1 Introduction
The transformation of a carbonyl group to a methylene unit is indeed an important reaction in synthetic organic chemistry. Various classical types of reduction methods such as alkali metal-mediated reduction in liquid ammonia [1], Lewis acid-promoted metal hydride reduction [2], Clemmensen reduction [3], and Wolf–Kishner–Huang-type reductions [4,5] are employed for the reduction of the carbonyl group. Then other methods were developed, like H3PO2-mediated reduction [6], reduction in supercritical i-PrOH at high temperatures (350–400 °C) [7], hydrogenation of aromatic ketones catalyzed by sol–gel entrapment combined with Pd–[Rh(COD)Cl]2 under high hydrogen pressure (400 psi) [8], a hydrogenation procedure in a three-phase emulsion [9], and a Pd-catalyzed hydrogenation of ketones at high temperature (200 °C) under a hydrogen atmosphere (30 bar) [10]. Also sodium dithionite promoted reduction, Pt and Pd catalyzed hydrogenation, Ru-mediated reduction in the presence of HCO2H/Et3N, electrochemical reduction and yeast-catalyzed reduction [11–15] were reported. Some of the literature methods have disadvantages such as harsh reaction conditions, high reaction temperatures and/or high pressure, toxic reagents; also, a large amount of reducing agents is usually required.
Tashiro et al. pioneered the reduction of aryl ketones to the corresponding alcohols or alkane derivatives in water using various metal–Al alloys (Ni–Al, Co–Al, Cu–Al, Fe–Al). Among them, a Ni–Al alloy in water was found as a good agent to reduce the aromatic ketones and aldehydes to the corresponding cyclohexane derivatives, but a large amount of alloy was employed in these studies [16]. Next, the reduction of acetophenones was performed by using Ni–Al alloy in water under microwave irradiation [17]. The reductive reactions of a series of aromatic ketones with noble metal catalysts such as Rh, Ru, Pd or Pt in the presence of Al powder in water using a sealed tube was reported by them [18]. Raney Ni–Al was found to be very efficient in the reduction of phenol, naphthalenes, biphenyls, acenaphthene and dechlorination of mono and dichlorobiphenyls to the corresponding hydrocarbon derivatives, in the absence of organic solvents at 90 °C in dilute aqueous alkaline solution. The reduction of benzophenones was also carried out using Raney Ni–Al in water with KOH and other alkaline earth hydroxides [19–22]. Xia et.al. studied the influence of triethylamine on the hydrodechlorination reactivity of chlorophenols over Raney Ni catalyst [23]. Facile hydrogenation of ketones catalyzed by platinum on carbon under ordinary pressure and temperatures was reported by Sajiki et.al. [24].
An essential aspect of green chemistry is to utilize water not only as a source of hydrogen and/or oxygen, but also as an alternative solvent [25]. Water has many advantages as a solvent from the viewpoints of its cost, safety, operational simplicity and environmental aspects compared to most organic solvents [26–28]. The chemoselective reduction of various carbonyl compounds to alcohols with ammonia borane, a non-toxic, environmentally benign and easily handled reagent in neat water was achieved with a quantitative conversion and a high isolated yield [29]. Recently, a selective reduction of ketones was also reported based on Ni–Al alloy coupled with a high hydrostatic pressure in an aqueous medium and the selective reduction of unprotected indoles as well as quinolines in water using Ni–Al alloy [30,31]. The reduction or oxido–reduction reaction of cinnamaldehyde and of its derivatives with Ni–Al alloy and Al powder in water was also reported [32].
Previously, benzophenone was selected as the model compound for the reduction of the carbonyl group as well as the aromatic rings [21,33]. In our present study, we also explored the reduction of carbonyl group using Raney Ni–Al alloy and aromatic rings of benzophenone with Raney Ni–Al alloy and Al powder in presence of Pt/C in water at a relatively lower temperature in a sealed tube. To our knowledge, no reports are available regarding the reduction of benzophenone employing these reducing agents in water under mild reaction conditions. In this paper, we demonstrated a simple and convenient method for the reduction of both carbonyl group and aromatic rings using commercially available Raney Ni–Al alloy and Al powder in presence of Pt/C in H2O.
