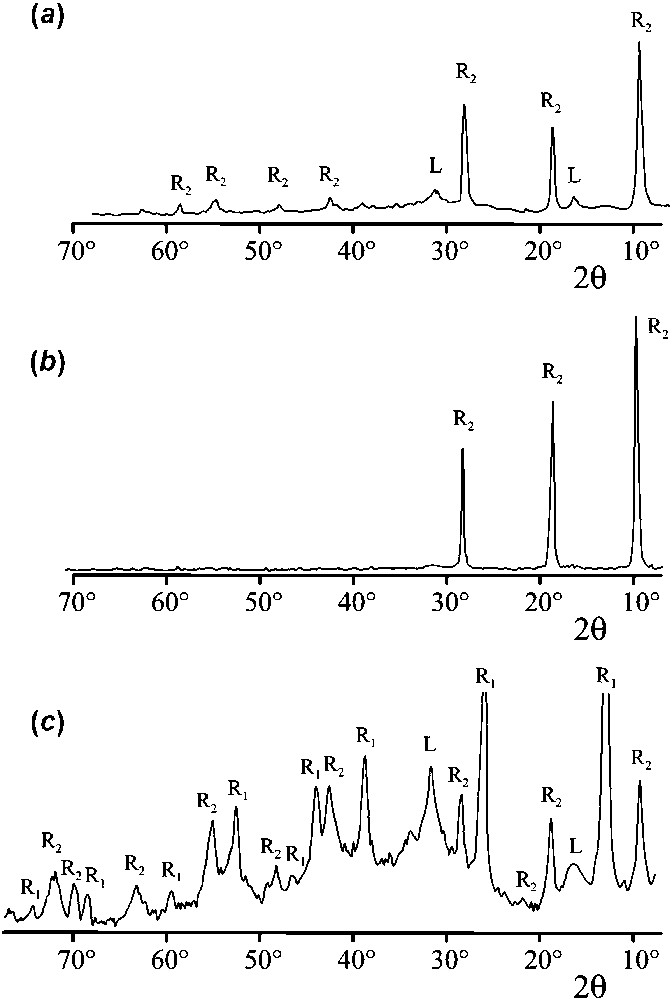
XRD patterns of the intermediate products obtained by oxidation of aqueous suspensions of Fe(II)-containing precipitates in the presence of Cl− and
XRD patterns of the intermediate products obtained by oxidation of aqueous suspensions of Fe(II)-containing precipitates in the presence of Cl− and
Clichés de diffraction des rayons X des produits intermédiaires obtenus par oxydation de suspensions aqueuses de précipités contenant du Fe(II) en présence d'ions Cl− et
Clichés de diffraction des rayons X des produits intermédiaires obtenus par oxydation de suspensions aqueuses de précipités contenant du Fe(II) en présence d'ions Cl− et
We demonstrated previously that in marine environments the dissolution of iron in seawater should lead to
6 Oxidation of GRs and formation of rust
Other phases can also be obtained from GRs in more specific conditions. Akaganeite forms from GR(Cl−) in solutions containing a large excess of
First, a
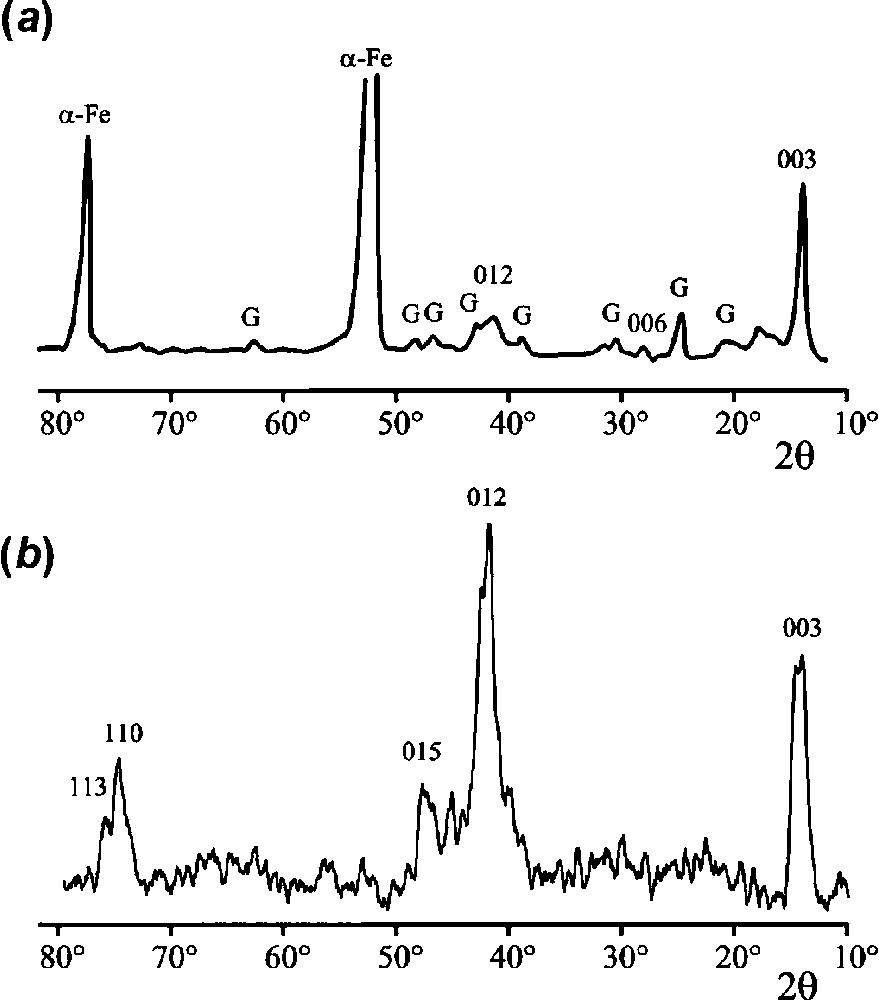
XRD patterns of the ‘ferric
XRD patterns of the ‘ferric
Clichés de diffraction de rayons X de la « rouille verte
Clichés de diffraction de rayons X de la « rouille verte
The two most intense lines visible in the pattern of the dried rust layer are those of the substrate α-Fe. Lines of goethite α-FeOOH are also observed, together with three other lines that can be attributed to the ferric GR. The main one corresponds to an interplanar distance of 0.735 nm (
The pattern obtained by oxidation of
7 Conclusion
The determining role of GRs in the corrosion processes of ferrous alloys in neutral and alkaline media is now well settled. FeII–III hydroxysalts constitute a major step before the formation of the various components of rust and may control partially the properties of the rust layers formed on steel. Therefore, the positive role of various corrosion inhibitors commonly used to prevent degradation of steels in neutral or alkaline media are partially explained by the influence those species may have upon the formation and/or transformation of GRs. Phosphates, nitrites and nitrates are examples of such inhibitors.
Vous devez vous connecter pour continuer.
S'authentifier