1. Introduction
Emissions of gases containing organic compounds result from various natural sources, industrial, transportation (outdoor sources) and household (indoor sources) activities [1, 2, 3, 4]. Alongside major pollutants of municipal waste thermal incinerators (NOx, SO2, HCl, HF, CO, heavy metals, mineral pollutants) gas emissions contain different volatile organic compounds (VOCs) consisting in hydrocarbons, derivatives containing oxygen, halogenated derivatives, dioxins and furans [5, 6, 7, 8]. VOCs are a group of ubiquitous contaminants which are responsible for atmospheric pollution, and which can contribute to the destruction of the ozone layer or as a precursor of photochemical smog and to the creation of global warming [3, 5, 6, 7]. As a result of specific properties (high volatility, specific odour, toxicity, carcinogenic and mutagenic nature), VOCs represent a potential risk for human health as well [6, 9, 10].
The emissions of VOCs can be controlled using methods based on recovery and destruction [2, 3, 11, 12]. Several traditional technologies, such as adsorption at low concentration and thermal oxidation for high concentration, have been employed to removing VOCs from emission with many advantages and limitations [6, 7, 13, 14, 15]. Catalytic oxidation has been evidenced to be one of the most reliable and suitable technology for the post-treatment emissions at low aromatic or non-aromatic VOCs concentration [3, 12, 16, 17]. It usually requires lower temperatures than thermal oxidation, due to the use of catalysts [2, 7, 11, 18]. Low-temperature catalysts involving noble metals and metal oxides provide the possibility of fast and selective production of the targeted chemical products (CO2 and H2O) under relatively mild conditions [8, 12, 19, 20, 21]. The transitional metal oxides (V2O3, MnO2, WO2, CeO2, CuO2, Cr2O3, Fe2O3) loaded on supports (TiO2, Al2O3, SiO2) show catalytic activity in the oxidative degradation of aromatic and halogenated VOCs [2, 7, 11, 14, 18, 22, 23].
In past decades, extensive research has been carried out for the oxidation of gas stream containing non-halogenated or halogenated VOCs using different supported vanadia-based catalysts. These researches are presented in [2, 11, 24, 25, 26, 27, 28, 29, 30]. The catalysts based on V2O5–WO3/TiO2 and V2O5-MoO3/TiO2 were originally designed for controlling nitrogen oxides emissions, via its selective reduction using suitable reducing agents’ (ammonia or urea) and are known as SCR-DeNOx catalysts. Selective catalytic reduction (SCR) of NOx with ammonia is the most efficient method for reducing NOx to N2 (De-NOx) and it is widely used in EU, USA and Japan [2, 11].
The structure of the TiO2 support in the anatase crystalline type [24, 25, 31]. Vanadia-based SCR-DeNOx catalysts show chlorine poisoning resistance [2, 11, 29, 32, 33, 34]. Researchers have demonstrating that the use of V2O5–WO3/TiO2 commercial catalysts (by IHI/Japan) is a viable alternative for treatment of gas emissions with a low content of VOCs [35, 36, 37], and for oxidation of the mercury from gaseous emissions [38, 39, 40]. The most often applied SCR-DeNOx catalyst consists of vanadia on titania support, with the addition of WO3 to increase the temperature window, SiO2 to stabilize the structure and MoO3 to make the catalyst more resistant towards poisoning by SO2 [2, 11, 34, 41].
According to literature, three degradation mechanisms were proposed to describe the catalytic oxidation of organic compounds over metal or metal oxide-supported catalysts: Mars–van Krevelen (MvK) model (two-stage redox model), Langmuir–Hinshelwood (L–H) model, and the Eley–Rideal (E–R) model. The validity of each mechanism is determined by the catalyst composition and the VOC composition [4, 12, 32, 42, 43].
In this paper, the kinetic investigation of the catalytic oxidation process of aromatic VOCs in the presence of the V2O5–WO3/TiO2(0.53 wt% V2O5) commercial catalyst, is presented. Benzene (C6H6) and its mono-halogenated derivatives such as chlorobenzene (C6H5Cl) and bromobenzene (C6H5Br) were used as model compounds of aromatic VOCs. The kinetic investigation aims to evaluate the apparent activation energy (Ea) and effective constant rate (kef) of catalytic oxidation reaction of the chlorobenzene and bromobenzene comparative with benzene. The experimental results are of interest to the literature because they are obtained using a commercial catalyst, simulating the operating real conditions of industrial process.