2 Experimental
2.1 Materials and apparatus
All melting points are uncorrected. 1H NMR spectra were recorded at 300 MHz on a Nippon Denshi JEOL FT-300 NMR spectrometer in CDCl3 with Me4Si as an internal reference. IR spectra were measured as KBr pellets on a Nippon Denshi JIR-AQ2OM spectrometer. Mass spectra were obtained using a Shimadzu GC-MS-QP5050A ultrahigh performance mass spectrometer AOC-20I, 100 V equipped with a direct-inlet system. GLC analyses were performed with a Shimadzu gas chromatograph, GC-2010.
2.2 General procedure for the reduction of aromatic compounds
To the mixture of the substrate (20 mg, 0.11 mmol) (Wako), Raney Ni–Al alloy (100 mg, 50:50 wt%), Al powder (500 wt%)(53–150 μm, 99.5%) (Wako) and Pt/C, Pd/C, Ru/C or Rh/C (20 mg) (4.5 mol % metal) was added water (0.5 mL) (Wako distilled water). After heating at 60–80 °C for 3–18 h, the mixture was cooled to room temperature. The solution was diluted with 1 mL of water and then stirred overnight at room temperature in a sealed tube. After 24 h, the solution was extracted with diethyl ether (2 mL × 3) following the reported procedure [32]. The organic layers were combined, dried over MgSO4, filtered through a cotton layer and concentrated in vacuo to give the corresponding hydrogenated product. The yields were determined by GLC analysis using the standard compound (1,2,3,4-tetrahydronaphthalene), and products were identified by GC–MS.
3 Results and discussion
In the present method, the reduction of the carbonyl group and the benzene rings of benzophenone to the corresponding diphenylmethane has been effectively carried out in water under mild conditions. To achieve a more environmentally-friendly chemical process, the reduction of benzophenone (Scheme 1, 1a) was carried out using Raney Ni–Al alloy in water in a sealed tube. Besides the desired product diphenylmethane (Scheme 1, 2a), a mixture of diphenylmethanol (Scheme 1, 3a), cyclohexylphenylmethane (Scheme 1, 4a) and dicyclohexylmethane (Scheme 1, 5a) was also obtained from the reaction. The relative distribution of the products was found to be dependent on the reaction conditions being used. The effect of the reaction temperature, reaction time, amount of Ni–Al alloy and the optimum volume of water for the reduction of benzophenone (1) was investigated.
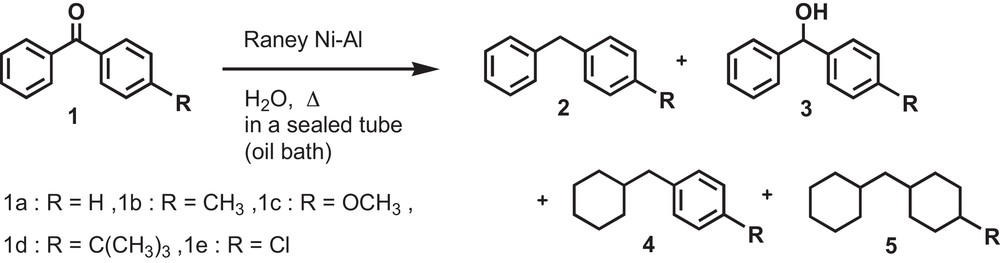
Reduction of benzophenones (1) by using Raney Ni–Al alloy in H2O.
Initially, the effect of the reaction temperature was examined for the reduction of benzophenone (1a) by using Ni–Al alloy in a sealed tube. The reduction product diphenylmethane (2a) was obtained in a good yield at 60 °C for 3 h. It is to be mentioned that the reduction did not proceed at room temperature for 3 h. Then the extent of reduction of benzophenone was found to gradually increase with increasing temperature. At a higher reaction temperature of more than 60 °C, the reduction product 2a started to convert into other products. The higher temperature favors the conversion of 2a to products 4a and 5a (Fig. 1a).
