1 Introduction
Electrospray is a phenomenon generating ultrafine droplets, when a high voltage is applied to the surface of liquid (Fig. 1) [1], and it is used as a powder-processing method. To date, electrospray pyrolysis, i.e., combination of the electrospray and an in-flight thermal treatment, has attracted much attention as a preparation method of functional nano- or micro-particles, such as submicrometer Y2O3 powder [2], CeO2 nanoparticles [3], and so on. We previously reported the preparation of spherical TiO2 nano- and micro-particles by the electrospray pyrolysis method [4]; as a precursor, titanium(IV) bis(ammonium lactato) dihydroxide aqueous solutions (TALH aq 0.2–20 wt%) were used, and we succeeded to prepare spherical anatase TiO2 particles [4]. However, the final powder yield (Ti-base) at the electrostatic collector was only ∼6%, because synthesized particles with the same electrical charge repelled each other, and most of them deposited on the reactor walls during the pyrolysis [4]. To overcome this low-yield problem, as the part 1 of this paper, we developed a double-nozzle electrospray system, where positively and negatively charged sprays were superimposed to neutralize the charges of droplets [5]. Relatively fine and monodisperse droplets (7.58 μm in diameter with a geometrical standard deviation of 1.37) were obtained by the double-nozzle electrospray.
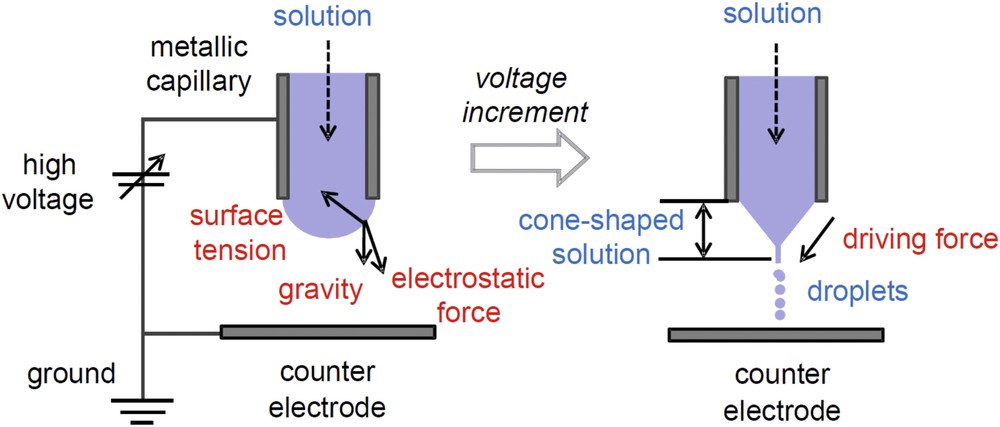
Schematic illustration of electrospray [1].
In this study, as the part 2, we report the synthesis and characterization of anatase TiO2 powders by the double-nozzle electrospray pyrolysis method. Thanks to the neutralization of droplets by the double-nozzle electrospray, the final TiO2 powder yield after pyrolysis was much improved from 6% [4] to 55.4%. Photocatalytic activity for H2 evolution was studied for the anatase TiO2 powders prepared by the double-nozzle electrospray pyrolysis method.
2 Experimental procedure
2.1 Double-nozzle electrospray pyrolysis: powder production and yield calculation
Fig. 2 shows a schematic illustration of the double-nozzle electrospray pyrolysis system. In the double-nozzle setting, TALH aqueous solution (2.0 wt%) and pure H2O were separately injected into capillaries by using two syringe pumps (30 mL/h each), and were electrosprayed by using positive (+4 kV) and negative (−4 kV) DC voltage, respectively. Coalescence of droplets with positive and negative charges resulted in charge neutralization. Under a stream of dry clean air (5 L/min), the droplets were carried to the stainless steel tube (50 mm in diameter and 50 cm in length) heated with a tubular furnace at 350, 400 or 450 °C. Within the stainless steel tube reactor, the TALH aq droplets (diluted to 1 wt%) were dried and pyrolyzed into TiO2 particles. In this study, the TiO2 particles were collected by using a glass or quartz fiber filter (instead of an electrostatic collector [4]) due to the charge neutralization. The connection part between the outlet of the stainless steel tube reactor and the inlet of the filter holder was heated with a ribbon heater to prevent water vapor condensation. The flow rates of air sucked by a suction pump measured by using a rotameter (hereinafter referred to as “pump suction flow rates”) were set to 5, 10 or 15 L/min. These pump suction flow rates were determined to be larger than those at the inlet of the filter holder for each furnace temperature calculated by using PHOENICS of computational fluid dynamics (CFD) simulation software (Fig. S1). A water vapor trap and a cylinder filled with silica gel were used to remove the water entering a pump.

Schematic illustration of the double-nozzle electrospray pyrolysis system.