2. Materials and methods
2.1. Catalyst
For this study the honeycomb monoliths V2O5–WO3/TiO2(0.53 wt% V2O5) commercial catalyst supplied by IHI/Japan specific for SCR-DeNOx processes in high-dust system was used. Table 1 summarizes the characteristic data for the commercial catalyst (by CL-AS IHI-807060/Japan).
Characteristics of the SCR-DeNOx (V2O5–WO3/TiO2) commercial catalyst (CL-AS IHI-807060/Japan)
The catalysts are usually integrated into the flue gas cleaning chain in the so-called high-dust position, upstream of an electrostatic precipitator [2, 34]. Typically, the content of active component is normally low ( <1 wt% V2O5) to restrict the generation of N2O and side reaction of SO2 oxidation [30, 34, 44, 41]. Honeycomb monoliths can offer more benefits e.g. better mass transfer, reusability and a better dispersion of catalysts in addition to other physical properties, enhanced energy efficiency and considerable cost operation reductions [11, 41].
2.2. Catalytic test in flow stream
Catalytic evaluations of benzene and its halogenated derivatives were carried out by atmospheric pressure for low inlet concentrations (<100 ppm) using a continuous-flow fixed-bed tubular reactor. In this study the conditions of a waste gas flow resulting from municipal waste incinerators were simulated. The reaction temperature range of activity test was 150–350 °C in air stream and an excess if oxygen (7 vol.% O2), both in absence and presence of water vapours (5 vol.% H2O). The total flow rate of simulated flue gas was 0.177 m3/h (calculated at normal conditions of pressure and temperature).
The catalyst was used in a monolith form with 3 × 3 channels and a length of 110 cm having a geometric surface area of 153.5 cm2 according to the required area velocity of 11.5 m/h (corresponding to the contact time of 0.564 s). Area velocity (AV) is defined to ratio of inlet gas volume under standard conditions per geometric surface area of the catalyst. The length of the sample catalysts and the inlet gas flow were adjusted to simulate flow conditions and residence time characteristic for one catalyst layers of an industrial SCR-DeNOx plant.
The feed stream passed through the catalytic unit and reacted with the catalyst placed in reactor. The reactor consists in two concentric quartz tubes placed in an electrically heated oven. The inlet gas flow was heated in the outer ring cylinder to the required reaction temperature before its flow was reversed and returned in the inner cylinder of the reactor where the monolith catalyst test element was placed. Inside the monolith catalyst a thermo-element was inserted, which was connected to a computer, the reaction temperature being thus monitored on-line. Each catalytic oxidation test conducted in this study was under isothermal operation.
Benzene or its mono-halogenated derivatives was supplied by a liquid-injection system called controlled evaporation and mixing. Here the liquid aromatic hydrocarbon, controlled by a liquid flow controller, is transported by a carrier inert gas, into the evaporator–mixer and flows as vapour into the system. The catalytic activity was evaluated in terms of aromatic VOC conversion by gas chromatography equipped with FID and ECD (ParkinElmer, USA). A continues nondispersive Binos 1001 infrared analyser (Rosemount, Germany) was used to determine the CO and an Infralyt 4 (VEB Junkalor, Germany) for the CO2 concentration of the gases. The conversion of aromatic VOCs was calculated according to the flowing expression (1):
(1) |
2.3. Kinetic studies
The catalytic process is complex and involves a series of elementary processes, such as: external diffusion of reactants, internal diffusion of reactants, adsorption of reactants, reaction on the surface of the catalyst, desorption of the products from the surface, internal diffusion of products and external diffusion of products [45].