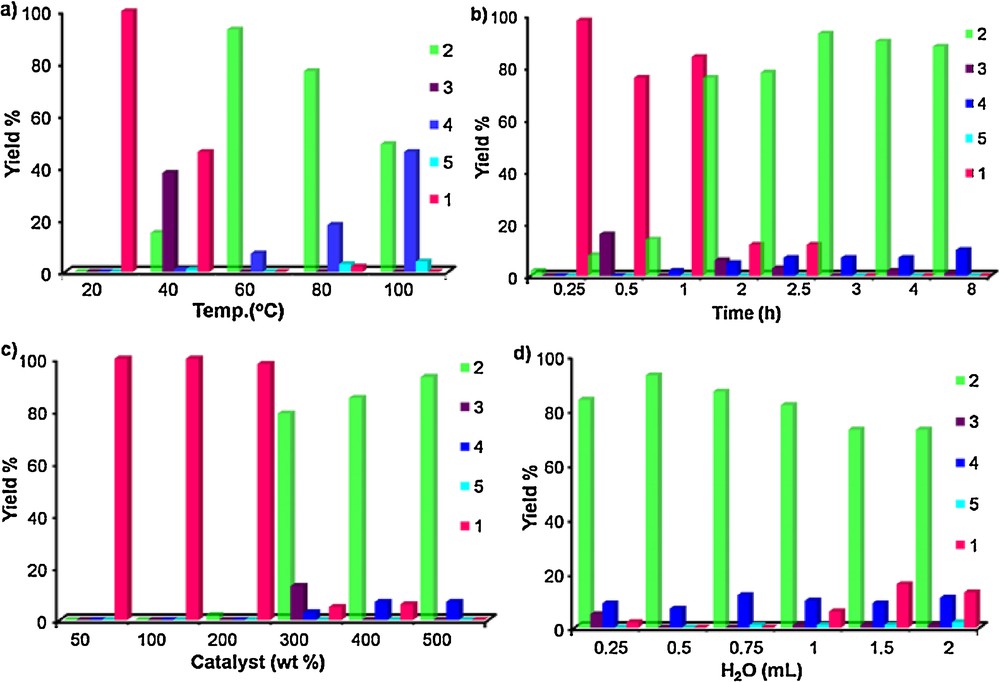
(Color online.) Reduction of benzophenone using Raney Ni–Al alloy; (a) temperature effect; (b) time effect; (c) catalyst effect; (d) H2O effect.
Next, the reduction of benzophenone (1a) was carried out for screening the reaction time at 60 °C by using Raney Ni–Al alloy. During the time of reaction of 1a for 3 h, the reduction product 2a was found in the highest yield (93%). At a longer reaction time of more than 3 h, the product 2a tended to transform into 3a and 4a (Fig. 1b). Subsequently, the reduction of 1a was conducted in the stated reaction conditions to observe the effects of the amount of reagent. While increasing the amount of Raney Ni–Al alloy wt% from 50 to 500, the reduction of benzophenone 1a did not start until 200 wt% of reagent was used. Finally, a 500 wt% amount of Raney Ni–Al alloy was found to be the most suitable quantity to obtain the reduction product 2a in a good yield (Fig. 1c).
The reduction of 1a by using 500 wt% Raney Ni–Al alloy was also investigated under the above reaction conditions to observe the effects of the volume of water. Using 0.5 mL of water, product 2a was obtained in a high yield. On the other hand, decreasing the volume of water to 0.25 mL led to a lesser reduction of 1a. Besides, a lesser reduction of 1a was also observed with increasing the volume of water (0.75–2 mL). This shows that, compared to 0.5 mL of water, a smaller or larger volume of water is not suitable for a sufficient interaction between benzophenone (1a) and the reagents. This indicates that 0.5 mL is the optimum volume of water for the reduction of 1a (Fig. 1d). From these results, it was concluded that a 500 wt% amount of Raney Ni–Al alloy in 0.5 mL of water at 60 °C for 3 h gives the optimum reaction conditions for the reduction of benzophenone (1a) to diphenylmethane (2a) with high yield.
Using these optimized reaction conditions, we investigated the reduction kinetics of benzophenone (1a); the results are presented in Table 1 (ESI Fig. S6).
Reduction of benzophenone (1a) by using Ni-Al in H2Oa,b.