In order to determine the sample yield, a quartz fiber filter (Pallflex 2500 QAT-UP) with a heatproof temperature of 1093 °C was used. After the 1-h sampling of TiO2 particles, the quartz fiber filters with samples were weighed to calculate the total collection mass. Then, the filters with samples were heated at 500 °C for 1 h to remove the organic residue. The mass difference before and after the heating corresponds to the organic remnant mass. The mass difference between the pristine filter and that after the heating corresponds to the TiO2 sample mass. Using these values, the Ti-based sample yield (compared with the starting material) was calculated.
2.2 Characterization
Characterization methods of the obtained TiO2 powder are similar to those in our previous study [4]. Briefly, the microstructure of the TiO2 powders was observed by scanning electron microscopy (SEM, JSM-6500F, JEOL). The constituent phases of the powder were analyzed by X-ray diffraction (XRD, Cu-Kα, 40 kV and 40 mA, MultiFlex, Rigaku). The photocatalytic H2 evolution (water splitting) was carried out in a closed gas-circulation system in an inner irradiation-type photoreactor made of Pyrex glass as described in previous studies [6–9]. TiO2 powders (1 g each) prepared by the electrospray pyrolysis method were suspended in an aqueous ethanol solution (720 mL distilled H2O + 80 mL ethanol) by using a magnetic stirrer. A high-pressure Hg lamp (Ushio, Japan; UM-452, 450 W) was utilized as the UV light source. The mixture was deaerated by purging with Ar gas stream. To maintain the reaction temperature, cooling water was circulated through a cylindrical Pyrex jacket located around the light source. The evolved gasses were periodically analyzed by using an on-line gas chromatograph (Shimadzu GC-8A, Molecular sieve 5A, TCD, Ar Carrier) until the reaction time reached 3 h. A commercial TiO2 powder (P25, Degussa/Nippon Aerosil Co., Ltd., mean primary particle size of 21 nm) was used as a reference material.
3 Results and discussion
3.1 Effects of furnace temperatures and pump suction flow rates on the yield
First, effects of the furnace temperatures (350, 400 and 450 °C) and the pump suction flow rates (5, 10 and 15 L/min) on the sample yields were evaluated (Fig. 3). When the furnace temperature was 450 °C, the pump suction flow rates were set as 10, 12 and 15 L/min, because, at 5 L/min, an electric discharge occurred around the spray nozzles, as reported in the literature studies [10,11]. In Fig. 3(a), it is evident that the total collection mass decreased with increasing furnace temperature, which is attributed to the change of organic remnant mass as shown in Fig. 3(b). In Fig. 3(a), the total collection mass increased with increasing pump suction flow rate, which can be also explained by the increased organic remnant by the reduction of in-flight time in the furnace. As shown in Fig. 3(c) and (d), the maximum Ti-based yield, 55.4%, was obtained for the conditions of 400°C–10 L/min. Also, a high Ti-based yield, 50.4%, was obtained for the conditions of 450°C–12 L/min. The peak around 10 L/min can be explained by the longest in-flight time in the reactor, which is in good agreement with the simulation done using the Phoenics software (Fig. S1) [12]. When the pump suction flow rate is smaller, more droplets attached to the wall of the reactor, and when the flow rate is larger, thermal decomposition of TALH becomes insufficient. In the following sections, the conditions of 400°C–10 L/min were used as the optimum ones.

Effects of the furnace temperatures and the pump suction flow rates on the yield: (a) Total collection mass, (b) organic remnant mass, (b) TiO2 collection mass, and (d) Ti-based yield.
3.2 Characterization of TiO2 powders by electrospray pyrolysis
After 60 min sampling of the electrospray-pyrolyzed particles under the conditions of 400°C–10 L/min, the samples with filters were ultrasonicated in water. After the ultrasonication, the powders were dried on a ceramic hot-plate heated at 500 °C. Also, another sample was just scraped off from the filter (without ultrasonication). Fig. 4 shows SEM images and appearances of the electrospray-pyrolyzed samples collected by (a and c) the ultrasonication method and (b and d) scraped off method, respectively. With the ultrasonication (Fig. 4(a)), the particles had irregular shapes, with the size of ca. 50 nm–10 μm. However, without ultrasonication (Fig. 4(b)), most of the particles retained their original spherical-like and/or hollow shapes, typical shapes by electrospraying, with the size of ca. 100 nm–7 μm. Although spherical particles were obtained in Fig. 4(b), the particle size distribution was much wider than that of the previous study using the single-nozzle electrospray [4], where monodisperse TiO2 microspheres were obtained. The wider particle size distribution by the double-nozzle setting is attributed to the neutralization and hence the coalescence of the droplets. In the part 1 (see Fig. 13 of Ref. [5]), the mean droplet size by the double-nozzle electrospray was 7.58 μm, which theoretically corresponds to the final TiO2 particle size of ca. 0.8 μm. Hence the experimental TiO2 size distribution of ca. 100 nm–7 μm indicates the coalescence of the droplets.

SEM images and appearances of electrospray-pyrolyzed samples collected by (a and c) the ultrasonication method and (b and d) scraped off method.