In a previous study, Lazar et al. [45] demonstrated that, at the temperature of 250 °C and for space velocities ranged between 2700–13,100 h−1, the benzene catalytic oxidation in humid air stream (5 vol.% H2O) occurs following a first order reaction. Establishment of equation rate of catalytic process was done by using the formal kinetic of chemical reactions, being established also a mathematical model for the experimental conditions. An excess of oxygen is used in oxidation reaction, fact that allows the neglecting of oxygen concentration, the rate of catalytic oxidation process (
(2) |
The study concerning the kinetic of the chlorobenzene (C6H5Cl) and bromobenzene (C6H5Br) oxidation process in the presence of the V2O5–WO3/TiO2 (0.53 wt% V2O5) commercial catalyst is continued in order to establish the dependence between the temperature (T) and effective constant rate (kef), as well as to assess the apparent activation energy of the reaction (Ea). An effective constant rate will be considered, taking into account the presence of transfer through pores. Finally, verification of the presence of transfer through pores is achieved using the value of activation energy for the catalytic process. The dependence of effective constant rate by temperature obeys the Arrhenius equation (3):
(3) |
For the establishment of the dependence between temperature and effective constant rate in the studied experimental conditions the linearization of the Arrhenius equation (3) can be used, considering the pre-exponential factor (k0) and the apparent activation energy (Ea) as unknown variables (4):
(4) |
3. Results and discussion
3.1. The dependence relation between the temperature and effective rate constant
Temperature is an important parameter for the kinetic investigation of catalytic processes and for the design and the operation of catalytic reactor. To establish the dependence relation between the temperature and effective rate constant, the influence of the temperature and the oxidative environment upon catalytic conversion of benzene and its mono-halogenated derivatives was investigated.
The experimental data regarding the influence of temperature and the absence or presence of water vapours (5 vol.% H2O) upon catalytic conversion of chlorobenzene and bromobenzene compared with benzene are presented in Figure 1. It was demonstrated that independent of VOCs nature and concentration, initial gas phase composition, all the studied benzene and its mono-halogenated derivatives participate in catalytic oxidation reaction on V2O5–WO3/TiO2 (0.53 wt% V2O5) commercial catalyst starting at temperature of 150 °C. The catalytic conversion in oxidation reaction in non-humid air stream exceeds the value of 85% at temperature of 350 °C.