Entry | Time (h) | 2a | 3a | Yield [%]c,d 4a | Recovery 1a |
1 | 0.25 | 1 | 0 | 0 | 99 |
2 | 0.5 | 1 | 0 | 0 | 99 |
3 | 0.75 | 7 | 27 | 0 | 66 |
4 | 1 | 28 | 24 | 2 | 46 |
5 | 1.5 | 37 | 24 | 2 | 37 |
6 | 2 | 84 | 2 | 5 | 9 |
7 | 2.5 | 84 | 1 | 6 | 9 |
8 | 3 | 93 [86] | 0 | 7 | 0 |
9 | 12 | 80 | 0 | 20 | 0 |
10 | 24 | 71 | 0 | 29 | 0 |
a Substrate: 20 mg (0.11 mmol), Ni–Al alloy: 100 mg (500 wt%), H2O: 0.5 mL.
b Conditions: temperature, 60 °C.
c The yields were determined by GLC.
d The isolated yields are shown in square brackets.
It was observed that with increasing time, the maximum yield (93%) of the desired compound 2a was obtained after 3 h. When the reaction time was increased to more than 3 h, compound 2a was gradually converted into compound 4a.
It is assumed that diphenylmethanol (3a) serves as an intermediate for the final product 2a under the reaction conditions employed. Next, 3a was subjected to the same reaction conditions and it showed a similar reduction pattern to that of benzophenone (ESI Table S5). Then the reduction of substituted benzophenones was also examined (Table 2).
Reduction of substituted benzophenones (1) by using Ni-Al in H2Oa,b.
Entry | Substrate | 2 | 3 | Yield [%]c,d 4 | Recovery 1 |
1 | H | 93 [86] | 0 | 7 | 0 |
2 | CH3 | 94 [88] | 0 | 0 | 6 |
3 | OCH3 | 99 [90] | 0 | 0 | 1 |
4 | C(CH3)3 | 7 | 4 | 0 | 89 |
5 | Cl | 10 (2a) | 11 (3a) | 0 | 79 |
a Substrate: 20 mg (0.11 mmol), Ni–Al alloy: 100 mg (500 wt%), H2O: 0.5 mL.
b Condition: temperature, 60 °C; time: 3 h.
c The yields were determined by GLC.
d The isolated yields are shown in square brackets.
The substituted benzophenones underwent reduction under standard conditions. 4-Methylbenzophenone (1b) showed a similar activity to that of compound 1a to provide product 2b with a yield of 94%; 4-methoxybenzophenone (1c) gave a 99% yield of carbonyl group reduction product. Probably because of the bulky tert-butyl group, 4-tert-butylbenzophenone (1d) gave a negligible amount of the corresponding diphenylmethane derivative 2d along with the recovery of the unreacted starting compound 1d. In order to confirm that assumption, we further examined the reduction of 4-tert-butylacetophenone under the same reaction conditions. 1-(4-tert-Butylphenyl) ethanol (61%) was obtained with 39% recovery of the starting material. An electronegative substituent like 4-chlorobenzophenone (1e) led to dechlorination along with a large recovery of unreacted-starting material (79%) under the same reaction conditions. So the outcome of the reduction depends on the substituent pattern of benzophenone.
The reduction of phenyl benzyl ketone and acetophenone was carried out under the same reaction conditions using Raney Ni–Al alloy. They gave 1,2-diphenylethane (94%) and ethylbenzene (96%) respectively in almost quantitative yield (Table 3).
Reduction of various ketones (1) by using Ni–Al in H2Oa,b.
Entry | Substrate | Product | Yield [%]c,d | Recovery |
1 | 94 [90] | 3 | ||
2 | 96 [64] | 4 |
a Substrate: 20 mg (0.11 mmol), Ni–Al alloy: 100 mg (500 wt%), H2O: 0.5 mL.
b Conditions: temperature, 60 °C; time, 3 h.
c The yields were determined by GLC.
d The isolated yields are shown in a square bracket.
4 Transition-metal-catalyzed reduction
It was found that using Raney Ni–Al alloy at 60 °C for 3 h is effective for the reduction of the carbonyl group to provide methylene units. But the reduction of the aromatic ring was not facile under the same reaction conditions. With this in mind, various transition metal catalysts (Pt/C, Pd/C, Ru/C and Rh/C) were introduced into the mixture of Al powder to observe the effect of these catalysts. Moreover, the reaction temperature was raised to 130 °C to perform the reduction of the aromatic rings of benzophenone.