Fig. 5 shows XRD patterns of electrospray-pyrolyzed samples collected by the ultrasonication method and the scraped off method. The main constituent phase of both samples was anatase TiO2; however, the broad peaks indicated the low crystallinity of TiO2 as well as the existence of some residual organic impurities. Since the ultrasonicated sample was shortly dried by the ceramic hot-plate, the peaks became slightly sharper than those without ultrasonication. Consequently, with the additional annealing at 500 °C for 1 h for the ultrasonicated sample, the sample became whitish and the anatase peaks became more evident (Fig. S2).
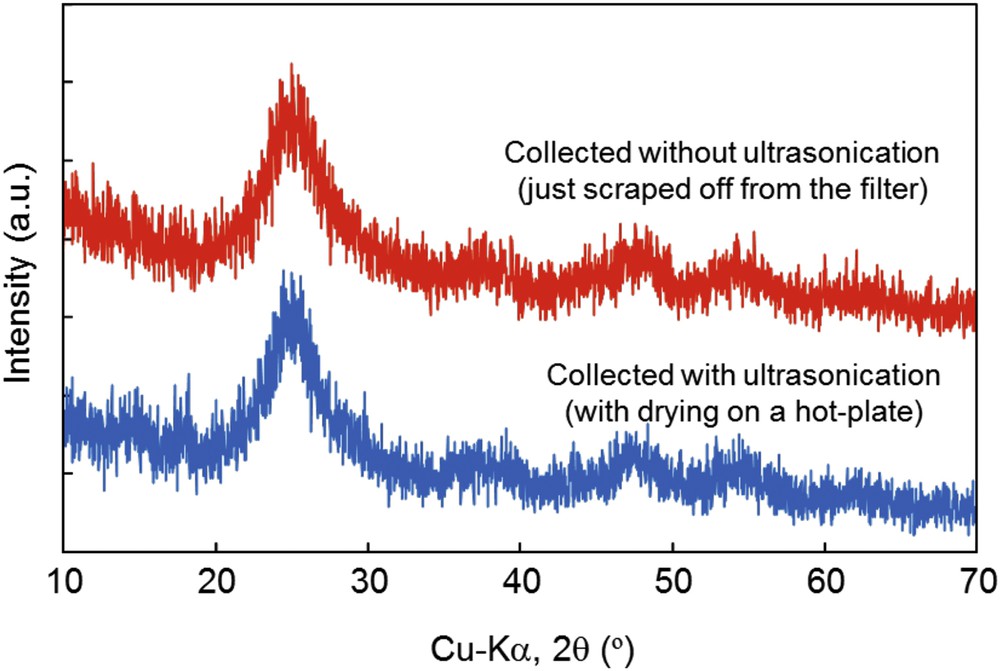
XRD patterns of electrospray-pyrolyzed samples collected by the ultrasonication method (with drying) and the scraped off method.
Fig. 6 demonstrates the photocatalytic H2 evolution from the water splitting reaction over the TiO2 powders made by the electrospray pyrolysis method. TiO2 P25 powder was also measured under the same conditions as a reference. In good accordance with the XRD results, finer TiO2 powders with some organic impurities showed better hydrogen evolution. This tendency was the same as our previous report [4]. The results can be explained by the combination of (i) impurity effect (residual organics acted as a sacrificial agent for oxygen), (ii) doping effect (absorbing visible light, potentially by nitrogen or carbon doping) and (iii) reasonable surface area and crystallinity. Photographs of the reactor before, during and after UV light irradiation are shown in Fig. S3.

Photocatalytic H2 evolution from the water splitting reaction over the TiO2 powders made by the electrospray pyrolysis method. A commercial TiO2 powder (P25) was also measured under the same conditions as a reference.
3.3 Effectiveness and future requirement of the double-nozzle electrospraying
As discussed in the Part. 1 [5], double-nozzle electrospraying with different charges is effective for the charge neutralization of droplets. In an early study by Langer and Yamate in 1969 [13], they demonstrated that the double-nozzle electrospraying was effective to prepare core-shell type particles, e.g., a hard wax coating with a glycerin core. In 1997, Borra et al. [14] utilized the double-nozzle electrospraying as a homogeneous mixing method in chemical reactions. In this paper, we also demonstrated the effectiveness of the double-nozzle electrospraying, viz., to improve the yield of TiO2 powder synthesis from a liquid precursor. Some more studies, however, are still required to suppress the increase of the final particle size via the charge neutralization of droplets. As for the electrospray pyrolysis, more advanced reactor design (size/shape of the furnace, gas flow, position of spray nozzles, etc.) will be promising to solve the problem.
4 Conclusions
We have reported the synthesis and characterization of anatase TiO2 powders by the double-nozzle electrospray pyrolysis method. By using the double-nozzle setting, the Ti-based yield was much improved from 6% [4] to 55.4%. However, due to the charge neutralization and the coalescence of droplets, the particle size distribution of the TiO2 powders became much wider than that of the single nozzle setting. The brownish anatase TiO2 powder containing some organic residues showed better photocatalytic performance, compared with heat-treated whitish powder and commercial TiO2 P25 powder. In this research, the TiO2 precursor and H2O were used as the double-nozzle sources, but further improvement is promising, such as TiO2 and SrO precursors to prepare SrTiO3.