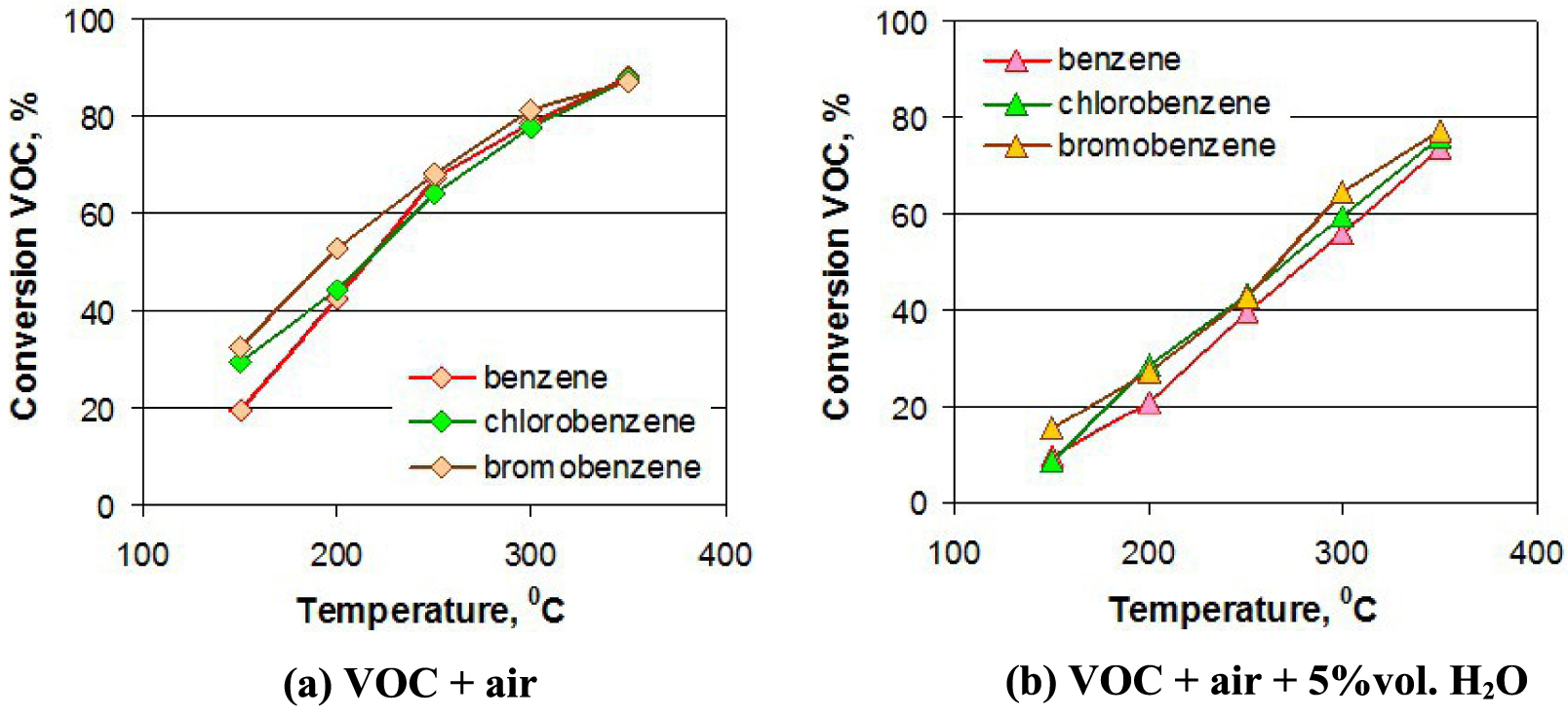
Comparative influence of temperature on conversion of benzene and its mono-halogenated derivatives over V2O5–WO3/TiO2 (0.53 wt% V2O5) commercial catalyst (100–150 mg VOC/m3 at normal conditions of pressure and temperature, AV = 11.5 m/h).
In previous studies [36], the conversion of benzene and its mono-halogenated derivatives is presented in different reaction environments. Also, the selectivity of V2O5–WO3/TiO2 (0.53 wt% V2O5) commercial catalyst and reaction by-products were investigated. It is observed that the catalytic conversion increases with temperature and the oxidation reaction is not complete, predominant being the oxidation reaction with formation of CO and CO2. The presence of water vapours in reaction environment leads to a decrease of catalytic conversion, but favourably influences the catalyst selectivity.
The reactivity of benzene and its mono-halogenated derivatives decreases in order: bromobenzene > chlorobenzene > benzene. This behaviour may be explained by saturated character of benzene, which is given by the cyclic structure of the molecule, which makes that the catalytic oxidation reaction of benzene to be slightly inferior to those of oxidation reaction of its halogenated derivatives [29, 36, 42]. The literature suggesting that the presence of water vapours in the feed favoured the catalyst deactivation on account of the competitive adsorption and oxidation of VOCs and water molecules on the active site. The adsorption behaviour of VOCs on the catalyst surface can correlated to the polarity of the VOC molecules [2, 12, 29, 43]. Although the presence of water vapours will reduce the oxidation efficiency, the deactivation is not observed. This result could possibly be attributed to the removal of Cl (or Br) from the surface as water would facilitate the formation of easily desorbed HCl (or HBr) via the Deacon reaction [2, 32, 34, 36].
The activation energy for the catalytic oxidation reactions of benzene, chlorobenzene and bromobenzene in the studied oxidation environments were further calculated. Utilizing linear regression method, the ln(kef)exp = f(T−1) dependence relationships (Figure 2), which lead to calculus of apparent activation energy of the reaction (Ea) and pre-exponential factor (k0), are established. From analysis of ln(kef)exp = f(T−1) dependences results that, for all experimentally studied cases, the aromatic VOCs catalytic oxidative destruction process occurs without changing of the kinetic mechanism.