No reaction of aromatic rings was observed for 3 h using Pd/C, Ru/C and Rh/C. But in the presence of Pt/C, the reduction of carbonyl group as well as the reduction of one and of both aromatic rings occurred (Table 4; entry 2). By using only Raney Ni–Al alloy, the reduction product 5a was found in a lower yield compared to Pt/C. These results clearly show that Pt/C is a highly effective catalyst for the reduction of the aromatic ring. For transition–metal catalysts along with Al powder in water, the order of strength for hydrogenation was found in the following order: Pt/C> Raney Ni–Al alloy > Pd/C > Ru/C> Rh/C.
Reduction of benzophenone (1a) by using Al powder and catalyst in H2Oa,b.
Entry | Catalyst | Additives | 2a | 3a | Yield [%]c 4a | 5a | Recovery 1a |
1 | Ni-Al | – | 77 | 0 | 19 | 3 | 1 |
2 | Pt/C | Al | 41 | 0 | 38 | 21 | 0 |
3 | Pd/C | Al | 51 | 7 | 0 | 0 | 43 |
4 | Ru/C | Al | 34 | 0 | 0 | 0 | 66 |
5 | Rh/C | Al | 17 | 0 | 0 | 0 | 83 |
a Substrate: 20 mg (0.11 mmol), Al powder: 100 mg (500 wt%), catalyst: 20 mg (4.5 mol% metal), H2O: 0.5 mL.
b Conditions: temperature, 130 °C; time, 3 h.
c The yields were determined by GLC.
So it turned out that Al powder in water is a good reducing agent in the presence of Pt/C. Accordingly, the reduction of benzophenone (1a) was carried out using this reducing agent in a sealed tube. It was observed that a mere increase in temperature was not enough to yield the desired aromatic ring reduction product. Then the reaction time was extended to 12 h with the same reaction temperature to obtain the required reduction product.
When the reduction of benzophenone (1a) was carried out at 130 °C for 12 h by using Raney Ni–Al alloy, a mixture of 2a (8%), 4a (82%) and 5a (10%) was found (Table 5; entry 1). No reduction occurred when only Pt/C was used under the same reaction conditions (Table 5; entry 3). For the complete reduction of benzophenone (1a), an introduction of another reagent was found necessary alongside Raney Ni–Al alloy. The addition of Pt/C and Al powder along with Raney Ni–Al alloy was found suitable for the effective reduction to afford product 5a as the sole product (90%) (Table 5; entry 6). These results clearly show that a transition-metal catalyst increases the reducing capability of Raney Ni–Al alloy. Consequently, using these reagents, the reaction temperature could be gradually decreased. We found that a temperature of 80 °C for 18 h was the right condition for the reduction of both aromatic rings of benzophenone. At this relatively lower temperature a new reduction product dicyclohexylmethanol (6a) was found in trace amounts. Thus Pt/C was also established as an ideal catalyst in this case. So it is suggested that Pt/C is capable of acting as the most effective catalyst in the presence of Raney Ni–Al alloy and Al powder [34] (Scheme 2) (Table 6).
Reduction of benzophenone (1a) by using Ni–Al, Al powder and Pt/C in H2Oa,b.
Entry | Catalyst | Additives | 2a | 4a | Yield [%]c 5a | Recovery 1a |
1 | Ni-Al | – | 8 | 82 | 10 | 0 |
2 | Ni-Al | Al | 6 | 87 | 7 | 0 |
3 | Pt/C | – | 0 | 0 | 0 | 100 |
4 | Pt/C | Al | 69 | 23 | 5 | 3 |
5 | Pt/C + Ni-Al | – | 17 | 0 | 84 | 0 |
6 | Pt/C + Ni-Al | Al | 2 | 8 | 90 | 0 |
a Substrate: 20 mg (0.11 mmol), Ni–Al alloy: 100 mg (500 wt%), Al powder: 100 mg (500 wt%), catalyst: 20 mg (4.5 mol% metal), H2O: 0.5 mL.
b Condition: temperature, 130 °C; time, 12 h.
c The yields were determined by GLC.