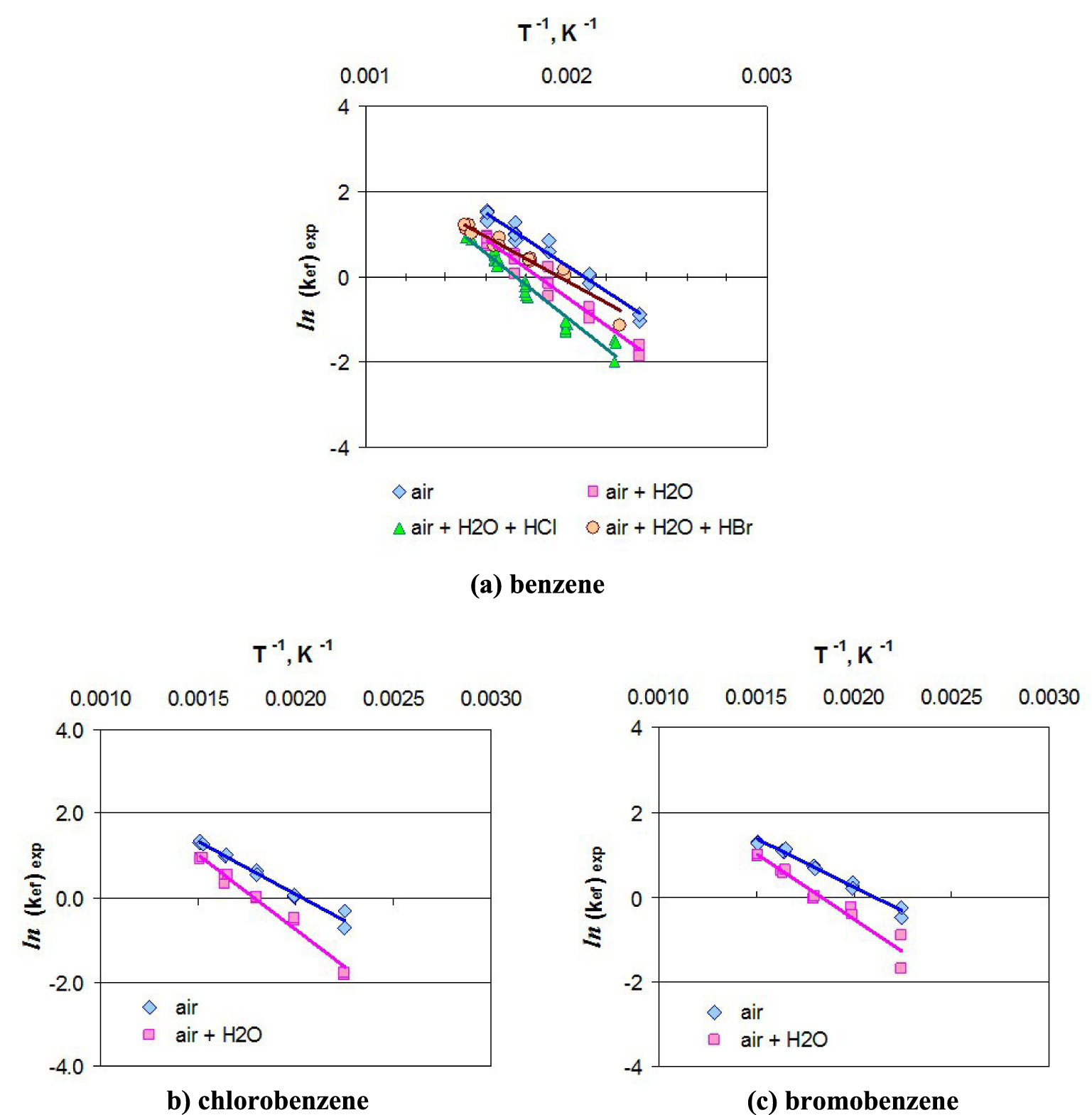
The ln(kef)exp − T−1 dependences for aromatic VOCs catalytic oxidation process over V2O5–WO3/TiO2 (0.53 wt% V2O5) commercial catalyst (100–150 mg VOC/m3 at normal conditions of pressure and temperature, 260 ppm HCl, 260 ppm HBr, AV = 11.5 m/h).