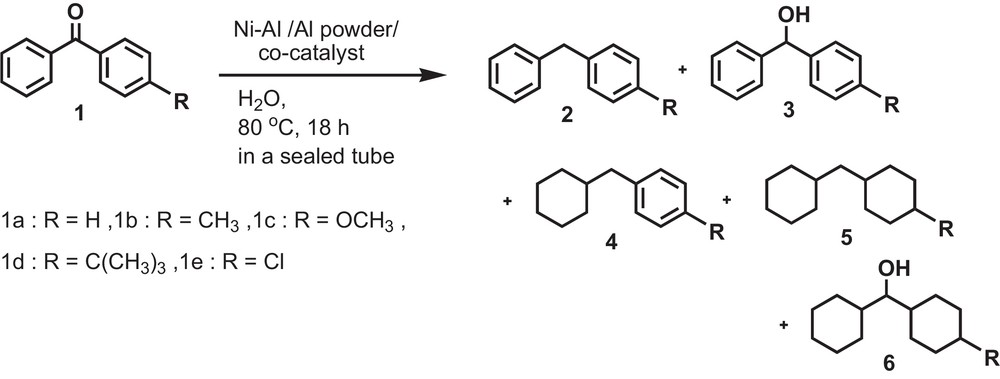
Reduction of substituted benzophenones (1) by using Raney Ni–Al, Al powder and Pt/C in H2O.
Reduction of benzophenone (1a) by using Ni–Al, Al powder and catalyst in H2Oa,b.
Entry | Catalyst | 2a | 4a | Yield [%]c 5a | 6a | Recovery 1a |
1 | None | 10 | 82 | 8 | 0 | 0 |
2 | Pt/C | 0 | 0 | 92 | 8 | 0 |
3 | Pd/C | 4 | 36 | 60 | 0 | 0 |
4 | Ru/C | 0 | 1 | 97 | 2 | 0 |
5 | Rh/C | 0 | 2 | 92 | 6 | 0 |
a Substrate: 20 mg (0.11 mmol), Ni-Al alloy: 100 mg (500 wt%), Al powder: 100 mg (500 wt%), catalyst: 20 mg (4.5 mol% metal), H2O: 0.5 mL.
b Conditions: temperature, 80 °C; time, 18 h.
c The yields were determined by GLC.
We also explored the effect of the substituent on the complete reduction of benzophenones (1) under the above reaction conditions, as reported in Table 7. We obtained a high yield (83%) of both aromatic ring reduced products (cis and trans) (5b) for 4-methylbenzophenone (1b) along with 4-methyldicyclohexylmethanol (6b) in 17% yield. In the case of 4-methoxybenzophenone (1c), 84% of compound 5c (cis and trans) and 5a (16%) were obtained. These results strongly suggest that the newly developed reducing agent not only reduces the aromatic ring but also cleaves the polar C–O bond. In case of 4-tert-butylbenzophenone (1d), the complete reduction product (5d) was obtained in a lower yield (58%) along with 42% of 4-tert-butyldicyclohexylmethanol (6d). We did not observe any steric effect arising from the tert-butyl group under the conditions used in the reduction, because the tert-butyl group is placed in para position, which is too far to exert any steric effect on the carbonyl moiety. To ensure this, we also examined the reduction of 4-tert-butylacetophenone under the same reaction conditions. Only 35% of 1-tert-butyl-4-ethylcyclohexane (cis & trans) were obtained with the formation of 1-(4-tert-butylcyclohexyl)ethanol (65%, cis & trans). 4-chlorobenzophenone (1e) leads to a mixture of compounds 2a (31%), 4a (49%) and 5a (20%) resulting in dehalogenation.
Reduction of substituted benzophenones (1a) by using Ni–Al, Al powder and Pt/C in H2Oa,b.
Entry | Substrate | 2 | 4 | Yield [%]c 5 | 6 | Recovery 1 |
1 | H | 0 | 0 | 90 | 10 | 0 |
2 | CH3 | 0 | 0 | 83d | 17d | 0 |
3 | OCH3 | 0 | 0 | 16 (5a) + 84d | 0 | 0 |
4 | C(CH3)3 | 0 | 0 | 58d | 42d | 0 |
5 | Cl | 31 (2a) | 49 (4a) | 20 (5a) | 0 | 0 |
a Substrate: 20 mg (0.11 mmol), Ni–Al alloy: 100 mg (500 wt%), Al powder: 100 mg (500 wt%), catalyst: 20 mg (4.5 mol% metal), H2O: 0.5 mL.
b Condition: temperature, 80 °C; time: 18 h.
c The yields were determined by GLC.
d cis and trans.