In Table 2, values of pre-exponential factor (k0, in s−1) and apparent activation energy (Ea, in kJ/mol) are presented alongside the dependence relationship of effective constant rate by temperature for experimental conditions investigation (kef)exp in the case of aromatic VOC catalytic oxidation on V2O5–WO3/TiO2 (0.53 wt% V2O5) commercial catalyst.
Apparent activation energy and dependence of catalytic reaction effective constant rate in function of temperature for aromatic VOCs oxidation over V2O5–WO3/TiO2 (0.53 wt% V2O5) commercial catalyst (100–150 mg VOC/m3 at normal conditions of pressure and temperature, 260 ppm HCl, 260 ppm HBr, AV = 11.5 m/h)
VOC | Oxidation environment conditions | Apparent activation energy, Ea (kJ/mol) | Constant rate expression | R2 |
---|---|---|---|---|
C6H6 | air | 25.45 | 0.980 | |
air + H2O | 28.26 | 0.980 | ||
air + H2O + HCl | 31.20 | 0.980 | ||
air + H2O + HBr | 21.55 | 0.980 | ||
C6H5Cl | air | 20.91 | 0.980 | |
air + H2O | 29.47 | 0.980 | ||
C6H5Br | air | 18.77 | 0.984 | |
air + H2O | 25.14 | 0.950 |
The experimental data of the apparent activation energy of benzene and its mono-halogenated derivatives is in correlation with the literature [2, 23, 27, 29, 30, 31, 32]. As well, the comparative analysis concerning apparent activation energy for the three types of aromatic VOCs oxidation reaction evidences the fact that, in the case of benzene and its mono-halogenated derivatives, the values of activation energy are sensible equal. The low value of activation energy can be attributed to the low content of active component V2O5 in the commercial catalyst. Much higher values are reported in the literature, for high values of content V2O5 in catalyst. For example: Wang et al., reported increasing values for the activation energy of the catalytic oxidation reaction of chlorobenzene at 190–220 °C depending on the content of the active component: between 39–45 kJ/mol for using 3 wt% V2O5/TiO2 catalyst and 62.5 kJ/mol for using 5 wt% V2O5/TiO2, respectively [29, 30]. The apparent activation energy is relatively small toward the specific value equal to 42 kJ/mol considered in literature as being the limit at which mass transformation is the limiting rate step for a chemical process.
Lazar et al. [35] demonstrate that NOx selective catalytic reduction on V2O5–WO3/TiO2 (0.53 wt% V2O5) commercial catalyst can occur in parallel to benzene oxidation reaction, the presence of the latter not diminishing the efficiency of NOx reduction. Competition between VOC oxidation process and NOx selective catalytic reduction may be attributed to activities of the Lewis acid site of the SCR-DeNOx catalyst that, in the presence of water vapours, lead to formation of Brönsted acid site, responsible for nitrogen oxides conversion, but, on the other hand, may participate in benzene oxidation reaction.
3.2. The kinetic mechanism
The small apparent activation energy values of benzene and its mono-halogenated derivatives oxidation over V2O5–WO3/TiO2 (0.53 wt% V2O5) commercial catalyst suggests that the catalytic process rate is influenced by elementary processes of mass transfer through catalyst pores (intern diffusion of reactants) and by chemical transformation [24, 27, 45].
The kinetic mechanism of the catalytic oxidation of benzene and its mono-halogenated is established taking into account the following simplifying hypotheses: (1) the catalytic process occurs in isotherm regime; (2) experimental reactor is one with total reaction mass transportation (case when finite a concentration variation in unit time exits); (3) volume variations of the gas phase may be neglected; (4) equation rate is established using the chemical reactions formal kinetic [45].
According to literature, the heterogeneous oxidation of VOCs on transition metal oxides catalyst usually follows the Mars–van-Krevelen (MvK) mechanism, also known as surface lattice oxygen redox mechanism [26, 27, 32, 43]. This mechanism is based on alternative oxidation–reduction of the catalyst and is now generally accepted the assumption of a constant oxygen surface concentration on the catalyst. The catalytic reaction occurring through the interaction between reactant molecules and an oxidized portion of the catalyst. Then follows replenishment of surface oxygen vacancies by bulk oxygen [4, 8, 42, 43].
According to these assumptions, and the mechanism of aromatic VOCs catalytic oxidation hexachlorobenzene proposed in literature [8, 24, 28, 31, 32, 33, 36] the oxidation of benzene and its halogenated derivatives on V2O5–WO3/TiO2 catalyst follows the similar route, and the reaction formulas could be approximately described as follows:
- Adsorption of aromatic VOC and oxygen:
- The aromatic VOC is oxidized by surface lattice oxygen V − Osurface:
- The O2 heals the oxygen vacancies V −□surface of catalyst to fulfil the catalytic cycle
- The surface oxygen vacancies V −□surface are regenerated by bulk lattice oxygen V − Obulk
As mentioned in literature [31, 32, 42, 43], the O2 adsorption is the critical step and governs the kinetic mechanism of the catalytic oxidation process of VOCs. The gas phase oxygen is found to be crucial in the nonhalogenated or halogenate aromatic VOCs oxidation reaction. The halogen deposition on the surface would inhibit the O2 adsorption, thus hindering the whole MvK cycle and resulting in the catalyst deactivation.
The main steps for chemical aromatic VOC species in catalytic process can be described after an adsorption–reaction–desorption as follows: (1) transport of the reactants (VOC and O2) from the bulk of a monolith catalyst, (2) transport of the reactants in the pores of the monolith catalyst to an active site, (3) adsorption of the reactants to the active site, (4) reaction of reactants to form an adsorbed product, (5) desorption of the product from the active site, (6) transport of the products in the pores of the catalytic particle out of the monolith, (7) transport of the products from the monolith to the bulk of the mixture.
4. Conclusions
Aromatic VOCs and NOx coexist together in the flue gas of municipal solid waste incineration plants. Vanadium-based catalysts designed for the process of selective catalytic reduction of nitrogen oxides is an alternative for the oxidative destruction of aromatic VOCs from gas effluents.
A comparative kinetic study regarding the benzene and its mono-halogenated derivatives (chlorobenzene and bromobenzene) catalytic oxidative destruction on V2O5–WO3/TiO2 (0.53 wt% V2O5) commercial catalyst, is presented. The catalytic oxidation reaction rate of this aromatic VOCs in the presence of oxygen can be described as power law model was chosen as a first approximation. This model is the simplest kinetic equation that describes the rate as a function of the concentration (2). In order to verify the dependence between the temperature and the effective constant rate, the experimental data achieved in the kinetic study concerning the influence of temperature on benzene and its mono-halogenated derivatives catalytic conversion were used.
The effective constant rate (kef) follows the Arrhenius equation and thus connect the reaction temperature with the rate of catalytic process. The plot of ln(kef) vs. T−1 calculated from the experimental data for different aromatic VOCs (Table 1). Thus, according to the Arrhenius law both the dimensionless apparent activation energy (Ea∕R) and pre-exponential factor (k0) related to the kinetic parameter have been calculated from these data. The correlation coefficient R2, obtained for the Arrhenius equation is 0.95–0.98 and it shows the right match with the experimental data for the kinetics’ first order reaction.
Depending on the conditions of oxidation, the activation energy for the benzene and its mono-halogenated derivatives catalytic oxidation reactions has values ranged between 18–32 kJ/mol, under the value considered in literature as being the limit at which mass transformation is the limiting rate step for a chemical process. The relatively small values of apparent activation energy suggest that the catalytic process occurs following a kinetic combined model that should take into account the intern diffusion of reactants by catalyst pores and chemical transformation reaction. The two-stage redox model kinetic mechanism (MvK) was proposed to describe the catalytic oxidation of benzene and its mono-halogenated derivatives over V2O5–WO3/TiO2 (0.53 wt% V2O5) commercial catalyst. First, aromatic VOC and oxygen is adsorbed on catalyst surface, and the adsorbed VOC is oxidized by the active lattice oxygen. The redox cycle is ensured by restoring the active centres of catalyst as a result of replenishment of surface oxygen vacancies by bulk oxygen.
Conflicts of interest
Authors have no conflict of interest to declare.