Next, the reduction of intermediate compounds (2) of benzophenone derivatives (1) was examined by using the reagents as shown in Table 8. All substituted diphenylmethanes underwent complete reduction to yield cis and trans products at 60 °C within 12 h. But 4-methoxydiphenylmethane (2c) showed 79% complete reduction with a concurrent cleavage of the polar CO bond to form 5a (19%) as mentioned previously (Scheme 3).
Reduction of various intermediate compounds (2) by using Ni–Al, Al powder and Pt/C in H2Oa,b.
Entry | Substrate (2) | Yield [%]c | |
5 | Recovery 2 | ||
1 | H | 100 | 0 |
2 | CH3 | 100d | 0 |
3 | OCH3 | 21(5a) + 79d | 0 |
4 | C(CH3)3 | 100d | 0 |
a Substrate: 20 mg (0.11 mmol), Ni–Al alloy: 100 mg (500 wt%), Al powder: 100 mg (500 wt%), Catalyst: 20 mg (4.5 mol% metal), H2O: 0.5 mL.
b Condition: temperature, 60 °C; time, 12 h.
c The yields were determined by GLC.
d cis and trans.
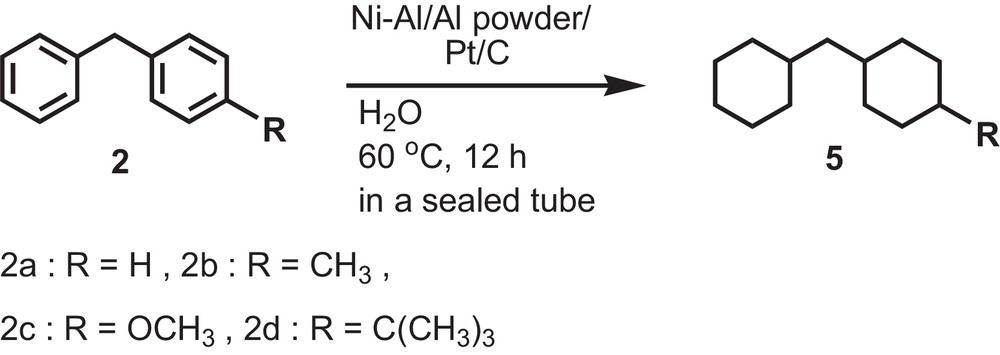
Reduction of substituted diphenylmethanes (2) by using Raney Ni–Al, Al powder and Pt/C in H2O.
Finally, we tried to reduce various types of ketones using the above catalysts under the same reaction conditions. For a rigid structure of fluorenone, we obtained a comparatively lower yield (54%) of both aromatic ring reduced products (Table 9; entry 3). In this case, the yield of 30% carbonyl group and 11% hydroxyl group containing aromatic ring reduction products were obtained. These types of reduction products were also reported by Hashimoto et al. [18]. On the other hand, for a flexible structure of benzyl phenyl ketone and benzil, 72 and 75% of 1,2-dicyclohexylethane were obtained along with 28 and 18% of 1,2-dicyclohexylethanol (Table 9; entries 2, 4). Diphenylmethanol also showed the same reduction pattern, producing 86% of dicyclohexylmethane and 14% of dicyclohexylmethanol (Table 9; entry 1). From these results, it is concluded that the approach of different types of ketones towards the highly porous Pt metal catalyst's surface depends on the nature of the substrates.
Reduction of various ketones by using Ni–Al, Al powder and Pt/C in H2Oa,b.
Entry | Substrate | Product Yield [%]c | Recovery | |||
1 | 0 | |||||
2 | 0 | |||||
3 | 0 | |||||
4 | 0 |
a Substrate: 20 mg (0.11 mmol), Ni–Al alloy: 100 mg (500 wt%), Al powder: 100 mg (500 wt%), catalyst: 20 mg (4.5 mol% metal), H2O: 0.5 mL.
b Condition: temperature, 80 °C; time, 18 h.
c The yields were determined by GLC.
One of the most important advantages of this method is that the reaction can be carried out in water, which is the most benign and is readily available. Besides, water serves as an economic source of hydrogen that obviates the need for any addition of hydride or hydrogen gas. Moreover, this method precludes any use of strong base/alkali. Probably, the Ni of the alloy readily adsorbs hydrogen, which, in turn, facilitates the effective hydrogenation of the substrates. In addition, the reaction does not produce any toxic wastes, while the only by-product that forms is an alumina-supported Ni catalyst (Ni/Al2O3) that could be easily filtered out and can be used in other hydrogenation processes.
5 Proposed reaction pathway
The reaction mechanism for reduction is not yet fully understood. It may be proposed that the aluminum metal of the Raney Ni–Al alloy reacts with water, producing a reactive form of hydrogen, while the highly porous nickel metal surface offers sites for the adsorption of those in situ generated active type of hydrogens. Also we have observed that when Pt/C was added to Al powder and Raney Ni–Al alloy, it became more effective in water. Here, the solvent water may play an important role in the creation of an active catalytic surface (Fig. 2) [20].
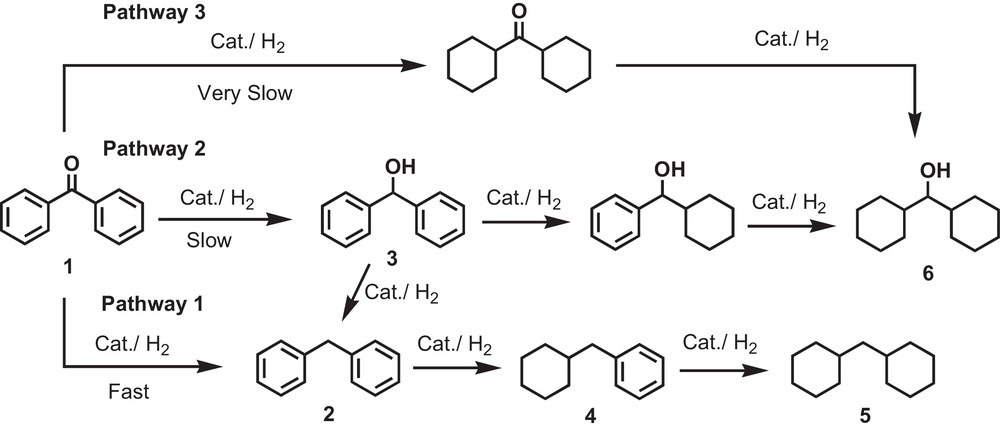
Proposed reaction pathways for the reduction of benzophenone.
Based on the GC–MS results, detailed reaction pathways for the reduction of benzophenone can be proposed [35]. In pathway 1, the reduction of the carbonyl group produced diphenylmethane (2) as the main product, while aromatic rings were gradually reduced. On the other hand, the carbonyl group is reduced to benzhydrol (3), cyclohexylphenylmethanol and dicyclohexylmethanol (6) successively, as depicted in pathway 2. Moreover, compound 6 was also produced in pathway 3. We can assume that pathway 1 is faster than the other ones (2 and 3). It may be concluded that the approach of benzophenone towards the catalyst's surface is much more favorable for obtaining the desired product in a high yield.
6 Conclusion
It was found that the carbonyl group of benzophenone could be converted into the corresponding diphenylmethane by using Raney Ni–Al alloy in a high yield. Besides, both aromatic rings were also reduced in a high yield with Ni–Al alloy and Al powder in the presence of Pt/C in H2O under mild reaction conditions in a sealed tube. Without using any organic solvents, Raney Ni–Al alloy in water turns out to be a powerful reducing agent. The nature of reduction products greatly depends on the temperature, reaction time, volume of water and the amount of catalyst being used. We believe that Raney Ni–Al alloy in water provides a very useful technique for the reduction of aromatic compounds. This novel approach is characterized by the ease and quickness of the reaction, its simplicity of manipulation and the mildness of the reaction conditions. Moreover, the convenience and low costs are also additional advantages of this method.
Acknowledgement
This study was conducted under the Cooperative Research Program of “Network Joint Research Center for Materials and Devices (Institute for Materials Chemistry and Engineering, Kyushu University)”.